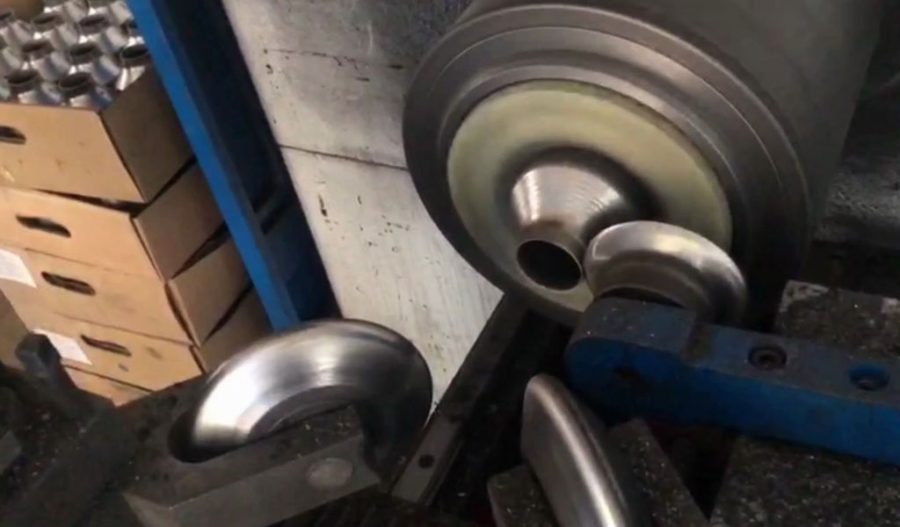
Power spinning, also known as rotary forming or power metal spinning, is a metalworking process that employs a rotating spindle and tool to shape and form materials into various geometries. It is widely utilized in industries such as aerospace, automotive, medical, and consumer products due to its versatility, efficiency, and ability to produce complex shapes with tight tolerances. This article delves into the principles, techniques, applications, and advantages of power spinning, providing an in-depth understanding of the process.
Principles of Power Spinning
The fundamental principle of power spinning involves the application of centrifugal force to shape a metal blank into a desired form. The process typically begins with a flat circular blank, often made of materials such as aluminum, steel, or titanium, which is mounted on a spinning lathe or machine. As the spindle rotates at high speeds, a forming tool applies pressure against the blank, causing it to deform and conform to the shape of the tool.
The deformation occurs through a combination of stretching, bending, and compressing the material. The high-speed rotation generates a substantial amount of centrifugal force, which facilitates the flow of the material into the contours of the tool. This allows for the production of intricate geometries that would be challenging or impossible to achieve using traditional machining methods.
Techniques and Equipment
Power spinning can be performed using various techniques, including conventional spinning, shear spinning, and flow forming. Each method has its unique characteristics and applications, depending on the specific requirements of the workpiece.
- Conventional Spinning: This technique involves the manual or automated movement of the forming tool along the surface of the spinning blank. The tool typically moves in a linear fashion, applying force to create the desired shape. This method is suitable for producing simple shapes, such as cones or cylinders, and is often used for small to medium production runs.
- Shear Spinning: In shear spinning, the forming tool applies a more aggressive force to the material, resulting in a thinner wall section and tighter tolerances. This technique is particularly advantageous for producing parts with complex geometries or profiles, as it allows for greater control over the material flow.
- Flow Forming: Flow forming is a specialized type of power spinning that focuses on elongating and thinning the material rather than merely shaping it. In this technique, the forming tool moves axially along the blank, causing the material to flow and elongate. Flow forming is commonly used in the production of components such as tubes, sleeves, and rings.
The equipment used in power spinning typically consists of a spinning lathe or machine equipped with a rotating spindle, a forming tool, and a clamping mechanism to secure the blank. Modern power spinning machines are often computer numerical control (CNC) equipped, enabling precise control over speed, pressure, and tool movement. This level of automation enhances the consistency and repeatability of the process, making it suitable for high-volume production runs.
Applications of Power Spinning
Power spinning is employed in a wide range of applications across various industries. Its ability to produce lightweight, strong, and complex parts makes it particularly valuable in sectors where performance and efficiency are paramount.
- Aerospace: In the aerospace industry, power spinning is used to manufacture components such as fuel tanks, housings, and structural elements. The lightweight nature of spun parts contributes to overall weight reduction in aircraft, enhancing fuel efficiency and performance. Additionally, the high strength-to-weight ratio of spun materials is critical for meeting stringent aerospace standards.
- Automotive: Power spinning plays a significant role in automotive manufacturing, particularly in the production of components like exhaust systems, fuel tanks, and wheel rims. The process allows for the creation of seamless and lightweight parts, which can improve vehicle performance and reduce emissions.
- Medical Devices: The medical industry utilizes power spinning to create precision components such as surgical instruments, implants, and casings for medical devices. The ability to produce intricate shapes with tight tolerances is essential for ensuring the functionality and safety of these devices.
- Consumer Products: Power spinning is also used in the production of various consumer goods, including kitchenware, lighting fixtures, and decorative items. The aesthetic appeal of spun products, combined with their strength and durability, makes them popular choices for manufacturers.
Advantages of Power Spinning
The power spinning process offers several advantages over traditional machining methods, making it an attractive option for manufacturers. These benefits include:
- Material Efficiency: Power spinning minimizes material waste by utilizing a single blank to produce the final part. The ability to shape materials without excessive cutting or trimming contributes to cost savings and sustainability.
