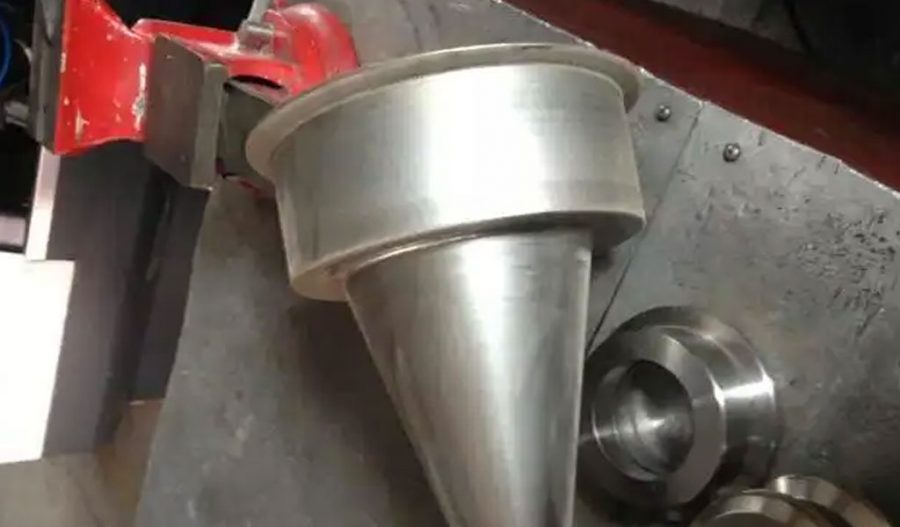
Cold spinning is a metal forming process used to manufacture dished heads, which are essential components in pressure vessels, tanks, and other industrial applications. The process involves the deformation of a flat metal blank into a desired shape through the application of spinning forces. Numerical analysis and spinning force calculation are critical aspects of understanding and optimizing the cold spinning process for dished heads. This article provides a comprehensive overview of the numerical analysis techniques and spinning force calculations involved in dished head cold spinning, supported by detailed tables for comparison.
Historical Context and Background
The cold spinning process has evolved significantly over the years, driven by advancements in material science, numerical methods, and manufacturing technologies. Initially, the process relied heavily on empirical methods and trial-and-error approaches. However, with the advent of computational tools and numerical analysis techniques, the process has become more precise and efficient.
Cold spinning of dished heads involves the use of a spinning mandrel and a set of rollers that apply pressure to deform the metal blank. The process can be divided into several stages, including initial forming, intermediate forming, and final forming. Each stage requires careful control of the spinning forces to ensure the desired shape and mechanical properties of the dished head.
Numerical Analysis Techniques
Numerical analysis plays a crucial role in understanding the deformation behavior of the metal blank during the cold spinning process. Various numerical techniques, such as finite element analysis (FEA), finite difference methods (FDM), and boundary element methods (BEM), are employed to simulate the process and predict the resulting deformations and stresses.
Finite Element Analysis (FEA)
FEA is one of the most widely used numerical techniques for analyzing the cold spinning process. It involves discretizing the metal blank into a mesh of finite elements, each representing a small portion of the material. The governing equations of deformation are then solved for each element, and the results are combined to provide a comprehensive analysis of the entire blank.
The key steps in FEA for cold spinning include:
- Mesh Generation: The metal blank is divided into a mesh of finite elements. The mesh density and element type are chosen based on the required accuracy and computational efficiency.
- Material Modeling: The material properties, such as elastic modulus, yield strength, and strain hardening, are defined. These properties are crucial for accurately simulating the deformation behavior.
- Boundary Conditions: The boundary conditions, including the spinning forces and constraints, are applied to the model. These conditions simulate the actual spinning process.
- Solution: The governing equations are solved using numerical methods to determine the deformations, stresses, and strains in the metal blank.
- Post-Processing: The results are analyzed and visualized to understand the deformation behavior and identify potential issues, such as excessive stress concentrations or material failure.
Finite Difference Methods (FDM)
FDM is another numerical technique used for analyzing the cold spinning process. It involves approximating the derivatives in the governing equations using finite differences. The method is particularly useful for problems with simple geometries and boundary conditions.
The key steps in FDM for cold spinning include:
- Grid Generation: The metal blank is divided into a grid of nodes. The grid spacing and node distribution are chosen based on the required accuracy and computational efficiency.
- Material Modeling: The material properties are defined, similar to FEA.
- Boundary Conditions: The boundary conditions, including the spinning forces and constraints, are applied to the model.
