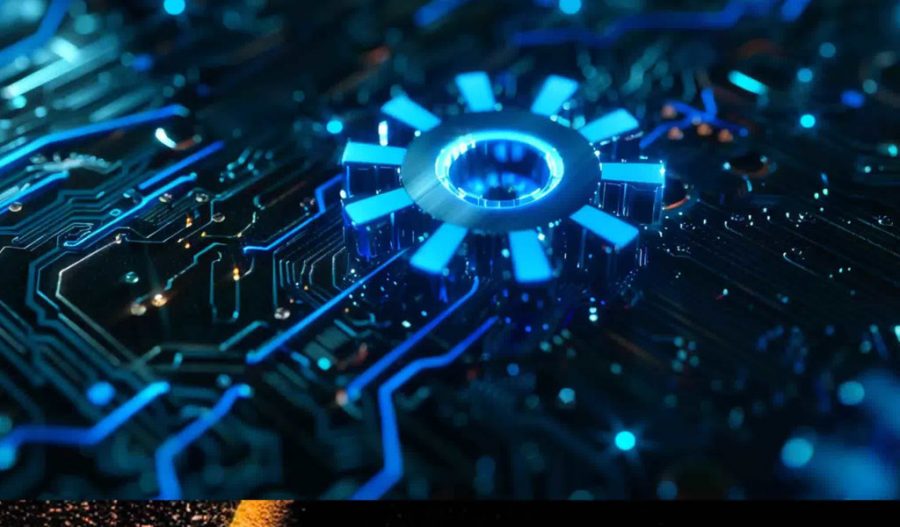
Heating, Ventilation, and Air Conditioning (HVAC) systems are integral to modern building infrastructure, providing thermal comfort and maintaining indoor air quality (IAQ) across residential, commercial, and industrial environments. These systems regulate temperature, humidity, and air purity, ensuring occupant well-being and operational efficiency. The design and implementation of HVAC systems represent a multidisciplinary effort, combining principles of mechanical engineering, thermodynamics, fluid mechanics, and building science. Since their inception in the early 20th century, HVAC technologies have evolved significantly, driven by advancements in energy efficiency, environmental concerns, and the need for sustainable building practices.
The term “HVAC” encompasses three primary functions: heating, which increases ambient temperature; ventilation, which circulates and refreshes air; and air conditioning, which cools and dehumidifies indoor spaces. In some contexts, the abbreviation extends to “HVAC&R” to include refrigeration, reflecting the systems’ broader applications. This article explores the intricate processes of designing and implementing HVAC systems, detailing the components, methodologies, standards, and challenges involved. It also examines historical developments, modern innovations, and comparative analyses of system types, providing a holistic understanding of this critical technology.
Historical Development of HVAC Systems
The origins of HVAC systems can be traced to ancient civilizations, where rudimentary methods addressed heating and ventilation needs. The Romans, for instance, developed the hypocaust, a system of underfloor heating using hot air circulated through channels, demonstrating early ingenuity in thermal regulation. Ventilation, meanwhile, relied on natural airflow through strategically placed openings, a practice seen in Persian windcatchers and medieval European architecture.
The modern HVAC era began in the 19th century with the Industrial Revolution. In 1834, American inventor Jacob Perkins patented the first vapor-compression refrigeration cycle, laying the groundwork for air conditioning. By 1902, Willis Carrier, often dubbed the “father of air conditioning,” designed a system to control humidity in a Brooklyn printing plant, marking the birth of mechanical climate control. Carrier’s innovation used chilled water coils to cool air, a principle still foundational to contemporary systems.
Heating technologies advanced concurrently, with steam and hot-water radiators becoming widespread in the late 19th century. Ventilation gained prominence in the 20th century as public health concerns linked stale air to disease transmission, prompting mechanical solutions like exhaust fans. The integration of these functions into cohesive HVAC systems emerged mid-century, spurred by urbanization and the rise of high-rise buildings requiring centralized climate control.
Today, HVAC systems are governed by standards from organizations like the American Society of Heating, Refrigerating and Air-Conditioning Engineers (ASHRAE), reflecting decades of refinement in design and implementation practices.
