
An industrial hopper is a critical piece of equipment widely utilized across various industries for the storage, handling, and controlled dispensing of bulk materials. These materials can range from powders and granules to larger aggregates, such as grains, coal, sand, cement, or even industrial byproducts like ash or slag. Hoppers are engineered to facilitate the efficient movement of materials in industrial processes, serving as intermediary storage units that ensure a consistent supply to downstream equipment, such as conveyors, mixers, or processing machinery. Their design and functionality are rooted in principles of material science, mechanical engineering, and fluid dynamics, making them indispensable in sectors like manufacturing, agriculture, mining, construction, and chemical processing.
The concept of a hopper dates back to ancient times, with rudimentary versions used in agricultural settings to store and dispense grains. However, the modern industrial hopper, as understood today, emerged during the Industrial Revolution in the 18th and 19th centuries, when mechanized production necessitated more sophisticated methods for handling bulk materials. Today, industrial hoppers are highly specialized, often custom-designed to meet the specific needs of an application, taking into account factors such as material properties, flow characteristics, environmental conditions, and operational throughput. This article provides a comprehensive exploration of industrial hoppers, delving into their design, types, applications, material considerations, operational mechanics, and comparative analyses, supported by detailed tables for scientific rigor.
Historical Development of Industrial Hoppers
The evolution of industrial hoppers mirrors the broader trajectory of industrial technology. In pre-industrial societies, hoppers were simple containers—often made of wood, clay, or woven materials—used to funnel grain into mills or storage silos. Archaeological evidence from ancient Egypt and Mesopotamia suggests that conical structures made of mud brick were employed as early hoppers to direct grain into grinding stones. These early designs relied on gravity to move materials, a principle that remains central to modern hopper functionality.
With the advent of the Industrial Revolution, the demand for efficient bulk material handling surged. The mechanization of industries like mining and textiles required robust systems to manage coal, ores, and fibers. Early industrial hoppers were constructed from iron or steel, reflecting advancements in metallurgy, and were integrated into steam-powered machinery. By the late 19th century, engineers began to study material flow more systematically, laying the groundwork for modern hopper design. The 20th century saw further refinements, with the introduction of standardized manufacturing processes, advanced materials like stainless steel and polymers, and computational tools for optimizing hopper geometry.
Today, industrial hoppers are a testament to interdisciplinary engineering, incorporating insights from physics, chemistry, and computer-aided design (CAD). Their development continues to evolve with innovations in automation, sensor technology, and sustainable manufacturing practices, reflecting the broader push toward efficiency and environmental responsibility in industrial operations.
Design and Structure of Industrial Hoppers
The design of an industrial hopper is a complex process that balances structural integrity, material flow dynamics, and operational efficiency. At its core, a hopper consists of a storage chamber with an inlet at the top for receiving materials and an outlet at the bottom for discharge. The geometry of the hopper—typically conical, pyramidal, or cylindrical with a tapered base—is engineered to promote smooth, predictable flow while minimizing blockages or material degradation.
Key Components
- Inlet: The entry point where bulk materials are loaded into the hopper. Inlets may be fitted with gates, valves, or feeders to regulate input.
- Body: The main storage volume, which can vary in shape and capacity depending on the application. Common shapes include conical (circular base), wedge-shaped (rectangular base), or transitional (a hybrid design).
- Outlet: The exit point, often equipped with a discharge valve, gate, or feeder (e.g., screw feeder, rotary valve) to control the release of materials.
- Supports: Structural elements such as legs, skirts, or frames that elevate the hopper and bear its weight, especially when filled with dense materials.
- Ancillary Features: These may include vibrators to prevent material bridging, liners to reduce wear, or sensors to monitor fill levels and flow rates.
Material Flow Considerations
The flow of materials through a hopper is governed by the interplay between the hopper’s geometry and the physical properties of the stored material, such as particle size, shape, density, moisture content, and cohesiveness. Two primary flow patterns are observed:
- Mass Flow: All material moves uniformly toward the outlet, minimizing stagnation and segregation. This is ideal for cohesive or perishable materials and requires steep hopper walls (typically 60–70° from horizontal).
- Funnel Flow: Material in the center discharges first, while material near the walls remains stationary until the center empties. This is common in less steep hoppers (angles <45°) and suits free-flowing, non-cohesive materials like dry sand.