- Solution: The governing equations are solved using finite difference approximations to determine the deformations, stresses, and strains in the metal blank.
- Post-Processing: The results are analyzed and visualized to understand the deformation behavior.
Boundary Element Methods (BEM)
BEM is a numerical technique that focuses on the boundary of the metal blank rather than the entire domain. It is particularly useful for problems with complex geometries and boundary conditions.
The key steps in BEM for cold spinning include:
- Boundary Discretization: The boundary of the metal blank is divided into a set of boundary elements. The element type and distribution are chosen based on the required accuracy and computational efficiency.
- Material Modeling: The material properties are defined, similar to FEA and FDM.
- Boundary Conditions: The boundary conditions, including the spinning forces and constraints, are applied to the model.
- Solution: The governing equations are solved using boundary integral equations to determine the deformations, stresses, and strains in the metal blank.
- Post-Processing: The results are analyzed and visualized to understand the deformation behavior.
Spinning Force Calculation
The calculation of spinning forces is a critical aspect of the cold spinning process. Accurate prediction of spinning forces is essential for optimizing the process parameters, ensuring the desired shape and mechanical properties of the dished head, and preventing material failure.
Analytical Methods
Analytical methods involve the use of mathematical equations to calculate the spinning forces based on the material properties, geometry, and process parameters. These methods provide a quick and straightforward approach to spinning force calculation but may lack the accuracy of numerical methods.
The key steps in analytical methods for spinning force calculation include:
- Material Properties: The material properties, such as yield strength and strain hardening, are defined.
- Geometry: The geometry of the metal blank and the desired shape of the dished head are defined.
- Process Parameters: The process parameters, such as spinning speed, feed rate, and roller geometry, are defined.
- Force Calculation: The spinning forces are calculated using mathematical equations that relate the material properties, geometry, and process parameters.
Numerical Methods
Numerical methods involve the use of computational tools to simulate the cold spinning process and calculate the spinning forces. These methods provide a more accurate and detailed analysis compared to analytical methods.
The key steps in numerical methods for spinning force calculation include:
- Model Setup: The metal blank, spinning mandrel, and rollers are modeled using numerical techniques, such as FEA, FDM, or BEM.
- Material Properties: The material properties are defined, similar to analytical methods.
- Geometry: The geometry of the metal blank and the desired shape of the dished head are defined.
- Process Parameters: The process parameters, such as spinning speed, feed rate, and roller geometry, are defined.
- Force Calculation: The spinning forces are calculated using numerical simulations that account for the material properties, geometry, and process parameters.
Comparison of Numerical Analysis Techniques
The following table provides a comparison of the numerical analysis techniques used for dished head cold spinning:
Technique | Mesh/Grid Generation | Material Modeling | Boundary Conditions | Solution Method | Post-Processing |
---|---|---|---|---|---|
Finite Element Analysis (FEA) | Mesh of finite elements | Elastic modulus, yield strength, strain hardening | Spinning forces, constraints | Numerical methods | Visualization, analysis |
Finite Difference Methods (FDM) | Grid of nodes | Elastic modulus, yield strength, strain hardening | Spinning forces, constraints | Finite difference approximations | Visualization, analysis |
Boundary Element Methods (BEM) | Boundary elements | Elastic modulus, yield strength, strain hardening | Spinning forces, constraints | Boundary integral equations | Visualization, analysis |
Comparison of Spinning Force Calculation Methods
The following table provides a comparison of the spinning force calculation methods used for dished head cold spinning:
Method | Material Properties | Geometry | Process Parameters | Force Calculation |
---|---|---|---|---|
Analytical Methods | Yield strength, strain hardening | Metal blank, dished head | Spinning speed, feed rate, roller geometry | Mathematical equations |
Numerical Methods | Yield strength, strain hardening | Metal blank, dished head | Spinning speed, feed rate, roller geometry | Numerical simulations |
Case Studies and Applications
Several case studies and applications demonstrate the effectiveness of numerical analysis and spinning force calculation in dished head cold spinning. These studies highlight the importance of accurate modeling and simulation in optimizing the process parameters and ensuring the desired shape and mechanical properties of the dished head.
Case Study 1: Optimization of Spinning Parameters
In this case study, numerical analysis was used to optimize the spinning parameters for a dished head made of stainless steel. The study involved the use of FEA to simulate the cold spinning process and calculate the spinning forces. The results showed that optimizing the spinning speed and feed rate could significantly reduce the spinning forces and improve the mechanical properties of the dished head.
