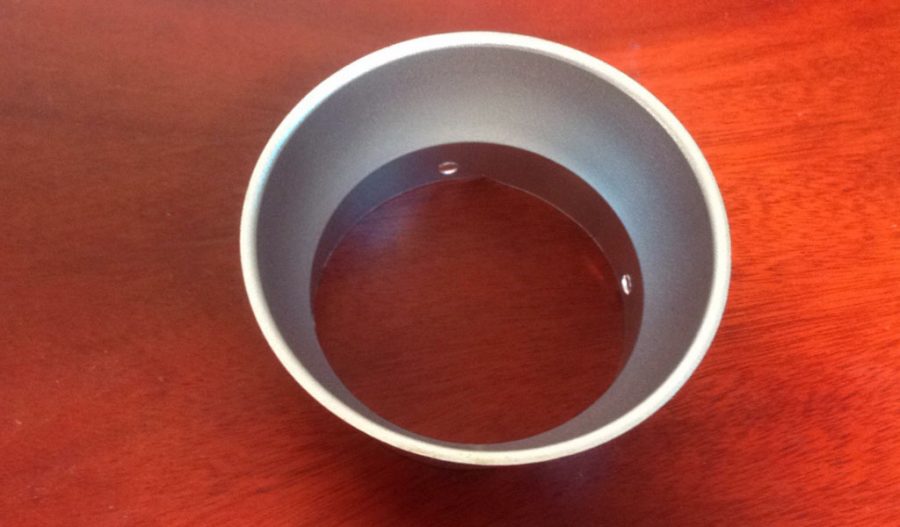
Molybdenum crucibles are essential containers used in rare earth smelting furnaces, quartz continuous melting furnaces, and sapphire single crystal growth furnaces. The quality of molybdenum crucibles directly affects the quality of sapphire single crystals, especially in sapphire single crystal production. With the increasing demand for high-quality sapphire single crystals due to the growth of the LED industry, the requirements for molybdenum crucibles have become more stringent. Traditional methods of producing molybdenum crucibles cannot meet the growing demand. This study introduces spinning processing as a new technical approach to address the challenges of producing molybdenum crucibles.
High-Temperature Processing:
Due to the poor plasticity of pure molybdenum material, spinning processing cannot be completed at room temperature. High-temperature tensile tests show that pure molybdenum demonstrates sufficient plasticity for spinning at temperatures above 600°C. However, at temperatures above 900°C, grain growth during recrystallization can affect the crucible’s performance. Therefore, molybdenum must be heated to between 600°C and 900°C for spinning. Numerical simulations indicate that the thinning ratio in each pass during spinning should not exceed 40% to prevent material accumulation in front of the spinning tool. Additionally, the feed ratio should not exceed 1.0 mm/r to avoid instability and poor shaping results.
Optimized Spinning Process:
Considering the cost and the need for varying wall thickness and tapering of the crucible, the optimal spinning process involves:
Calculating the diameter and thickness of the pure molybdenum round blank using the volume equivalence method.
Using hot-rolled pure molybdenum round blanks.
Performing multiple passes of conventional spinning to achieve the desired taper and bottom dimensions of the crucible.
Switching to multiple passes of strong spinning to achieve the required wall thickness, all while maintaining the workpiece at the appropriate temperature.
Equipment and Tooling:
Equipment, tooling, and measurement instruments significantly impact the quality and geometric precision of the finished product. The spinning machine must have both conventional and strong spinning capabilities. Heating should be done using oxy-acetylene flames or electromagnetic induction heating. The tooling includes spinning wheels, core molds, tail tops, and other auxiliary tools:
Core molds must match the taper required for the crucible.
Large-radius spinning wheels are chosen for their impact on the spinning process and product quality.
Tail tops must be appropriately sized to prevent bulging during spinning; small diameters are used for conventional spinning and large diameters for strong spinning.
Real-time temperature monitoring of the workpiece is essential throughout the process.
Research on Difficult-to-Form Metals:
Molybdenum’s high melting point and strength make it unsuitable for conventional plastic forming methods, which typically involve casting or sintering. This research explores the mechanical properties of molybdenum at high temperatures and develops a mechanical model for spinning. The study provides insights into the process conditions needed for spinning molybdenum and successfully produces thin-walled rotational bodies.
