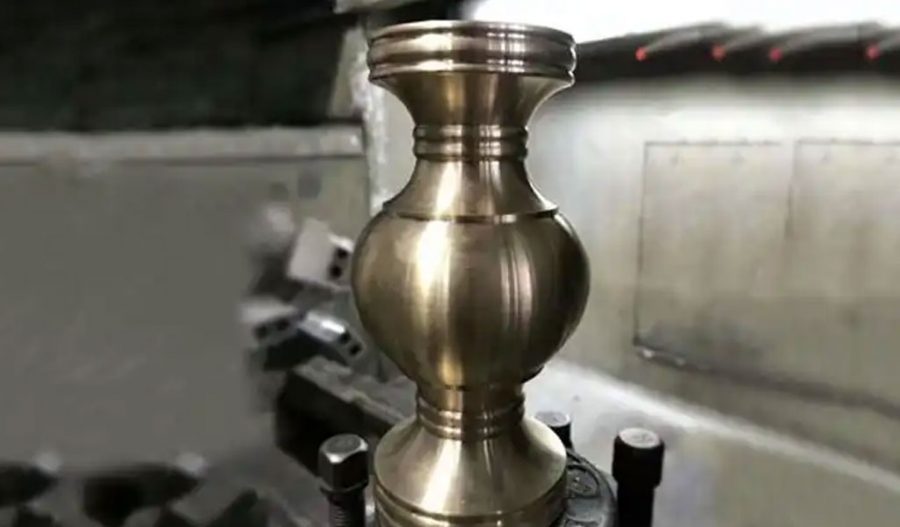
Wheel spinning, also known as spin forming or metal spinning, is an advanced manufacturing process that has gained significant attention in the production of high-strength precision large pipe fittings. This process involves the shaping of metal components through the application of rotational forces, resulting in highly accurate and robust parts. The demand for high-strength precision pipe fittings has surged in various industries, including oil and gas, chemical processing, and aerospace, due to their critical role in ensuring the integrity and efficiency of piping systems. This article delves into the intricacies of wheel spinning, its advantages over traditional manufacturing methods, and its applications in producing large pipe fittings.
Historical Context
The origins of metal spinning can be traced back to ancient times, where artisans used manual spinning techniques to shape metals into various forms. However, the modern iteration of wheel spinning emerged during the Industrial Revolution, driven by the need for mass production and precision engineering. The advent of computer-controlled machinery and advanced materials has further refined the process, making it a viable option for manufacturing large, high-strength pipe fittings.
Principles of Wheel Spinning
Wheel spinning is a cold forming process that utilizes a spinning lathe to shape a metal blank into the desired form. The process involves several key components:
- Mandrel: A cylindrical tool that holds the metal blank in place and provides the internal shape.
- Spinning Wheel: A tool that applies pressure to the metal blank, gradually shaping it as it rotates.
- Tailstock: A support mechanism that holds the mandrel and ensures stability during the spinning process.
- Control System: Modern spinning lathes are equipped with computer numerical control (CNC) systems that automate the process, ensuring precision and repeatability.
The spinning process can be broken down into several stages:
- Blank Preparation: The metal blank is cut to the required size and shape. Common materials include stainless steel, titanium, and high-strength alloys.
- Mounting: The blank is mounted onto the mandrel, which is then secured in the spinning lathe.
- Spinning: The lathe rotates the mandrel and blank at high speeds, while the spinning wheel applies pressure to shape the metal. The wheel can be adjusted to create various profiles and thicknesses.
- Finishing: After the desired shape is achieved, the part is removed from the mandrel and undergoes finishing processes such as polishing, heat treatment, or coating.
Advantages of Wheel Spinning
Wheel spinning offers several advantages over traditional manufacturing methods such as casting, forging, and welding. These advantages include:
- High Precision: The controlled nature of the spinning process allows for the production of parts with tight tolerances and high dimensional accuracy.
- Strength and Durability: The cold forming process enhances the mechanical properties of the material, resulting in parts with superior strength and durability.
- Cost-Effective: Wheel spinning reduces material waste and eliminates the need for multiple machining steps, making it a cost-effective option for large-scale production.
- Versatility: The process can be adapted to produce a wide range of shapes and sizes, making it suitable for various applications.
- Environmentally Friendly: The reduced material waste and energy consumption make wheel spinning a more sustainable manufacturing option.
Comparison with Traditional Manufacturing Methods
To better understand the benefits of wheel spinning, it is useful to compare it with traditional manufacturing methods. The following table provides a detailed comparison:
Feature | Wheel Spinning | Casting | Forging | Welding |
---|---|---|---|---|
Precision | High | Moderate | Moderate | Low to Moderate |
Strength | High | Moderate | High | Moderate |
Material Waste | Low | High | Moderate | Low |
Cost | Moderate | High | High | Moderate |
Versatility | High | Moderate | Moderate | High |
Environmental Impact | Low | High | Moderate | Moderate |
Production Speed | Moderate to High | Slow | Moderate | Moderate |
Surface Finish | Excellent | Rough | Good | Fair |
Applications | Precision components, large pipe fittings | Complex shapes, large components | High-strength components | Structural components, repairs |
Applications in Large Pipe Fittings
Large pipe fittings are critical components in various industrial applications, where they are subjected to high pressures, temperatures, and corrosive environments. Wheel spinning is particularly well-suited for manufacturing these fittings due to its ability to produce high-strength, precision parts. Some of the key applications include:
- Oil and Gas Industry: Pipe fittings in the oil and gas industry must withstand extreme conditions, including high pressures and temperatures. Wheel-spun fittings offer the necessary strength and durability to ensure the integrity of piping systems.
