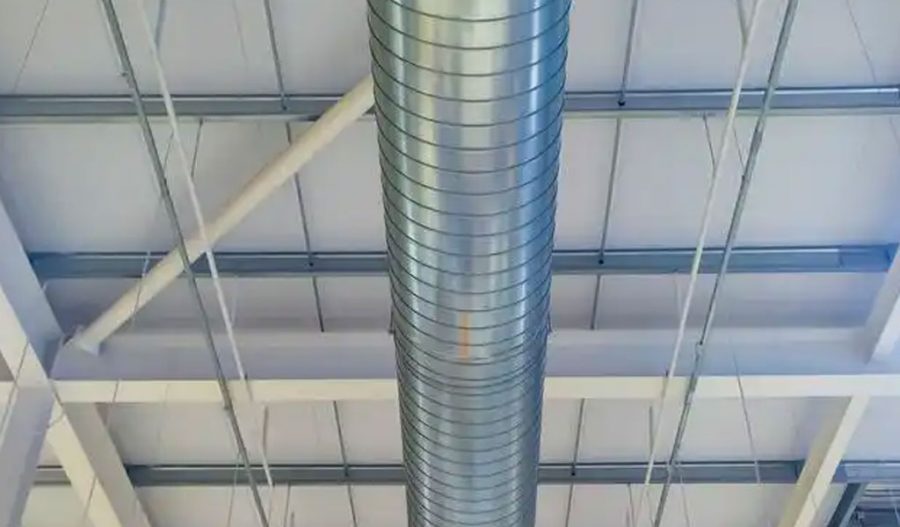
Spinning forming technology, encompassing conventional spinning, shear spinning, and flow forming, represents a cornerstone of modern metalworking, particularly for the production of axisymmetric components. Over the past few decades, these techniques have matured significantly, driven by advancements in automation, material science, and computational modeling. Their application to high-performance materials—such as titanium alloys, aluminum alloys, magnesium alloys, nickel-based superalloys, and advanced composites—has expanded their relevance across industries like aerospace, automotive, defense, and energy. These materials, characterized by high strength-to-weight ratios, corrosion resistance, and thermal stability, pose unique challenges due to their complex deformation behaviors and limited formability at ambient temperatures. This article provides a comprehensive exploration of matured spinning forming technologies, their application to high-performance materials, and recent advancements, supported by detailed comparative analyses.
Spinning forming is a chipless, incremental forming process that shapes a rotating metal blank or preform into a desired geometry using localized pressure from rollers or tools. Unlike traditional forging or deep drawing, spinning minimizes material waste, reduces tooling costs, and enables the production of near-net-shape components. The maturation of spinning technologies has been marked by the integration of computer numerical control (CNC) systems, finite element analysis (FEA), and advanced material characterization, allowing for precise control over process parameters and improved part quality. This article delves into the historical evolution, process mechanics, material considerations, technological advancements, and industrial applications of spinning forming, with a focus on high-performance materials.
Historical Evolution of Spinning Forming
Origins and Early Development
Metal spinning, one of the oldest chipless forming techniques, traces its roots to ancient civilizations. Archaeological evidence suggests that spinning-like processes were used in ancient Egypt around 3000 BC to shape pottery, with hand-driven wheels shaping clay. By 25 BC, the technique was adapted for metalworking, notably for crafting circular iron shields. During the medieval period, wooden spinning lathes, manually operated by assistants, were employed to produce items like vases, tea kettles, and trophies. These early methods relied heavily on artisan skill, limiting reproducibility and scalability.
The Industrial Revolution marked a turning point, with the introduction of steam-powered machinery in the 18th and 19th centuries. Rolling mills, hammers, and presses, powered by steam engines, enabled larger-scale metal forming. By the early 20th century, manual spinning lathes were refined, and the process began to be applied to industrial components, particularly in small-batch production. The development of shear spinning and flow forming in the mid-20th century expanded the capabilities of spinning, allowing for significant thickness reduction and enhanced mechanical properties.
Modern Advancements
The advent of CNC technology in the late 20th century revolutionized spinning forming. CNC spinning lathes, such as the Leifeld PNC350-800, introduced automation and precision, enabling the production of complex geometries with consistent quality. The integration of FEA and process simulation software further enhanced process design, allowing engineers to predict material flow, stress distribution, and potential defects. Recent decades have seen the development of novel spinning techniques, such as non-axisymmetric spinning, hot spinning, and spinning-extrusion forming, tailored to high-performance materials. These advancements have positioned spinning as a viable alternative to conventional forging and deep drawing, particularly for lightweight, high-strength components.
