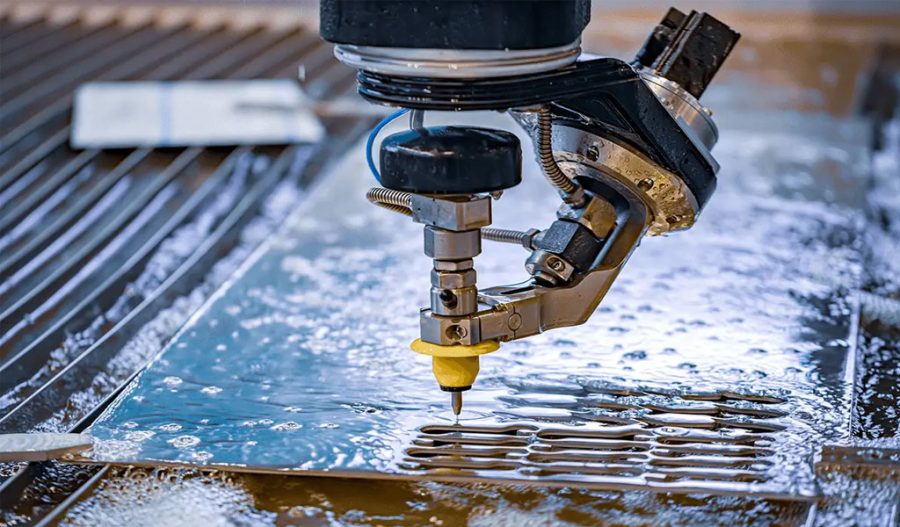
In the realm of industrial cutting technologies, two methods stand out prominently: waterjet cutting and laser cutting. Both techniques have revolutionized manufacturing processes, offering precision, efficiency, and versatility. However, understanding the nuances of each method is crucial for selecting the most suitable option for specific applications. In this comprehensive article, we delve into the intricacies of waterjet and laser cutting, exploring their materials compatibility, diverse applications, and the respective benefits they bring to various industries.
Section 1: Understanding Waterjet Cutting
Waterjet cutting, a method utilizing a high-pressure stream of water mixed with an abrasive substance, has gained traction across industries for its ability to precisely cut a wide range of materials. The principle behind waterjet cutting is simple yet highly effective: harnessing the power of water, accelerated to high velocities, to erode and penetrate materials with exceptional accuracy. Let’s delve deeper into the workings of waterjet cutting:
1.1 – How Waterjet Cutting Works:
Waterjet cutting systems operate on the principle of hydraulic intensification, where water is pressurized to extreme levels, often exceeding 60,000 pounds per square inch (psi), creating a potent cutting force. This high-pressure water is then forced through a small nozzle, typically made of materials like sapphire or diamond, to produce a concentrated stream.
To enhance cutting efficiency, abrasive particles, such as garnet or aluminum oxide, are often introduced into the water stream. These abrasive particles effectively amplify the cutting power, enabling waterjet systems to slice through materials that pure water alone cannot penetrate.
1.2 – Materials Compatibility:
One of the most significant advantages of waterjet cutting is its remarkable compatibility with an extensive array of materials. From metals to composites to fragile substances like glass, ceramics, and even food products, waterjet cutting demonstrates its versatility across numerous industries.
Materials compatible with waterjet cutting include:
- Metals (steel, aluminum, titanium, etc.)
- Non-metals (glass, ceramics, plastics, rubber, wood, etc.)
- Composites (carbon fiber, fiberglass, etc.)
- Natural materials (stone, marble, granite, etc.)
The ability to cut such a diverse range of materials makes waterjet cutting an attractive option for manufacturers seeking versatility and precision in their cutting processes.
1.3 – Applications:
Waterjet cutting finds applications in various industries due to its versatility and precision. Some notable applications include:
- Aerospace: Cutting intricate shapes in aerospace components with precision and minimal heat-affected zones.
- Automotive: Fabricating automotive parts from metals and composites with high accuracy.
- Architectural: Creating custom designs in materials like glass, stone, and metal for architectural applications.
- Food Industry: Slicing food products, such as fruits, vegetables, and meats, with precision and cleanliness.
- Electronics: Cutting circuit boards and other electronic components without generating heat that could damage sensitive materials.
The broad spectrum of applications underscores the importance of waterjet cutting in modern manufacturing processes.
1.4 – Benefits of Waterjet Cutting:
Waterjet cutting offers numerous advantages, making it a preferred choice for many manufacturers. Some key benefits include:
- Precision: Waterjet cutting provides exceptional accuracy, enabling the production of intricate shapes and designs with tight tolerances.
- Versatility: The ability to cut a wide range of materials makes waterjet cutting suitable for diverse applications across various industries.
