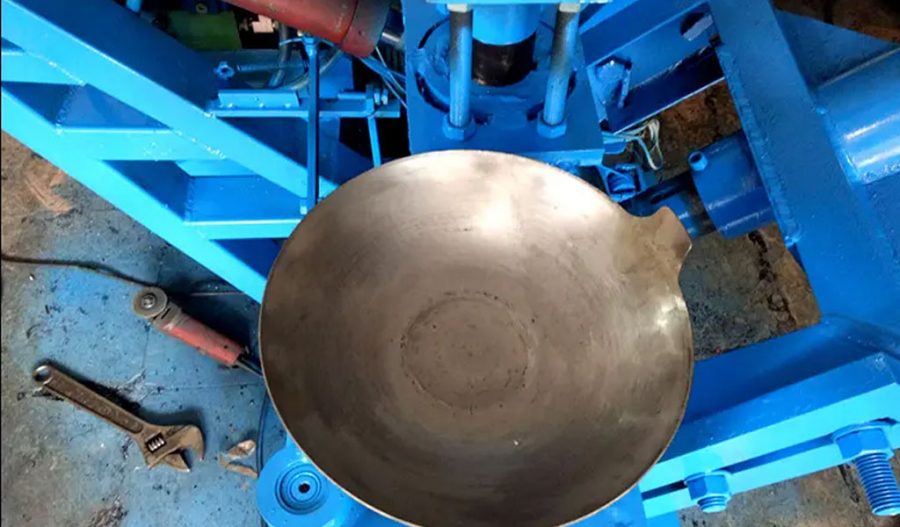
Automatic metal spinning machines represent a significant advancement in the field of metalworking, combining traditional craftsmanship with modern automation. These machines are designed to automate the process of metal spinning, a technique used to create symmetrical metal objects by rotating a metal blank on a lathe and shaping it with a tool. The automation of this process enhances precision, efficiency, and repeatability, making it suitable for mass production and complex designs.
History of Metal Spinning
Metal spinning, also known as spin forming or spinning, dates back to ancient Egypt and China, where artisans manually spun metal to create objects such as bowls and vases. The process was largely unchanged for centuries, relying on the skill and dexterity of the spinner. The industrial revolution brought about significant changes, with the introduction of powered lathes and the ability to spin larger and thicker metal blanks.
The first significant leap towards automation occurred in the mid-20th century with the development of semi-automatic spinning machines. These machines incorporated mechanical aids to assist the spinner but still required manual intervention. Fully automatic metal spinning machines emerged later, driven by advancements in computer numerical control (CNC) technology.
Principles of Metal Spinning
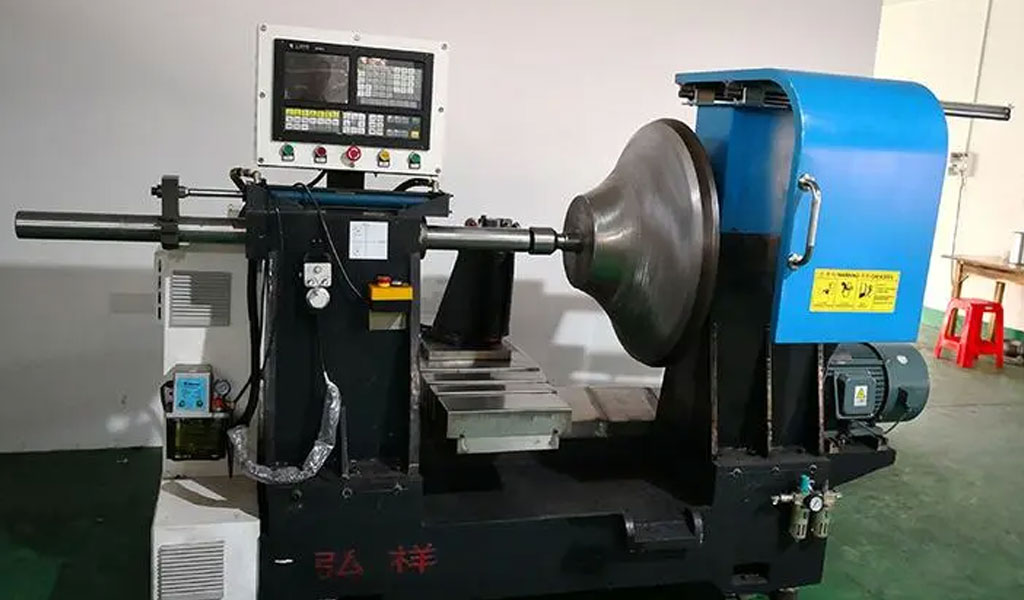
Basic Process
The basic process of metal spinning involves securing a metal blank (usually a flat disc or tube) onto a mandrel attached to a lathe. The blank is then rotated at high speed while a forming tool, usually made of steel or carbide, is pressed against it. This process shapes the metal into a desired form, which can range from simple hemispheres to complex, multi-curved profiles.
