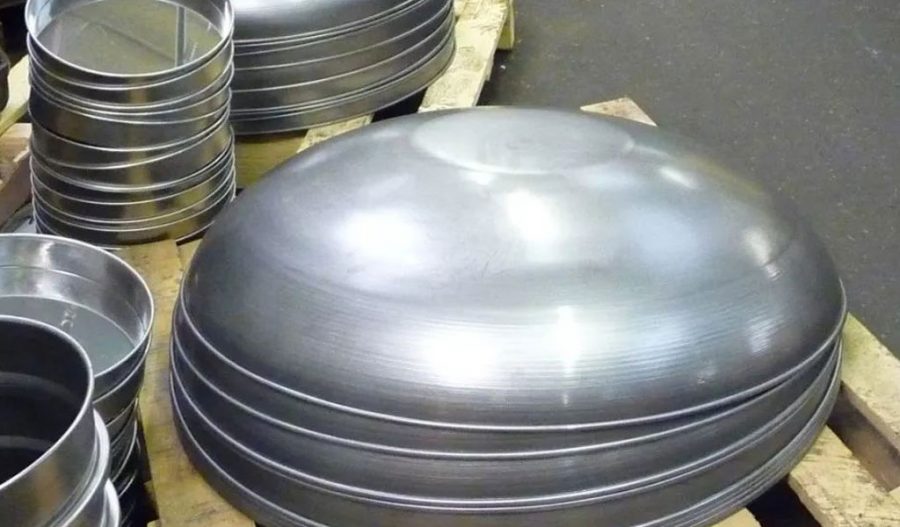
Metal spinning, also known as spin forming or spinning, is a metalworking process by which a disc or tube of metal is rotated at high speed and formed into an axially symmetric part. This technique, which dates back centuries, has evolved significantly with advancements in technology and materials science, making it a critical method in modern bulk handling applications. In the context of bulk handling, metal spinning is employed to fabricate components such as containers, hoppers, silos, and chutes that are integral to industries like agriculture, mining, pharmaceuticals, and food processing. This article delves into the principles, processes, materials, applications, and scientific underpinnings of metal spinning as it pertains to bulk handling, providing a comprehensive exploration of its relevance in industrial systems.
The origins of metal spinning can be traced to ancient civilizations, where artisans manually shaped metal using rudimentary tools. However, its modern industrial application emerged during the 19th century with the advent of mechanized lathes and the growing demand for precision-engineered components. In bulk handling, where large volumes of granular, powdered, or liquid materials must be stored, transported, or processed, the durability, customization, and cost-effectiveness of spun metal parts make them indispensable. The process involves securing a metal blank—typically a flat circular sheet or pre-formed tube—onto a spinning lathe, where it is rotated at high speeds while a tool, often a roller or mandrel, applies pressure to shape the metal over a form or mold. This results in seamless, robust structures capable of withstanding the mechanical stresses and environmental conditions encountered in bulk handling systems.
Fundamentally, metal spinning relies on the principles of plastic deformation, where the metal is stretched and compressed beyond its yield strength but below its ultimate tensile strength. This allows the material to flow into the desired shape without fracturing. The process can be categorized into three primary types: conventional spinning, shear spinning, and tube spinning. Conventional spinning, the most common method, involves gradually forming the metal over a mandrel without significantly altering its thickness. Shear spinning, by contrast, reduces the thickness of the workpiece while increasing its diameter, making it suitable for creating conical or tapered components like hoppers. Tube spinning, meanwhile, is used to elongate or thin tubular sections, often employed in the production of cylindrical silos or pipes for bulk material transport.
In bulk handling, the choice of spinning technique depends on the specific requirements of the component. For instance, hoppers—funnel-shaped containers used to dispense bulk materials—benefit from shear spinning due to their tapered geometry, which facilitates the controlled flow of materials such as grains, powders, or aggregates. Silos, which store large quantities of bulk solids, often require conventional spinning to produce seamless cylindrical bodies that resist internal pressure and corrosion. The adaptability of metal spinning allows engineers to tailor components to the physical properties of the handled materials, such as particle size, density, abrasiveness, and moisture content, ensuring optimal performance in real-world applications.
