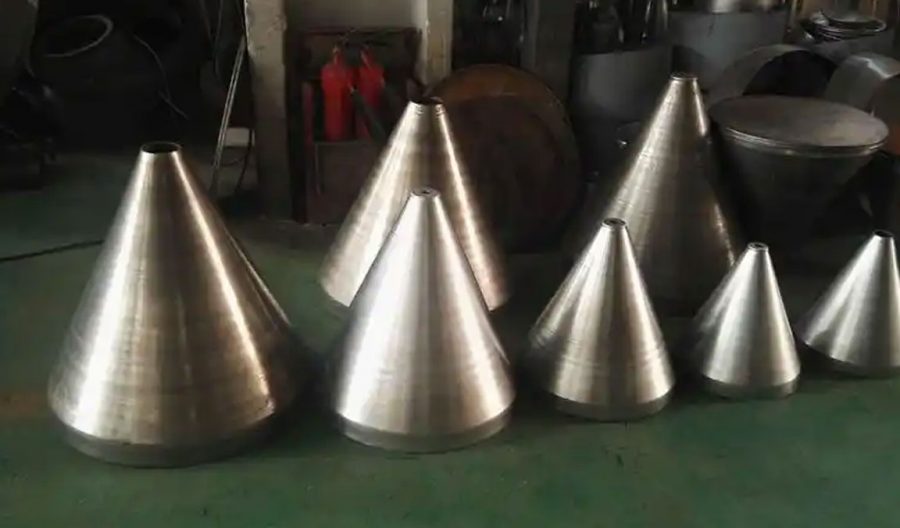
Metal spinning is a manufacturing process that involves the use of a rotating workpiece and a tool to shape the metal into desired forms. The process is widely used in industries ranging from aerospace to automotive, creating parts such as cylindrical components, cones, and hemispheres. Despite its many advantages, such as the ability to produce complex shapes with high precision and relatively low material wastage, metal spinning does have several limitations. These limitations are largely dictated by the nature of the process itself, the characteristics of the materials being used, and the operational constraints inherent in spinning equipment.
1. Material Limitations
Metal spinning can be applied to a wide range of metals, including aluminum, copper, brass, stainless steel, titanium, and various alloys. However, not all materials are equally suited for the process, and some materials present particular challenges.
a. Hardness and Ductility
Metal spinning is best suited for materials that are both ductile and malleable. This is because the process relies on the material’s ability to deform plastically under pressure. Harder metals, particularly those with low ductility, may not be ideal for spinning. Metals such as high-carbon steels, titanium alloys, and certain types of hardened stainless steels can be more difficult to spin because they require more force to deform, potentially leading to cracks, tearing, or damage to the workpiece. These materials also present greater wear and tear on the tooling, increasing maintenance costs.
b. Thickness Limitations
The process is particularly effective for producing parts with relatively consistent thicknesses, but the thickness of the material being spun can present challenges. In some cases, the metal may not deform uniformly, leading to variations in wall thickness. Thicker materials are more difficult to spin because they require higher forces to deform, which can increase the likelihood of material failure. Additionally, thicker parts may require more precise control of the spinning process to achieve uniformity.
c. Material Availability
While metals like aluminum, copper, and brass are readily available and commonly used in metal spinning, the availability of other metals, such as specialty alloys or rare metals, may be more limited. This can pose a significant limitation in industries that require specific material properties, such as aerospace or medical device manufacturing, where the use of highly specialized materials may not always be compatible with the spinning process.
2. Geometric Limitations
Although metal spinning allows for the creation of complex shapes, it does have some constraints when it comes to the geometry of the parts.
a. Forming Complex Geometries
The primary limitation of metal spinning is its inability to produce highly complex shapes with deep undercuts or intricate internal features. While shallow, conical, or cylindrical parts can be spun with relative ease, parts with more complex geometries, such as those requiring multiple changes in diameter, sharp internal angles, or deep recesses, are difficult to produce through spinning alone. Such features may require additional machining operations, such as milling or turning, which increases the overall cost and time of production.
b. Limited Control Over Thickness Distribution
Achieving uniform thickness throughout a spun part is a challenge. While skilled operators can minimize thickness variation, it is often difficult to achieve absolute uniformity, especially in parts with significant changes in radius or wall angles. The thickness tends to be greatest near the center of the part and thinner at the edges, which can cause structural weaknesses or difficulties in achieving the desired material properties.
c. Symmetry and Concentricity Issues
Another geometric limitation involves the potential for issues with symmetry and concentricity. Parts with complex rotational geometries may experience slight deviations during the spinning process, which can lead to off-center parts. The success of the process relies heavily on the precision of the machine and the skill of the operator, and any misalignment can result in imperfections that compromise the part’s functionality and aesthetic appeal.