- Minimal Material Distortion: Unlike traditional cutting methods that generate heat, waterjet cutting produces minimal heat-affected zones, reducing material distortion and preserving material integrity.
- Environmentally Friendly: Waterjet cutting is a clean and environmentally friendly process, as it does not produce hazardous fumes, dust, or waste.
- Cost-Effectiveness: While initial equipment costs may be higher than some traditional cutting methods, the versatility and efficiency of waterjet cutting can lead to long-term cost savings through reduced material waste and increased productivity.
These benefits position waterjet cutting as a competitive solution for manufacturers seeking precision, versatility, and efficiency in their cutting operations.
Section 2: Exploring Laser Cutting
Laser cutting, a widely utilized technology in modern manufacturing, employs a highly focused beam of light to precisely cut through various materials. This non-contact process offers unparalleled speed and accuracy, making it indispensable in industries ranging from automotive to electronics. Let’s delve into the workings, materials compatibility, applications, and benefits of laser cutting:
2.1 – How Laser Cutting Works:
Laser cutting operates on the principle of thermal ablation, where a laser beam melts, burns, or vaporizes material along a predetermined path. The intense energy of the laser beam is focused through a lens or a series of mirrors onto the workpiece, creating a localized area of heat that effectively cuts through the material.
Depending on the material and thickness being cut, different types of lasers are employed, including CO2 lasers, fiber lasers, and neodymium-doped yttrium aluminum garnet (Nd:YAG) lasers. Each type of laser offers unique advantages and is selected based on factors such as material compatibility, cutting speed, and precision requirements.
2.2 – Materials Compatibility:
Laser cutting is renowned for its ability to process a wide range of materials with exceptional precision. Some of the materials compatible with laser cutting include:
- Metals (steel, stainless steel, aluminum, copper, etc.)
- Non-metals (plastics, wood, rubber, acrylic, etc.)
- Composites (carbon fiber, fiberglass, etc.)
- Organic materials (leather, fabric, paper, etc.)
The versatility of laser cutting in handling such diverse materials makes it a preferred choice for manufacturers seeking efficient and precise cutting solutions.
2.3 – Applications:
The versatility and precision of laser cutting have led to its widespread adoption across numerous industries. Some common applications of laser cutting include:
- Manufacturing: Cutting and engraving metal and non-metal components for various manufacturing processes, including automotive, aerospace, and electronics.
- Signage and Advertisement: Creating intricate designs and lettering on materials like acrylic, wood, and metal for signage and advertising purposes.
- Medical Devices: Fabricating precision components for medical devices and equipment from materials like stainless steel and plastics.
- Fashion and Apparel: Cutting fabrics and leather with precision for the production of garments, accessories, and footwear.
- Electronics: Precision cutting of circuit boards, semiconductors, and other electronic components with minimal heat-affected zones.
The versatility and precision of laser cutting make it indispensable in numerous industries, driving innovation and efficiency in manufacturing processes.
2.4 – Benefits of Laser Cutting:
Laser cutting offers a plethora of benefits, making it a preferred choice for manufacturers seeking efficient and precise cutting solutions. Some key advantages include:
- High Precision: Laser cutting provides exceptional accuracy, allowing for intricate designs and tight tolerances to be achieved.
- Speed and Efficiency: Laser cutting is a fast and efficient process, capable of cutting complex shapes and patterns with minimal setup time.
- Minimal Material Waste: The precision of laser cutting results in minimal material wastage, leading to cost savings and increased efficiency.
- Non-contact Process: Laser cutting is a non-contact process, minimizing the risk of damage to delicate materials and reducing tool wear.
- Automation Compatibility: Laser cutting systems can be easily integrated into automated manufacturing processes, enhancing productivity and throughput.
These benefits highlight the significance of laser cutting in modern manufacturing, where efficiency, precision, and versatility are paramount.
Section 3: Comparative Analysis and Conclusion
Having explored the intricacies of waterjet and laser cutting, it’s essential to conduct a comparative analysis to understand their respective strengths and limitations. While both methods offer precision, versatility, and efficiency, certain factors may influence the selection of one over the other based on specific requirements.
3.1 – Comparative Analysis:
- Material Compatibility: Both waterjet and laser cutting exhibit remarkable compatibility with a wide range of materials. However, waterjet cutting may have an edge when it comes to cutting materials that are sensitive to heat or prone to thermal distortion, such as certain plastics, composites, and metals.
- Precision: Laser cutting generally offers higher precision and finer detail, making it ideal for applications that demand intricate designs and tight tolerances. However, waterjet cutting can also achieve impressive levels of precision, particularly in thick or hard materials.
