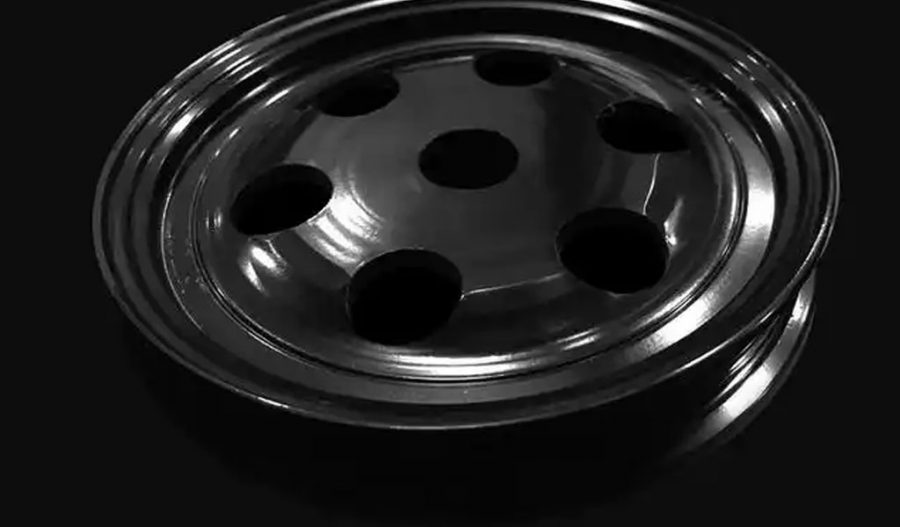
The process of 30CrMnSiA steel thin-walled tube staggered spinning is a specialized manufacturing technique that has garnered significant attention in the field of materials science and engineering. This technique involves the deformation of thin-walled tubes through a series of controlled spinning operations, resulting in high-precision, high-strength components. The 30CrMnSiA steel, known for its excellent mechanical properties and corrosion resistance, is particularly suited for applications requiring durability and precision. This article delves into the intricacies of the staggered spinning process, its applications, and the extensive research conducted to optimize this technique.
Historical Background
The development of spinning processes can be traced back to the early 20th century, with significant advancements made during the industrial revolution. Traditional spinning methods involved the use of manual lathes and simple tooling. However, with the advent of computer numerical control (CNC) machines and advanced materials, the spinning process has evolved into a highly precise and automated operation. The staggered spinning technique, in particular, has emerged as a cutting-edge method for producing thin-walled tubes with complex geometries.
Material Properties of 30CrMnSiA Steel
30CrMnSiA steel is a high-strength, low-alloy steel characterized by its excellent mechanical properties and good weldability. The chemical composition of 30CrMnSiA steel typically includes:
- Carbon (C): 0.28-0.34%
- Manganese (Mn): 0.80-1.10%
- Silicon (Si): 0.80-1.10%
- Chromium (Cr): 0.80-1.10%
- Nickel (Ni): 0.25% max
- Phosphorus (P): 0.035% max
- Sulfur (S): 0.035% max
The mechanical properties of 30CrMnSiA steel are summarized in Table 1:
Property | Value |
---|---|
Yield Strength (MPa) | 830-980 |
Tensile Strength (MPa) | 980-1180 |
Elongation (%) | 12-18 |
Hardness (HB) | 285-341 |
Impact Toughness (J) | 40-60 |
Staggered Spinning Process
The staggered spinning process involves the controlled deformation of a thin-walled tube through a series of spinning operations. The process can be broken down into several key stages:
- Preparation: The initial tube is prepared by cutting it to the desired length and ensuring that the ends are square and free of burrs.
- Heating: The tube is heated to a specific temperature to facilitate plastic deformation. The heating process is carefully controlled to avoid overheating, which can lead to material degradation.
- Spinning: The heated tube is placed on a spinning mandrel and rotated at high speeds. A series of rollers are used to apply pressure to the tube, gradually deforming it into the desired shape.
- Cooling: After the spinning operation, the tube is cooled to room temperature to stabilize its structure.
- Finishing: The final tube is inspected for dimensional accuracy and surface finish. Any necessary finishing operations, such as polishing or grinding, are performed to achieve the desired quality.
Research on Staggered Spinning
Extensive research has been conducted to optimize the staggered spinning process for 30CrMnSiA steel thin-walled tubes. Key areas of research include:
1. Thermal Analysis
Thermal analysis is crucial for understanding the temperature distribution and heat transfer during the spinning process. Researchers have employed finite element analysis (FEA) to simulate the thermal behavior of the tube during spinning. The results have shown that maintaining a uniform temperature distribution is essential for achieving consistent material properties and dimensional accuracy.
2. Mechanical Deformation
The mechanical deformation of the tube during spinning is a complex process involving plastic flow and strain hardening. Research has focused on optimizing the spinning parameters, such as roller pressure, rotation speed, and feed rate, to minimize residual stresses and ensure uniform deformation. Table 2 summarizes the key findings from mechanical deformation studies:
Parameter | Optimal Range | Effect on Deformation |
---|---|---|
Roller Pressure | 50-70 MPa | Uniform deformation, reduced residual stresses |
Rotation Speed | 1000-1500 rpm | Improved surface finish, reduced defects |
Feed Rate | 0.5-1.0 mm/rev | Controlled deformation, minimized thinning |
3. Microstructural Analysis
Microstructural analysis has been conducted to understand the changes in the material’s microstructure during the spinning process. Researchers have used scanning electron microscopy (SEM) and transmission electron microscopy (TEM) to examine the grain structure and dislocation density. The findings have indicated that the spinning process can lead to grain refinement and increased dislocation density, which contribute to the enhanced mechanical properties of the spun tube.
