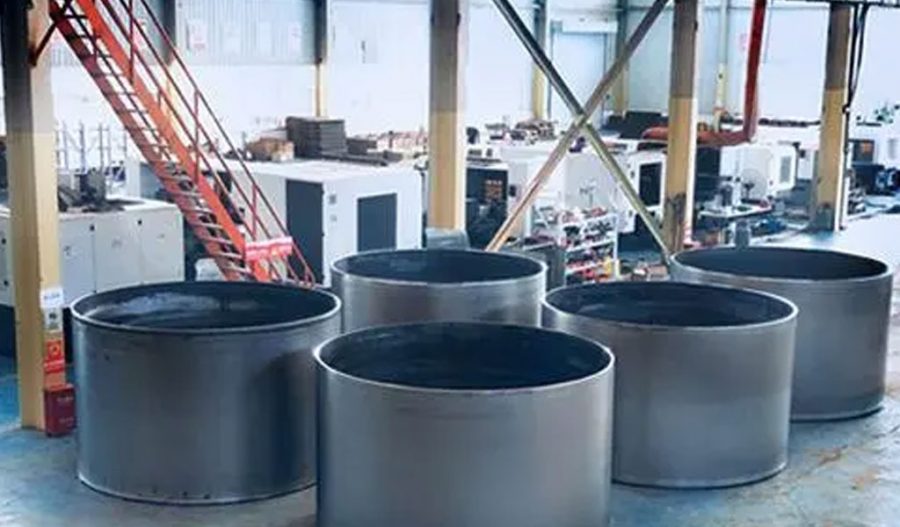
Shear spinning is a specialized metal forming process that involves the use of mechanical force to shape a metal workpiece by inducing shear deformation. This technique is part of a broader category of spinning methods, which are typically employed to produce thin-walled, axis-symmetric components from ductile metals. Unlike conventional turning or other machining processes, shear spinning utilizes a radial force applied by a rotating tool to gradually reduce the diameter of a blank, thereby producing a desired final shape. The process is distinct in that it specifically leverages the shear stress developed between the rotating tool and the workpiece to deform the material, rather than using the direct cutting or compression forces seen in other forming methods.
The application of shear spinning is vast, as it is commonly used in industries that require high-precision components with complex shapes and tight tolerances. These components include parts like cones, cylinders, hemispheres, and other intricate geometries commonly found in aerospace, automotive, medical, and defense applications. Due to its ability to produce parts with excellent dimensional accuracy, smooth surface finishes, and reduced material waste, shear spinning has become an essential process for manufacturing high-performance parts.
The Shear Spinning Process
Shear spinning typically involves a series of stages to form a blank into its final shape. The primary stages of the process include blank preparation, tool setup, deformation, and post-processing. Each of these stages plays a crucial role in achieving the desired final geometry and mechanical properties of the finished part.
1. Blank Preparation
The first step in shear spinning is the preparation of the metal blank. A blank is a piece of raw material that has been cut to an approximate size and shape that is suitable for spinning. This blank is often made from a ductile material, such as aluminum, titanium, or certain alloys, as these materials have the necessary plasticity to undergo deformation without cracking or failing during the process.
Before spinning, the blank may undergo preliminary operations such as heating to improve formability or surface treatments to enhance surface quality. The blank is typically mounted onto a spindle or mandrel that is securely fixed within the spinning machine.
2. Tool Setup
In shear spinning, the main tool used is a spinning roller or a forming tool, which is typically a rotating tool that applies radial pressure to the workpiece. This tool is mounted on a machine that rotates the blank while the tool exerts force on the blank’s surface. The tool’s shape and dimensions are carefully selected based on the desired final geometry of the part, as well as the material being used. The angle of the tool and the speed at which it rotates play a significant role in determining the quality of the part produced.
The machine setup also includes controlling the rotation speed of the blank and the tool, as well as any additional pressures applied during the process. Advanced shear spinning systems may employ automated controls to optimize the process, ensuring that the material is deformed in a controlled and precise manner.
3. Deformation
The core of the shear spinning process is the deformation of the blank. As the blank is rotated, the forming tool is brought into contact with the material. The tool applies a radial force that causes shear stress to develop between the blank and the tool. This shear force causes the material to elongate and thin out in the desired regions, gradually forming the component’s final shape.
As the tool moves along the surface of the blank, the material is stretched and formed into a thin-walled shape. This process is often referred to as “radial shear,” as the material is subjected to forces that are directed radially outward from the center of the blank. The shear deformation occurs primarily at the contact point between the tool and the blank, allowing the material to be shaped without the need for traditional cutting or grinding.
