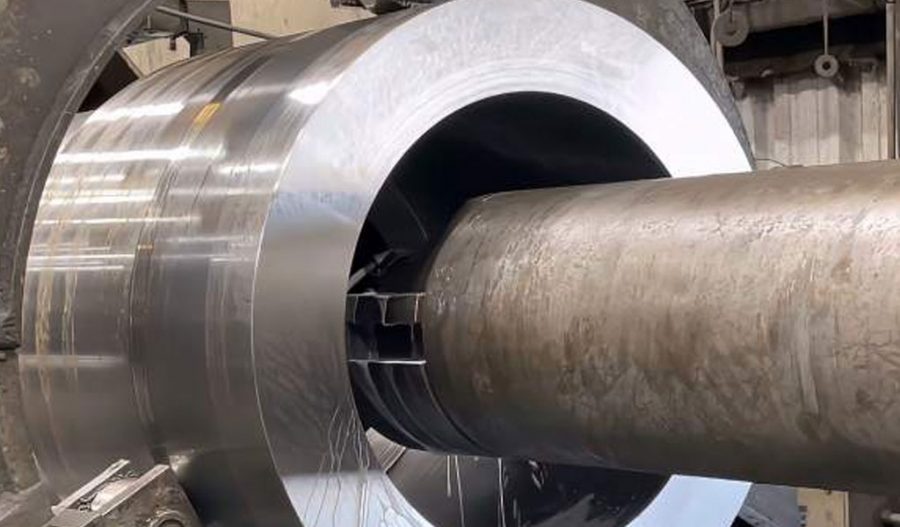
Monel, a high-performance alloy composed primarily of nickel and copper, is renowned for its exceptional strength, corrosion resistance, and durability, making it suitable for a variety of industrial applications. Two primary techniques used to shape and manufacture Monel components are metal spinning and turning. While both methods offer distinct advantages, they are employed based on different functional requirements, production scales, and end-use applications.
This article provides a comprehensive comparison of Monel spinning and Monel turning, covering their processes, advantages, limitations, applications, and the considerations that inform the choice between these two methods.
1. Overview of Monel
1.1 Composition and Properties
Monel alloys, including Monel 400, Monel K-500, and others, consist of a high percentage of nickel (around 63%) and copper (28-34%), with minor quantities of iron, manganese, carbon, and silicon. These alloys exhibit the following key properties:
- Corrosion resistance: Monel is highly resistant to corrosion, particularly in marine and chemical environments. It withstands exposure to saltwater, acids, and alkalis.
- High strength and toughness: Monel alloys maintain strength and ductility across a wide temperature range, from sub-zero temperatures to those in excess of 500°C.
- Good machinability: Despite its strength, Monel can be machined with relative ease, although special tools and techniques are often required due to its hardness.
Monel’s unique combination of properties makes it a favored material for applications such as marine engineering, chemical processing, and aerospace components.
1.2 Introduction to Metal Spinning
Metal spinning, also known as spin forming or spinning, is a manufacturing process that involves rotating a metal disc (or tube) at high speed while applying localized pressure to form the material into a desired shape. This method is particularly useful for producing axisymmetric parts, such as cones, hemispheres, and cylinders.
1.3 Introduction to Turning
Turning, in contrast, is a machining process where a cutting tool removes material from a rotating workpiece. In Monel turning, the material is held in a lathe, and a single-point cutting tool removes material to create cylindrical shapes or other symmetrical parts. Turning is one of the most common and versatile machining processes, offering high precision and surface quality.
2. The Metal Spinning Process for Monel
2.1 Basic Principles
Metal spinning is carried out by rotating a flat or cylindrical metal workpiece at high speed while a forming tool (often referred to as a roller) is pressed against it to gradually shape it. The force applied deforms the material, pushing it into a mold or mandrel to create the desired geometry.
The process is highly dependent on the ductility of the metal, and Monel’s high ductility allows it to be effectively spun, particularly in applications requiring seamless, smooth-surfaced components.
2.2 Equipment and Tools for Monel Spinning
Spinning can be done manually or with the assistance of CNC (computer numerical control) machinery. The key components of the spinning setup include:
- Lathe or spinning machine: Provides the rotational movement to the workpiece.
- Forming tool (roller): Applies pressure and shapes the metal as it spins.
- Mandrel: Serves as the inner support and determines the final shape of the component.
Spinning Monel, particularly with CNC machines, requires highly specialized tools due to the strength and toughness of the alloy.