- Chemical Processing: In chemical processing plants, pipe fittings are exposed to corrosive chemicals and high temperatures. The precision and strength of wheel-spun fittings make them ideal for these demanding environments.
- Aerospace Industry: The aerospace industry requires high-strength, lightweight components that can withstand extreme conditions. Wheel spinning allows for the production of precision fittings that meet these stringent requirements.
- Power Generation: In power plants, pipe fittings must handle high pressures and temperatures. Wheel-spun fittings provide the necessary strength and precision to ensure reliable operation.
Materials Used in Wheel Spinning
The choice of material is crucial in the wheel spinning process, as it directly affects the strength, durability, and performance of the final product. Common materials used in wheel spinning for large pipe fittings include:
- Stainless Steel: Known for its corrosion resistance and strength, stainless steel is a popular choice for pipe fittings in corrosive environments.
- Titanium: Titanium offers excellent strength-to-weight ratio and corrosion resistance, making it ideal for aerospace and chemical processing applications.
- High-Strength Alloys: Alloys such as Inconel and Hastelloy provide superior strength and resistance to high temperatures and corrosive environments.
- Aluminum: Lightweight and corrosion-resistant, aluminum is used in applications where weight is a critical factor.
Case Studies
Several case studies highlight the effectiveness of wheel spinning in manufacturing large pipe fittings. For instance, a major oil and gas company adopted wheel spinning to produce high-strength pipe fittings for offshore drilling platforms. The fittings demonstrated superior performance under extreme conditions, reducing maintenance costs and enhancing operational safety.
In another case, an aerospace manufacturer utilized wheel spinning to produce precision fittings for aircraft fuel systems. The fittings met the stringent requirements for strength, precision, and weight, contributing to the overall efficiency and safety of the aircraft.
Future Trends
The future of wheel spinning in manufacturing large pipe fittings looks promising, with several emerging trends:
- Advanced Materials: The development of new high-strength, lightweight materials will further enhance the performance of wheel-spun fittings.
- Automation and AI: The integration of advanced automation and artificial intelligence (AI) in the spinning process will improve precision, efficiency, and quality control.
- Sustainability: The focus on sustainability will drive the adoption of wheel spinning as a more environmentally friendly manufacturing option.
- Customization: The ability to produce customized fittings tailored to specific applications will increase the versatility and appeal of wheel spinning.
Conclusion
Wheel spinning represents a significant advancement in the manufacturing of high-strength precision large pipe fittings. Its ability to produce parts with high precision, strength, and durability makes it a superior alternative to traditional manufacturing methods. As industries continue to demand robust and reliable pipe fittings, the adoption of wheel spinning is poised to grow, driven by its numerous advantages and future innovations.
Maximize Tooling and CNC Metal Spinning Capabilities.
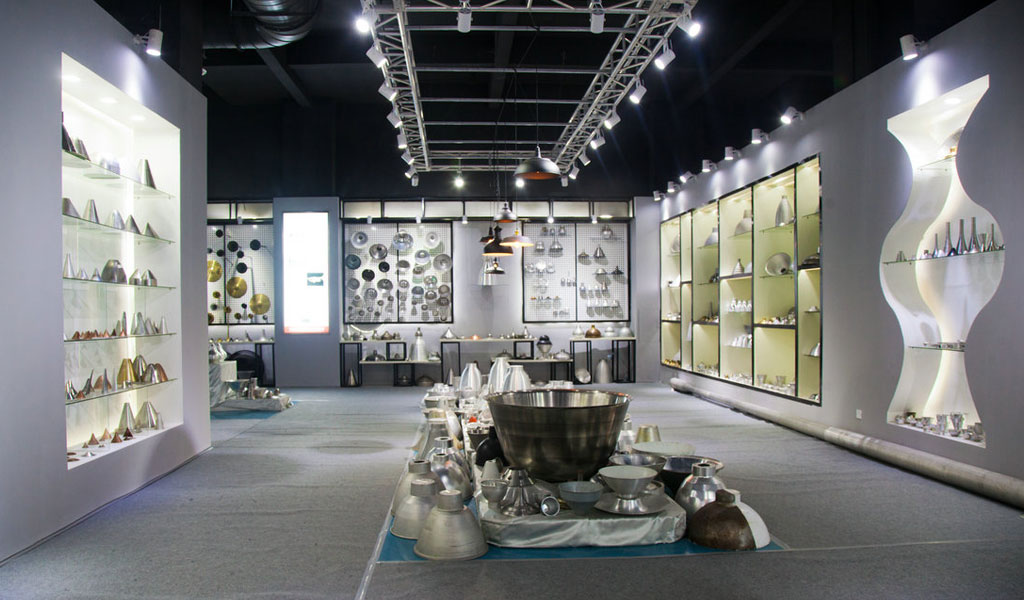
At BE-CU China Metal Spinning company, we make the most of our equipment while monitoring signs of excess wear and stress. In addition, we look into newer, modern equipment and invest in those that can support or increase our manufacturing capabilities. Our team is very mindful of our machines and tools, so we also routinely maintain them to ensure they don’t negatively impact your part’s quality and productivity.
Talk to us today about making a rapid prototype with our CNC metal spinning service. Get a direct quote by chatting with us here or request a free project review.
BE-CU China CNC Metal Spinning service include : CNC Metal Spinning,Metal Spinning Die,Laser Cutting, Tank Heads Spinning,Metal Hemispheres Spinning,Metal Cones Spinning,Metal Dish-Shaped Spinning,Metal Trumpet Spinning,Metal Venturi Spinning,Aluminum Spinning Products,Stainless Steel Spinning Products,Copper Spinning Products,Brass Spinning Products,Steel Spinning Product,Metal Spinnin LED Reflector,Metal Spinning Pressure Vessel,