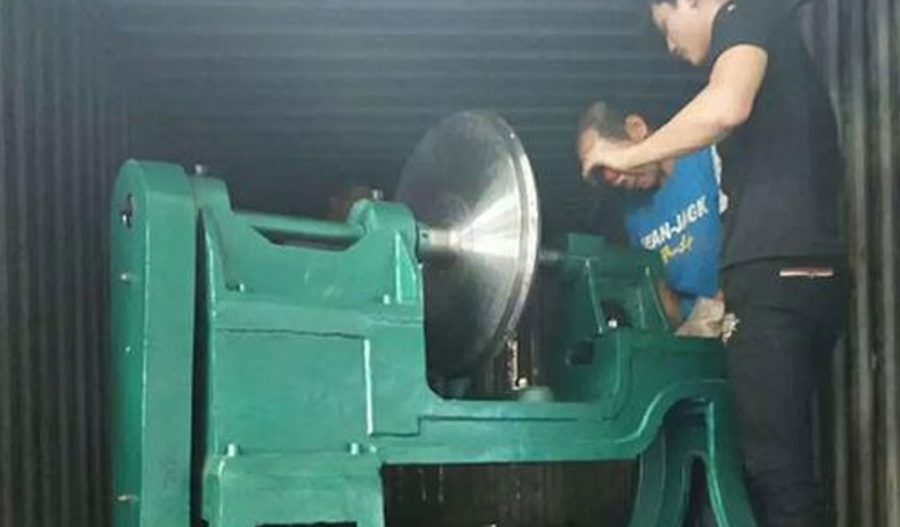
Metal spinning and stamping are both popular manufacturing processes used in various industries for producing complex metal parts. Both processes have distinct advantages and challenges when it comes to achieving tight tolerances. This article delves into the nuances of metal spinning tolerance versus stamping tolerance, comparing and contrasting the two processes in terms of precision, accuracy, and the factors that influence tolerance outcomes.
Metal Spinning Tolerance
Metal spinning, also known as spin forming, is a process where a metal disk is rotated at high speeds while a tool is used to shape the metal around a mandrel. This process is widely used for creating cylindrical or conical parts, such as tanks, cones, and other hollow shapes. The primary advantage of metal spinning lies in its ability to produce complex geometries with minimal tooling and waste. However, achieving tight tolerances in metal spinning is influenced by several factors, including the material used, the machine’s capabilities, and the skill of the operator.
Key Factors Affecting Metal Spinning Tolerance
- Material Properties: Different metals exhibit varying degrees of formability, and this directly impacts the achievable tolerances in metal spinning. For instance, softer metals like aluminum are generally easier to form and can achieve tighter tolerances compared to harder metals like titanium or stainless steel. The grain structure, temper, and thickness of the material also play a crucial role. Thicker materials may present challenges in terms of consistent material flow, which can affect the uniformity of the finished part.
- Tooling and Equipment: The precision of the mandrel, die, and spinning tools used can significantly affect the final tolerances of the part. High-quality mandrels and dies made from durable materials can reduce deviations and increase the accuracy of the formed part. The spinning machine’s speed and the control systems used for the process also affect how closely the machine can maintain tolerances. Manual spinning, for example, may lead to slightly more variation in tolerance compared to automated or hydraulic systems, where precision is more easily controlled.
- Operator Skill: Since metal spinning is a highly manual process, operator expertise is a key factor in achieving tight tolerances. Experienced operators can adjust the tool’s pressure and angle to fine-tune the shaping of the metal, reducing variations in wall thickness and overall part geometry. On the other hand, less experienced operators may struggle to maintain consistent force, leading to larger variations in tolerances.
- Part Geometry: The complexity of the part being spun also influences the achievable tolerance. Simple cylindrical shapes are easier to produce with higher precision, while parts with complex contours or varying wall thicknesses may result in greater variation in dimensions. For example, conical shapes often present challenges in maintaining uniformity in the sidewall angles and diameters.
- Process Variability: In metal spinning, the process inherently involves some variability due to factors such as material stretching, tool wear, and machine calibration. As the material is spun and formed, slight discrepancies can accumulate, leading to deviations in final dimensions. To minimize these variabilities, regular maintenance and calibration of the equipment are essential.
Tolerances in Metal Spinning
In terms of numerical tolerances, metal spinning can achieve tolerances typically in the range of ±0.01 inches to ±0.03 inches, depending on the specific material, part complexity, and process conditions. Tolerances can be tighter for smaller, simpler parts but may require additional quality control measures, such as post-spin machining or the use of precision measurement tools, to maintain consistency.