2.3 Types of Metal Spinning
Monel spinning can be divided into several sub-processes:
- Conventional spinning: The metal is thinned and extended into shape without significant change in thickness.
- Shear forming: The material is reduced in thickness during the spinning process, creating a stronger, lightweight product.
- Flow forming: A similar process to shear forming but involves greater deformation, particularly used in high-strength applications.
2.4 Advantages of Monel Spinning
- Cost-effective for small batch production: Spinning does not require expensive dies or molds, making it cost-effective for small production runs.
- High-quality surface finish: The spinning process provides excellent surface finishes with minimal post-processing.
- Material conservation: The process is highly efficient in terms of material use, as there is little to no waste.
- Seamless structures: Metal spinning creates continuous, seamless structures that are beneficial in pressure vessel and aerospace applications.
2.5 Challenges and Limitations of Monel Spinning
- Limited geometries: While spinning is ideal for axisymmetric parts, it is less suitable for complex geometries or parts requiring fine details.
- Thinning of material: In certain spinning processes, material thinning can compromise the structural integrity of the final part, particularly if precise thickness control is necessary.
- Process time: Manual spinning can be labor-intensive and time-consuming, especially for complex shapes.
3. The Turning Process for Monel
3.1 Basic Principles of Turning
Turning is a subtractive machining process in which a rotating workpiece is shaped by a stationary cutting tool. The workpiece is rotated at high speeds, and the cutting tool, controlled by a CNC machine or an operator, removes material layer by layer to achieve the desired shape and dimensions.
Monel turning often requires carbide-tipped or diamond-coated cutting tools due to the hardness of the material, especially when dealing with Monel K-500, which is precipitation-hardened for extra strength.
3.2 Equipment and Tools for Monel Turning
Monel turning is performed on a lathe, which rotates the workpiece and moves the cutting tool along the material’s surface. Some essential components include:
- CNC lathe or manual lathe: Provides precise control over the rotation and cutting depth.
- Cutting tool: Typically made of carbide or diamond-coated materials, necessary to withstand the hardness and toughness of Monel.
- Cooling and lubrication systems: Essential for preventing overheating of the tool and workpiece, as Monel tends to harden when subjected to high temperatures.
3.3 Turning Operations for Monel
There are several types of turning operations used to manufacture Monel parts, each suited to different aspects of component geometry and surface finish:
- Rough turning: Removes large amounts of material in a short time, shaping the workpiece roughly to its final form.
- Finish turning: Provides fine surface finishes and brings the component to its final dimensions.
- Thread turning: Used to create external and internal threads on cylindrical parts.
- Grooving and boring: Creates internal cavities or external grooves for specialized applications.
3.4 Advantages of Monel Turning
- Precision and accuracy: Turning is highly precise, enabling the production of parts with tight tolerances and detailed features.
- Versatility: Turning can produce parts with complex geometries, including threads, holes, and grooves.
- Surface finish: Monel turning yields excellent surface finishes with minimal roughness, reducing the need for post-processing.
- Scalability: Turning is scalable for both small and large production volumes.
3.5 Challenges and Limitations of Monel Turning
- Tool wear: Monel’s hardness can cause rapid tool wear, particularly in high-speed turning operations.
- Machining costs: The need for specialized cutting tools and cooling systems can increase costs.
- Material waste: Unlike spinning, which is a near-net-shape process, turning involves material removal, leading to more waste.
4. Key Differences Between Monel Spinning and Turning
4.1 Material Utilization
- Spinning: Monel spinning is a near-net-shape process, meaning that the starting material is largely retained in the final product, minimizing waste.
- Turning: Turning is a subtractive process that removes material from the workpiece, leading to higher material waste.
4.2 Precision and Tolerances
- Spinning: Spinning is less precise than turning, making it more suitable for parts where tight tolerances are not critical.
- Turning: Turning offers superior precision and is ideal for components requiring high accuracy and detailed features.
4.3 Surface Finish
- Spinning: While spinning can achieve good surface finishes, particularly with CNC-controlled processes, it may require additional finishing steps for high-end applications.
- Turning: Turning typically produces superior surface finishes with less post-processing.
4.4 Production Volume and Costs
- Spinning: Metal spinning is cost-effective for low to medium production volumes due to its minimal tooling requirements.
- Turning: Turning, particularly CNC turning, is well-suited to both small and large production volumes but may incur higher costs for specialized tooling.
4.5 Geometrical Capabilities
- Spinning: Best for axisymmetric shapes such as cones, cylinders, and hemispheres.