Fundamentals of Spinning Forming Processes
Conventional Spinning
Conventional spinning involves clamping a flat, circular metal blank against a rotating mandrel and gradually shaping it using a roller. The blank conforms to the mandrel’s shape without significant thickness reduction, making it suitable for producing hollow, axisymmetric parts like bowls, cones, and hemispheres. The process is typically performed at room temperature, though hot spinning is used for materials with limited ductility. Key parameters include spindle speed, roller feed rate, roller geometry, and lubrication, which influence surface finish, dimensional accuracy, and material flow.
Shear Spinning
Shear spinning, also known as power spinning, reduces the thickness of the blank while maintaining its diameter. The roller applies a controlled force, causing the material to flow axially along the mandrel, resulting in a thinner-walled component. This process is governed by the sine law, where the wall thickness after spinning is proportional to the sine of the cone angle. Shear spinning is ideal for producing conical or tapered components, such as rocket nose cones and turbine disks, and is often used with high-strength materials due to its ability to enhance mechanical properties through work hardening.
Flow Forming
Flow forming is an advanced spinning technique that significantly reduces the thickness of a tubular or cylindrical preform while elongating it axially. The preform is mounted on a rotating mandrel, and one or more rollers apply compressive forces, causing the material to flow along the mandrel. Flow forming can achieve thickness reductions of up to 90%, making it suitable for producing thin-walled, high-precision components like missile casings, automotive wheel rims, and pressure vessels. The process is highly flexible, allowing for complex geometries and improved material properties due to grain refinement and work hardening.
Comparison of Spinning Processes
The following table compares the key characteristics of conventional spinning, shear spinning, and flow forming:
Process | Thickness Reduction | Geometry | Material Flow | Applications | Advantages | Limitations |
---|---|---|---|---|---|---|
Conventional Spinning | Minimal | Axisymmetric, hollow shapes | Radial and circumferential | Bowls, hemispheres, reflectors | Low tooling costs, high flexibility | Limited to simple geometries, manual skill required |
Shear Spinning | Moderate to high | Conical, tapered shapes | Axial, governed by sine law | Rocket nose cones, turbine disks | Enhanced mechanical properties, precision | Limited to conical shapes, high forces required |
Flow Forming | High (up to 90%) | Cylindrical, tubular shapes | Axial, significant elongation | Missile casings, wheel rims, pressure vessels | Near-net-shape, improved material properties | Complex tooling, high equipment costs |
High-Performance Materials in Spinning Forming
Characteristics of High-Performance Materials
High-performance materials are defined by their exceptional mechanical, thermal, and chemical properties, making them ideal for demanding applications. Common high-performance materials used in spinning forming include:
- Titanium Alloys: Known for their high strength-to-weight ratio, corrosion resistance, and thermal stability, titanium alloys (e.g., Ti-6Al-4V) are widely used in aerospace and biomedical applications. Their limited formability at room temperature necessitates hot spinning.
- Aluminum Alloys: High-strength aluminum alloys (e.g., 7075, 6061) offer excellent corrosion resistance and lightweight properties, making them suitable for automotive and aerospace components. They are amenable to both cold and hot spinning.
- Magnesium Alloys: The lightest structural metals, magnesium alloys (e.g., AZ31, ZK60) are used in aerospace and automotive applications for weight reduction. Their hexagonal close-packed structure limits ductility, requiring elevated temperatures for spinning.
- Nickel-Based Superalloys: These alloys (e.g., Inconel 718) exhibit superior high-temperature strength and creep resistance, ideal for gas turbine components. Hot spinning is typically required due to their high strength and low ductility.
- Advanced Composites: Metal matrix composites (MMCs) and polymer matrix composites (PMCs) combine high strength with tailored properties. Spinning of MMCs is an emerging field, requiring specialized processes to manage reinforcement distribution.
Challenges in Spinning High-Performance Materials
Spinning high-performance materials presents several challenges:
- Limited Formability: Many high-performance materials have low ductility at room temperature, leading to cracking or wrinkling during spinning. Hot spinning or incremental forming techniques are often employed to enhance formability.
- Anisotropy: Materials like titanium and magnesium alloys exhibit anisotropic behavior, complicating material flow predictions and requiring advanced modeling.
- Tool Wear: The high strength of these materials increases tool wear, necessitating durable roller materials (e.g., carbide or ceramic) and optimized lubrication.
- Residual Stresses: Spinning induces residual stresses that can affect part performance, requiring post-processing like heat treatment.
