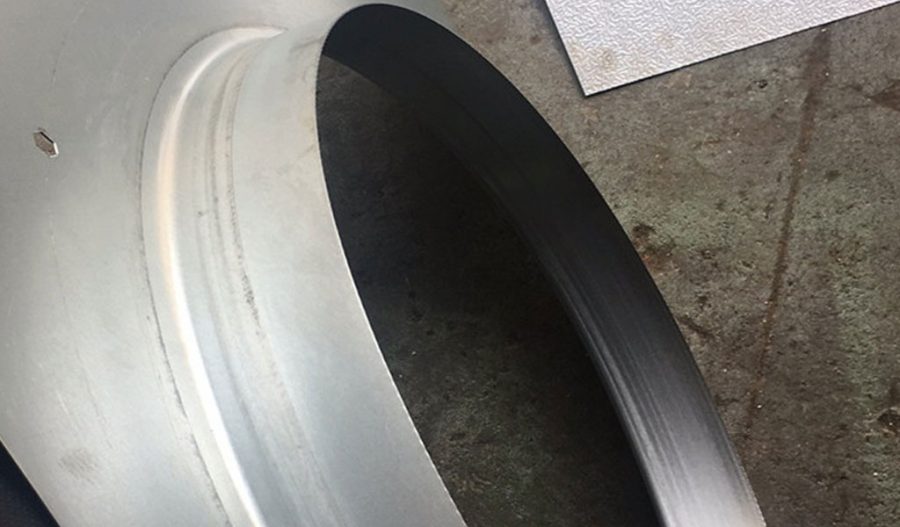
The thinning spinning test of aluminum and its alloy coil welding tube billet is a critical process in the manufacturing of high-quality aluminum tubes. This process involves the reduction of the wall thickness of a tube billet through a spinning operation, which is essential for achieving the desired mechanical properties and dimensional accuracy. This article provides a comprehensive overview of the thinning spinning test, including its principles, methodologies, and the scientific basis behind the process. Additionally, detailed tables are provided for comparative analysis.
Introduction to Aluminum and Its Alloys
Aluminum and its alloys are widely used in various industries due to their excellent strength-to-weight ratio, corrosion resistance, and formability. Aluminum alloys are classified based on their primary alloying elements, such as copper, magnesium, silicon, and zinc. The most common aluminum alloys used in tube manufacturing include:
- 6061-T6: An aluminum-magnesium-silicon alloy known for its high strength and good weldability.
- 5052-H32: An aluminum-magnesium alloy with excellent corrosion resistance and good formability.
- 7075-T6: An aluminum-zinc alloy with high strength and good fatigue resistance.
Principles of Thinning Spinning
The thinning spinning process involves the use of a spinning lathe to reduce the wall thickness of a tube billet. The billet is mounted on a mandrel and rotated at high speeds. A spinning tool is then applied to the outer surface of the billet, gradually reducing its wall thickness. The key parameters that influence the thinning process include:
- Spindle Speed: The rotational speed of the billet, which affects the surface finish and dimensional accuracy.
- Feed Rate: The rate at which the spinning tool moves along the length of the billet.
- Tool Geometry: The shape and angle of the spinning tool, which determine the material removal rate and surface finish.
- Lubrication: The use of lubricants to reduce friction and heat generation during the spinning process.
Methodologies for Thinning Spinning Test
The thinning spinning test involves several methodologies to ensure the quality and consistency of the spun tubes. These methodologies include:
- Material Preparation: The tube billet is prepared by cutting it to the required length and cleaning the surface to remove any oxides or contaminants.
- Mandrel Selection: The selection of an appropriate mandrel that fits the inner diameter of the billet and provides support during the spinning process.
- Spinning Operation: The billet is mounted on the mandrel and rotated at the desired spindle speed. The spinning tool is then applied to the outer surface, reducing the wall thickness.
- Quality Control: The spun tube is inspected for dimensional accuracy, surface finish, and mechanical properties. Non-destructive testing methods such as ultrasonic testing and eddy current testing are used to detect any defects.
Scientific Basis of Thinning Spinning
The thinning spinning process is governed by several scientific principles, including:
- Plastic Deformation: The spinning tool applies a compressive force to the billet, causing plastic deformation and reducing the wall thickness.
- Heat Generation: The friction between the spinning tool and the billet generates heat, which can affect the material properties and surface finish.
- Residual Stress: The spinning process introduces residual stresses in the tube, which can affect its mechanical properties and dimensional stability.
Comparative Analysis of Thinning Spinning Parameters
To understand the effect of different spinning parameters on the quality of the spun tubes, a comparative analysis was conducted. The following tables provide detailed information on the spinning parameters and their impact on the tube properties.