- Speed and Efficiency: Laser cutting is typically faster and more efficient than waterjet cutting, especially for thin materials and intricate shapes. However, waterjet cutting may offer advantages in certain applications where the material thickness or composition requires a slower cutting speed or where minimal heat-affected zones are critical.
- Operating Costs: The operating costs of waterjet and laser cutting systems can vary depending on factors such as energy consumption, maintenance requirements, and consumable costs. While laser cutting systems may have lower operating costs in terms of energy consumption, waterjet cutting systems may offer advantages in terms of consumable costs and maintenance requirements.
- Environmental Impact: Both waterjet and laser cutting are considered environmentally friendly processes compared to traditional cutting methods that generate hazardous fumes and waste. However, waterjet cutting may have a slight edge in terms of environmental impact, as it does not produce any airborne pollutants or require the use of harmful chemicals.
3.2 – Conclusion:
In conclusion, both waterjet and laser cutting technologies offer unique advantages and applications in modern manufacturing. The choice between the two methods depends on various factors, including material compatibility, precision requirements, speed and efficiency, operating costs, and environmental considerations.
For applications that demand high precision, intricate designs, and fine detail, laser cutting may be the preferred choice. On the other hand, waterjet cutting excels in applications where material thickness, composition, or sensitivity to heat are significant factors.
Ultimately, manufacturers must carefully evaluate their specific requirements and priorities to determine the most suitable cutting method for their needs. Whether opting for waterjet or laser cutting, the goal remains the same: to achieve optimal efficiency, precision, and quality in manufacturing processes.
By understanding the materials, uses, and benefits of waterjet and laser cutting, manufacturers can make informed decisions to enhance their production capabilities and stay competitive in today’s dynamic marketplace.
Maximize Tooling and CNC Metal Spinning Capabilities.
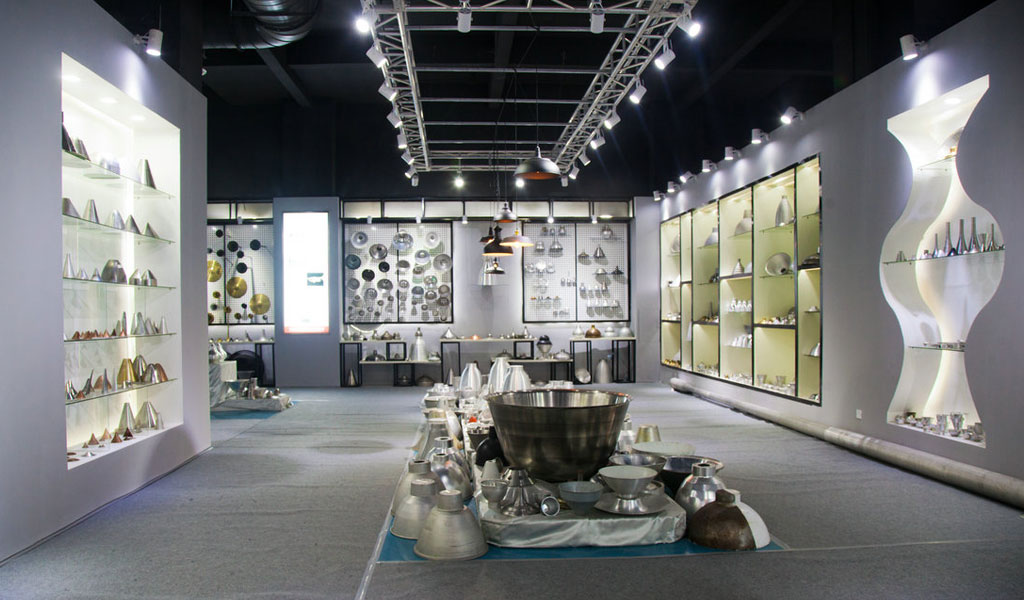
At BE-CU China Metal Spinning company, we make the most of our equipment while monitoring signs of excess wear and stress. In addition, we look into newer, modern equipment and invest in those that can support or increase our manufacturing capabilities. Our team is very mindful of our machines and tools, so we also routinely maintain them to ensure they don’t negatively impact your part’s quality and productivity.
Talk to us today about making a rapid prototype with our CNC metal spinning service. Get a direct quote by chatting with us here or request a free project review.
BE-CU China CNC Metal Spinning service include : CNC Metal Spinning,Metal Spinning Die,Laser Cutting, Tank Heads Spinning,Metal Hemispheres Spinning,Metal Cones Spinning,Metal Dish-Shaped Spinning,Metal Trumpet Spinning,Metal Venturi Spinning,Aluminum Spinning Products,Stainless Steel Spinning Products,Copper Spinning Products,Brass Spinning Products,Steel Spinning Product,Metal Spinnin LED Reflector,Metal Spinning Pressure Vessel,