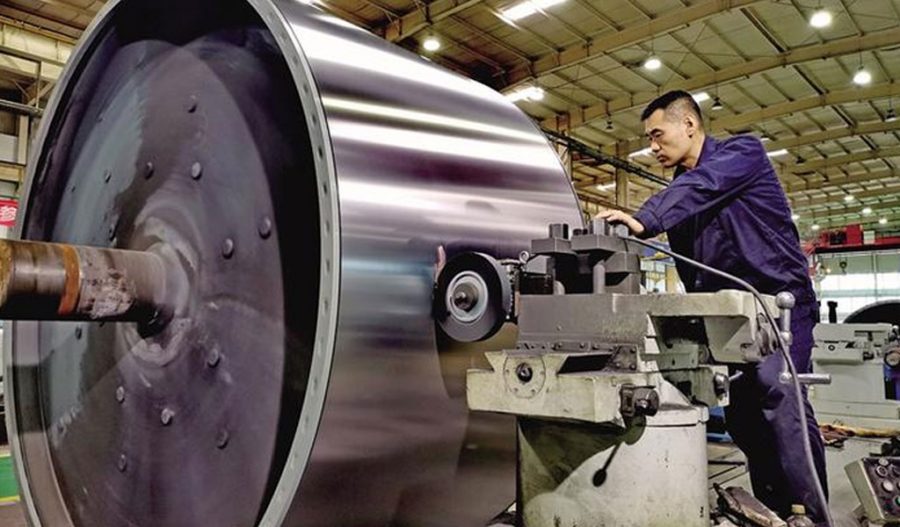
Spin forming is a special method of metal plastic forming, where the principle lies in securing the blank on the mold, which, together with the blank, spins at high speed. The outer spinning wheel applies significant pressure to the blank, causing the metal blank to deform, ultimately forming a part identical in shape to the mold.
Spin forming can be categorized into ordinary spin forming and strong spin forming. Ordinary spin forming refers to a process where the shape of the blank changes during forming, while the thickness remains constant. This type of spin forming has been around for a long time and finds widespread use in civilian applications such as utensils, tableware, and some parts with low precision requirements. On the other hand, strong spin forming involves both shape and thickness changes in the metal during forming, typically thinning the blank. In the strong spin forming process, the volume of the blank remains unchanged, and the thinning of the material enhances the part’s height. Strong spin forming is a non-cutting process, preserving the metal’s fiber flow direction and enhancing the part’s fatigue performance.
Strong spin forming technology is widely applied in various fields of national defense industries, particularly in the production of thin-walled, high-precision rotating parts. It offers several advantages:
- Increased strength and hardness of the material by approximately 35% to 45%, allowing for effective reduction of part thickness and weight in aerospace applications.
- Preservation of material’s fiber flow direction, enhancing fatigue performance.
- Improved part integrity due to absence of seam welds, particularly increasing fatigue life.
- Lower production costs and shorter manufacturing cycles due to non-cutting processing and simple forming molds.
- Significant reduction in blank thickness during forming, allowing for effective inspection of metallurgical defects.
- High precision with smaller dimensional and positional tolerances, sometimes exceeding those of mechanical machining.
Given these advantages, strong spin forming technology finds extensive applications in industries such as chemical, nuclear, shipbuilding, weapons manufacturing, and aerospace, particularly in the production of components for aircraft and aircraft engines.
Materials suitable for strong spin forming include not only traditional metals like carbon steel, aluminum and its alloys, copper and its alloys, and stainless steel but also various special materials developed in recent years such as high-strength steel, ultra-high-strength steel, titanium and its alloys, high-temperature alloys, tungsten, molybdenum, niobium, and their alloys.
With the increasing use of difficult-to-form materials like titanium alloys and high-temperature alloys in aircraft and aircraft engines, strong spin forming technology becomes more crucial. It enables the production of components with complex shapes and high precision, leading to improved reliability and reduced weight.
The widespread application of spin forming technology necessitates high requirements for spin forming machines, especially in terms of large turning diameters, high thrust, high precision, and high levels of automation. Foreign strong spin forming equipment has already been serialized and continuously developed towards larger, more versatile, and highly automated directions. With the development of computer technology, control systems for spin forming machines continue to evolve, ranging from fully developed numerical control for spindle speed to multi-wheel rotary frame spin forming machines.