Fundamentals of HVAC Design
The design of an HVAC system begins with understanding the building’s purpose, occupancy, and environmental conditions. This process involves calculating heating and cooling loads, selecting appropriate equipment, and ensuring compliance with regulatory codes.
Load Calculation
Load calculation determines the energy required to maintain desired indoor conditions. The process accounts for heat gains and losses from external sources (e.g., solar radiation, outdoor temperature) and internal factors (e.g., occupants, lighting, equipment). ASHRAE provides standardized methods, such as the Cooling Load Temperature Difference (CLTD) and Heat Balance (HB) approaches, to quantify these loads.
For example, a typical office building in a temperate climate might require 20-30 BTU/ft² (British Thermal Units per square foot) for cooling, depending on insulation, window area, and occupancy density. Software tools like Trane TRACE or Carrier HAP automate these calculations, incorporating variables such as:
- Outdoor Design Conditions: Temperature and humidity extremes based on geographic location (e.g., 95°F dry-bulb, 75°F wet-bulb for summer in New York).
- Indoor Design Conditions: Target temperature (e.g., 72°F) and relative humidity (e.g., 50%).
- Building Envelope: Insulation R-values, window U-factors, and air infiltration rates.
System Types and Selection
HVAC systems vary widely, categorized by their medium of heat transfer and distribution method. Common types include:
- All-Air Systems: Deliver conditioned air via ductwork (e.g., Variable Air Volume [VAV], Constant Air Volume [CAV]).
- Air-and-Water Systems: Combine air distribution with hydronic heating/cooling (e.g., fan-coil units).
- All-Water Systems: Use piped water for heat transfer (e.g., radiators, chilled beams).
- Unitary Systems: Self-contained units like rooftop units (RTUs) or split systems.
Selection depends on building size, budget, and performance goals. For instance, VAV systems suit large commercial spaces due to their zoning flexibility, while split systems are cost-effective for residences.
Components of HVAC Systems
Key components include:
- Air Handling Units (AHUs): Mix, filter, and condition air before distribution.
- Chillers and Boilers: Generate cold or hot water for cooling and heating.
- Ductwork and Piping: Transport air or water throughout the building.
- Thermostats and Controls: Regulate system operation, often integrated with Building Management Systems (BMS).
Implementation Process
Implementing an HVAC system involves translating design specifications into a functional installation. This multistage process requires coordination among engineers, contractors, and building owners.
Planning and Pre-Installation
The implementation begins with detailed schematics and mechanical drawings, specifying equipment locations, duct routes, and piping layouts. Contractors assess site conditions, ensuring structural compatibility and access for maintenance. For retrofit projects, existing systems are evaluated for integration or replacement.
Installation of Major Components
Installation starts with major equipment like chillers, boilers, and AHUs, typically placed in mechanical rooms or on rooftops. Proper anchorage and vibration isolation prevent operational noise and wear. Electrical and plumbing connections follow, adhering to codes like the National Electrical Code (NEC) and Uniform Plumbing Code (UPC).
Ductwork and Distribution Systems
Ductwork installation requires precision to minimize pressure losses and ensure airflow balance. Rectangular or round ducts, made of galvanized steel or fiberglass, are sealed to prevent leaks, which can reduce efficiency by up to 20%. Diffusers and registers distribute air evenly, while dampers regulate flow.
Testing and Commissioning
Commissioning verifies system performance against design intent. Tests include airflow measurement (using anemometers), temperature uniformity, and pressure checks. ASHRAE Standard 202 outlines commissioning protocols, ensuring energy efficiency and occupant comfort. For example, a VAV system might be tested to confirm turndown ratios meet specified minima (e.g., 30% of peak flow).
Energy Efficiency and Sustainability
Energy efficiency is a cornerstone of modern HVAC design, driven by rising utility costs and environmental regulations. Buildings account for approximately 40% of global energy consumption, with HVAC systems comprising half of that share in many cases.