- Surface Quality: Achieving a high-quality surface finish is challenging due to material hardness and potential for galling or adhesion.
Material Properties and Spinning Parameters
The following table summarizes the properties of key high-performance materials and their typical spinning parameters:
Material | Density (g/cm³) | Tensile Strength (MPa) | Formability | Spinning Temperature (°C) | Spindle Speed (rpm) | Roller Feed Rate (mm/rev) |
---|---|---|---|---|---|---|
Ti-6Al-4V | 4.43 | 900–1100 | Low | 600–900 | 200–500 | 0.1–0.5 |
Aluminum 7075 | 2.81 | 520–570 | Moderate | 200–400 | 500–1500 | 0.2–1.0 |
Magnesium AZ31 | 1.78 | 240–290 | Low | 250–450 | 300–800 | 0.1–0.8 |
Inconel 718 | 8.19 | 1200–1400 | Very low | 900–1100 | 100–300 | 0.05–0.3 |
Al/SiC MMC | 2.9–3.0 | 600–800 | Low | 300–500 | 200–600 | 0.1–0.6 |
Mechanics of Spinning Forming
Material Flow and Deformation
Spinning forming involves complex material flow governed by tensile, compressive, and shear stresses. In conventional spinning, the material flows radially and circumferentially, conforming to the mandrel’s shape. Shear spinning induces axial flow, with thickness reduction proportional to the sine of the cone angle. Flow forming causes significant axial elongation, with material flowing along the mandrel under high compressive forces. The incremental nature of spinning reduces overall forming forces compared to forging, enabling the processing of hard-to-deform materials.
Finite element analysis (FEA) is widely used to model material flow and deformation. FEA models incorporate material constitutive laws (e.g., Johnson-Cook, Voce), friction conditions, and process parameters to predict stress-strain distributions, thickness variations, and potential defects like wrinkling or cracking. Recent advancements in FEA include the use of adaptive meshing and coupled thermomechanical models to account for temperature effects in hot spinning.
Force and Energy Requirements
The forces in spinning forming depend on material properties, process parameters, and tool geometry. The roller force in flow forming, for example, can range from 10 to 100 kN, depending on the material and thickness reduction. Empirical formulas, such as those developed by Kalpakcioglu (1964), estimate forming forces based on material yield strength, roller feed rate, and reduction ratio. Energy requirements are minimized due to the incremental nature of the process, making spinning more energy-efficient than forging or deep drawing.
Surface Quality and Mechanical Properties
Spinning enhances the mechanical properties of high-performance materials through work hardening and grain refinement. For example, flow forming of aluminum alloys can increase tensile strength by 20–30% due to strain hardening. Surface quality is influenced by roller geometry, lubrication, and initial preform roughness. Fine initial surface finishes are critical, as spinning tends to amplify surface imperfections. Ultrasonic vibration-assisted spinning has been explored to improve surface quality by reducing friction and enhancing material flow.
Technological Advancements in Spinning Forming
CNC and Automation
The integration of CNC systems has transformed spinning forming, enabling precise control over roller paths, spindle speeds, and feed rates. CNC lathes like the Leifeld PNC350-800 support multi-axis motion, allowing for non-axisymmetric and complex geometries. Playback mode in CNC spinning reproduces forming cycles, ensuring consistency in high-volume production. Automation, including robotic assistance, has reduced cycle times and labor costs, with applications in automotive and aerospace manufacturing.
Hot Spinning
Hot spinning, performed at elevated temperatures (typically 600–1100°C for titanium and nickel alloys), enhances the formability of high-performance materials. Induction heating, laser heating, and torch heating are used to maintain uniform temperatures. Hot spinning reduces forming forces, minimizes cracking, and enables the production of complex shapes. Challenges include thermal gradients, oxidation, and mandrel durability, which require advanced heating systems and protective atmospheres.
Non-Axisymmetric and Novel Spinning Processes
Recent developments include non-axisymmetric spinning, non-circular cross-section spinning, and tooth-shaped spinning, which expand the range of producible geometries. These processes use multi-roller setups and advanced mandrel designs to control material flow in non-traditional paths. Spinning-extrusion forming (SEF), a hybrid process, combines spinning with axial extrusion to enhance rib filling in components like propellant tank shells, achieving up to 53% higher rib heights compared to traditional spinning.
Machine Learning and Process Optimization
Machine learning (ML) techniques are increasingly applied to optimize spinning processes. ML algorithms predict optimal process parameters, detect defects, and model material behavior based on experimental and simulation data. For example, supervised learning models have been used to correlate roller feed rates with surface quality, while unsupervised learning identifies patterns in material flow. These advancements reduce trial-and-error in process development and enhance the efficiency of spinning high-performance materials.
