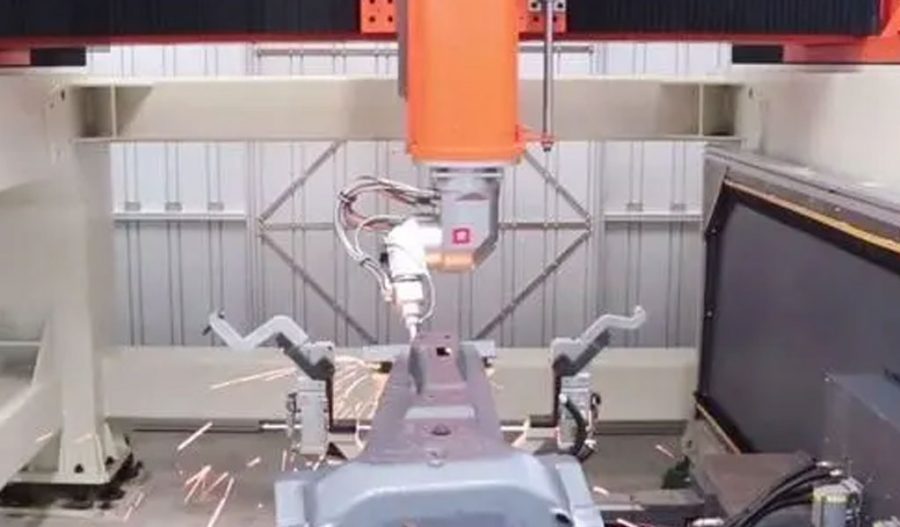
In the realm of manufacturing and industrial applications, precision and efficiency are paramount. Among the various technologies driving modern manufacturing processes, laser cutting stands out for its versatility and accuracy. Laser cutting has evolved significantly over the years, with advancements leading to the development of 5-axis and 3-axis laser cutting systems. These systems offer distinct advantages and capabilities, catering to different requirements and complexities in cutting operations. In this in-depth exploration, we delve into the intricacies of 5-axis and 3-axis laser cutting, elucidating their differences, functionalities, and applications.
Understanding Laser Cutting
Before delving into the specifics of 5-axis and 3-axis laser cutting, it’s essential to grasp the fundamentals of laser cutting technology. Laser cutting involves the use of a high-powered laser beam to precisely cut through various materials, ranging from metals and plastics to ceramics and composites. The laser beam is generated by a laser resonator and directed through a series of mirrors or fiber optics to the cutting head, where it is focused onto the workpiece.
The Basics of 3-Axis Laser Cutting
3-axis laser cutting, also known as 3D laser cutting, is a widely-used method in the manufacturing industry. As the name suggests, it operates on a three-axis Cartesian coordinate system, encompassing the X, Y, and Z axes. In a typical 3-axis laser cutting system, the laser head moves along the X and Y axes to navigate the workpiece’s surface, while the Z-axis controls the depth of the cut.
Advantages of 3-Axis Laser Cutting:
- Simplicity: 3-axis laser cutting systems are relatively straightforward in design and operation, making them easier to set up and maintain compared to more complex systems.
- Cost-Effectiveness: Due to their simplicity, 3-axis laser cutting machines often come with a lower initial investment and operating costs, making them accessible to a broader range of manufacturers.
- Versatility: While not as flexible as 5-axis systems, 3-axis laser cutting machines can still handle a wide range of materials and thicknesses, making them suitable for various applications.
Limitations of 3-Axis Laser Cutting:
- Limited Flexibility: The primary limitation of 3-axis laser cutting is its inability to tilt or rotate the cutting head, restricting its ability to access certain angles and contours in complex workpieces.
- Surface Quality: In some cases, 3-axis laser cutting may result in rougher surface finishes, especially when cutting thick materials or intricate designs.
The Advancements of 5-Axis Laser Cutting
In contrast to 3-axis laser cutting, 5-axis laser cutting represents a significant leap forward in terms of capability and versatility. As the name implies, 5-axis systems operate on a five-axis coordinate system, adding two additional axes of rotation to the X, Y, and Z axes found in 3-axis systems. This additional freedom of movement enables 5-axis laser cutting machines to access a wider range of angles and contours, making them ideal for complex, three-dimensional cutting tasks.
Advantages of 5-Axis Laser Cutting:
- Enhanced Precision: By incorporating additional axes of rotation, 5-axis laser cutting systems can achieve unparalleled precision and accuracy, especially when cutting intricate geometries or curved surfaces.
- Increased Flexibility: The ability to tilt and rotate the cutting head enables 5-axis laser cutting machines to access difficult-to-reach areas of the workpiece, allowing for more complex and intricate designs.
- Improved Surface Finish: 5-axis laser cutting often results in smoother surface finishes compared to 3-axis systems, reducing the need for secondary finishing processes and enhancing overall product quality.