Strategies for Efficiency
- High-Efficiency Equipment: ENERGY STAR-rated units, such as variable-speed compressors, reduce power usage.
- Heat Recovery: Systems like Energy Recovery Ventilators (ERVs) transfer heat between exhaust and incoming air, cutting heating/cooling demands by 20-30%.
- Insulation and Sealing: Enhanced building envelopes and duct insulation minimize thermal losses.
Renewable Integration
Solar-powered HVAC, geothermal heat pumps, and district heating/cooling networks exemplify sustainable trends. Geothermal systems, for instance, leverage stable ground temperatures (around 55°F) to achieve Coefficients of Performance (COP) exceeding 4.0, compared to 3.0 for conventional air-source heat pumps.
Regulatory Standards
Standards like ASHRAE 90.1 (Energy Standard for Buildings) mandate minimum efficiency levels, such as Seasonal Energy Efficiency Ratios (SEER) of 13-15 for residential units. Compliance ensures reduced carbon footprints and operational costs.
Indoor Air Quality (IAQ) Considerations
IAQ profoundly impacts health and productivity, with HVAC systems serving as the “respiratory system” of buildings. Poorly designed or maintained systems can exacerbate issues like mold growth or volatile organic compound (VOC) accumulation.
Ventilation Standards
ASHRAE Standard 62.1 specifies ventilation rates, such as 15-20 cubic feet per minute (cfm) per person in offices, to dilute contaminants. Natural ventilation supplements mechanical systems in mild climates, though it’s less controllable.
Filtration and Purification
Filters, rated by Minimum Efficiency Reporting Value (MERV), remove particulates; MERV 13 filters, for example, capture 90% of particles 1-3 microns in size, including some viruses. Advanced technologies like UV-C lights and bipolar ionization further neutralize pathogens.
Humidity Control
Maintaining 30-50% relative humidity prevents microbial growth and static buildup. Dehumidifiers and humidifiers, integrated into HVAC systems, achieve this balance, particularly in healthcare or industrial settings.
Challenges in HVAC Design and Implementation
Designing and installing HVAC systems presents numerous challenges, from technical complexities to economic constraints.
Spatial Constraints
In dense urban environments, limited mechanical room space complicates equipment placement. Modular or decentralized systems, like ductless mini-splits, address this by reducing footprint.
Cost Management
Initial costs for high-efficiency systems can be steep; a commercial VAV system might exceed $50/ft² versus $20/ft² for a basic RTU. Lifecycle cost analyses, factoring in energy savings, justify these investments.
Maintenance and Longevity
Regular maintenance—filter replacement, coil cleaning, refrigerant checks—extends system life (typically 15-20 years) but requires skilled labor. Neglect can halve efficiency and trigger failures.
Comparative Analysis of HVAC Systems
The following tables compare major HVAC system types across key metrics, aiding designers and implementers in selection.
Table 1: System Type Comparison
System Type | Application | Efficiency (COP) | Initial Cost ($/ft²) | Maintenance Complexity | IAQ Impact |
---|---|---|---|---|---|
All-Air (VAV) | Large commercial | 3.5-4.0 | 40-60 | High | Excellent (zoned) |
All-Air (CAV) | Small commercial | 3.0-3.5 | 30-45 | Moderate | Good |
Air-and-Water | Mixed-use buildings | 3.2-3.8 | 35-50 | Moderate | Very Good |
All-Water (Chilled Beam) | Offices, hospitals | 4.0-4.5 | 45-65 | Low | Excellent |
Unitary (Split System) | Residential | 3.0-3.5 | 15-25 | Low | Moderate |
Table 2: Energy Consumption by Component
Component | Energy Use (% of Total) | Typical Efficiency Measure | Cost to Upgrade ($) |
---|---|---|---|
Chiller | 40-50 | SEER 15+ | 10,000-50,000 |
AHU/Fan | 20-30 | Variable-Speed Motor | 5,000-15,000 |
Boiler | 15-25 | Condensing (95% AFUE) | 8,000-20,000 |
Ductwork | 5-10 | Sealing/Insulation | 1,000-5,000 |
Future Trends and Innovations
HVAC technology continues to evolve, driven by digitalization and sustainability goals. Smart thermostats, integrated with IoT, optimize performance via real-time data, reducing energy use by up to 15%. Artificial intelligence (AI) enhances predictive maintenance, identifying faults before they escalate.