Achieving the desired flow pattern requires careful calculation of the hopper’s wall angle, outlet size, and surface friction. The Jenike flow theory, developed by Andrew Jenike in the 1960s, provides a scientific framework for hopper design. It uses parameters like the material’s angle of internal friction (φ) and wall friction angle (φ_w) to determine the critical dimensions for mass flow. For instance, the minimum outlet diameter (D) to prevent arching—a common flow obstruction—is given by:
D=H(θ)⋅σcρb⋅g D = \frac{H(\theta) \cdot \sigma_c}{\rho_b \cdot g} D=ρb⋅gH(θ)⋅σc
Where:
- H(θ) H(\theta) H(θ) is a dimensionless flow factor dependent on hopper angle,
- σc \sigma_c σc is the material’s unconfined yield strength,
- ρb \rho_b ρb is bulk density,
- g g g is gravitational acceleration (9.81 m/s²).
This equation underscores the scientific precision required in hopper design, ensuring reliability in industrial settings.
Construction Materials
Hoppers are constructed from a variety of materials, selected based on the application’s demands:
- Carbon Steel: Durable and cost-effective, used for handling dry, non-corrosive materials like coal or gravel.
- Stainless Steel: Resistant to corrosion and contamination, ideal for food processing, pharmaceuticals, or chemical industries.
- Aluminum: Lightweight and corrosion-resistant, suitable for smaller hoppers or mobile units.
- Polymers/Plastics: Used for lightweight, non-reactive hoppers in specialized applications (e.g., polyethylene for acidic materials).
- Concrete: Employed in large, stationary hoppers for heavy aggregates like cement or ore.
Liners, such as ultra-high-molecular-weight polyethylene (UHMWPE) or ceramic coatings, may be added to reduce friction, wear, or material adhesion.
Types of Industrial Hoppers
Industrial hoppers are classified based on their design, function, and operational context. Below is an exhaustive overview of the main types:
1. Gravity Hoppers
The most common type, relying solely on gravity to move materials from inlet to outlet. They are simple, cost-effective, and widely used in agriculture (e.g., grain silos) and mining (e.g., ore chutes). Gravity hoppers can be conical or wedge-shaped, with outlet sizes tailored to prevent blockages.
2. Vibratory Hoppers
Equipped with vibrators or shakers, these hoppers enhance flow for sticky or cohesive materials like wet clay or fine powders. The vibration reduces bridging (where material forms an arch over the outlet) and rat-holing (where a narrow channel forms, leaving stagnant material). Vibratory hoppers are prevalent in food processing and chemical industries.
3. Screw Feed Hoppers
These integrate a screw conveyor at the outlet to control discharge rates precisely. They are ideal for metering applications, such as feeding raw materials into a mixer or extruder in plastic manufacturing or cement production.
4. Pneumatic Hoppers
Using air pressure or vacuum systems, pneumatic hoppers transport lightweight materials like powders or dust over long distances. Common in industries like pharmaceuticals and cement, they often pair with cyclones or filters to manage dust.
5. Self-Dumping Hoppers
Designed for mobility, these hoppers feature a tilting mechanism that allows them to empty their contents into a larger receptacle or processing unit. They are widely used in construction and waste management for handling debris or scrap metal.
6. Live-Bottom Hoppers
Equipped with moving floors or belts at the base, live-bottom hoppers ensure continuous discharge of difficult materials like sludge or biomass. They are critical in waste treatment and biofuel production.
7. Silo Hoppers
Large-scale hoppers integrated into silos for storing vast quantities of bulk materials. These are common in agriculture (grain storage) and industry (cement silos), with capacities ranging from hundreds to thousands of cubic meters.
Applications of Industrial Hoppers
Industrial hoppers serve a multitude of purposes across diverse sectors, each application leveraging their ability to store and dispense materials efficiently.
Agriculture
In agriculture, hoppers are integral to grain handling, seed distribution, and fertilizer processing. Grain hoppers, often conical and mounted on trailers or silos, ensure a steady supply to mills or packaging lines. Their design must account for grain’s low cohesiveness and susceptibility to moisture-induced spoilage, often incorporating aeration systems.
