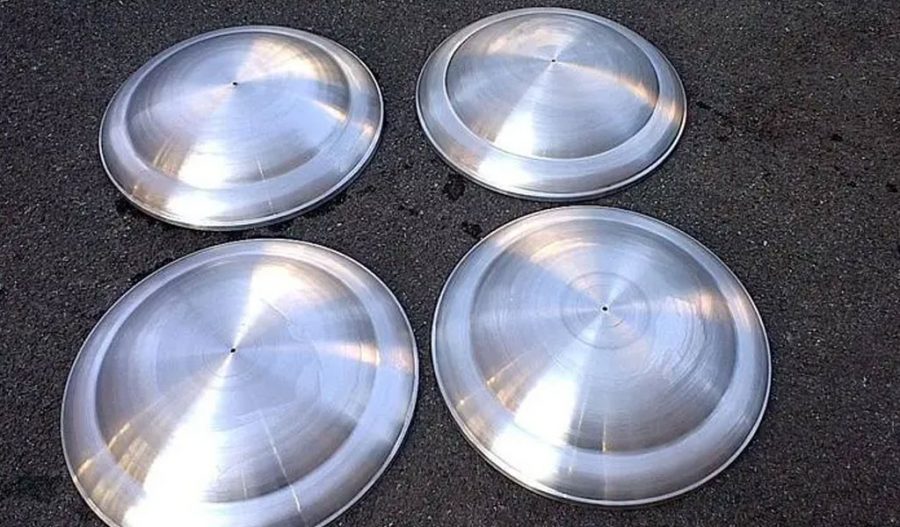
The combination of hemispherical spinning and 3D laser cutting is an advanced manufacturing process that integrates two distinct but complementary technologies: spinning and laser cutting. This hybrid approach offers significant advantages in terms of precision, material utilization, and the production of complex geometries that are often challenging or impossible to achieve using traditional techniques.
Hemispherical spinning, often referred to as metal spinning, is a metal-forming process that uses a rotating mandrel and a tool to shape a metal blank into a desired form, typically a hollow, axially symmetric object. The process is especially useful for creating spherical and hemispherical shapes, which have applications in industries such as aerospace, automotive, defense, and consumer products.
3D laser cutting, on the other hand, involves the use of high-powered lasers to cut materials along complex 3D paths with high precision. The technology has advanced rapidly in recent years due to improvements in laser power, accuracy, and automation capabilities. The combination of these two techniques allows manufacturers to create highly complex components with minimal material waste, while offering flexibility in design and the ability to rapidly iterate through prototypes.
This article explores the history, principles, processes, applications, and future potential of combining hemispherical spinning and 3D laser cutting, emphasizing the synergistic benefits offered by this integration in modern manufacturing.
Hemispherical Spinning
The roots of metal spinning can be traced back several millennia. Traditional spinning techniques were used as early as the 4th century BCE in China and the Middle East, where metalworkers shaped small bowls and other vessels from soft metals. Early spinning was entirely manual, relying on basic lathe-like devices. It remained largely an artisan technique used for creating symmetrical objects in small quantities.
Industrialization in the 19th century brought about the mechanization of spinning. In particular, the advent of powered lathes allowed for the development of more consistent and larger-scale production processes. The technique evolved further in the 20th century with the introduction of more sophisticated machinery, enabling the spinning of harder metals like steel and aluminum.
By the mid-20th century, spinning had become a highly versatile process used in many industries, particularly in the production of spherical and hemispherical components for pressure vessels, domes, and other structures requiring robust and geometrically precise designs.
3D Laser Cutting
Laser cutting technology emerged in the mid-20th century, initially for drilling holes in diamond dies. The development of carbon dioxide (CO₂) lasers in the 1960s made it possible to cut materials like steel, and by the 1970s, the first industrial applications of laser cutting began to appear.
By the late 20th century, 3D laser cutting technology had advanced to the point where it could handle complex, multi-axis cutting tasks. This made it an attractive option for industries requiring high precision, such as aerospace, automotive, and electronics manufacturing.
As lasers became more powerful and control systems became more precise, 3D laser cutting systems could be integrated into automated production lines. The advent of fiber lasers, known for their high efficiency and beam quality, further enhanced the capabilities of 3D laser cutting, making it possible to cut through thicker materials while maintaining high precision and minimal heat-affected zones.
Integration of Hemispherical Spinning and 3D Laser Cutting
The idea of combining spinning and laser cutting technologies emerged as manufacturers sought ways to produce complex, axially symmetric components with intricate features. Hemispherical spinning provides the capability to form large, rounded shapes, while 3D laser cutting allows for precise cutting of features like holes, slots, and contours into the spun parts.
