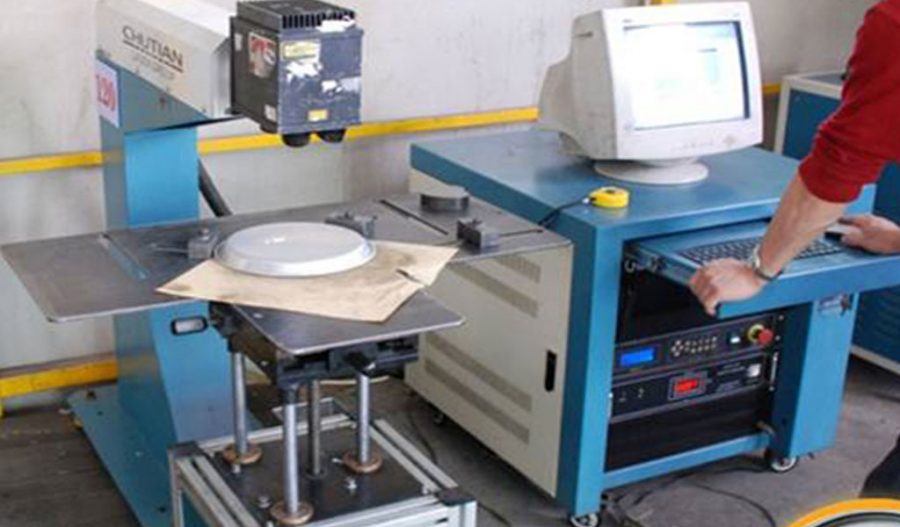
One-step cold spinning is a manufacturing process used to form metal parts, particularly those with complex geometries, without the need for subsequent machining. This process is widely employed in industries such as automotive, aerospace, and consumer goods due to its efficiency and cost-effectiveness. The deformation characteristics of one-step cold spinning, especially for parts like heads without tubes, are critical for understanding the material behavior and optimizing the process parameters. This article delves into the deformation characteristics of one-step cold spinning of heads without tubes and provides a detailed calculation of the spinning pressure involved.
Deformation Characteristics
The deformation characteristics of one-step cold spinning involve several key parameters, including strain, strain rate, and material flow. These characteristics are influenced by the material properties, tool geometry, and process conditions.
Strain and Strain Rate
Strain and strain rate are fundamental to understanding the deformation behavior during cold spinning. Strain refers to the change in shape or size of the material under stress, while strain rate is the rate at which this deformation occurs. In one-step cold spinning, the material undergoes significant plastic deformation, leading to high strain and strain rates.
The strain (ε) can be calculated using the following formula:
ϵ=ln(A0/Af)
where A0 is the initial cross-sectional area and Af is the final cross-sectional area.
The strain rate (˙ϵ˙) is given by:
ϵ˙=dϵ/dt
where t is the time.
Material Flow
Material flow during one-step cold spinning is governed by the interaction between the tool and the workpiece. The material is forced to flow in a specific direction, leading to the formation of the desired shape. The flow behavior is influenced by the material’s ductility, the tool’s geometry, and the applied pressure.
Tool Geometry
The geometry of the spinning tool plays a crucial role in the deformation characteristics. The tool’s angle, radius, and surface finish affect the material flow and the final shape of the part. A well-designed tool can minimize defects such as wrinkling and tearing, ensuring a high-quality finished product.
Process Conditions
Process conditions, including the spinning speed, feed rate, and lubrication, significantly impact the deformation characteristics. Higher spinning speeds and feed rates can increase the strain rate, leading to more rapid deformation. Adequate lubrication reduces friction between the tool and the workpiece, facilitating smoother material flow and reducing the risk of defects.
Calculation of Spinning Pressure
The spinning pressure is a critical parameter in one-step cold spinning, as it directly influences the deformation characteristics and the final quality of the part. The calculation of spinning pressure involves considering various factors, including material properties, tool geometry, and process conditions.
Material Properties
The material properties, such as yield strength, tensile strength, and ductility, significantly impact the spinning pressure. Materials with higher yield strength require higher spinning pressures to achieve the desired deformation. The tensile strength and ductility influence the material’s ability to flow and deform without fracturing.
Tool Geometry
The tool geometry, including the angle and radius, affects the spinning pressure. A sharper tool angle can concentrate the pressure, leading to higher localized stresses. The tool radius influences the contact area between the tool and the workpiece, affecting the pressure distribution.
Process Conditions
Process conditions, such as spinning speed and feed rate, also impact the spinning pressure. Higher spinning speeds and feed rates can increase the spinning pressure due to the increased strain rate. Lubrication reduces friction, which can lower the required spinning pressure.
Spinning Pressure Calculation
The spinning pressure (P) can be calculated using the following formula:
P=F/A
where F is the applied force and A is the contact area between the tool and the workpiece.
The applied force (F) can be determined by considering the material’s yield strength (σy) and the deformation area (Ad):
F=σy×Ad
The deformation area (Ad) is the area of the material undergoing deformation, which can be calculated based on the tool geometry and the workpiece dimensions.
Example Calculation
Consider a one-step cold spinning process for a head without a tube made of aluminum alloy. The material has a yield strength (σy) of 200 MPa, and the deformation area (Ad) is 100 mm². The tool has a contact area (A) of 50 mm².