The materials used in metal spinning for bulk handling are selected based on their mechanical properties, corrosion resistance, and compatibility with the processed substances. Common metals include stainless steel, carbon steel, aluminum, and copper alloys, each offering distinct advantages. Stainless steel, for example, is prized for its durability and resistance to rust, making it ideal for food-grade or chemical bulk handling systems where hygiene and contamination prevention are paramount. Carbon steel, being stronger and more cost-effective, is frequently used in heavy-duty applications like mining or construction material handling. Aluminum, with its lightweight and corrosion-resistant properties, suits systems where weight reduction is a priority, such as portable silos or transport containers. Copper alloys, though less common, are employed in specialized applications requiring high thermal conductivity or antimicrobial properties.
The scientific basis of metal spinning involves a complex interplay of material science, mechanics, and thermodynamics. During the spinning process, the metal undergoes significant strain, which alters its microstructure. Cold working, as occurs in most spinning operations, increases the metal’s hardness and strength through dislocation density increases within the crystal lattice. However, excessive deformation can lead to work hardening, raising the risk of cracking or fatigue failure. To mitigate this, some applications employ hot spinning, where the metal is heated to reduce its yield strength and enhance ductility. The temperature, spinning speed, and tool pressure must be precisely controlled to achieve the desired shape and properties, a process informed by finite element analysis (FEA) and computational modeling in modern engineering.
In bulk handling systems, the design of spun metal components must account for the dynamic behavior of the materials they contain. Granular materials, for instance, exhibit complex flow patterns influenced by factors such as angle of repose, cohesion, and friction. Hoppers must be engineered with steep enough walls to prevent bridging—where material forms an arch and blocks flow—or rat-holing, where a narrow channel empties while leaving material stagnant along the walls. Metal spinning enables the creation of smooth, seamless surfaces that minimize friction and wear, enhancing flow efficiency. Computational fluid dynamics (CFD) and discrete element modeling (DEM) are often used to simulate material behavior and optimize component geometry, underscoring the scientific rigor behind these applications.
The advantages of metal spinning in bulk handling are manifold. Unlike welded or riveted assemblies, spun components lack seams or joints that could weaken under stress or harbor contaminants, making them exceptionally robust and hygienic. The process also allows for rapid prototyping and production, reducing lead times compared to casting or forging. Furthermore, metal spinning is highly versatile, accommodating a wide range of sizes—from small pharmaceutical containers to massive industrial silos—without requiring extensive retooling. This scalability is particularly valuable in bulk handling, where systems must adapt to varying throughput demands across industries.
However, metal spinning is not without challenges. The process demands skilled operators or advanced CNC (computer numerical control) systems to ensure precision, especially for complex geometries. Material waste can also be a concern, as the initial blank must be larger than the final part, with excess trimmed away. In bulk handling applications, where components may be exposed to abrasive materials or harsh environments, surface treatments like galvanizing, powder coating, or polishing are often applied post-spinning to enhance durability. These additional steps, while increasing costs, are justified by the extended service life they confer.
To illustrate the practical applications of metal spinning in bulk handling, consider the agricultural sector. Grain silos, a staple of modern farming, are frequently produced via metal spinning due to their cylindrical shape and need for airtight seals. These silos must withstand the weight of thousands of tons of grain, resist corrosion from moisture, and prevent pest ingress—all requirements met by spun stainless or galvanized steel. Similarly, in the mining industry, conical chutes spun from carbon steel direct ore or coal into processing equipment, their tapered design minimizing clogging and wear. The pharmaceutical industry, meanwhile, relies on spun stainless steel hoppers to dispense powders in controlled, sterile environments, highlighting the process’s precision and cleanliness.
Comparatively, metal spinning competes with other fabrication methods like stamping, deep drawing, and hydroforming in bulk handling applications. Stamping, which involves pressing a metal sheet into a die, excels in high-volume production but struggles with seamless, deep components. Deep drawing, a related process, can produce hollow shapes but often requires multiple steps and leaves residual stresses. Hydroforming, using high-pressure fluid to shape metal, offers excellent precision but is costlier and slower than spinning. The table below provides a detailed comparison of these methods, emphasizing their suitability for bulk handling components.