One of the key advantages of shear spinning is the ability to achieve high-quality parts without generating excessive heat. Because the process primarily relies on shear stress and not thermal energy, it can be used with a variety of metals that might otherwise be prone to heat-related defects in other forming methods.
4. Post-Processing
Once the part has been formed, it often undergoes post-processing steps to ensure it meets the required specifications. Post-processing can include operations such as trimming, machining, polishing, and heat treatment to improve mechanical properties or surface finish. These steps are typically carried out after the part has cooled and is removed from the spinning machine.
In some cases, further shaping or fine-tuning of the part’s dimensions may be required, particularly for parts that must adhere to strict tolerances. Additional heat treatments, such as annealing or hardening, may also be used to enhance the material’s strength or other properties.
Key Advantages of Shear Spinning
Shear spinning offers several advantages over traditional machining methods, making it an attractive choice for a wide range of applications. Some of the key benefits of shear spinning include:
1. Material Efficiency
One of the most significant advantages of shear spinning is its ability to minimize material waste. In many machining processes, large amounts of material are removed as chips or swarf. However, in shear spinning, much of the material is preserved, with only minimal thinning of the blank to create the final part. This is particularly beneficial when working with expensive materials, such as titanium, that would otherwise generate high material costs.
2. High Precision and Tolerance
Shear spinning is well-suited to producing high-precision components with tight tolerances. The process can create parts with excellent dimensional accuracy, smooth surface finishes, and minimal deviation from the intended geometry. This is especially important in industries such as aerospace and medical device manufacturing, where part performance and reliability are critical.
3. Versatility in Part Design
Shear spinning can be used to produce a wide variety of part geometries, including conical shapes, hemispheres, and other complex forms. The process is highly flexible, and by adjusting the tool shape, speed, and force, manufacturers can produce a broad range of part designs that would be difficult or impossible to achieve using other methods.
4. Reduced Heat Generation
Since shear spinning relies on mechanical deformation rather than thermal energy, there is less risk of heat-related defects such as warping, oxidation, or cracking. This makes shear spinning particularly useful for forming materials that are sensitive to heat, such as aluminum, titanium, and certain high-strength alloys.
5. Improved Surface Finish
The shear spinning process results in a smoother surface finish compared to traditional machining techniques, as the part is formed rather than cut. This can reduce or eliminate the need for additional finishing operations, lowering manufacturing costs and time.
Applications of Shear Spinning
Shear spinning has a wide range of applications in various industries, particularly those that require high-precision parts made from durable materials. Some of the key sectors that benefit from shear spinning include:
1. Aerospace
In aerospace manufacturing, shear spinning is used to produce lightweight, high-strength components such as fuel tank components, housings, and brackets. The ability to form complex shapes with tight tolerances is crucial in this sector, where safety and performance are paramount.
2. Automotive
The automotive industry uses shear spinning to create parts such as exhaust components, engine covers, and heat shields. The process is ideal for producing lightweight, durable components that can withstand the high stresses and temperatures found in automotive applications.
3. Medical
Medical device manufacturers use shear spinning to produce components such as implants, surgical tools, and medical housings. The high precision and smooth surface finish offered by shear spinning are essential for meeting the strict regulatory and functional requirements of the medical industry.
4. Defense
In the defense industry, shear spinning is employed to create components for military equipment, including parts for missiles, radar systems, and aircraft. The process is valuable in producing high-performance, reliable components for use in harsh environments.
5. Industrial Applications
Shear spinning is used in a variety of industrial applications where high-strength, lightweight parts are required. This includes parts used in power generation, machinery, and telecommunications.
Materials Used in Shear Spinning
Shear spinning is typically performed on ductile metals, as these materials can undergo plastic deformation without cracking or failure. Some common materials used in shear spinning include:
- Aluminum Alloys: Aluminum and its alloys are often used in shear spinning due to their excellent formability and lightweight properties. Aluminum components are commonly used in aerospace, automotive, and industrial applications.
- Titanium Alloys: Titanium and its alloys are used for their high strength-to-weight ratio and resistance to corrosion. Titanium components produced by shear spinning are used in high-performance aerospace and medical applications.
- Copper and Brass: Copper and brass are used for their excellent electrical and thermal conductivity properties. These materials are commonly found in electrical components, heat exchangers, and plumbing systems.
- Stainless Steel: Stainless steel is often used in shear spinning for applications that require high strength and corrosion resistance. It is commonly used in aerospace, medical, and food processing applications.
- Nickel Alloys: Nickel-based alloys are used in high-temperature applications, such as in the aerospace and energy sectors, where parts need to withstand extreme environments.