In terms of spin forming technology, China is not far behind advanced foreign technologies. Although there may be gaps in automation and reliability compared to foreign advanced technologies, these gaps are narrowing. In recent years, China has made breakthroughs in the research and development of large spin forming equipment. As one of the earliest research institutions, the Aviation Industry Manufacturing Institute has nearly 50 years of history in the development of spin forming technology and equipment. It has maintained a leading position in domestic spin forming technology, especially in the development of special-shaped parts and spin forming of special materials.
Recently, the Manufacturing Institute has completed the process acceptance of the largest CNC vertical spin forming machine in Asia developed for a certain aerospace enterprise. This equipment adopts a vertical three-wheel structure, with a weight of 600 tons, a single wheel thrust of 100 tons, a machine tool turning diameter of 2.6 meters, and the ability to spin form large cylindrical parts with a diameter of 2.6 meters and a height of 3.5 meters. It can thin ultra-high-strength steel blanks from 35 millimeters to 2 millimeters, achieving a wall thickness precision of a hair, which exceeds that of mechanical machining. The equipment features three self-adjusting and self-balancing spin forces and unique functions such as synchronous feeding and off-center spin forming, demonstrating intelligent spin forming characteristics and reaching the overall technology to the international advanced level.
Spin forming is becoming increasingly widespread in its applications. Its technology can address significant bottlenecks in China’s manufacturing and defense industries, embodying the integration of military and civilian sectors and playing a significant strategic role in safeguarding national security and enhancing comprehensive national strength. With the development of China’s national economy and defense industry, spin forming, as a traditional craft, will continue to rejuvenate and play an increasingly important role.
Maximize Tooling and CNC Metal Spinning Capabilities.
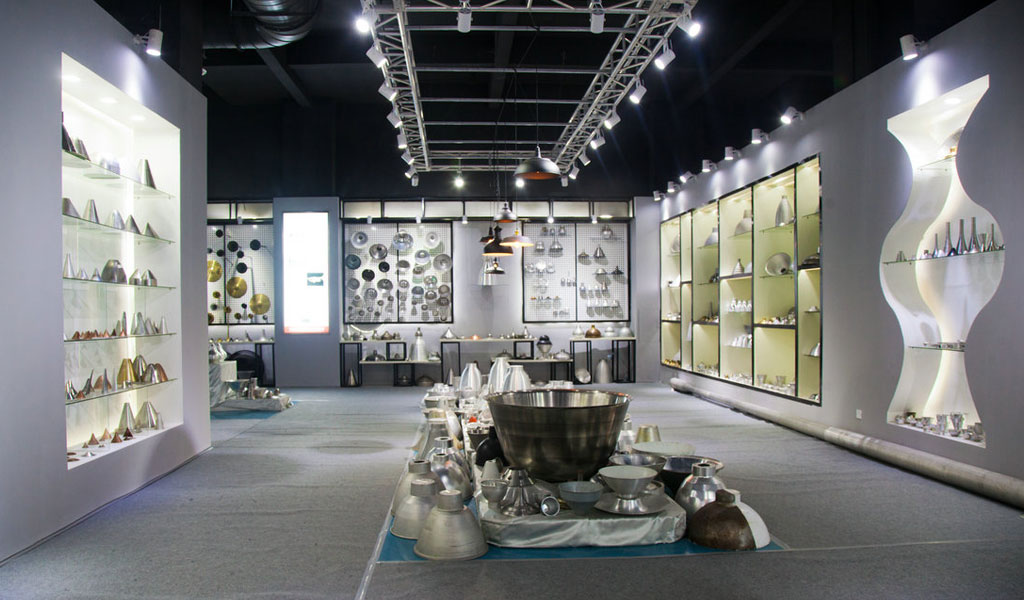
At BE-CU China Metal Spinning company, we make the most of our equipment while monitoring signs of excess wear and stress. In addition, we look into newer, modern equipment and invest in those that can support or increase our manufacturing capabilities. Our team is very mindful of our machines and tools, so we also routinely maintain them to ensure they don’t negatively impact your part’s quality and productivity.
Talk to us today about making a rapid prototype with our CNC metal spinning service. Get a direct quote by chatting with us here or request a free project review.
BE-CU China CNC Metal Spinning service include : CNC Metal Spinning,Metal Spinning Die,Laser Cutting, Tank Heads Spinning,Metal Hemispheres Spinning,Metal Cones Spinning,Metal Dish-Shaped Spinning,Metal Trumpet Spinning,Metal Venturi Spinning,Aluminum Spinning Products,Stainless Steel Spinning Products,Copper Spinning Products,Brass Spinning Products,Steel Spinning Product,Metal Spinnin LED Reflector,Metal Spinning Pressure Vessel,