Industrial Applications
Aerospace
Spinning forming is extensively used in aerospace for components like rocket nose cones, missile casings, turbine disks, and satellite reflectors. Titanium and nickel-based superalloys are preferred for their high strength and thermal resistance. Flow forming produces thin-walled, high-precision casings, while shear spinning is used for conical components. The ability to produce lightweight, near-net-shape parts reduces material costs and improves fuel efficiency.
Automotive
In the automotive industry, spinning is applied to produce wheel rims, exhaust components, and structural parts. Aluminum and magnesium alloys are favored for their lightweight properties, contributing to reduced vehicle weight and improved fuel economy. Flow forming of wheel rims achieves high strength and uniform thickness, while conventional spinning is used for decorative covers and prototypes.
Defense
Defense applications include missile bodies, pressure vessels, and armor components. Flow forming produces seamless, high-strength casings with minimal welds, enhancing reliability. Nickel-based superalloys and titanium alloys are used for their resistance to extreme environments. Spinning’s flexibility supports small-batch production, critical for defense prototyping.
Energy
In the energy sector, spinning is used for gas turbine components, nuclear reactor parts, and pressure vessels. Nickel-based superalloys and stainless steels are spun into complex shapes with high creep resistance. Flow forming ensures tight tolerances and enhanced fatigue properties, critical for long-term performance in harsh conditions.
Recent Research and Developments
Incremental Sheet Forming (ISF) Integration
Incremental sheet forming (ISF), a related technique, has been integrated with spinning to enhance flexibility. Single-point incremental forming (SPIF), inspired by spinning, uses a single tool to shape sheet metal without a mandrel, enabling complex geometries. Recent studies have developed special-purpose ISF machines for high-performance materials, improving formability and reducing tooling costs. ISF is particularly suited for small-lot production and prototyping.
Ultrasonic Vibration-Assisted Spinning
Ultrasonic vibration-assisted spinning applies high-frequency vibrations to the roller or mandrel, reducing friction and forming forces. Experiments on AA-6061 aluminum preforms have shown improved surface quality and reduced wall thickness deviation. This technique is promising for hard-to-deform materials like titanium and nickel alloys, where high forces and tool wear are significant challenges.
Spinning-Extrusion Forming (SEF)
SEF, a novel hybrid process, introduces an axial extrusion force during spinning to enhance rib filling in components with inner ribs. Research by Xia et al. (2019) demonstrated a 53% increase in rib filling height compared to traditional spinning, attributed to enhanced tension-shear and compression-shear deformation stages. SEF is particularly relevant for aerospace components like propellant tank shells, where structural integrity is critical.
Comparative Analysis of Recent Results
The following table compares recent experimental results in spinning forming of high-performance materials, focusing on key performance metrics:
Study | Material | Process | Thickness Reduction (%) | Surface Roughness (Ra, µm) | Tensile Strength Increase (%) | Key Findings |
---|---|---|---|---|---|---|
Xia et al. (2019) | Aluminum 6061 | SEF | 60 | 0.8 | 25 | 53% higher rib filling height; enhanced tension-shear deformation |
Konkova et al. (2015) | Ti-6Al-4V | Hot Flow Forming | 80 | 1.2 | 30 | Grain refinement improved fatigue life; required 900°C spinning temperature |
Ma et al. (2018) | Inconel 718 | Hot Spinning | 50 | 1.5 | 20 | Reduced forming forces at 1000°C; oxidation control critical |
Yuan et al. (2020) | Magnesium AZ31 | Hot Shear Spinning | 40 | 0.9 | 15 | Improved formability at 400°C; anisotropic behavior modeled via FEA |
Li et al. (2021) | Al/SiC MMC | Flow Forming | 70 | 1.0 | 28 | Uniform reinforcement distribution; required specialized roller geometry |
Future Directions
Sustainable Manufacturing
Sustainability is a growing focus in spinning forming, with efforts to reduce energy consumption, material waste, and emissions. Near-net-shape capabilities of flow forming minimize scrap, while advancements in electric servo presses reduce energy requirements. Recycling of high-performance materials, such as titanium and aluminum alloys, is being explored to enhance environmental performance.
Integration with Additive Manufacturing
Hybrid manufacturing, combining spinning with additive manufacturing (AM), is an emerging trend. AM can produce complex preforms, which are then spun to achieve final dimensions and properties. This approach reduces material waste and enables the production of tailored components with graded properties, particularly for aerospace and biomedical applications.