Table 1: Comparison of Metal Fabrication Methods for Bulk Handling Components
Parameter | Metal Spinning | Stamping | Deep Drawing | Hydroforming |
---|---|---|---|---|
Geometry | Axially symmetric, seamless | Flat or shallow shapes | Hollow, moderate depth | Complex, seamless |
Wall Thickness | Uniform or tapered (shear spinning) | Uniform | Uniform, may thin at edges | Variable, controlled |
Material Waste | Moderate (trimming required) | Low | Moderate | Low |
Production Speed | Moderate to high | Very high | Moderate | Low to moderate |
Tooling Cost | Low to moderate | High | Moderate to high | High |
Strength | High (seamless) | Moderate (joints possible) | Moderate (residual stress) | High (uniform deformation) |
Applications | Hoppers, silos, chutes | Flat panels, lids | Containers, shallow hoppers | Complex tanks, pipes |
Cost per Unit | Low for small batches | Low for large batches | Moderate | High |
Surface Finish | Smooth, customizable | Good, may require finishing | Good, may show stretch marks | Excellent |
The scientific optimization of metal spinning for bulk handling extends to tool design and process parameters. Tools, typically made of hardened steel or carbide, must withstand the frictional heat and forces of deformation. Their shape—whether rounded, pointed, or flat—affects the material flow and surface finish. Spinning speed, measured in revolutions per minute (RPM), influences heat generation and strain rate, with higher speeds suited to ductile materials like aluminum and lower speeds for brittle ones like high-carbon steel. Lubrication, often with oils or synthetic compounds, reduces friction and tool wear, a critical factor in maintaining precision over long production runs.
In modern manufacturing, CNC spinning lathes have revolutionized the process, offering repeatability and complex programming capabilities. These machines use servo motors and real-time feedback to adjust tool pressure and speed, ensuring uniformity across batches. For bulk handling components, this precision translates to tighter tolerances—typically within ±0.5 mm—essential for mating parts in conveyor systems or ensuring leak-proof seals in silos. The integration of sensors and data analytics further enhances quality control, detecting defects like thinning or cracking during production.
Environmental considerations also play a role in metal spinning for bulk handling. The process generates less waste than casting, where molten metal losses are common, and its energy consumption is lower than forging, which requires heating entire billets. Recycling of scrap metal from trimming is standard practice, aligning with sustainability goals in industries like food processing and agriculture. Moreover, the longevity of spun components reduces replacement frequency, lowering the lifecycle carbon footprint of bulk handling systems.
The future of metal spinning in this field is poised for innovation. Additive manufacturing techniques, such as 3D printing of mandrels, could enable more intricate designs, while hybrid processes combining spinning with laser cutting or welding may expand its capabilities. Research into lightweight alloys and composites, spun into hybrid structures, promises to reduce system weight without sacrificing strength—a boon for mobile bulk handling units. Additionally, advancements in automation and artificial intelligence could further streamline production, predicting optimal parameters based on material properties and component specifications.
To quantify the mechanical performance of spun metal components in bulk handling, consider the following stress analysis. A cylindrical silo of r=2 m r = 2 \, \text{m} r=2m, height h=10 m h = 10 \, \text{m} h=10m, and wall thickness t=5 mm t = 5 \, \text{mm} t=5mm, filled with grain (density ρ=800 kg/m3 \rho = 800 \, \text{kg/m}^3 ρ=800kg/m3), experiences hoop stress (σh \sigma_h σh) due to internal pressure. Using the thin-walled pressure vessel formula:
σh=tp⋅r
where p=ρ⋅g⋅h=800⋅9.81⋅10=78,480Pa, the hoop stress is:
σh=0.00578,480⋅2=31.39MPa
For stainless steel with a yield strength of 200 MPa, this yields a safety factor of 200/31.39≈6.37 200 / 31.39 \approx 6.37 200/31.39≈6.37, well within safe limits. Such calculations, grounded in mechanics, validate the suitability of spun components for demanding applications.
