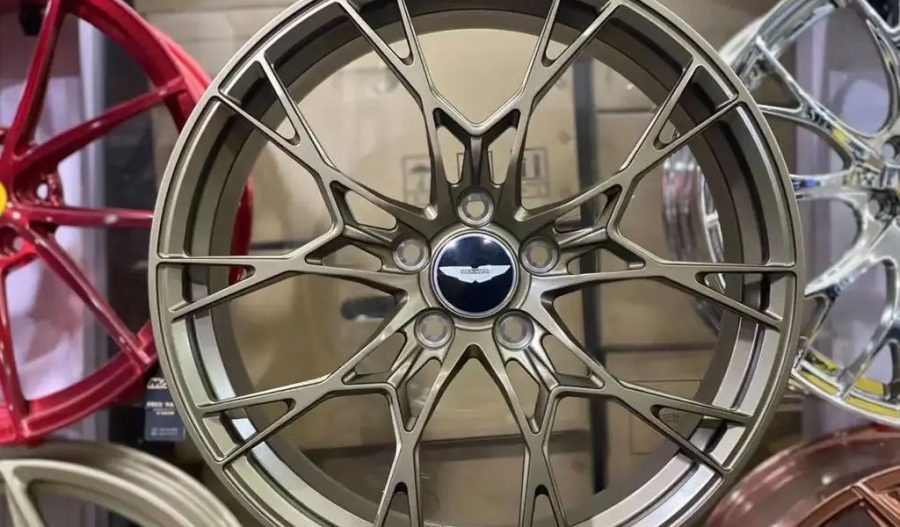
In the world of automotive and aerospace engineering, the debate over the most effective and efficient methods for producing wheel hubs is ongoing. Two primary manufacturing techniques stand out: CNC spinning and precision forging. Each method offers unique benefits and poses specific challenges, making them suitable for different applications and industries. This article delves deep into the intricacies of both CNC spinning and precision forging, comparing their processes, advantages, drawbacks, and real-world applications.
Understanding Wheel Hubs
Wheel hubs are a fundamental component in the wheel assembly of vehicles. They serve as the mounting point for the wheel and the interface for the brake rotor or drum. Wheel hubs house the wheel bearings, facilitating smooth rotation and supporting the vehicle’s weight. Given their critical role, wheel hubs must possess high strength, durability, and precision.
Historical Perspective
Historically, wheel hubs were manufactured using basic casting and machining techniques. However, as automotive and aerospace industries advanced, the demand for higher performance, safety, and efficiency led to the adoption of more sophisticated manufacturing methods such as CNC spinning and precision forging.
CNC Spinning Wheel Hubs
CNC (Computer Numerical Control) spinning, also known as flow forming or shear forming, is a metal forming technique that uses CNC machinery to shape a metal blank or preform into a cylindrical or conical component. The process involves rotating a metal blank on a mandrel while CNC-controlled rollers apply pressure to gradually shape the metal.
The Detailed Process
- Setup: A metal blank, often a flat disk or cylindrical tube, is securely mounted onto a rotating mandrel.
- Spinning: As the mandrel spins at high speed, CNC-controlled rollers apply localized pressure to the metal blank, deforming it into the desired shape.
- Trimming and Finishing: The formed wheel hub undergoes trimming to remove excess material and may receive additional finishing treatments such as heat treatment, machining, and surface coating to achieve the final specifications.
Advantages of CNC Spinning
- Precision and Consistency: The CNC control allows for high precision and repeatability, ensuring that each wheel hub meets stringent dimensional tolerances.
- Material Efficiency: The spinning process is highly material-efficient, producing minimal waste compared to traditional machining methods.
- Enhanced Mechanical Properties: The deformation process can enhance the mechanical properties of the metal, resulting in stronger and more durable components.
Challenges of CNC Spinning
- High Equipment Costs: CNC aluminum spinning machinery is sophisticated and expensive, necessitating significant initial investment.
- Complex Process Control: The process requires precise control and skilled operators to achieve optimal results.
- Design Limitations: Certain complex geometries and intricate features may be challenging or impossible to achieve with CNC spinning alone.
Applications of CNC Spinning Wheel Hubs
CNC spinning is commonly used in high-performance automotive and aerospace applications where precision and material properties are paramount. Examples include racing cars, high-performance sports cars, and aircraft components.
Precision Forging Wheel Hubs
Precision forging is a manufacturing process that involves shaping metal using localized compressive forces. Unlike traditional forging, precision forging aims to produce components with near-net shape, requiring minimal post-processing.
The Detailed Process
- Heating: The metal blank is heated to a specific temperature, making it malleable.