Advanced Materials and Composites
The spinning of advanced composites, such as carbon fiber-reinforced MMCs, is a frontier area. Challenges include managing reinforcement distribution and matrix-reinforcement bonding during deformation. Research is focused on developing specialized spinning processes, such as vibration-assisted spinning and multi-roller setups, to address these issues.
Digital Twins and Industry 4.0
The adoption of digital twins—virtual models of spinning processes—enhances real-time monitoring and optimization. Digital twins integrate sensor data, FEA, and ML to predict defects, optimize parameters, and improve quality control. Industry 4.0 technologies, such as IoT and cloud computing, are being applied to create smart spinning systems with predictive maintenance and adaptive control.
Conclusion
Matured spinning forming technologies, including conventional spinning, shear spinning, and flow forming, have transformed the manufacturing of high-performance materials. Their ability to produce lightweight, high-strength, near-net-shape components has made them indispensable in aerospace, automotive, defense, and energy applications. Advancements in CNC automation, hot spinning, non-axisymmetric processes, and machine learning have expanded their capabilities, while challenges like limited formability and tool wear are being addressed through innovative techniques like ultrasonic vibration and spinning-extrusion forming. As sustainability, hybrid manufacturing, and digitalization drive future developments, spinning forming will continue to play a critical role in advanced manufacturing, supported by ongoing research and industrial adoption.
Maximize Tooling and CNC Metal Spinning Capabilities.
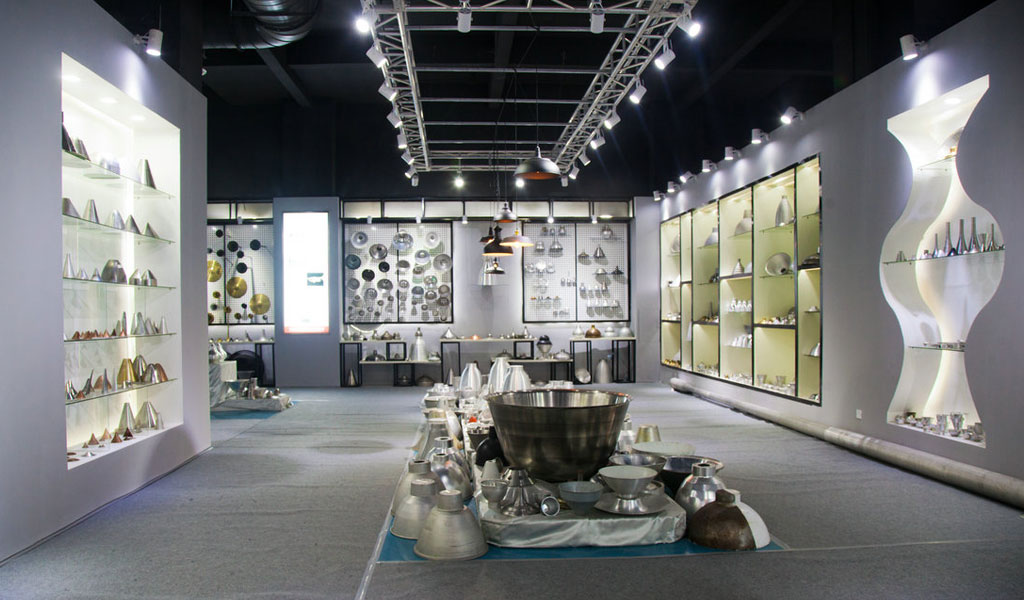
At BE-CU China Metal Spinning company, we make the most of our equipment while monitoring signs of excess wear and stress. In addition, we look into newer, modern equipment and invest in those that can support or increase our manufacturing capabilities. Our team is very mindful of our machines and tools, so we also routinely maintain them to ensure they don’t negatively impact your part’s quality and productivity.
Talk to us today about making a rapid prototype with our CNC metal spinning service. Get a direct quote by chatting with us here or request a free project review.
BE-CU China CNC Metal Spinning service include : CNC Metal Spinning,Metal Spinning Die,Laser Cutting, Tank Heads Spinning,Metal Hemispheres Spinning,Metal Cones Spinning,Metal Dish-Shaped Spinning,Metal Trumpet Spinning,Metal Venturi Spinning,Aluminum Spinning Products,Stainless Steel Spinning Products,Copper Spinning Products,Brass Spinning Products,Steel Spinning Product,Metal Spinnin LED Reflector,Metal Spinning Pressure Vessel,