3. Size Limitations
The size of the part being produced also imposes significant limitations on the spinning process.
a. Maximum Size Constraints
Metal spinning machines have maximum size limits based on the size of the tooling and the capacity of the machine. Large parts, such as those required in industries like aerospace or heavy equipment, may exceed the practical limits of the spinning process. For instance, while small to medium-sized parts can be spun on conventional machines, very large parts, such as those with diameters exceeding 100 inches, may require custom equipment or become impractical due to the forces involved.
b. Difficulty with Large, Heavy Parts
When the material being spun is thick or heavy, handling the part becomes increasingly difficult. For instance, parts with significant mass can cause excessive wear on the machine’s components and bearings. Additionally, the rotating speeds required for larger parts may result in vibration or instability during the spinning process, leading to imperfections in the finished product.
c. Thin-Walled Parts
While metal spinning is generally effective for producing thin-walled parts, there are limitations on the degree of thinness that can be achieved. Extremely thin walls may collapse under the pressure of the spinning process, and the material may not hold its shape. Thin-walled parts are also more susceptible to distortions during cooling or handling, and additional techniques may be required to reinforce these parts during production.
4. Tooling and Equipment Constraints
The equipment and tooling used in metal spinning also impose certain limitations on the process.
a. Tooling Wear and Maintenance
The spinning process places significant stress on the tooling, particularly in high-volume production runs. Tools may wear out more quickly when working with hard or abrasive materials, leading to increased downtime for tool changes and maintenance. This wear can affect the precision of the spun parts, and frequent tool replacements can increase the cost of production. Additionally, the cost of high-quality tooling, such as custom-made tools for specific parts, can be prohibitive.
b. Machine Capacity and Precision
The precision of the final product depends heavily on the capabilities of the metal spinning machine. Some machines may have limited accuracy, especially when it comes to achieving tight tolerances or controlling the thickness distribution. While newer, high-end machines can offer advanced features such as automated adjustments and feedback systems, older machines or lower-cost models may struggle to meet the demands of high-precision applications.
c. Material Clamping Issues
The process of clamping the material to the spinning machine can sometimes be problematic. Inadequate clamping can lead to slippage, which in turn can result in part defects. Furthermore, clamping mechanisms need to be adjusted and set up correctly for each part, which can be time-consuming and increase the potential for human error.
5. Skill and Labor Requirements
Metal spinning is a highly skilled process that requires trained operators to ensure the quality of the finished product.
a. Operator Skill Dependency
The quality of the spun part is heavily dependent on the skill of the operator. Inexperienced operators may struggle with controlling the various parameters of the process, such as the pressure applied, tool speed, and material deformation. In some cases, even small mistakes in technique can lead to large defects or waste, affecting both the cost-effectiveness and efficiency of production. While automated systems can assist with some aspects of the process, human oversight and expertise remain crucial to achieving high-quality results.
b. Labor Intensity
Compared to some other manufacturing processes, metal spinning can be more labor-intensive. Operators must often monitor and adjust the process in real-time to ensure that the material is being formed correctly. This manual intervention, particularly in custom or low-volume production, can make metal spinning less efficient compared to more automated processes such as stamping or injection molding.
c. Training and Experience Requirements
In industries where precision is critical, such as aerospace or medical device manufacturing, operators need extensive training and experience. Metal spinning, while straightforward in concept, is highly sensitive to variables such as material type, machine settings, and tooling conditions. The need for specialized training can increase the overall cost of production and limit the availability of skilled labor.
6. Cost Considerations
Metal spinning is generally regarded as a cost-effective manufacturing process, particularly for small to medium production runs. However, there are specific cost-related limitations associated with the process.
a. Tooling and Setup Costs
Although metal spinning does not require expensive molds or dies, the setup costs can still be significant, particularly for custom parts. Each new part requires the design and fabrication of tooling, which can be a substantial initial investment. For smaller production runs, this cost can be prohibitive when compared to other processes like casting or additive manufacturing.
b. High Initial Setup Time
Before the actual spinning process can begin, operators must spend time setting up the machine, loading the material, and adjusting the tooling. For complex or one-off parts, the setup time can be considerable, which reduces the overall efficiency of the process. This is particularly true in small-batch production, where the time and cost of setup are not amortized across a large volume of parts.
c. Material Waste
While metal spinning is efficient in terms of material usage compared to other processes such as casting or forging, it still produces some material waste. In particular, if a part requires significant material removal to achieve the desired shape, the waste can become substantial. Additionally, if the material is particularly hard to work with or the spinning process is not optimized, the amount of scrap produced can increase.