Composite Spinning Method:
The application of composite spinning methods (conventional and strong spinning) addresses the challenge of creating thin-walled components with variable wall thickness. This approach combines the geometric shaping capabilities of conventional spinning with the wall-thickness control of strong spinning, overcoming the limitations of single-method spinning processes.
Improved Production of Molybdenum Crucibles:
The spinning method enhances material utilization, achieving high precision and mechanical properties in molybdenum crucibles, which extends their service life and improves production efficiency. The process simplifies manufacturing and shortens production cycles.
Foundation for Future Research:
The findings provide technical support and theoretical guidance for further research into spinning difficult-to-form metals and composite spinning methods. This research broadens the application of refractory metals and offers new processing methods for challenging designs.
This study demonstrates a significant advancement in the production of large thin-walled molybdenum crucibles, addressing both technological and practical challenges in the field.
Maximize Tooling and CNC Metal Spinning Capabilities.
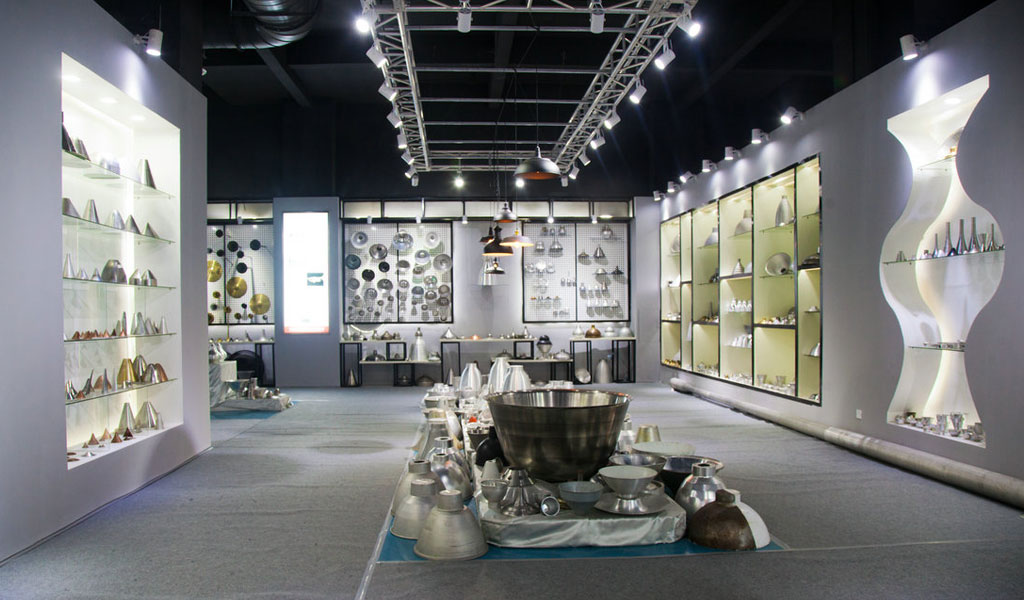
At BE-CU China Metal Spinning company, we make the most of our equipment while monitoring signs of excess wear and stress. In addition, we look into newer, modern equipment and invest in those that can support or increase our manufacturing capabilities. Our team is very mindful of our machines and tools, so we also routinely maintain them to ensure they don’t negatively impact your part’s quality and productivity.
Talk to us today about making a rapid prototype with our CNC metal spinning service. Get a direct quote by chatting with us here or request a free project review.
BE-CU China CNC Metal Spinning service include : CNC Metal Spinning,Metal Spinning Die,Laser Cutting, Tank Heads Spinning,Metal Hemispheres Spinning,Metal Cones Spinning,Metal Dish-Shaped Spinning,Metal Trumpet Spinning,Metal Venturi Spinning,Aluminum Spinning Products,Stainless Steel Spinning Products,Copper Spinning Products,Brass Spinning Products,Steel Spinning Product,Metal Spinnin LED Reflector,Metal Spinning Pressure Vessel,