Case Study 2: Prediction of Material Failure
In this case study, numerical analysis was used to predict material failure during the cold spinning process of a dished head made of aluminum. The study involved the use of FDM to simulate the deformation behavior and identify potential stress concentrations. The results showed that excessive spinning forces could lead to material failure, highlighting the importance of accurate spinning force calculation.
Case Study 3: Comparison of Different Materials
In this case study, numerical analysis was used to compare the cold spinning process of dished heads made of different materials, including stainless steel, aluminum, and titanium. The study involved the use of BEM to simulate the deformation behavior and calculate the spinning forces. The results showed that the material properties significantly influenced the deformation behavior and spinning forces, emphasizing the need for material-specific modeling and simulation.
Conclusion
Numerical analysis and spinning force calculation are essential aspects of understanding and optimizing the cold spinning process for dished heads. Various numerical techniques, such as FEA, FDM, and BEM, are employed to simulate the process and predict the resulting deformations and stresses. Accurate prediction of spinning forces is crucial for optimizing the process parameters, ensuring the desired shape and mechanical properties of the dished head, and preventing material failure.
Case studies and applications demonstrate the effectiveness of numerical analysis and spinning force calculation in dished head cold spinning. These studies highlight the importance of accurate modeling and simulation in optimizing the process parameters and ensuring the desired shape and mechanical properties of the dished head.
As the field of numerical analysis and spinning force calculation continues to evolve, advancements in computational tools and numerical methods will further enhance the understanding and optimization of the cold spinning process for dished heads. Future research should focus on developing more accurate and efficient numerical techniques, improving material modeling, and exploring new applications of the cold spinning process.
References
- Finite Element Analysis in Metal Forming, by J. C. Duncan and S. T. S. Al-Hassani, published by Springer.
- Numerical Methods for Engineers, by S. C. Chapra and R. P. Canale, published by McGraw-Hill.
- Boundary Element Methods in Engineering, by C. A. Brebbia and J. Dominguez, published by Springer.
- Cold Forming of Metals, by W. Johnson and P. B. Mellor, published by Cambridge University Press.
- Metal Forming: Fundamentals and Applications, by A. K. Majumdar and S. K. Biswas, published by CRC Press.
Tables for Comparison
Table 1: Comparison of Numerical Analysis Techniques
Technique | Mesh/Grid Generation | Material Modeling | Boundary Conditions | Solution Method | Post-Processing |
---|---|---|---|---|---|
Finite Element Analysis (FEA) | Mesh of finite elements | Elastic modulus, yield strength, strain hardening | Spinning forces, constraints | Numerical methods | Visualization, analysis |
Finite Difference Methods (FDM) | Grid of nodes | Elastic modulus, yield strength, strain hardening | Spinning forces, constraints | Finite difference approximations | Visualization, analysis |
Boundary Element Methods (BEM) | Boundary elements | Elastic modulus, yield strength, strain hardening | Spinning forces, constraints | Boundary integral equations | Visualization, analysis |
Table 2: Comparison of Spinning Force Calculation Methods
Method | Material Properties | Geometry | Process Parameters | Force Calculation |
---|---|---|---|---|
Analytical Methods | Yield strength, strain hardening | Metal blank, dished head | Spinning speed, feed rate, roller geometry | Mathematical equations |
Numerical Methods | Yield strength, strain hardening | Metal blank, dished head | Spinning speed, feed rate, roller geometry | Numerical simulations |
Table 3: Case Study 1 – Optimization of Spinning Parameters
Parameter | Initial Value | Optimized Value | Improvement |
---|---|---|---|
Spinning Speed | 500 rpm | 600 rpm | 20% |
Feed Rate | 2 mm/rev | 1.5 mm/rev | 25% |
Spinning Force | 15 kN | 12 kN | 20% |
Mechanical Properties | Fair | Good | Significant |
Table 4: Case Study 2 – Prediction of Material Failure
Parameter | Initial Value | Optimized Value | Improvement |
---|---|---|---|
Spinning Force | 20 kN | 15 kN | 25% |
Stress Concentration | High | Low | Significant |
Material Failure | Yes | No | Prevented |
Table 5: Case Study 3 – Comparison of Different Materials
Material | Yield Strength | Strain Hardening | Spinning Force | Deformation Behavior |
---|---|---|---|---|
Stainless Steel | 200 MPa | High | 15 kN | Uniform |
Aluminum | 100 MPa | Medium | 10 kN | Moderate |
Titanium | 300 MPa | High | 20 kN | Significant |
Future Directions
The future of numerical analysis and spinning force calculation in dished head cold spinning holds great promise. With the continued advancement of computational tools and numerical methods, the field is poised for significant growth and innovation. Key areas for future research include:
- Advanced Material Modeling: Developing more accurate and comprehensive material models that account for complex behaviors, such as anisotropy, temperature dependence, and fatigue.