Challenges and Limitations of Shear Spinning
While shear spinning offers numerous advantages, there are also some challenges and limitations associated with the process:
1. Material Limitations
Not all materials are suitable for shear spinning. The process works best with ductile metals that can undergo plastic deformation without cracking. Brittle or hard materials may not deform properly and could lead to part defects or failures.
2. Tool Wear
The tools used in shear spinning are subjected to significant stresses during the process, which can result in wear over time. This can affect the precision of the process and may require frequent tool replacement or reconditioning.
3. Complexity of Setup
Shear spinning requires precise setup and control of various parameters, including tool angles, speeds, and forces. Improper setup can lead to defects such as uneven thinning, warping, or surface roughness. Ensuring that the process is carefully optimized is critical to achieving high-quality results.
4. Production Volume
Shear spinning is more suitable for low to medium-volume production runs due to the time and effort required for setup and tooling. For high-volume production, alternative methods such as stamping or casting may be more cost-effective.
Conclusion
Shear spinning is a versatile and efficient manufacturing process that is widely used to create high-precision, lightweight components for various industries. By utilizing shear forces to deform materials, shear spinning offers several advantages, including material efficiency, high precision, and reduced heat generation. While it is primarily used for ductile materials such as aluminum, titanium, and stainless steel, it is an indispensable tool in the production of high-performance parts for aerospace, automotive, medical, and defense applications. As manufacturing technologies continue to evolve, shear spinning remains an essential technique for creating complex geometries with tight tolerances and excellent surface finishes.
Maximize Tooling and CNC Metal Spinning Capabilities.
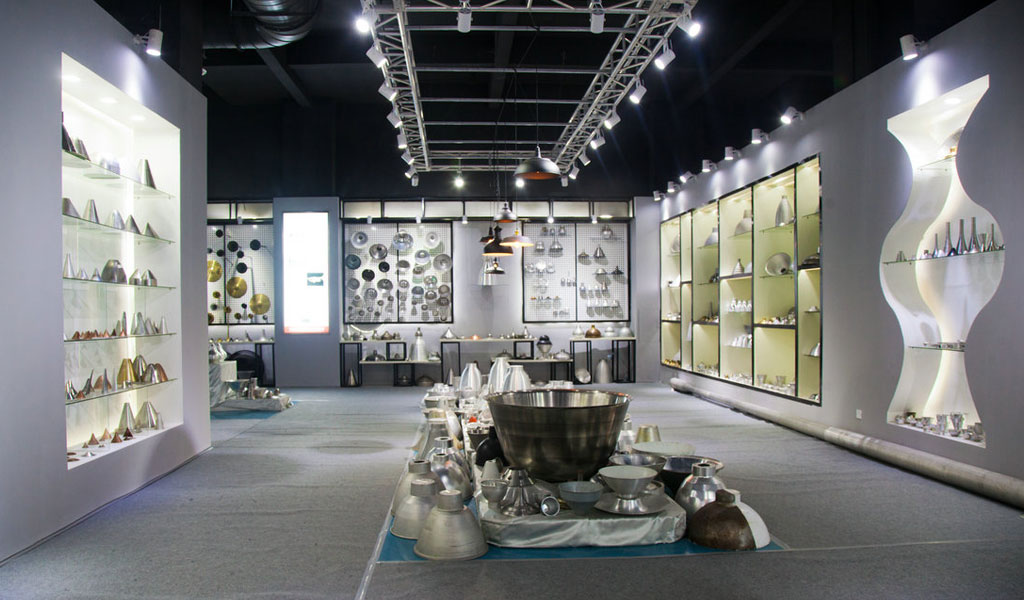
At BE-CU China Metal Spinning company, we make the most of our equipment while monitoring signs of excess wear and stress. In addition, we look into newer, modern equipment and invest in those that can support or increase our manufacturing capabilities. Our team is very mindful of our machines and tools, so we also routinely maintain them to ensure they don’t negatively impact your part’s quality and productivity.
Talk to us today about making a rapid prototype with our CNC metal spinning service. Get a direct quote by chatting with us here or request a free project review.
BE-CU China CNC Metal Spinning service include : CNC Metal Spinning,Metal Spinning Die,Laser Cutting, Tank Heads Spinning,Metal Hemispheres Spinning,Metal Cones Spinning,Metal Dish-Shaped Spinning,Metal Trumpet Spinning,Metal Venturi Spinning,Aluminum Spinning Products,Stainless Steel Spinning Products,Copper Spinning Products,Brass Spinning Products,Steel Spinning Product,Metal Spinnin LED Reflector,Metal Spinning Pressure Vessel,