- Cost-Effectiveness: The high production speeds associated with power spinning lead to reduced cycle times and labor costs. Additionally, the lower tooling costs compared to other forming methods further enhance its cost-effectiveness.
- Design Flexibility: Power spinning allows for the production of complex geometries that may be challenging to achieve with traditional machining. This design flexibility enables engineers to explore innovative solutions and optimize product performance.
- High Strength and Durability: The forming process enhances the mechanical properties of the material, resulting in parts that exhibit increased strength and durability. This characteristic is particularly advantageous in demanding applications, such as aerospace and automotive.
- Tight Tolerances: Power spinning can achieve tight tolerances, ensuring that components meet stringent specifications. The precision of the process is particularly valuable in industries where dimensional accuracy is critical.
Limitations of Power Spinning
Despite its numerous advantages, power spinning does have certain limitations that manufacturers must consider. These include:
- Material Limitations: While power spinning is suitable for a wide range of metals, certain materials with high hardness or brittleness may pose challenges during the forming process. Manufacturers must carefully select materials that can withstand the deformation without cracking or failing.
- Part Size Constraints: The size of the parts produced by power spinning is often limited by the capabilities of the spinning machine and tooling. While the process can produce larger components, it may not be suitable for extremely large or heavy parts.
- Initial Setup Costs: The initial investment in spinning equipment and tooling can be significant, particularly for custom or specialized applications. Manufacturers must weigh the upfront costs against the potential long-term benefits of power spinning.
- Skill Requirements: While modern CNC machines have automated many aspects of power spinning, skilled operators are still needed to oversee the process and troubleshoot issues that may arise. Training and expertise in the field are essential for successful implementation.
Conclusion
Power spinning is a versatile and efficient metal forming process that has found applications across a diverse range of industries. Its ability to produce complex shapes with high strength and tight tolerances makes it an attractive option for manufacturers seeking to optimize performance and reduce costs. As technology continues to advance, the potential for power spinning will likely expand, offering new opportunities for innovation and design in the world of metalworking.
Through its principles, techniques, applications, and advantages, power spinning stands as a testament to the evolution of manufacturing processes, bridging the gap between traditional methods and modern automated solutions. As industries seek to push the boundaries of design and performance, power spinning will undoubtedly play a crucial role in shaping the future of manufacturing.
Maximize Tooling and CNC Metal Spinning Capabilities.
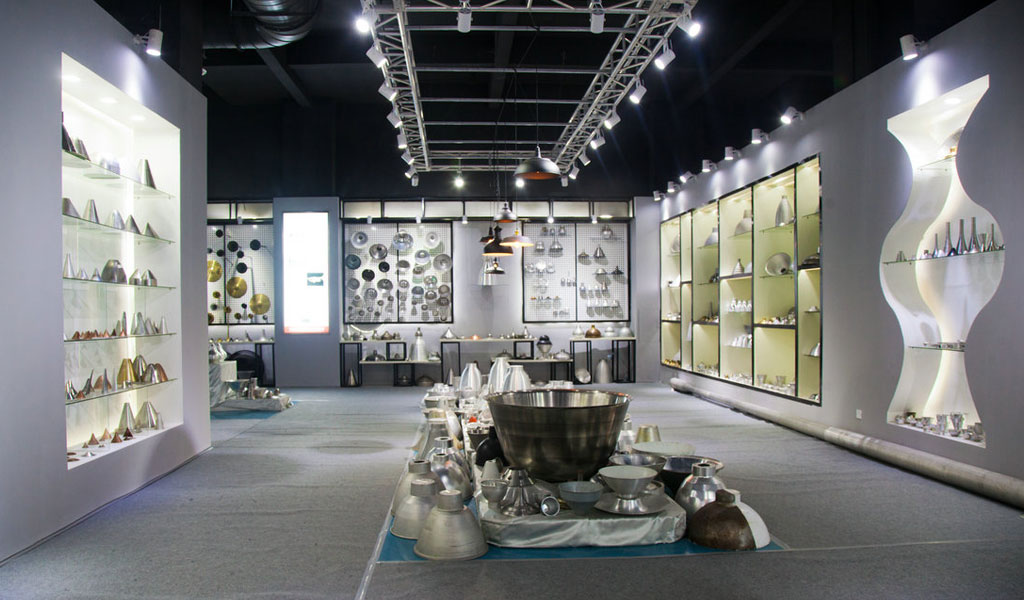
At BE-CU China Metal Spinning company, we make the most of our equipment while monitoring signs of excess wear and stress. In addition, we look into newer, modern equipment and invest in those that can support or increase our manufacturing capabilities. Our team is very mindful of our machines and tools, so we also routinely maintain them to ensure they don’t negatively impact your part’s quality and productivity.
Talk to us today about making a rapid prototype with our CNC metal spinning service. Get a direct quote by chatting with us here or request a free project review.
BE-CU China CNC Metal Spinning service include : CNC Metal Spinning,Metal Spinning Die,Laser Cutting, Tank Heads Spinning,Metal Hemispheres Spinning,Metal Cones Spinning,Metal Dish-Shaped Spinning,Metal Trumpet Spinning,Metal Venturi Spinning,Aluminum Spinning Products,Stainless Steel Spinning Products,Copper Spinning Products,Brass Spinning Products,Steel Spinning Product,Metal Spinnin LED Reflector,Metal Spinning Pressure Vessel,