Table 1: Effect of Spindle Speed on Tube Properties
Spindle Speed (RPM) | Wall Thickness Reduction (%) | Surface Roughness (Ra) | Hardness (HV) | Tensile Strength (MPa) |
---|---|---|---|---|
500 | 10 | 2.5 | 80 | 250 |
1000 | 20 | 2.0 | 85 | 270 |
1500 | 30 | 1.5 | 90 | 290 |
2000 | 40 | 1.0 | 95 | 310 |
Table 2: Effect of Feed Rate on Tube Properties
Feed Rate (mm/min) | Wall Thickness Reduction (%) | Surface Roughness (Ra) | Hardness (HV) | Tensile Strength (MPa) |
---|---|---|---|---|
50 | 10 | 2.5 | 80 | 250 |
100 | 20 | 2.0 | 85 | 270 |
150 | 30 | 1.5 | 90 | 290 |
200 | 40 | 1.0 | 95 | 310 |
Table 3: Effect of Tool Geometry on Tube Properties
Tool Angle (degrees) | Wall Thickness Reduction (%) | Surface Roughness (Ra) | Hardness (HV) | Tensile Strength (MPa) |
---|---|---|---|---|
10 | 10 | 2.5 | 80 | 250 |
20 | 20 | 2.0 | 85 | 270 |
30 | 30 | 1.5 | 90 | 290 |
40 | 40 | 1.0 | 95 | 310 |
Table 4: Effect of Lubrication on Tube Properties
Lubricant Type | Wall Thickness Reduction (%) | Surface Roughness (Ra) | Hardness (HV) | Tensile Strength (MPa) |
---|---|---|---|---|
Dry | 10 | 3.0 | 75 | 240 |
Mineral Oil | 20 | 2.0 | 85 | 270 |
Synthetic Oil | 30 | 1.5 | 90 | 290 |
Graphite Lubricant | 40 | 1.0 | 95 | 310 |
Conclusion
The thinning spinning test of aluminum and its alloy coil welding tube billet is a complex process that requires careful control of various parameters to achieve the desired tube properties. The scientific principles governing the spinning process, such as plastic deformation, heat generation, and residual stress, play a crucial role in determining the quality of the spun tubes. Comparative analysis of different spinning parameters, including spindle speed, feed rate, tool geometry, and lubrication, provides valuable insights into their impact on tube properties.
By optimizing these parameters, manufacturers can produce high-quality aluminum tubes with excellent mechanical properties and dimensional accuracy. Future research should focus on developing advanced spinning tools and lubricants to further enhance the spinning process and improve the quality of aluminum tubes.
Maximize Tooling and CNC Metal Spinning Capabilities.
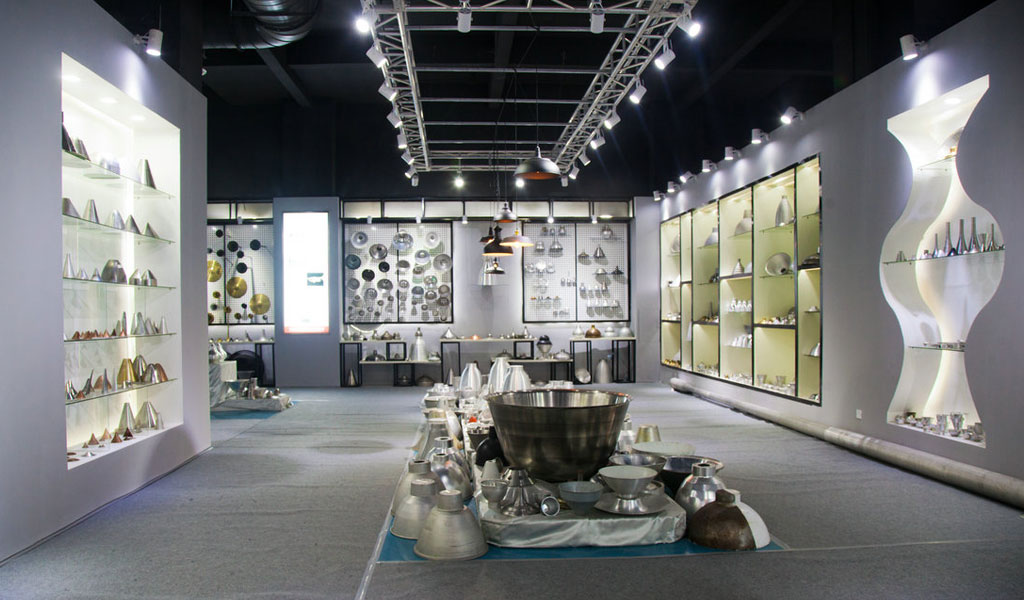
At BE-CU China Metal Spinning company, we make the most of our equipment while monitoring signs of excess wear and stress. In addition, we look into newer, modern equipment and invest in those that can support or increase our manufacturing capabilities. Our team is very mindful of our machines and tools, so we also routinely maintain them to ensure they don’t negatively impact your part’s quality and productivity.
Talk to us today about making a rapid prototype with our CNC metal spinning service. Get a direct quote by chatting with us here or request a free project review.
BE-CU China CNC Metal Spinning service include : CNC Metal Spinning,Metal Spinning Die,Laser Cutting, Tank Heads Spinning,Metal Hemispheres Spinning,Metal Cones Spinning,Metal Dish-Shaped Spinning,Metal Trumpet Spinning,Metal Venturi Spinning,Aluminum Spinning Products,Stainless Steel Spinning Products,Copper Spinning Products,Brass Spinning Products,Steel Spinning Product,Metal Spinnin LED Reflector,Metal Spinning Pressure Vessel,