- Turning: Capable of producing a wider range of geometries, including threads, grooves, and non-cylindrical features.
5. Applications of Monel Spinning and Turning
5.1 Monel Spinning Applications
- Aerospace components: Seamless, cylindrical parts such as rocket nozzles and fuel tanks.
- Chemical processing equipment: Pressure vessels, storage tanks, and other corrosion-resistant containers.
- Marine engineering: Components exposed to seawater, such as pump housings and valve bodies.
5.2 Monel Turning Applications
- Valves and pumps: Precision-machined components for fluid handling systems.
- Fasteners and threaded parts: Bolts, nuts, and threaded connectors requiring high strength and corrosion resistance.
- Precision components: Aerospace and defense parts where tight tolerances are critical.
6. Conclusion
Both Monel spinning and turning offer distinct advantages and are chosen based on specific application requirements, production volume, and desired geometries. Spinning excels in producing seamless, axisymmetric components with minimal material waste, making it ideal for industries such as aerospace and chemical processing. Turning, on the other hand, provides superior precision and surface finish, making it the preferred choice for complex geometries and high-tolerance applications.
When selecting between these two processes, engineers and manufacturers must consider factors such as production cost, material efficiency, and the specific mechanical and dimensional requirements of the final product. Both processes play a vital role in the efficient and cost-effective fabrication of Monel components, contributing to the alloy’s widespread use across various industries.
Maximize Tooling and CNC Metal Spinning Capabilities.
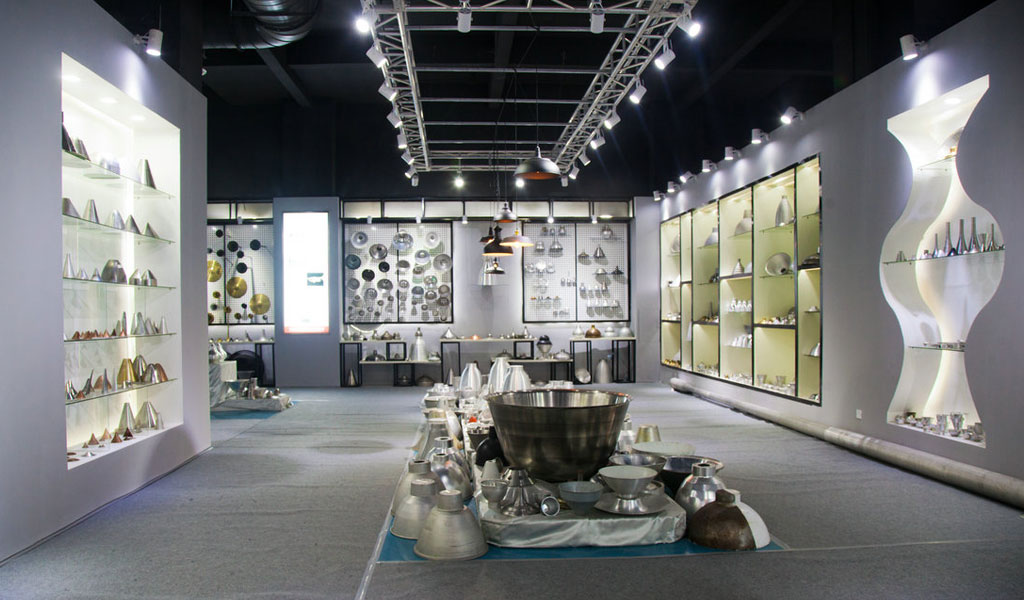
At BE-CU China Metal Spinning company, we make the most of our equipment while monitoring signs of excess wear and stress. In addition, we look into newer, modern equipment and invest in those that can support or increase our manufacturing capabilities. Our team is very mindful of our machines and tools, so we also routinely maintain them to ensure they don’t negatively impact your part’s quality and productivity.
Talk to us today about making a rapid prototype with our CNC metal spinning service. Get a direct quote by chatting with us here or request a free project review.
BE-CU China CNC Metal Spinning service include : CNC Metal Spinning,Metal Spinning Die,Laser Cutting, Tank Heads Spinning,Metal Hemispheres Spinning,Metal Cones Spinning,Metal Dish-Shaped Spinning,Metal Trumpet Spinning,Metal Venturi Spinning,Aluminum Spinning Products,Stainless Steel Spinning Products,Copper Spinning Products,Brass Spinning Products,Steel Spinning Product,Metal Spinnin LED Reflector,Metal Spinning Pressure Vessel,