
Years from now, when reviewing the domestic manufacturing progress of major equipment in China, September 6, 2013, will stand out as a significant milestone. On this day, China’s first large-scale powerful spinning equipment, the “SY-100L Large Vertical CNC Powerful Spinning Machine,” officially passed the acceptance test by the user unit, the Xi’an Aerospace Propulsion Machinery Factory of the China Aerospace Corporation. After ten years of technological preparation and development, supported by the major science and technology project “High-end CNC Machine Tools and Basic Manufacturing Equipment,” the hundred-ton CNC spinning equipment has finally met expectations, passed user trials, and was officially delivered for use.
On September 6, a large-scale CNC powerful spinning equipment and technology application promotion conference was held in Xi’an, hosted by the Implementation Management Office of the “High-end CNC Machine Tools and Basic Manufacturing Equipment” science and technology major project, and organized by the Beijing Aeronautical Manufacturing Engineering Research Institute, the Xi’an Aerospace Propulsion Machinery Factory, the AVIC Aviation Specialized Equipment Research and Development Engineering Center, and the AVIC Aviation Manufacturing Technology Center. At the conference, Wang Fuchang, Inspector of the Equipment Department of the Ministry of Industry and Information Technology, and Academician Cao Chunxiao from the Chinese Academy of Sciences gave high praise to the equipment.
The Largest in Asia
On September 6, at the Xi’an Aerospace Propulsion Machinery Factory, a formerly state-secret unit, reporters observed the process of spinning large thin-walled parts during the acceptance of the SY-100L Large Vertical CNC Powerful Spinning Machine.
“14 meters above ground, 3 meters underground.” The first impression of this large machine is imposing. Huang Guojun, Deputy General Manager of CITIC Heavy Industries Group’s Casting and Forging Sales Company, explained from a professional perspective that although this machine is not very large compared to other large equipment manufactured by the company, it requires very high technical parameters. The successful development after ten years and the participation of many parties highlight its significance and value. Moreover, as a hundred-ton spinning equipment, it is not only unique in China but also the largest in Asia. Currently, besides the United States and Russia, only China can achieve this level in this field of technology.
What does it mean to sharpen a sword for ten years? Zhang Jun, Director of the Beijing Aeronautical Manufacturing Engineering Research Institute of AVIC, explained that the development of the large vertical CNC powerful spinning equipment mainly meets the manufacturing needs of large thin-walled rotating parts in aviation, aerospace, shipbuilding, nuclear industry, and chemical industry. To address the manufacturing bottlenecks of urgently needed high-thrust launch rockets, missiles, aircraft engines, and to promote the application of spun structural parts in large aircraft, aircraft engines, missiles, and large pressure vessels, filling the strategic gap in China, the Xi’an Aerospace Propulsion Machinery Factory initiated the development project for large CNC powerful spinning machines in 2001. In early 2004, it formally signed a contract with the Beijing Aeronautical Manufacturing Engineering Research Institute of AVIC for the development of the equipment. This project was listed by the Ministry of Industry and Information Technology as a 2011 topic of the national “High-end CNC Machine Tools and Basic Manufacturing Equipment” science and technology major project (referred to as “04 CNC Machine Tools Project”). With strong assistance from relevant component manufacturers such as Zhejiang University, Wuhan Heavy Machine Tool Co., Ltd., CITIC Heavy Industries, and Jinan Second Machine Tool Works, the Beijing Aeronautical Manufacturing Engineering Research Institute of AVIC and the Xi’an Aerospace Propulsion Machinery Factory overcame various difficulties and achieved the equipment’s assembly at the user site in November 2011. By November 2012, the equipment’s static, dynamic, and functional debugging was completed, and testing commenced.
As of now, after more than six months of spinning process trials, the equipment shows high overall structural strength, good rigidity, and high control precision, with advanced functions such as synchronous feeding, staggered spinning, and intelligent pressure adjustment. Its overall performance is excellent, and the performance indicators of the spun parts meet the user’s requirements. Its spinning roller thrust and the size of parts it can spin are the largest in Asia.
Wang Decheng, Vice President of the Mechanical Science Research Institute, gave high praise to the successful development of this equipment. He said it represents a new breakthrough in spinning equipment, following the 36,000-ton extrusion machine and 80,000-ton forging machine of the “04 CNC Machine Tools Project.” The successful development of this project achieved two major breakthroughs: in technology and equipment. Firstly, the breakthrough in technology. While two years ago, the “04 CNC Machine Tools Project” achieved breakthroughs in extrusion and forging technologies, today it has achieved a new breakthrough in spinning technology. This is an important realization of the “04 CNC Machine Tools Project’s” goal of solving large-scale CNC forming.
The breakthrough in equipment is mainly reflected in: it will strongly support the demand for large thin-walled rotating parts forming in four major areas: aerospace, shipbuilding, power generation, and automotive. The “04 CNC Machine Tools Project” was originally aimed at these four fields. This equipment significantly breaks the constraints imposed by foreign technology blockades on the development of these fields, compensates for the deficiencies in existing forming processes and equipment, and enhances the coverage capabilities of large, complex, and precise forming equipment.