- Forging: The heated blank is placed in a die and subjected to high compressive forces, shaping it into the desired form.
- Cooling and Finishing: The forged component is cooled and undergoes additional processes such as trimming, machining, and heat treatment to achieve the final dimensions and properties.
Advantages of Precision Forging
- Superior Mechanical Properties: The forging process aligns the metal’s grain structure, resulting in components with excellent strength and fatigue resistance.
- High Dimensional Accuracy: Precision forging can produce components with tight tolerances and intricate details.
- Material Efficiency: The near-net shape process minimizes material waste and reduces the need for extensive machining.
Challenges of Precision Forging
- High Tooling Costs: The production of forging dies is costly and time-consuming, making the process less economical for low production volumes.
- Heat Treatment Requirements: Forged components often require additional heat treatment to achieve desired mechanical properties.
- Specialized Equipment: Precision forging requires specialized equipment and significant infrastructure investment.
Applications of Precision Forging Wheel Hubs
Precision forging is widely used in the automotive industry for passenger vehicles and commercial trucks due to its ability to produce strong and reliable components. It is also prevalent in industrial machinery and equipment, where durability and performance are critical.
Comparative Analysis: CNC Spinning vs. Precision Forging
Efficiency is a crucial factor when comparing CNC spinning and precision forging. CNC spinning is typically more efficient for small to medium production runs, thanks to its flexibility and reduced material waste. Precision forging, conversely, is highly efficient for large-scale production, where the high initial tooling costs can be amortized over a large volume of parts.
Mechanical Properties and Performance
The mechanical properties of wheel hubs produced by CNC spinning and precision forging differ due to the distinct manufacturing processes. Precision forging often results in superior mechanical properties, including higher tensile strength and fatigue resistance, due to the optimized grain structure. CNC spinning also produces strong components, but the properties can vary based on the material and specific process parameters used.
Design Flexibility and Complexity
Design flexibility is another critical consideration. CNC spinning offers greater flexibility, allowing for the production of complex shapes and custom designs without the need for expensive tooling changes. Precision forging, while capable of producing intricate details, is more limited in design flexibility due to the constraints of the forging dies.
Cost Considerations
The cost of producing wheel hubs using CNC spinning and precision forging varies based on production volume, material, and design complexity. CNC spinning tends to be more cost-effective for low to medium production volumes, while precision forging becomes more economical for high-volume production due to the high initial cost of tooling and equipment.
Suitability for Applications
The choice between CNC spinning and precision forging depends on the specific application requirements. For high-performance and custom applications, CNC spinning may be preferred due to its precision and flexibility. Precision forging is ideal for applications demanding high strength, durability, and cost-efficiency in large production volumes.
Industry Case Studies
Automotive Industry
In the automotive industry, both CNC spinning and precision forging are employed to produce wheel hubs for various types of vehicles. High-performance sports cars and racing vehicles often utilize CNC-spun wheel hubs for their lightweight and precise characteristics. Passenger cars and commercial trucks, on the other hand, typically use precision-forged wheel hubs for their strength and reliability.
Aerospace Industry
The aerospace industry demands components with high strength-to-weight ratios and precise tolerances. CNC spinning is commonly used to produce wheel hubs and other critical components for aircraft due to its ability to produce lightweight and high-precision parts. Precision forging is also used in aerospace applications, particularly for components that require exceptional strength and durability.
Industrial and Heavy Machinery
In industrial and heavy machinery applications, wheel hubs are subjected to harsh operating conditions and heavy loads. Both CNC spinning and precision forging are utilized based on the specific requirements. CNC spinning is favored for custom and prototype components, while precision forging is used for mass-produced components that need to withstand extreme stress and wear.
The Future of Wheel Hub Manufacturing
As technology advances, both CNC spinning and precision forging are evolving to meet the demands of modern engineering. Developments in material science, automation, and computer-aided design (CAD) are enhancing the capabilities of these manufacturing methods. For instance, advanced alloys and composites are being integrated into the processes to produce even stronger and lighter wheel hubs.
Integration with Industry 4.0
The integration of Industry 4.0 technologies, such as the Internet of Things (IoT), artificial intelligence (AI), and machine learning, is transforming wheel hub manufacturing. These technologies enable real-time monitoring and optimization of manufacturing processes, leading to improved quality control, reduced downtime, and increased efficiency.
Sustainability Considerations
Sustainability is becoming a key consideration in manufacturing. Both CNC spinning and precision forging are being adapted to reduce environmental impact. CNC spinning, with its material efficiency, contributes to less waste. Precision forging is also being optimized to use less energy and generate less waste, aligning with global sustainability goals.