The integration of these processes was initially driven by industries such as aerospace and defense, where complex, lightweight, and geometrically intricate parts are often required. Over time, this hybrid approach has spread to other industries, including automotive and consumer goods manufacturing.
Combining Hemispherical Spinning and 3D Laser Cutting
The integration of hemispherical spinning and 3D laser cutting into a single manufacturing process offers numerous advantages, particularly when producing complex, symmetric parts with intricate features.
The combination process typically begins with hemispherical spinning to create a blank in the desired shape. After spinning, the part is transferred to a 3D laser cutting system, where intricate features like holes, slots, or other cutouts are added.
In some advanced manufacturing environments, the processes can be combined into a single automated workflow. For example, a robot might move the spun part directly from the spinning lathe to the laser cutting station, reducing handling time and increasing production efficiency.
Advantages of the Combined Process
- Precision: Hemispherical spinning provides high geometric accuracy in forming the basic shape, while 3D laser cutting offers precision in adding complex features.
- Material Efficiency: Both processes are highly efficient in terms of material usage. Hemispherical spinning minimizes material waste by deforming a blank into shape rather than cutting away excess material. Laser cutting precisely removes material where necessary, further reducing waste.
- Design Flexibility: Combining the two processes allows manufacturers to produce parts with complex geometries that would be difficult to achieve using traditional methods. For example, a hemispherical dome with precisely placed cutouts or openings can be manufactured in a single workflow.
- Cost-Effectiveness: The combination of these processes can reduce tooling costs and lead times compared to more traditional methods such as stamping or casting. This is particularly important for industries where rapid prototyping and iterative design processes are common.
Maximize Tooling and CNC Metal Spinning Capabilities.
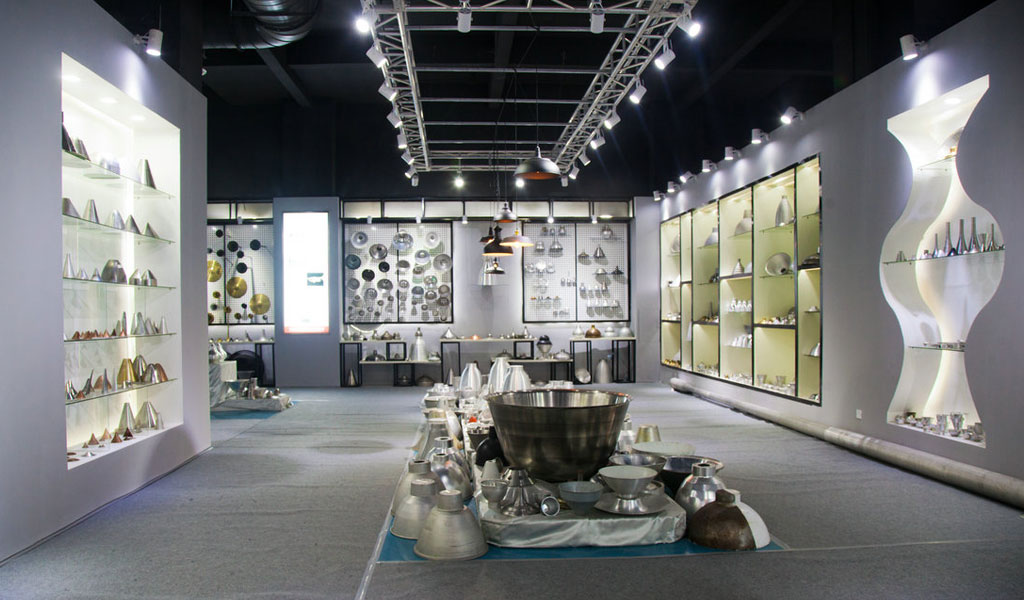
At BE-CU China Metal Spinning company, we make the most of our equipment while monitoring signs of excess wear and stress. In addition, we look into newer, modern equipment and invest in those that can support or increase our manufacturing capabilities. Our team is very mindful of our machines and tools, so we also routinely maintain them to ensure they don’t negatively impact your part’s quality and productivity.
Talk to us today about making a rapid prototype with our CNC metal spinning service. Get a direct quote by chatting with us here or request a free project review.
BE-CU China CNC Metal Spinning service include : CNC Metal Spinning,Metal Spinning Die,Laser Cutting, Tank Heads Spinning,Metal Hemispheres Spinning,Metal Cones Spinning,Metal Dish-Shaped Spinning,Metal Trumpet Spinning,Metal Venturi Spinning,Aluminum Spinning Products,Stainless Steel Spinning Products,Copper Spinning Products,Brass Spinning Products,Steel Spinning Product,Metal Spinnin LED Reflector,Metal Spinning Pressure Vessel,