Types of Metal Spinning
There are several types of metal spinning, including:
- Conventional Spinning: The forming tool gradually deforms the metal blank into the shape of the mandrel. This method is used for creating symmetrical objects like bowls, cones, and domes.
- Shear Spinning: In shear spinning, the metal is thinned as it is shaped, reducing its thickness uniformly. This technique is used for making objects like pressure vessels and missile cones, where material strength is critical.
- Tube Spinning: This involves the spinning of tubes rather than flat blanks, allowing for the creation of cylindrical objects with varying wall thicknesses.
- Flow Forming: A variant of tube spinning, flow forming stretches the metal while maintaining the integrity of its structure, ideal for producing high-precision cylindrical components.
Evolution of Automatic Metal Spinning Machines
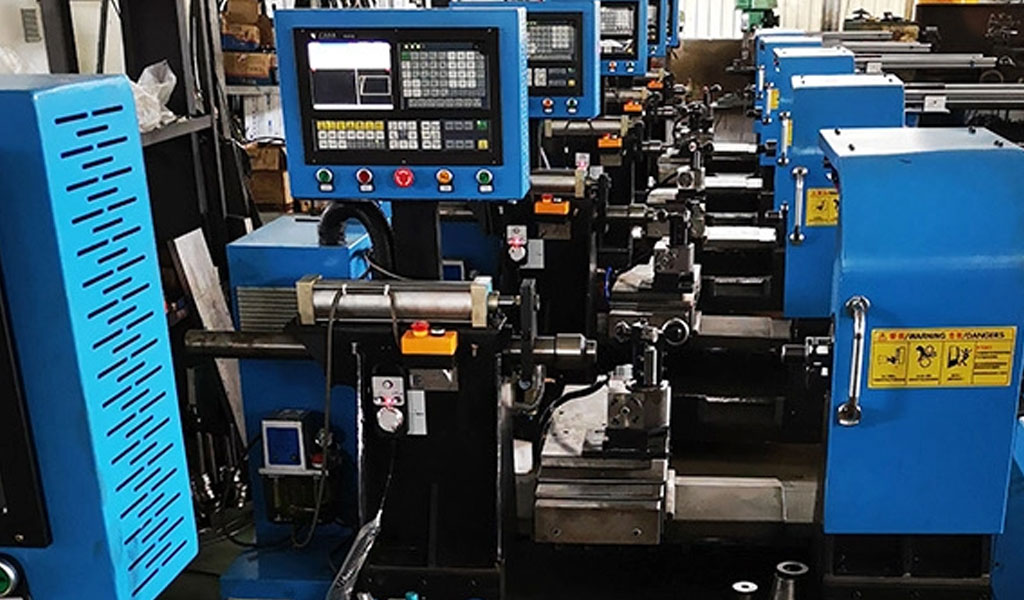
Early Innovations
The initial phase of automation in metal spinning began with mechanical aids that reduced the physical effort required from the operator. These aids included lever systems and motorized spindles. However, the process still relied heavily on the operator’s skill for precision.