Mining and Quarrying
Hoppers in mining handle ores, coal, and aggregates, feeding crushers, screens, or conveyor belts. These are typically rugged, large-capacity units made of steel or reinforced concrete, capable of withstanding abrasive materials and harsh environments.
Construction
In construction, hoppers store and dispense cement, sand, or gravel into mixers or batching plants. Self-dumping hoppers are particularly useful on job sites for managing debris or transporting materials to elevated platforms.
Food Processing
Food-grade hoppers, made of stainless steel, handle ingredients like flour, sugar, or spices. They must comply with hygiene standards (e.g., FDA or EU regulations), featuring smooth surfaces and easy-clean designs to prevent contamination.
Chemical and Pharmaceutical Industries
Hoppers in these sectors manage powders, pellets, or hazardous substances, often requiring sealed designs, explosion-proof features, or inert linings to handle reactive materials safely.
Waste Management
Hoppers process industrial waste, recyclables, or sludge, feeding incinerators, compactors, or sorting lines. Live-bottom hoppers excel here, handling sticky or heterogeneous materials.
Operational Mechanics and Challenges
The operation of an industrial hopper hinges on its ability to maintain consistent material flow while avoiding common issues like blockages, segregation, or wear. These challenges are addressed through design optimization and auxiliary equipment.
Flow Issues
- Bridging: Occurs when cohesive materials form a stable arch over the outlet. Prevented by steep wall angles, vibrators, or air cannons.
- Rat-Holing: A narrow flow channel forms, leaving material stagnant. Addressed by mass flow design or mechanical agitation.
- Segregation: Different particle sizes separate during discharge, affecting downstream processes. Mitigated by uniform hopper geometry and feeders.
Wear and Maintenance
Abrasive materials like sand or ore erode hopper walls, necessitating liners or regular maintenance. Corrosion from moist or acidic materials is another concern, particularly for steel hoppers, requiring protective coatings or material upgrades.
Safety Considerations
Hoppers pose risks like dust explosions (e.g., in grain or coal handling) or worker injury during maintenance. Safety features include pressure relief valves, grounding systems, and lockout-tagout mechanisms.
Comparative Analysis of Hopper Types
To provide a scientific basis for understanding industrial hoppers, the following tables compare key types based on design, application, and performance metrics.
Table 1: Structural and Design Comparison
Hopper Type | Shape | Material | Capacity (m³) | Flow Mechanism | Typical Wall Angle |
---|---|---|---|---|---|
Gravity | Conical/Wedge | Steel/Aluminum | 1–100 | Gravity | 45–70° |
Vibratory | Conical | Stainless Steel | 0.5–50 | Vibration + Gravity | 50–65° |
Screw Feed | Cylindrical | Steel | 1–200 | Screw + Gravity | 60–70° |
Pneumatic | Cylindrical | Steel/Plastic | 0.1–10 | Air Pressure | N/A |
Self-Dumping | Rectangular | Steel | 0.5–5 | Tilt + Gravity | 30–45° |
Live-Bottom | Rectangular | Steel/Concrete | 5–500 | Belt + Gravity | 20–40° |
Silo | Conical | Concrete/Steel | 100–10,000 | Gravity | 60–80° |
Table 2: Application Suitability
Hopper Type | Agriculture | Mining | Construction | Food Processing | Chemical | Waste Management |
---|---|---|---|---|---|---|
Gravity | High | High | Medium | Medium | Low | Low |
Vibratory | Medium | Low | Low | High | High | Medium |
Screw Feed | Low | Medium | High | Medium | High | Low |
Pneumatic | Low | Low | Low | High | High | Medium |
Self-Dumping | Low | Medium | High | Low | Low | High |
Live-Bottom | Low | Low | Medium | Low | Medium | High |
Silo | High | High | High | Medium | Medium | Low |
Table 3: Performance Metrics
Hopper Type | Flow Rate (t/h) | Energy Use (kW) | Maintenance Frequency | Cost (USD) |
---|---|---|---|---|
Gravity | 10–500 | 0 | Low | 1,000–10,000 |
Vibratory | 5–200 | 0.5–5 | Medium | 5,000–20,000 |
Screw Feed | 1–100 | 1–10 | High | 10,000–50,000 |
Pneumatic | 0.1–50 | 5–20 | Medium | 15,000–100,000 |
Self-Dumping | 5–50 | 0–2 | Medium | 2,000–15,000 |
Live-Bottom | 20–1,000 | 5–50 | High | 50,000–200,000 |
Silo | 100–5,000 | 0 | Low | 100,000+ |
Advanced Engineering and Innovations
Modern hopper design benefits from cutting-edge technologies:
- Finite Element Analysis (FEA): Simulates stress and flow to optimize structural integrity and material efficiency.
