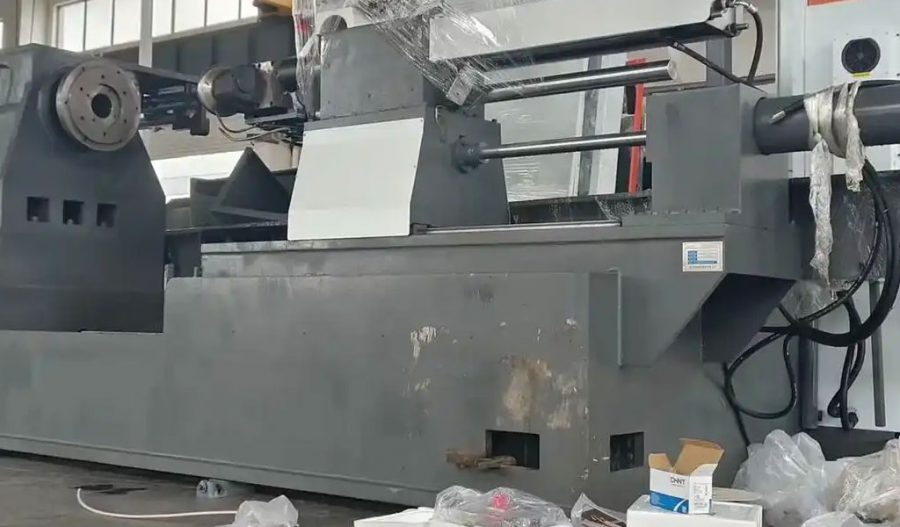
Multi-pass spinning is a manufacturing process used to produce large, complex thin-walled shells, which are essential components in various industries, including aerospace, automotive, and chemical processing. This process involves the incremental deformation of a metal blank into a desired shape through a series of spinning passes. The wall thickness variation of these shells during multi-pass spinning is a critical parameter that affects the structural integrity, performance, and reliability of the final product. Understanding and controlling this variation is crucial for ensuring the quality and efficiency of the manufacturing process.
Introduction to Multi-Pass Spinning
Multi-pass spinning, also known as flow forming or shear spinning, is a cold forming process that transforms a rotating metal blank into a thin-walled shell by applying a series of localized deformations. The process typically involves a spinning mandrel, which holds the workpiece, and a set of rollers that apply pressure to the workpiece as it rotates. The rollers move along the length of the workpiece, gradually reducing its wall thickness and shaping it into the desired form.
The multi-pass nature of the process allows for the progressive reduction of wall thickness, which is essential for achieving the required dimensional accuracy and mechanical properties. Each pass involves a specific set of parameters, including roller feed rate, roller pressure, and mandrel speed, which are carefully controlled to ensure uniform deformation and minimal wall thickness variation.
Factors Influencing Wall Thickness Variation
Several factors influence the wall thickness variation during multi-pass spinning. These factors can be broadly categorized into material properties, process parameters, and tooling design.
- Material Properties: The mechanical properties of the material, such as yield strength, ductility, and work hardening behavior, significantly affect the wall thickness variation. Materials with higher ductility and lower yield strength are more susceptible to thinning during the spinning process. Additionally, the grain structure and anisotropy of the material can influence the deformation behavior and result in non-uniform wall thickness.
- Process Parameters: The key process parameters that affect wall thickness variation include roller feed rate, roller pressure, mandrel speed, and the number of passes. Higher roller feed rates and pressures can lead to more significant thinning, while slower feed rates and lower pressures can result in more uniform wall thickness. The mandrel speed also plays a crucial role, as it affects the heat generation and material flow during the deformation process.
- Tooling Design: The design of the spinning mandrel and rollers is critical for controlling wall thickness variation. The geometry of the mandrel, including its taper and surface finish, can influence the material flow and deformation pattern. Similarly, the design of the rollers, such as their shape, size, and surface finish, can affect the localized deformation and wall thickness uniformity.
Mechanisms of Wall Thickness Variation
The wall thickness variation during multi-pass spinning occurs due to several mechanisms, including plastic deformation, material flow, and residual stresses.
- Plastic Deformation: The primary mechanism of wall thickness variation is plastic deformation, which occurs as the rollers apply pressure to the workpiece. The localized deformation causes the material to flow and thin out, resulting in a reduction in wall thickness. The extent of plastic deformation depends on the material properties and process parameters, as discussed earlier.
- Material Flow: The material flow during the spinning process is influenced by the geometry of the mandrel and rollers, as well as the process parameters. Non-uniform material flow can lead to variations in wall thickness, as some regions may experience more deformation than others. The material flow pattern can be controlled by optimizing the tooling design and process parameters.
- Residual Stresses: Residual stresses are introduced into the workpiece during the spinning process due to the localized deformation and heat generation. These stresses can cause the material to deform further after the spinning process, leading to additional wall thickness variation. Controlling the process parameters and using appropriate post-processing techniques, such as annealing, can help minimize residual stresses and their impact on wall thickness variation.