Post-Spin Machining
While metal spinning is capable of producing relatively accurate parts, certain features may require additional processing to achieve the desired tolerance. For example, complex holes, edges, or surfaces may need to be machined after spinning to bring them within specified tolerances. This added machining process can increase the cost and lead time for producing the final part.
Stamping Tolerance
Stamping, also known as press forming, is a high-speed manufacturing process used for producing flat or shallow parts from sheet metal. The material is placed in a die, and a punch is used to shape it into the desired form. This process is often used for producing large quantities of parts with high repeatability, such as automotive body panels, electronic components, and appliance parts. Stamping typically offers high precision and can achieve much tighter tolerances compared to metal spinning, due to its automated nature and the use of hardened dies.
Key Factors Affecting Stamping Tolerance
- Material Properties: Similar to metal spinning, the material used in stamping plays a crucial role in determining the achievable tolerance. Materials with high tensile strength, such as high-carbon steel, are more difficult to form and may lead to variations in part dimensions if not handled correctly. Additionally, the thickness of the material and its ability to undergo plastic deformation without fracturing or cracking will affect the final tolerance. Thicker materials tend to produce greater variations in part dimensions due to springback and other formability issues.
- Die Design and Precision: The accuracy of the die used in the stamping process is one of the most significant factors in achieving tight tolerances. High-precision dies are capable of producing parts with minimal variation, and their design can be customized to compensate for material flow characteristics and other potential variabilities. However, die wear can lead to gradual increases in tolerance deviations over time, so regular maintenance and replacement of worn-out dies are critical for maintaining precision.
- Press Machine Capabilities: The precision of the press machine used in stamping directly affects the tolerance of the final part. Hydraulic and mechanical presses can be calibrated to exert controlled force, allowing for consistent shaping of the material. Press speed, ram stroke, and force distribution all impact the accuracy of the stamping process. Faster stamping speeds can lead to slightly looser tolerances, as the time available for material flow and die interaction is reduced.
- Material Springback: Springback is the tendency of the material to return to its original shape after being deformed. This effect is more pronounced in certain materials and can result in parts that do not meet the required dimensions. Springback can be compensated for in stamping by adjusting the die design to overbend the material, allowing it to “snap back” to the correct shape once the die is removed. However, this compensation must be calculated carefully, as improper adjustments can lead to additional dimensional issues.
- Part Complexity: The complexity of the stamped part also influences the achievable tolerance. Simple, shallow parts are easier to form with tight tolerances, while deep-drawn parts or those with intricate features can present challenges. More complex parts may require additional processing or tooling adjustments to maintain desired tolerances, particularly if features like holes, slots, or raised elements are involved.
- Automation and Repeatability: One of the primary advantages of stamping over metal spinning is the level of automation and repeatability it offers. Stamping processes are often highly automated, with parts fed into the die using robotic systems or conveyors. This consistency leads to a higher level of precision, as the same die and press are used to produce large volumes of parts, reducing the potential for human error. In contrast, metal spinning is often more manual, which can lead to variability between parts.
Tolerances in Stamping
Stamping can achieve significantly tighter tolerances than metal spinning. Common tolerances for stamping can range from ±0.001 inches to ±0.005 inches for simple, flat parts. For more complex stamped parts, tolerances may vary between ±0.005 inches and ±0.010 inches, depending on the part’s geometry and material. In high-precision stamping applications, such as in the automotive or electronics industries, tolerances can be as tight as ±0.001 inches, which is generally considered a standard for most stamping operations.
Post-Stamping Processes
Like metal spinning, stamping may require secondary operations to achieve final tolerances. These operations include deburring, trimming, and hole punching, which can further refine the part’s dimensions. Some stamped parts also require additional heat treatments, coatings, or surface finishing to meet performance specifications. In contrast to metal spinning, where parts are often directly machined after spinning, stamping tolerances are typically tight enough to minimize the need for secondary machining, though additional operations can still improve dimensional accuracy.
Comparing Metal Spinning Tolerance and Stamping Tolerance
When comparing metal spinning and stamping tolerance, it is clear that both processes have their strengths and limitations. Metal spinning is more versatile and cost-effective for small production runs or complex shapes, but its tolerance range tends to be slightly looser due to the inherent manual nature of the process. Stamping, on the other hand, is ideal for high-volume production of flat or shallow parts with tight tolerances, but it requires significant initial investment in tooling and equipment.