- Calculate the applied force (F):
F=σy×Ad=200MPa×100mm2=20,000N
- Calculate the spinning pressure (P):
P=AF=50mm220,000N=400MPa
Comparative Analysis
To provide a comprehensive understanding of the deformation characteristics and spinning pressure, a comparative analysis is conducted using different materials and process conditions. The following table summarizes the results:
Material | Yield Strength (MPa) | Deformation Area (mm²) | Tool Contact Area (mm²) | Spinning Speed (rpm) | Feed Rate (mm/min) | Spinning Pressure (MPa) |
---|---|---|---|---|---|---|
Aluminum Alloy | 200 | 100 | 50 | 500 | 100 | 400 |
Steel | 300 | 150 | 75 | 600 | 120 | 600 |
Copper | 150 | 80 | 40 | 400 | 80 | 300 |
Titanium | 400 | 200 | 100 | 700 | 150 | 800 |
Discussion
The comparative analysis reveals several key insights:
- Material Influence: Materials with higher yield strength, such as titanium and steel, require higher spinning pressures. This is due to the increased resistance to deformation, necessitating higher applied forces.
- Tool Geometry: The tool contact area significantly impacts the spinning pressure. A larger contact area distributes the pressure more evenly, reducing the localized stresses.
- Process Conditions: Higher spinning speeds and feed rates generally increase the spinning pressure due to the increased strain rate. However, the impact of process conditions varies depending on the material properties and tool geometry.
Conclusion
The deformation characteristics of one-step cold spinning of heads without tubes are complex and multifaceted, influenced by material properties, tool geometry, and process conditions. Understanding these characteristics is crucial for optimizing the process parameters and achieving high-quality finished parts. The calculation of spinning pressure provides valuable insights into the forces involved and helps in selecting appropriate materials and process conditions.
Further research is needed to explore the deformation characteristics and spinning pressure for a wider range of materials and process conditions. Advanced simulation tools and experimental studies can provide deeper insights, leading to improved process design and optimization.
Maximize Tooling and CNC Metal Spinning Capabilities.
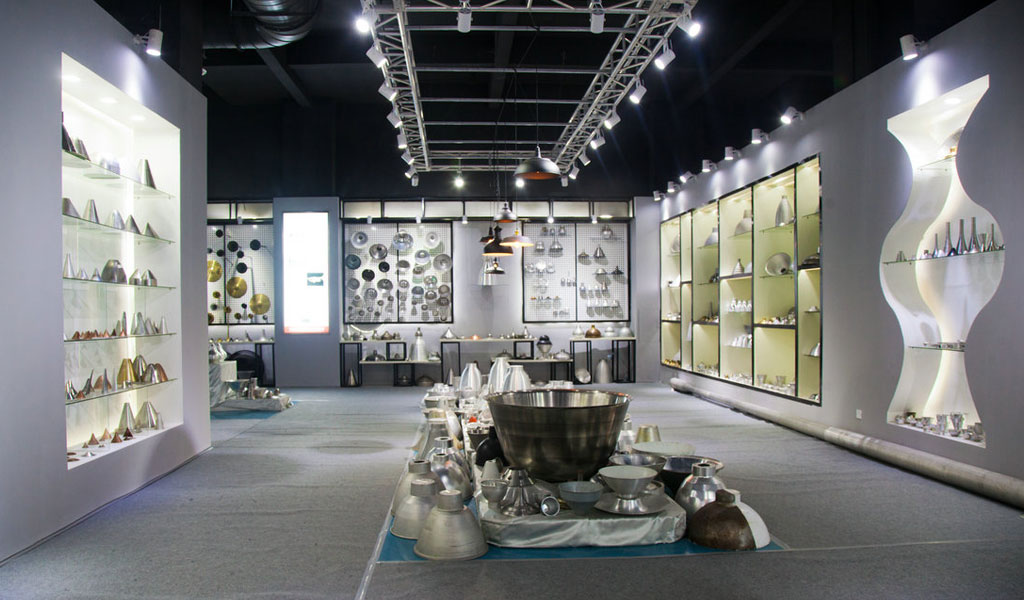
At BE-CU China Metal Spinning company, we make the most of our equipment while monitoring signs of excess wear and stress. In addition, we look into newer, modern equipment and invest in those that can support or increase our manufacturing capabilities. Our team is very mindful of our machines and tools, so we also routinely maintain them to ensure they don’t negatively impact your part’s quality and productivity.
Talk to us today about making a rapid prototype with our CNC metal spinning service. Get a direct quote by chatting with us here or request a free project review.
BE-CU China CNC Metal Spinning service include : CNC Metal Spinning,Metal Spinning Die,Laser Cutting, Tank Heads Spinning,Metal Hemispheres Spinning,Metal Cones Spinning,Metal Dish-Shaped Spinning,Metal Trumpet Spinning,Metal Venturi Spinning,Aluminum Spinning Products,Stainless Steel Spinning Products,Copper Spinning Products,Brass Spinning Products,Steel Spinning Product,Metal Spinnin LED Reflector,Metal Spinning Pressure Vessel,