Modeling and Simulation of Wall Thickness Variation
To better understand and control the wall thickness variation during multi-pass spinning, various modeling and simulation techniques have been developed. These techniques allow for the prediction of wall thickness variation based on material properties, process parameters, and tooling design.
- Finite Element Analysis (FEA): FEA is a powerful tool for simulating the deformation behavior of materials during the spinning process. By discretizing the workpiece into finite elements, FEA can predict the stress and strain distributions, material flow, and wall thickness variation. This information can be used to optimize the process parameters and tooling design to achieve more uniform wall thickness.
- Analytical Models: Analytical models provide a simplified representation of the spinning process and can be used to estimate wall thickness variation based on material properties and process parameters. These models typically involve mathematical equations that describe the deformation behavior and material flow during the spinning process. While less accurate than FEA, analytical models can provide valuable insights and are useful for initial process design and optimization.
- Empirical Models: Empirical models are based on experimental data and statistical analysis. These models correlate the wall thickness variation with various process parameters and material properties, allowing for the prediction of wall thickness variation based on historical data. Empirical models are particularly useful for processes where the underlying mechanisms are complex and difficult to model analytically.
Experimental Studies on Wall Thickness Variation
Numerous experimental studies have been conducted to investigate the wall thickness variation during multi-pass spinning. These studies have focused on various aspects, including the effect of material properties, process parameters, and tooling design on wall thickness variation.
- Material Properties: Experimental studies have shown that materials with higher ductility and lower yield strength are more susceptible to thinning during the spinning process. For example, aluminum alloys, which are commonly used in aerospace applications, exhibit significant wall thickness variation due to their high ductility. In contrast, materials with higher yield strength, such as stainless steel, show more uniform wall thickness variation.
- Process Parameters: The effect of process parameters on wall thickness variation has been extensively studied. Research has shown that higher roller feed rates and pressures lead to more significant thinning, while slower feed rates and lower pressures result in more uniform wall thickness. The mandrel speed also plays a crucial role, as it affects the heat generation and material flow during the deformation process.
- Tooling Design: The design of the spinning mandrel and rollers has been found to significantly influence wall thickness variation. Studies have shown that mandrels with a gradual taper and smooth surface finish promote more uniform material flow and reduce wall thickness variation. Similarly, rollers with optimized geometry and surface finish can improve the localized deformation and wall thickness uniformity.
Control Strategies for Wall Thickness Variation
Controlling the wall thickness variation during multi-pass spinning is essential for ensuring the quality and performance of the final product. Various control strategies have been developed to achieve more uniform wall thickness.
- Process Parameter Optimization: Optimizing the process parameters, such as roller feed rate, roller pressure, and mandrel speed, can help control wall thickness variation. By carefully selecting and adjusting these parameters, it is possible to achieve more uniform deformation and minimize wall thickness variation.
- Tooling Design Optimization: The design of the spinning mandrel and rollers can be optimized to promote more uniform material flow and reduce wall thickness variation. This includes selecting the appropriate mandrel taper, surface finish, and roller geometry.
- Adaptive Control Systems: Adaptive control systems use real-time feedback to adjust the process parameters during the spinning process. These systems can monitor the wall thickness variation and make adjustments to the roller feed rate, roller pressure, and mandrel speed to maintain uniform wall thickness.
- Post-Processing Techniques: Post-processing techniques, such as annealing and heat treatment, can be used to minimize residual stresses and improve the wall thickness uniformity. These techniques help to relieve the internal stresses introduced during the spinning process and reduce further deformation.
Case Studies and Industrial Applications
The control of wall thickness variation during multi-pass spinning has significant implications for various industrial applications. Case studies have demonstrated the importance of wall thickness uniformity in ensuring the structural integrity and performance of large complex thin-walled shells.
- Aerospace Industry: In the aerospace industry, thin-walled shells are used in the construction of aircraft fuselages, wings, and other structural components. Uniform wall thickness is critical for ensuring the structural integrity and aerodynamic performance of these components. Case studies have shown that optimizing the process parameters and tooling design can significantly reduce wall thickness variation and improve the quality of aerospace components.
- Automotive Industry: In the automotive industry, thin-walled shells are used in the manufacture of lightweight and high-strength components, such as engine blocks and transmission cases. Controlling the wall thickness variation is essential for ensuring the dimensional accuracy and mechanical properties of these components. Experimental studies have demonstrated the effectiveness of adaptive control systems and post-processing techniques in achieving uniform wall thickness.
- Chemical Processing Industry: In the chemical processing industry, thin-walled shells are used in the construction of pressure vessels, heat exchangers, and other equipment. Uniform wall thickness is crucial for ensuring the safety and efficiency of these components. Case studies have shown that optimizing the material properties and process parameters can significantly reduce wall thickness variation and improve the performance of chemical processing equipment.
Future Directions and Research Opportunities
The study of wall thickness variation during multi-pass spinning is an active area of research, with numerous opportunities for future development. Advances in materials science, process modeling, and control systems offer promising avenues for improving the uniformity of wall thickness in large complex thin-walled shells.