4. Fatigue and Fracture Behavior
The fatigue and fracture behavior of spun tubes have been extensively studied to ensure their reliability in service. Research has shown that the staggered spinning process can improve the fatigue life of the tubes by reducing the number of defects and improving the surface finish. Fracture toughness tests have also indicated that the spun tubes exhibit superior resistance to crack propagation compared to conventionally manufactured tubes.
Applications of Staggered Spinning
The staggered spinning process for 30CrMnSiA steel thin-walled tubes has a wide range of applications in various industries, including:
- Aerospace: The high strength-to-weight ratio and excellent fatigue resistance of spun tubes make them ideal for aerospace applications, such as aircraft landing gear and structural components.
- Automotive: The automotive industry benefits from the precision and durability of spun tubes, which are used in components like drive shafts and suspension systems.
- Energy: In the energy sector, spun tubes are used in high-pressure piping systems and heat exchangers, where their corrosion resistance and mechanical strength are critical.
- Medical: The medical industry utilizes spun tubes in the manufacture of surgical instruments and implants, where precision and biocompatibility are essential.
Case Studies
Several case studies have been conducted to demonstrate the practical applications and benefits of the staggered spinning process. One notable case study involved the production of high-precision drive shafts for an automotive manufacturer. The study compared the performance of conventionally manufactured drive shafts with those produced using the staggered spinning process. The results, summarized in Table 3, highlighted the superior performance of the spun drive shafts:
Parameter | Conventional Drive Shafts | Spun Drive Shafts |
---|---|---|
Dimensional Accuracy | ±0.5 mm | ±0.1 mm |
Surface Finish | Ra 1.6 μm | Ra 0.8 μm |
Fatigue Life | 10^5 cycles | 10^6 cycles |
Weight Reduction | None | 15% |
Future Directions
The future of the staggered spinning process for 30CrMnSiA steel thin-walled tubes holds great promise. Ongoing research is focused on further optimizing the process parameters, developing new tooling materials, and integrating advanced automation technologies. Additionally, the exploration of hybrid manufacturing techniques, combining spinning with other processes like additive manufacturing, offers exciting possibilities for creating complex, high-performance components.
Conclusion
The staggered spinning process for 30CrMnSiA steel thin-walled tubes represents a significant advancement in manufacturing technology. Through extensive research and development, this process has been optimized to produce high-precision, high-strength components with superior mechanical properties. The applications of this technique span various industries, from aerospace to medical, highlighting its versatility and potential. As research continues, the staggered spinning process is poised to play an increasingly important role in the future of advanced manufacturing.
Maximize Tooling and CNC Metal Spinning Capabilities.
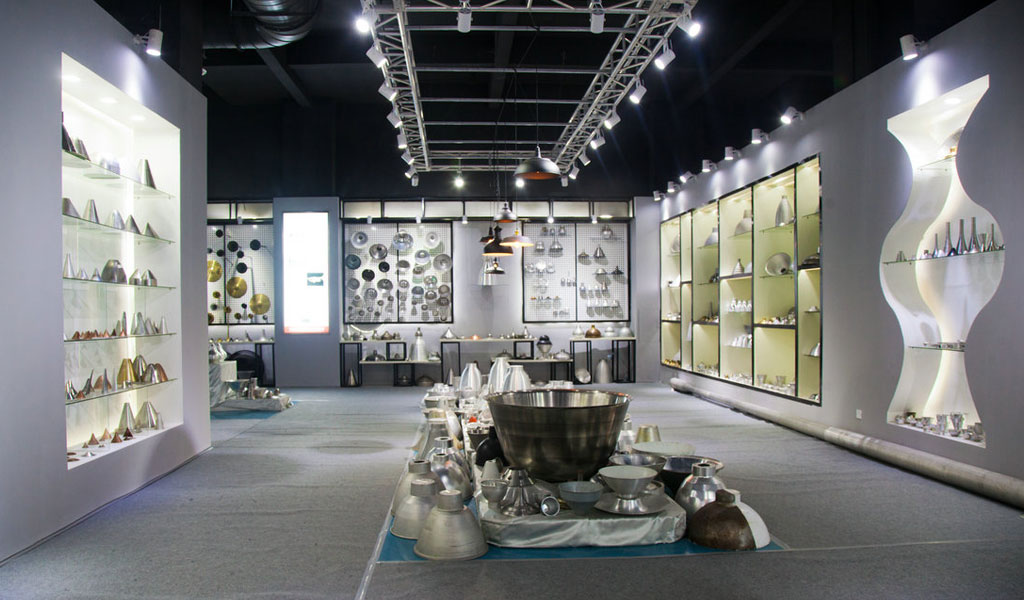
At BE-CU China Metal Spinning company, we make the most of our equipment while monitoring signs of excess wear and stress. In addition, we look into newer, modern equipment and invest in those that can support or increase our manufacturing capabilities. Our team is very mindful of our machines and tools, so we also routinely maintain them to ensure they don’t negatively impact your part’s quality and productivity.
Talk to us today about making a rapid prototype with our CNC metal spinning service. Get a direct quote by chatting with us here or request a free project review.
BE-CU China CNC Metal Spinning service include : CNC Metal Spinning,Metal Spinning Die,Laser Cutting, Tank Heads Spinning,Metal Hemispheres Spinning,Metal Cones Spinning,Metal Dish-Shaped Spinning,Metal Trumpet Spinning,Metal Venturi Spinning,Aluminum Spinning Products,Stainless Steel Spinning Products,Copper Spinning Products,Brass Spinning Products,Steel Spinning Product,Metal Spinnin LED Reflector,Metal Spinning Pressure Vessel,