Emergence of CNC Technology
The advent of CNC technology revolutionized metal spinning. CNC systems use computer software to control the movements of the lathe and forming tool, allowing for precise and repeatable operations. This development enabled the production of complex shapes with minimal manual intervention and increased the overall efficiency of the process.
Modern Automatic Metal Spinning Machines
Today’s automatic metal spinning machines are highly sophisticated, integrating advanced CNC controls with powerful motors and robust construction. These machines can handle a wide range of materials, including aluminum, steel, brass, and titanium, and are capable of producing components with high precision and consistency.
Key Features
- CNC Control: The heart of modern automatic metal spinning machines is the CNC system, which allows for programmable and precise control of the spinning process. CNC systems enable the storage and recall of multiple programs, facilitating quick setup and changeover.
- Multi-Axis Control: Advanced machines offer multi-axis control, allowing the forming tool to move in multiple directions. This capability is essential for producing complex geometries and fine details.
- Automated Tooling: Automatic tool changers and tool presetting systems enhance productivity by reducing downtime between operations. Some machines also incorporate automated lubrication and cooling systems to extend tool life.
- Sensors and Feedback Systems: Sensors monitor various parameters such as spindle speed, forming force, and tool position, providing real-time feedback to ensure accuracy and prevent defects.
- Robust Construction: Heavy-duty frames and spindles are designed to withstand the forces involved in metal spinning, ensuring stability and longevity.
Advantages of Automatic Metal Spinning Machines
- Precision and Consistency: The automation of the spinning process eliminates the variability associated with manual operations, ensuring consistent quality across batches.
- Efficiency: Automated machines can operate at higher speeds and with greater efficiency, reducing cycle times and increasing throughput.
- Complexity and Flexibility: CNC control allows for the production of intricate shapes and complex geometries that would be difficult or impossible to achieve manually.
- Cost Savings: Reduced labor costs and increased production efficiency translate to overall cost savings, making automated metal spinning economically viable for large-scale production.
- Safety: Automation reduces the physical demands on operators and minimizes the risk of injuries associated with manual spinning.
Applications of Automatic Metal Spinning Machines
Automatic metal spinning machines are used across various industries due to their versatility and precision. Some notable applications include:
Aerospace
The aerospace industry requires components with high strength-to-weight ratios and precise tolerances. Automatic metal spinning machines produce parts such as nose cones, missile casings, and engine components, where consistency and material integrity are critical.
Automotive
In the automotive sector, metal spinning is used to create parts like wheels, exhaust components, and transmission housings. The ability to produce lightweight yet strong components is particularly advantageous for improving fuel efficiency and performance.
Lighting
The lighting industry utilizes metal spinning to manufacture reflectors, housings, and other components. The reflective surfaces and precise shapes produced by spinning enhance the efficiency and aesthetics of lighting fixtures.
HVAC
Heating, ventilation, and air conditioning (HVAC) systems benefit from metal-spun components such as fan blades, ducting, and diffusers. The smooth surfaces and precise dimensions achieved through spinning improve airflow and system efficiency.
Medical Equipment
Medical devices and equipment often require custom-shaped components made from biocompatible materials. Metal spinning is used to create surgical instruments, implants, and diagnostic equipment housings.
Consumer Goods
From kitchenware to musical instruments, metal spinning is employed to produce a wide range of consumer goods. The process allows for the creation of aesthetically pleasing and functional products with consistent quality.
Challenges and Future Directions
Challenges
- Initial Investment: The cost of acquiring and setting up automatic metal spinning machines can be high, posing a barrier for small manufacturers.
- Skill Requirement: While automation reduces the need for manual dexterity, operators still require training to program and maintain CNC systems.
- Material Limitations: Some materials may pose challenges due to their properties, such as brittleness or high strength, requiring specialized tooling and techniques.
- Maintenance: Regular maintenance and calibration of CNC systems are essential to ensure precision and prevent downtime.
Future Directions
- Advanced Materials: Research into new materials and alloys will expand the range of applications for metal spinning, particularly in high-performance industries.