- Advanced Materials: The development of advanced materials with tailored mechanical properties can help reduce wall thickness variation during the spinning process. Research is ongoing to develop materials with improved ductility, yield strength, and work hardening behavior, which can promote more uniform deformation and wall thickness.
- Process Modeling and Simulation: Advances in process modeling and simulation techniques, such as FEA and machine learning, can provide more accurate predictions of wall thickness variation. These techniques can be used to optimize the process parameters and tooling design, leading to more uniform wall thickness.
- Adaptive Control Systems: The development of advanced adaptive control systems can further improve the control of wall thickness variation during the spinning process. These systems can use real-time feedback and machine learning algorithms to adjust the process parameters dynamically, ensuring more uniform wall thickness.
- Post-Processing Techniques: Innovations in post-processing techniques, such as laser annealing and ultrasonic treatment, can help minimize residual stresses and improve the wall thickness uniformity. These techniques can be integrated into the manufacturing process to enhance the quality and performance of the final product.
Conclusion
The wall thickness variation of large complex thin-walled shells during multi-pass spinning is a critical parameter that affects the structural integrity, performance, and reliability of the final product. Understanding and controlling this variation is essential for ensuring the quality and efficiency of the manufacturing process. Factors influencing wall thickness variation include material properties, process parameters, and tooling design. Mechanisms of wall thickness variation involve plastic deformation, material flow, and residual stresses. Modeling and simulation techniques, such as FEA and analytical models, provide valuable insights into the deformation behavior and wall thickness variation. Experimental studies and case studies have demonstrated the importance of optimizing process parameters, tooling design, and post-processing techniques to achieve more uniform wall thickness. Future research opportunities include the development of advanced materials, process modeling techniques, adaptive control systems, and post-processing techniques to further improve the control of wall thickness variation during multi-pass spinning.
In summary, the study of wall thickness variation during multi-pass spinning is a multifaceted and interdisciplinary field that combines materials science, process engineering, and control systems. By leveraging advances in these areas, it is possible to achieve more uniform wall thickness and enhance the quality and performance of large complex thin-walled shells in various industrial applications.
Maximize Tooling and CNC Metal Spinning Capabilities.
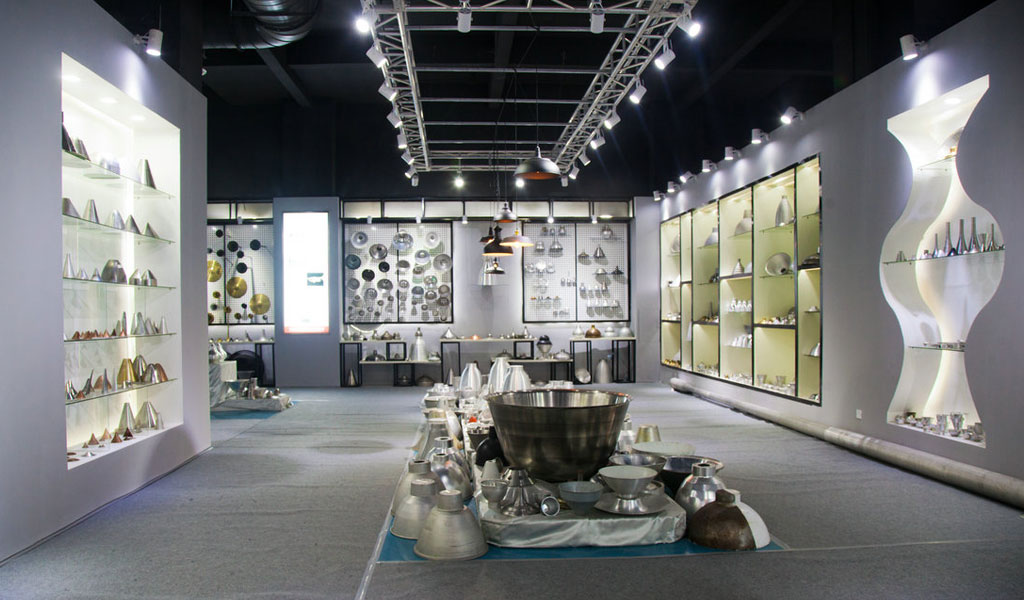
At BE-CU China Metal Spinning company, we make the most of our equipment while monitoring signs of excess wear and stress. In addition, we look into newer, modern equipment and invest in those that can support or increase our manufacturing capabilities. Our team is very mindful of our machines and tools, so we also routinely maintain them to ensure they don’t negatively impact your part’s quality and productivity.
Talk to us today about making a rapid prototype with our CNC metal spinning service. Get a direct quote by chatting with us here or request a free project review.
BE-CU China CNC Metal Spinning service include : CNC Metal Spinning,Metal Spinning Die,Laser Cutting, Tank Heads Spinning,Metal Hemispheres Spinning,Metal Cones Spinning,Metal Dish-Shaped Spinning,Metal Trumpet Spinning,Metal Venturi Spinning,Aluminum Spinning Products,Stainless Steel Spinning Products,Copper Spinning Products,Brass Spinning Products,Steel Spinning Product,Metal Spinnin LED Reflector,Metal Spinning Pressure Vessel,