Applications of 5-Axis Laser Cutting:
- Aerospace: The aerospace industry relies heavily on 5-axis laser cutting for the fabrication of complex components such as turbine blades, engine parts, and structural elements, where precision and reliability are paramount.
- Automotive: In automotive manufacturing, 5-axis laser cutting is used for producing intricate components like body panels, chassis parts, and exhaust systems, enabling automakers to achieve lightweight designs and improved fuel efficiency.
- Medical Devices: 5-axis laser cutting plays a crucial role in the production of medical devices and implants, where precision and biocompatibility are critical requirements.
Choosing the Right System for Your Needs
When deciding between 5-axis and 3-axis laser cutting systems, several factors must be considered to ensure the chosen system meets your specific requirements and objectives.
- Complexity of Parts: If your applications involve highly complex geometries or three-dimensional components, a 5-axis laser cutting system may be the preferred choice due to its enhanced flexibility and precision.
- Material Thickness: While both 5-axis and 3-axis systems can cut a wide range of materials, including metals, plastics, and composites, the thickness of the material may influence your decision. For thicker materials or multi-layered assemblies, a 5-axis system may offer better results.
- Production Volume: The anticipated production volume and throughput of your operations will also impact your choice of laser cutting system. 3-axis systems may suffice for low to medium-volume production runs, while 5-axis systems are better suited for high-volume manufacturing environments.
Conclusion
In conclusion, the choice between 5-axis and 3-axis laser cutting ultimately depends on the specific requirements of your applications, including the complexity of parts, material thickness, and production volume. While 3-axis laser cutting offers simplicity and cost-effectiveness, 5-axis laser cutting provides enhanced precision, flexibility, and surface finish, making it ideal for demanding applications in industries such as aerospace, automotive, and medical devices. By understanding the differences and capabilities of these two cutting-edge technologies, manufacturers can make informed decisions to optimize their production processes and achieve superior results.
Maximize Tooling and CNC Metal Spinning Capabilities.
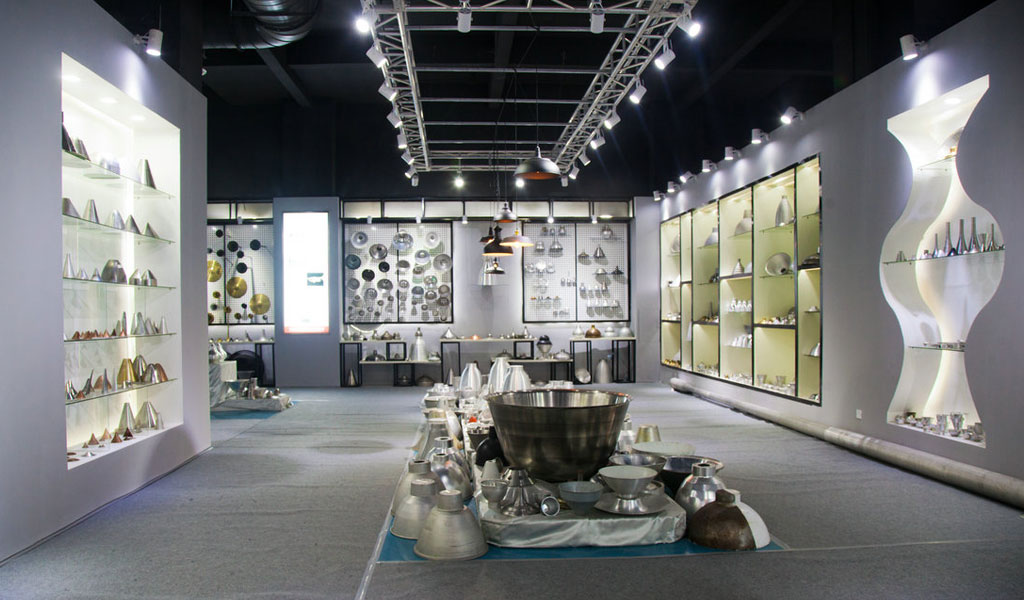
At BE-CU China Metal Spinning company, we make the most of our equipment while monitoring signs of excess wear and stress. In addition, we look into newer, modern equipment and invest in those that can support or increase our manufacturing capabilities. Our team is very mindful of our machines and tools, so we also routinely maintain them to ensure they don’t negatively impact your part’s quality and productivity.
Talk to us today about making a rapid prototype with our CNC metal spinning service. Get a direct quote by chatting with us here or request a free project review.
BE-CU China CNC Metal Spinning service include : CNC Metal Spinning,Metal Spinning Die,Laser Cutting, Tank Heads Spinning,Metal Hemispheres Spinning,Metal Cones Spinning,Metal Dish-Shaped Spinning,Metal Trumpet Spinning,Metal Venturi Spinning,Aluminum Spinning Products,Stainless Steel Spinning Products,Copper Spinning Products,Brass Spinning Products,Steel Spinning Product,Metal Spinnin LED Reflector,Metal Spinning Pressure Vessel,