- Integration with Industry 4.0: The integration of metal spinning machines with Industry 4.0 technologies, such as IoT and AI, will enhance process monitoring, predictive maintenance, and overall efficiency.
- Sustainability: Advances in sustainable manufacturing practices, including recycling and energy-efficient processes, will make metal spinning more environmentally friendly.
- Hybrid Manufacturing: Combining metal spinning with other manufacturing processes, such as additive manufacturing, will open new possibilities for creating complex and high-performance components.
Conclusion
Automatic metal spinning machines represent a fusion of traditional craftsmanship and modern technology, offering precision, efficiency, and versatility in metalworking. With applications spanning multiple industries, these machines play a crucial role in the production of high-quality components. As technology continues to advance, the capabilities of automatic metal spinning machines will further expand, driving innovation and enhancing manufacturing processes across the globe.
Maximize Tooling and CNC Metal Spinning Capabilities.
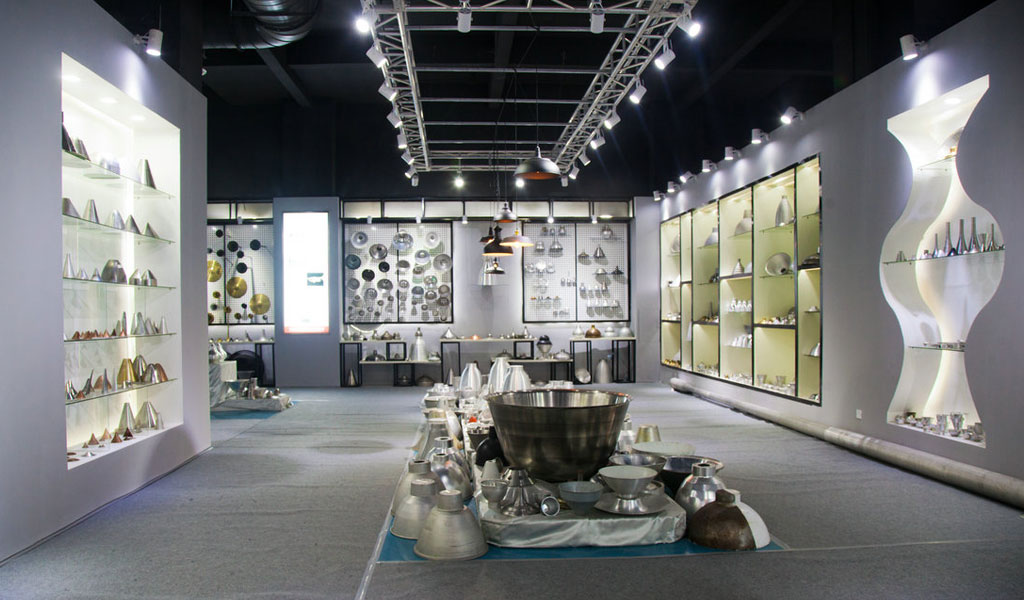
At BE-CU China Metal Spinning company, we make the most of our equipment while monitoring signs of excess wear and stress. In addition, we look into newer, modern equipment and invest in those that can support or increase our manufacturing capabilities. Our team is very mindful of our machines and tools, so we also routinely maintain them to ensure they don’t negatively impact your part’s quality and productivity.
Talk to us today about making a rapid prototype with our CNC metal spinning service. Get a direct quote by chatting with us here or request a free project review.
BE-CU China CNC Metal Spinning service include : CNC Metal Spinning,Metal Spinning Die,Laser Cutting, Tank Heads Spinning,Metal Hemispheres Spinning,Metal Cones Spinning,Metal Dish-Shaped Spinning,Metal Trumpet Spinning,Metal Venturi Spinning,Aluminum Spinning Products,Stainless Steel Spinning Products,Copper Spinning Products,Brass Spinning Products,Steel Spinning Product,Metal Spinnin LED Reflector,Metal Spinning Pressure Vessel,