User Attraction
Reflecting on the ten-year development process, experts involved in the equipment’s development express their appreciation. The large vertical CNC powerful spinning equipment possesses the high precision of CNC machine tools, the strong rigidity and heavy load characteristics of heavy machine tools. The research and project initiation were challenging, with high design difficulty, precision requirements, complex structure, difficulties in procuring key parts, oversized components, manufacturing challenges, coordination difficulties among various units and departments, assembly challenges, inspection difficulties, and spinning difficulties, along with funding and time constraints. The successful development of the large vertical CNC powerful spinning machine marks a new height in China’s manufacturing technology for large thin-walled rotating metal parts and is a result of collaboration between industry, academia, and research.
In addition to breakthroughs in technology and equipment, Wang Decheng told reporters that the project’s breakthrough also lies in its success as a model of the “04 CNC Machine Tools Project” adherence to the industry-university-research-use cooperation model. This machine involves multiple technological collaborations, including large casting and forging parts, hydraulic control, etc., each of which poses a significant challenge. It should be said that it represents a challenge to extreme manufacturing. Following the project office’s suggestions and the leading unit’s full organization, a cooperative advantage between industry, academia, and research was formed.
Wang Decheng also believes that the ten-year preparation and breakthrough under the support of the “04 CNC Machine Tools Project” once again proves the necessity and core role of major national projects, especially the “04 CNC Machine Tools Project,” in the development of strategic emerging industries such as national defense and military industry. High-end technology is not achieved overnight; long-term preparation and national support are essential.
Wang Fuchang agreed with this view. He said that the “04 CNC Machine Tools Project” has explored, improved, and adjusted continuously during its implementation, emphasizing four aspects: Firstly, demand-driven, with the projects included being urgently needed for national economic and defense construction, not merely to meet certain indicators.
Secondly, close integration of industry, academia, and research, particularly between manufacturers and users. Because manufacturing enterprises are not familiar with user needs and process issues, the current projects are mostly led by users.
Thirdly, integration of main machines with CNC systems, tools, and other functional components. Although domestically produced CNC systems and functional components still have gaps in practical applications, especially in high-end equipment studied in major projects, efforts are emphasized to provide opportunities for domestic functional components to participate.
Fourthly, emphasis on “use.” Current projects require users to use the equipment for at least six months. No development can guarantee 100% success, so usage is crucial.
Wang Fuchang indicated that the “04 CNC Machine Tools Project” has been implemented for five years and is currently undergoing a mid-term evaluation to clarify the focus of future work. He hopes relevant enterprises will actively participate and contribute ideas for the implementation of the project, especially enterprises in aerospace and other fields, to provide suggestions for the development of urgently needed equipment.
Maximize Tooling and CNC Metal Spinning Capabilities.
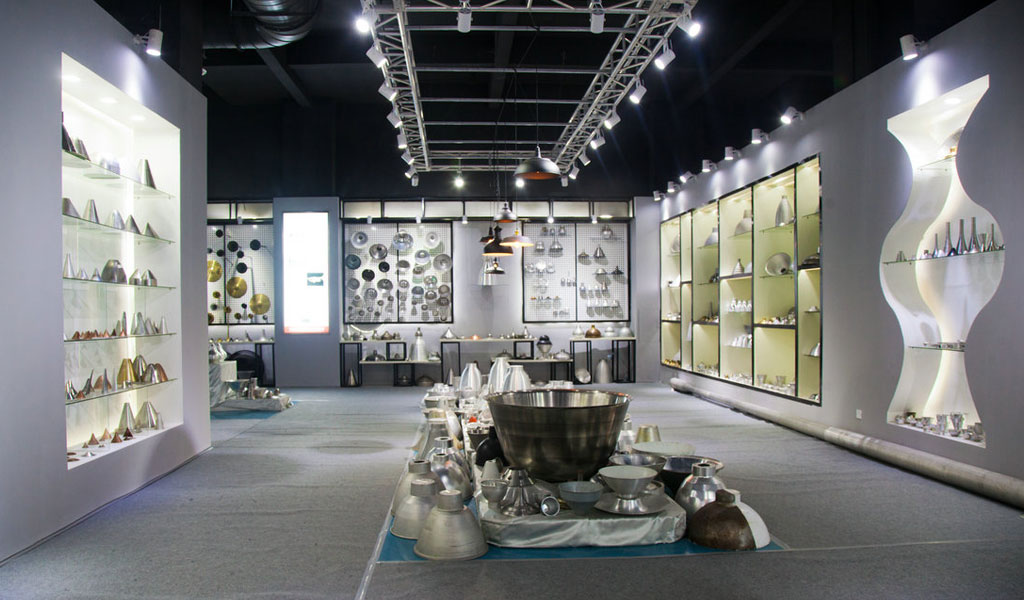
At BE-CU China Metal Spinning company, we make the most of our equipment while monitoring signs of excess wear and stress. In addition, we look into newer, modern equipment and invest in those that can support or increase our manufacturing capabilities. Our team is very mindful of our machines and tools, so we also routinely maintain them to ensure they don’t negatively impact your part’s quality and productivity.
Talk to us today about making a rapid prototype with our CNC metal spinning service. Get a direct quote by chatting with us here or request a free project review.
BE-CU China CNC Metal Spinning service include : CNC Metal Spinning,Metal Spinning Die,Laser Cutting, Tank Heads Spinning,Metal Hemispheres Spinning,Metal Cones Spinning,Metal Dish-Shaped Spinning,Metal Trumpet Spinning,Metal Venturi Spinning,Aluminum Spinning Products,Stainless Steel Spinning Products,Copper Spinning Products,Brass Spinning Products,Steel Spinning Product,Metal Spinnin LED Reflector,Metal Spinning Pressure Vessel,