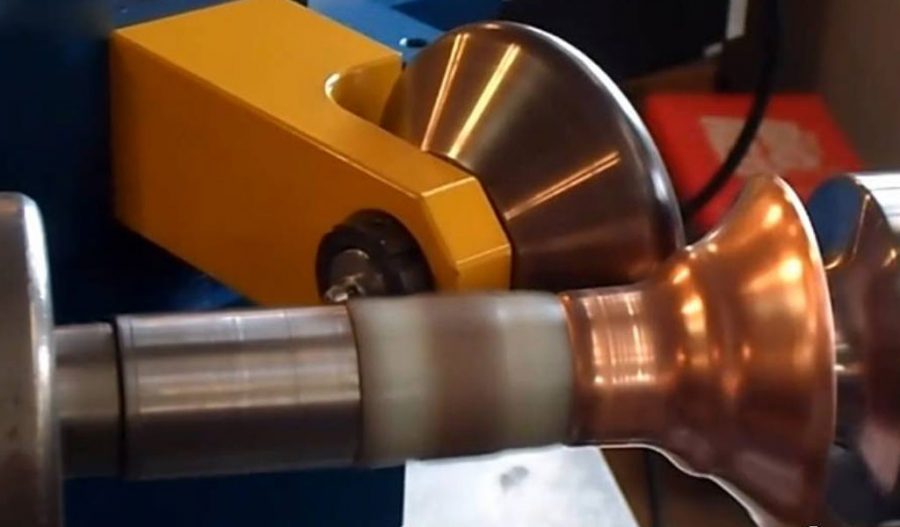
Metal spinning, also known as spin forming or spinning, is a metalworking process by which a disc or tube of metal is rotated at high speed and formed into an axially symmetric part. This process is highly versatile, allowing for the creation of complex shapes with minimal tooling costs compared to other manufacturing methods like casting or machining.
Designing for metal spinning requires careful consideration of several factors, including material selection, part geometry, tooling design, and finishing requirements. In this article, we’ll delve into each of these areas and provide practical tips for creating successful metal spinning designs.
Material Selection
- Ductility and Workability: Choose materials with high ductility and workability, such as aluminum, stainless steel, and copper, which are well-suited for the metal spinning process.
- Thickness Considerations: Opt for materials with uniform thickness to ensure consistent forming during spinning. Non-uniform thickness can lead to uneven deformation and surface imperfections.
- Material Properties: Consider the mechanical properties of the chosen material, including tensile strength, elongation, and yield strength, to ensure it can withstand the forming process without failure.
- Surface Finish Requirements: Determine the desired surface finish of the final part and select a material that can achieve the required smoothness or texture through spinning and subsequent finishing processes.
Geometric Considerations
- Symmetry and Axiality: Design parts with axial symmetry to leverage the full capabilities of the metal spinning process. Symmetrical designs ensure uniform material flow and minimize the risk of wrinkling or thinning.
- Taper and Draft Angles: Incorporate taper and draft angles into the design to facilitate material flow and release during spinning. Adequate taper angles prevent sticking and allow for easy removal of the formed part from the spinning mandrel.
- Avoid Sharp Corners and Fillets: Sharp corners can cause material thinning and cracking during spinning. Instead, use generous fillets and smooth transitions between features to promote uniform deformation.
- Wall Thickness Optimization: Maintain consistent wall thickness throughout the part to prevent deformation and ensure structural integrity. Avoid sudden changes in thickness that can lead to stress concentration and part failure.
- Feature Size and Complexity: Consider the size and complexity of features such as flanges, ribs, and embossments to ensure they can be accurately formed through spinning without distortion or tearing.
Tooling Design
As with workpieces, the tooling used in the metal spinning process can be customized to meet the needs of a particular project. Low-volume productions can save money by implementing tools made from less expensive metals. Hardwood tools, for example, make excellent temporary tools because they are less costly and can effectively handle prototype, low-volume, or soft metal orders. Soft tools made from aluminum and softer steels form permanent tools that are intended only for short production runs. For longer production runs or productions spinning stronger metals, the tools must be hardened.
Metal spinning processes employ mandrels, which are shafts or spindles that undergo the relatively soft forces involved in spinning metal pieces. The workmanship and quality of the mandrel has a significant impact on the accuracy and functionality of resulting parts.
While metal spinning tooling materials do affect total costs, this metal forming service is still more cost-effective than many other fabrication processes. Manufacturers can produce high-quality mandrels through simple turning and machining. This is much simpler than creating dies, using highly manual alternative processes, or using tools that require a long lead time. Overall, the lower costs of spin forming tooling can reduce startup production costs between 80% and 90%.
- Mandrel Design: Design spinning mandrels with precision to match the desired geometry of the final part. Use materials with low friction coefficients and adequate hardness to minimize wear and ensure accurate replication of features.
- Spinner Design: Select an appropriate spinner configuration based on the size and complexity of the part. Choose between manual, CNC, or hydraulic spinning machines depending on production volume and accuracy requirements.