Both processes are influenced by material properties, tooling precision, and part complexity, though stamping tends to achieve tighter tolerances overall due to its automated nature and the ability to control material flow more precisely. Metal spinning, however, is more suited for parts with intricate shapes that are difficult or impossible to produce using stamping alone.
In terms of specific applications, metal spinning is often used for aerospace, defense, and artistic industries, where complex, custom-shaped parts are required. Stamping, on the other hand, is widely used in industries like automotive manufacturing, consumer electronics, and household appliances, where high-volume production with tight tolerances is paramount.
Conclusion
The tolerance capabilities of metal spinning and stamping are influenced by various factors, including material properties, equipment precision, and part complexity. While stamping generally offers higher precision and tighter tolerances due to its automated nature and the consistency of die-based forming, metal spinning provides greater flexibility for producing complex parts. Both processes are vital to modern manufacturing and, when used appropriately, can yield parts with high accuracy and consistency, depending on the specific requirements of the application.
Ultimately, the choice between metal spinning and stamping depends on the specific needs of the project, including part geometry, material requirements, production volume, and tolerance specifications. Understanding the differences in tolerance capabilities between the two processes helps manufacturers make informed decisions to achieve the desired balance of cost, time, and precision.4o
Maximize Tooling and CNC Metal Spinning Capabilities.
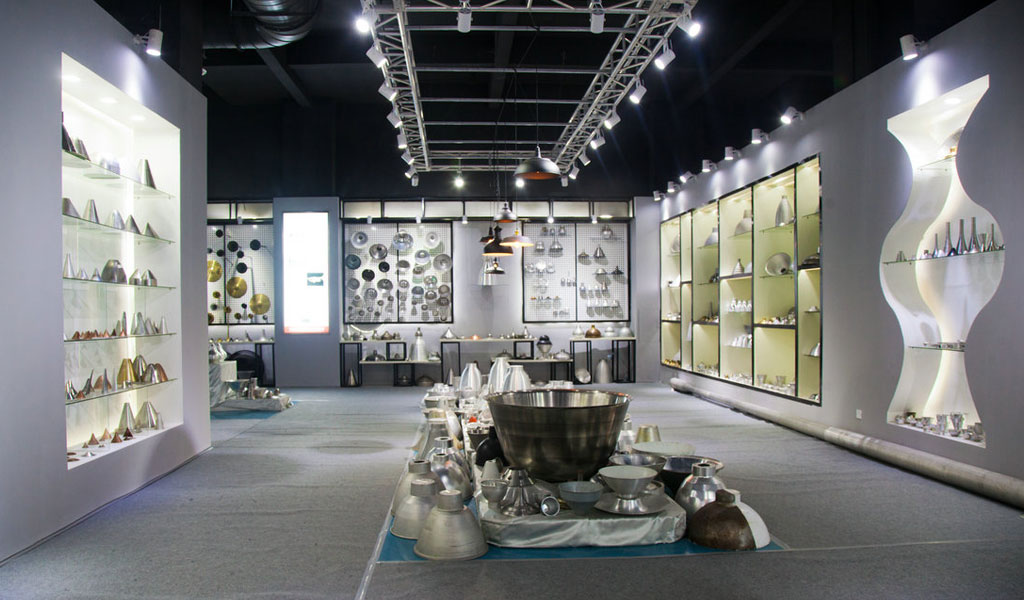
At BE-CU China Metal Spinning company, we make the most of our equipment while monitoring signs of excess wear and stress. In addition, we look into newer, modern equipment and invest in those that can support or increase our manufacturing capabilities. Our team is very mindful of our machines and tools, so we also routinely maintain them to ensure they don’t negatively impact your part’s quality and productivity.
Talk to us today about making a rapid prototype with our CNC metal spinning service. Get a direct quote by chatting with us here or request a free project review.
BE-CU China CNC Metal Spinning service include : CNC Metal Spinning,Metal Spinning Die,Laser Cutting, Tank Heads Spinning,Metal Hemispheres Spinning,Metal Cones Spinning,Metal Dish-Shaped Spinning,Metal Trumpet Spinning,Metal Venturi Spinning,Aluminum Spinning Products,Stainless Steel Spinning Products,Copper Spinning Products,Brass Spinning Products,Steel Spinning Product,Metal Spinnin LED Reflector,Metal Spinning Pressure Vessel,