Table 2: Mechanical Properties of Common Spun Metals for Bulk Handling
Material | Yield Strength (MPa) | Tensile Strength (MPa) | Density (kg/m³) | Corrosion Resistance | Typical Use |
---|---|---|---|---|---|
Stainless Steel | 200–300 | 500–700 | 7,900 | Excellent | Food silos, hoppers |
Carbon Steel | 250–400 | 400–600 | 7,850 | Moderate (coated) | Mining chutes, silos |
Aluminum | 90–150 | 150–300 | 2,700 | Good | Portable containers |
Copper Alloys | 100–250 | 300–500 | 8,900 | Excellent | Specialty hoppers |
In conclusion, metal spinning stands as a cornerstone of bulk handling technology, blending historical craftsmanship with cutting-edge science. Its ability to produce seamless, durable, and customizable components addresses the diverse needs of industries managing bulk materials. Through ongoing research and technological refinement, metal spinning will continue to evolve, reinforcing its role in efficient, sustainable industrial systems. This article, spanning the intricacies of the process and its applications, underscores its scientific and practical significance, offering a detailed resource for engineers, researchers, and practitioners alike.
Maximize Tooling and CNC Metal Spinning Capabilities.
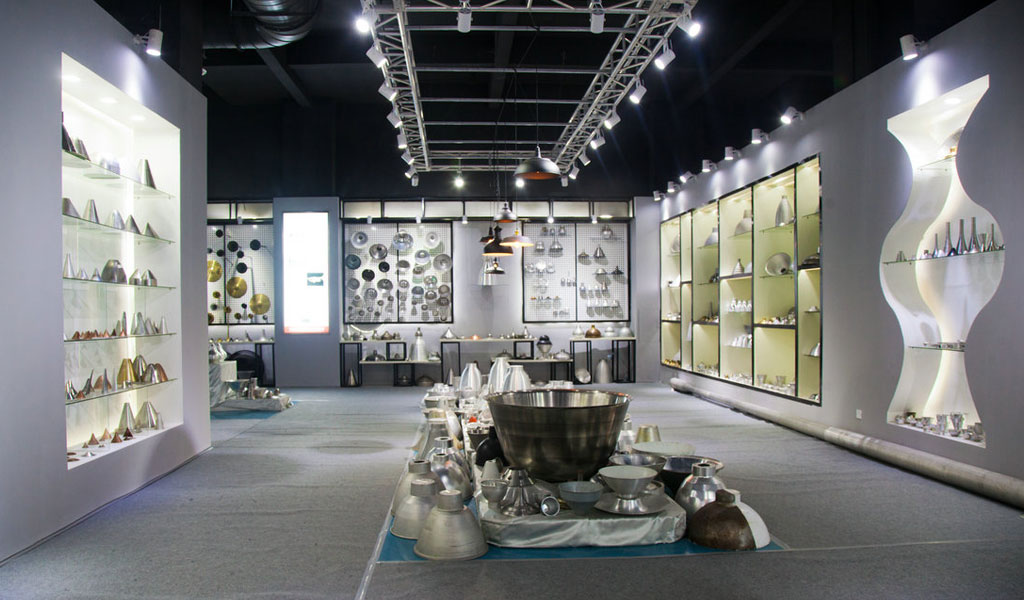
At BE-CU China Metal Spinning company, we make the most of our equipment while monitoring signs of excess wear and stress. In addition, we look into newer, modern equipment and invest in those that can support or increase our manufacturing capabilities. Our team is very mindful of our machines and tools, so we also routinely maintain them to ensure they don’t negatively impact your part’s quality and productivity.
Talk to us today about making a rapid prototype with our CNC metal spinning service. Get a direct quote by chatting with us here or request a free project review.
BE-CU China CNC Metal Spinning service include : CNC Metal Spinning,Metal Spinning Die,Laser Cutting, Tank Heads Spinning,Metal Hemispheres Spinning,Metal Cones Spinning,Metal Dish-Shaped Spinning,Metal Trumpet Spinning,Metal Venturi Spinning,Aluminum Spinning Products,Stainless Steel Spinning Products,Copper Spinning Products,Brass Spinning Products,Steel Spinning Product,Metal Spinnin LED Reflector,Metal Spinning Pressure Vessel,