- Sensors: Monitor fill levels, pressure, or blockages in real-time, integrating with Industry 4.0 systems.
- Automation: Robotic feeders and AI-driven flow control enhance precision and reduce labor costs.
- Sustainable Materials: Recycled steel or biodegradable polymers reduce environmental impact.
Conclusion
Industrial hoppers are a cornerstone of bulk material handling, embodying a blend of historical ingenuity and modern engineering. Their versatility, spanning agriculture to waste management, underscores their importance in global industry. By understanding their design principles, types, and applications—supported by detailed comparative data—engineers and operators can select and maintain hoppers that maximize efficiency, safety, and longevity. As industries evolve, so too will hoppers, adapting to new materials, technologies, and sustainability demands.
Maximize Tooling and CNC Metal Spinning Capabilities.
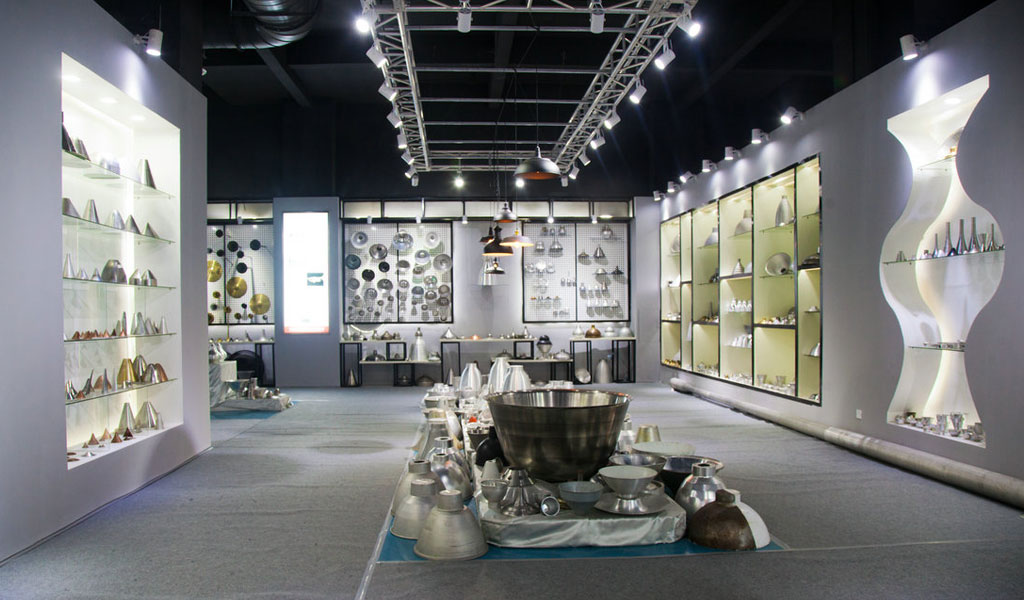
At BE-CU China Metal Spinning company, we make the most of our equipment while monitoring signs of excess wear and stress. In addition, we look into newer, modern equipment and invest in those that can support or increase our manufacturing capabilities. Our team is very mindful of our machines and tools, so we also routinely maintain them to ensure they don’t negatively impact your part’s quality and productivity.
Talk to us today about making a rapid prototype with our CNC metal spinning service. Get a direct quote by chatting with us here or request a free project review.
BE-CU China CNC Metal Spinning service include : CNC Metal Spinning,Metal Spinning Die,Laser Cutting, Tank Heads Spinning,Metal Hemispheres Spinning,Metal Cones Spinning,Metal Dish-Shaped Spinning,Metal Trumpet Spinning,Metal Venturi Spinning,Aluminum Spinning Products,Stainless Steel Spinning Products,Copper Spinning Products,Brass Spinning Products,Steel Spinning Product,Metal Spinnin LED Reflector,Metal Spinning Pressure Vessel,