- Tailstock Support: Provide adequate tailstock support to prevent deflection and vibration during spinning. Proper alignment between the mandrel and tailstock is crucial for maintaining concentricity and dimensional accuracy.
- Tooling Maintenance: Regularly inspect and maintain spinning tooling to ensure optimal performance and longevity. Address any signs of wear or damage promptly to avoid defects in the formed parts.
Finishing Touches
- Surface Treatment Options: Consider post-spinning surface treatments such as polishing, grinding, or chemical etching to achieve the desired aesthetic and functional properties. Surface treatments can enhance corrosion resistance, improve paint adhesion, or create decorative finishes.
- Quality Inspection: Implement thorough quality inspection processes to verify dimensional accuracy and surface quality of spun parts. Use precision measurement tools such as coordinate measuring machines (CMMs) and surface profilometers to assess compliance with design specifications.
- Prototype Iteration: Iterate on the design through prototyping and testing to identify and address any issues early in the development process. Prototype testing allows for validation of design assumptions and optimization of spinning parameters for production.
- Documentation and Standards Compliance: Maintain comprehensive documentation of the spinning process parameters, material specifications, and quality requirements. Ensure compliance with industry standards and customer specifications to meet regulatory and performance criteria.
Conclusion
Designing for metal spinning requires a multidisciplinary approach that combines creativity, engineering expertise, and manufacturing knowledge. By carefully considering material selection, geometric factors, tooling design, and finishing requirements, designers can create metal spinning designs that meet performance objectives while minimizing cost and lead time.
Whether producing simple cylindrical components or intricate decorative pieces, adhering to the tips outlined in this article will help ensure a successful metal spinning design process from concept to production. Embrace the versatility and efficiency of metal spinning as a manufacturing technique, and unleash your creativity to bring innovative designs to life.
With these comprehensive tips, designers and engineers can confidently embark on metal spinning projects, pushing the boundaries of what’s possible in terms of form, function, and aesthetics. Let the spinning begin!
Maximize Tooling and CNC Metal Spinning Capabilities.
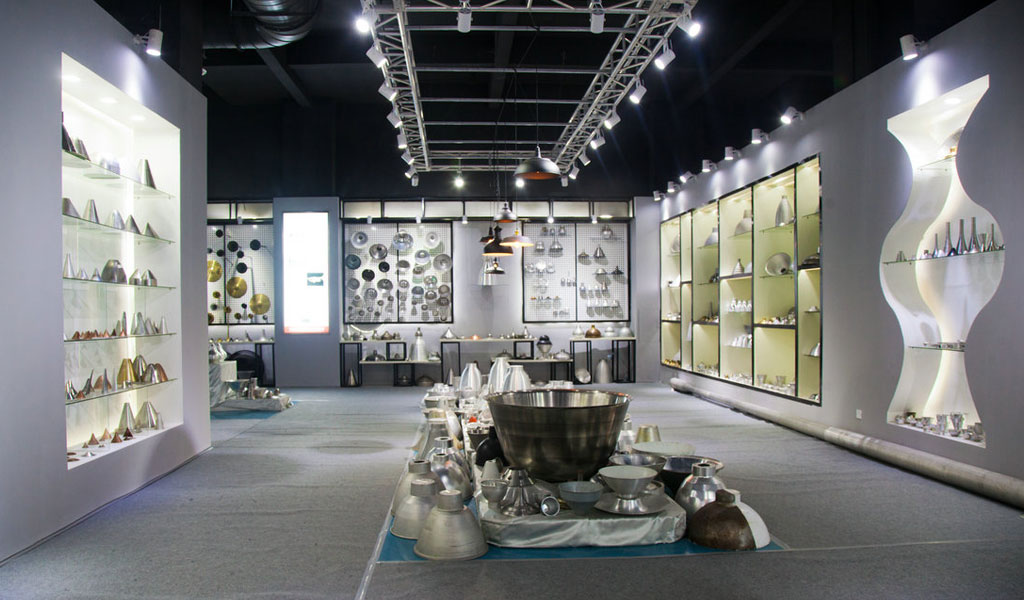
At BE-CU China Metal Spinning company, we make the most of our equipment while monitoring signs of excess wear and stress. In addition, we look into newer, modern equipment and invest in those that can support or increase our manufacturing capabilities. Our team is very mindful of our machines and tools, so we also routinely maintain them to ensure they don’t negatively impact your part’s quality and productivity.
Talk to us today about making a rapid prototype with our CNC metal spinning service. Get a direct quote by chatting with us here or request a free project review.
BE-CU China CNC Metal Spinning service include : CNC Metal Spinning,Metal Spinning Die,Laser Cutting, Tank Heads Spinning,Metal Hemispheres Spinning,Metal Cones Spinning,Metal Dish-Shaped Spinning,Metal Trumpet Spinning,Metal Venturi Spinning,Aluminum Spinning Products,Stainless Steel Spinning Products,Copper Spinning Products,Brass Spinning Products,Steel Spinning Product,Metal Spinnin LED Reflector,Metal Spinning Pressure Vessel,