To provide a well-rounded perspective, insights from industry leaders and experts are invaluable. Interviews with engineers, manufacturers, and industry analysts highlight the strengths and weaknesses of CNC spinning and precision forging. Their experiences and opinions help to contextualize the practical applications and future trends in wheel hub manufacturing.
Current research and development trends focus on improving the efficiency, precision, and material properties of wheel hubs. Studies and experimental projects aim to push the boundaries of what CNC spinning and precision forging can achieve. Collaborative efforts between academia and industry are driving innovations that could redefine the future of wheel hub manufacturing.
Conclusion
The debate between CNC spinning and precision forging for wheel hub manufacturing is nuanced and multifaceted. Both methods offer significant advantages and come with their own set of challenges. CNC spinning excels in precision, flexibility, and material efficiency, making it ideal for high-performance and custom applications. Precision forging, with its superior mechanical properties and cost-efficiency in large production volumes, is well-suited for automotive, aerospace, and industrial applications.
The choice between CNC spinning and precision forging ultimately depends on the specific requirements of the application, production volume, and cost considerations. As technology advances and new materials and processes are developed, the landscape of wheel hub manufacturing will continue to evolve, offering even more sophisticated solutions for engineers and manufacturers.
By understanding the intricacies of both CNC spinning and precision forging, industry professionals can make informed decisions that best meet their needs, ensuring the production of high-quality, durable, and reliable wheel hubs.
Maximize Tooling and CNC Metal Spinning Capabilities.
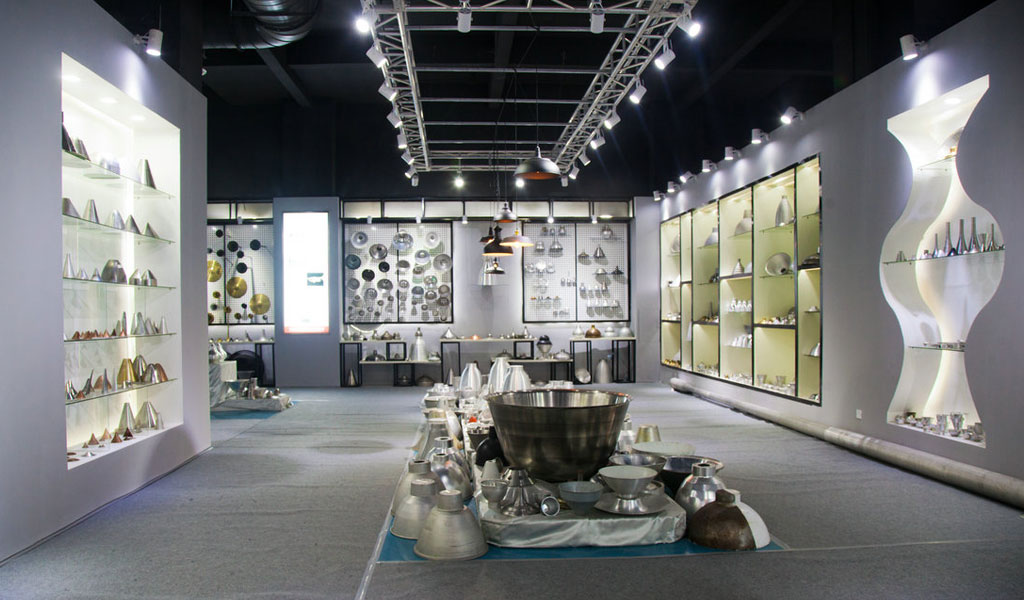
At BE-CU China Metal Spinning company, we make the most of our equipment while monitoring signs of excess wear and stress. In addition, we look into newer, modern equipment and invest in those that can support or increase our manufacturing capabilities. Our team is very mindful of our machines and tools, so we also routinely maintain them to ensure they don’t negatively impact your part’s quality and productivity.
Talk to us today about making a rapid prototype with our CNC metal spinning service. Get a direct quote by chatting with us here or request a free project review.
BE-CU China CNC Metal Spinning service include : CNC Metal Spinning,Metal Spinning Die,Laser Cutting, Tank Heads Spinning,Metal Hemispheres Spinning,Metal Cones Spinning,Metal Dish-Shaped Spinning,Metal Trumpet Spinning,Metal Venturi Spinning,Aluminum Spinning Products,Stainless Steel Spinning Products,Copper Spinning Products,Brass Spinning Products,Steel Spinning Product,Metal Spinnin LED Reflector,Metal Spinning Pressure Vessel,