Low-GWP (Global Warming Potential) refrigerants, like R-32 or R-454B, replace high-impact HFCs, aligning with the Kigali Amendment to the Montreal Protocol. Modular designs and 3D printing of components promise faster, customized implementations.
Conclusion
The design and implementation of HVAC systems are complex yet essential processes, balancing comfort, efficiency, and air quality. From ancient heating methods to cutting-edge smart systems, HVAC has transformed how we inhabit spaces. As energy and environmental pressures mount, ongoing innovation ensures these systems remain vital to sustainable living. This article has provided a detailed examination of the principles, practices, and prospects of HVAC, offering a resource for professionals and enthusiasts alike.
Maximize Tooling and CNC Metal Spinning Capabilities.
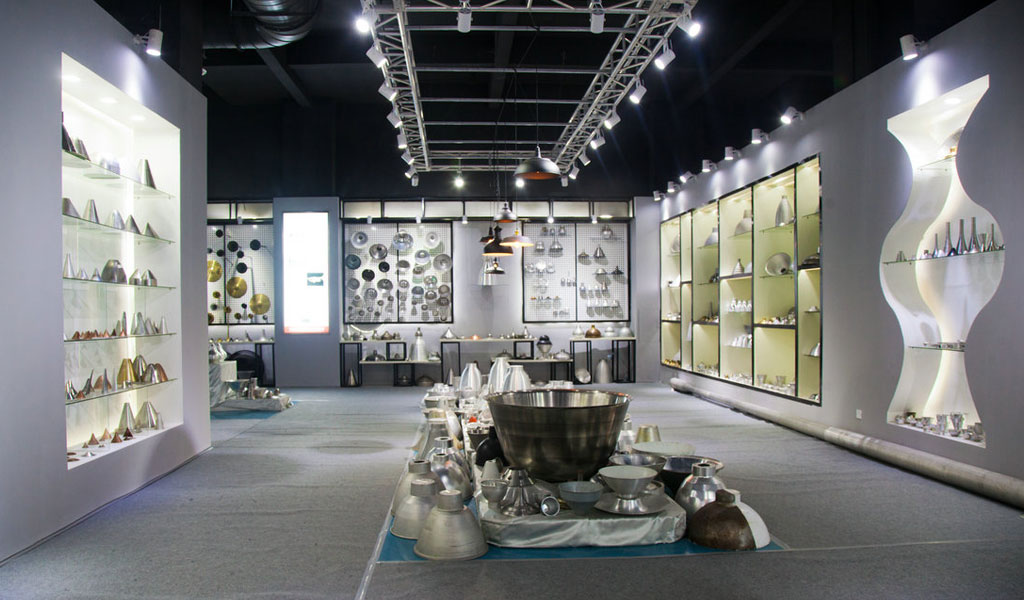
At BE-CU China Metal Spinning company, we make the most of our equipment while monitoring signs of excess wear and stress. In addition, we look into newer, modern equipment and invest in those that can support or increase our manufacturing capabilities. Our team is very mindful of our machines and tools, so we also routinely maintain them to ensure they don’t negatively impact your part’s quality and productivity.
Talk to us today about making a rapid prototype with our CNC metal spinning service. Get a direct quote by chatting with us here or request a free project review.
BE-CU China CNC Metal Spinning service include : CNC Metal Spinning,Metal Spinning Die,Laser Cutting, Tank Heads Spinning,Metal Hemispheres Spinning,Metal Cones Spinning,Metal Dish-Shaped Spinning,Metal Trumpet Spinning,Metal Venturi Spinning,Aluminum Spinning Products,Stainless Steel Spinning Products,Copper Spinning Products,Brass Spinning Products,Steel Spinning Product,Metal Spinnin LED Reflector,Metal Spinning Pressure Vessel,