7. Limitations of Automation and Scale
While automation has made significant inroads into the metal spinning process, there are still challenges when it comes to fully automating certain aspects.
a. Limited Automation for Complex Parts
Automating the entire spinning process, especially for parts with complex geometries, remains challenging. While some operations, such as the spinning of simple, symmetrical parts, can be automated, parts with intricate features may require manual intervention at various stages. The complexity of controlling multiple variables, such as tool speed, material deformation, and pressure, makes it difficult to achieve full automation without compromising quality.
b. Scaling Production
While metal spinning is efficient for small to medium-sized production runs, scaling the process for mass production can be difficult. Each part requires specific adjustments to the machine and tooling, and the process may not be as fast as other manufacturing techniques, such as stamping or injection molding. In high-volume applications, other processes may be more cost-effective due to their higher throughput.
Maximize Tooling and CNC Metal Spinning Capabilities.
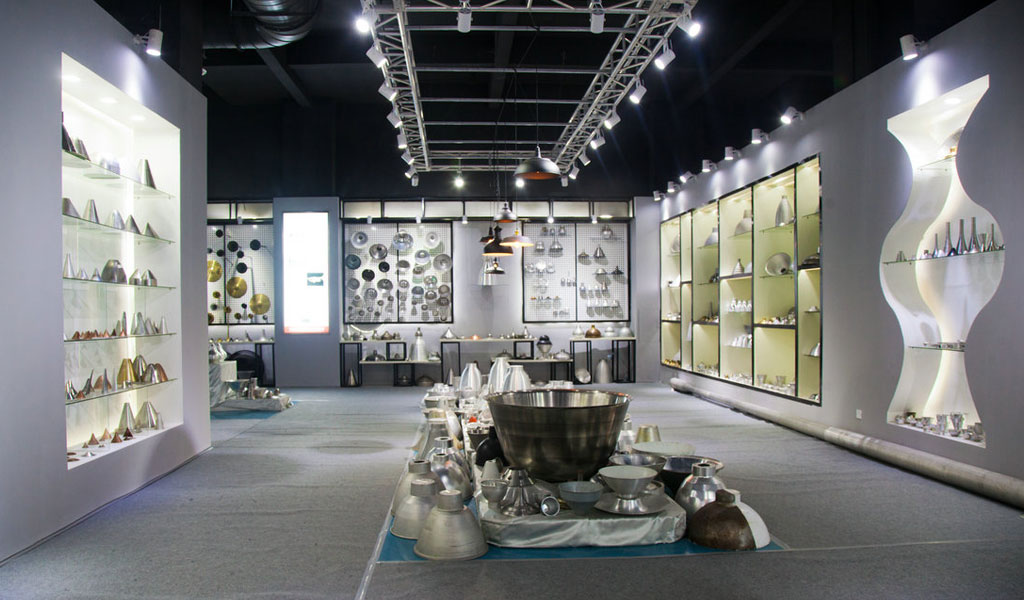
At BE-CU China Metal Spinning company, we make the most of our equipment while monitoring signs of excess wear and stress. In addition, we look into newer, modern equipment and invest in those that can support or increase our manufacturing capabilities. Our team is very mindful of our machines and tools, so we also routinely maintain them to ensure they don’t negatively impact your part’s quality and productivity.
Talk to us today about making a rapid prototype with our CNC metal spinning service. Get a direct quote by chatting with us here or request a free project review.
BE-CU China CNC Metal Spinning service include : CNC Metal Spinning,Metal Spinning Die,Laser Cutting, Tank Heads Spinning,Metal Hemispheres Spinning,Metal Cones Spinning,Metal Dish-Shaped Spinning,Metal Trumpet Spinning,Metal Venturi Spinning,Aluminum Spinning Products,Stainless Steel Spinning Products,Copper Spinning Products,Brass Spinning Products,Steel Spinning Product,Metal Spinnin LED Reflector,Metal Spinning Pressure Vessel,