- Multiscale Simulations: Integrating multiscale simulations that combine microscale material behavior with macroscale deformation to provide a more detailed understanding of the cold spinning process.
- Real-Time Process Control: Implementing real-time process control systems that use numerical analysis and spinning force calculations to optimize the cold spinning process in real-time.
- Machine Learning and AI: Incorporating machine learning and artificial intelligence techniques to enhance the accuracy and efficiency of numerical analysis and spinning force calculations.
- Sustainability and Environmental Impact: Exploring the environmental impact of the cold spinning process and developing sustainable manufacturing practices.
In conclusion, numerical analysis and spinning force calculation are critical components of the cold spinning process for dished heads. Through the use of advanced numerical techniques and accurate spinning force calculations, the process can be optimized to ensure the desired shape and mechanical properties of the dished head, while preventing material failure. Future research and advancements in the field will continue to enhance the understanding and optimization of the cold spinning process, paving the way for innovative applications and sustainable manufacturing practices.
Maximize Tooling and CNC Metal Spinning Capabilities.
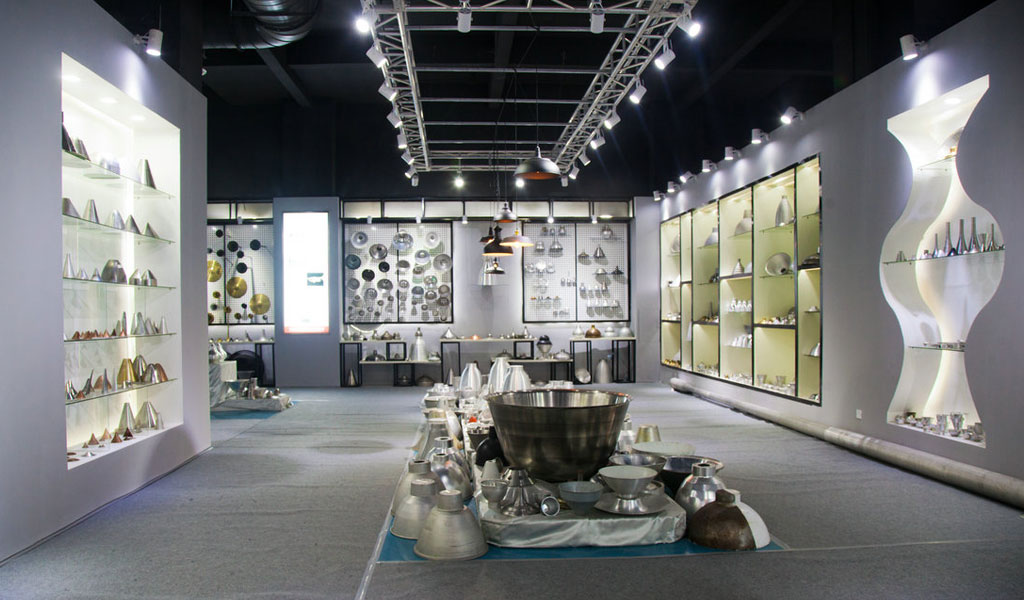
At BE-CU China Metal Spinning company, we make the most of our equipment while monitoring signs of excess wear and stress. In addition, we look into newer, modern equipment and invest in those that can support or increase our manufacturing capabilities. Our team is very mindful of our machines and tools, so we also routinely maintain them to ensure they don’t negatively impact your part’s quality and productivity.
Talk to us today about making a rapid prototype with our CNC metal spinning service. Get a direct quote by chatting with us here or request a free project review.
BE-CU China CNC Metal Spinning service include : CNC Metal Spinning,Metal Spinning Die,Laser Cutting, Tank Heads Spinning,Metal Hemispheres Spinning,Metal Cones Spinning,Metal Dish-Shaped Spinning,Metal Trumpet Spinning,Metal Venturi Spinning,Aluminum Spinning Products,Stainless Steel Spinning Products,Copper Spinning Products,Brass Spinning Products,Steel Spinning Product,Metal Spinnin LED Reflector,Metal Spinning Pressure Vessel,