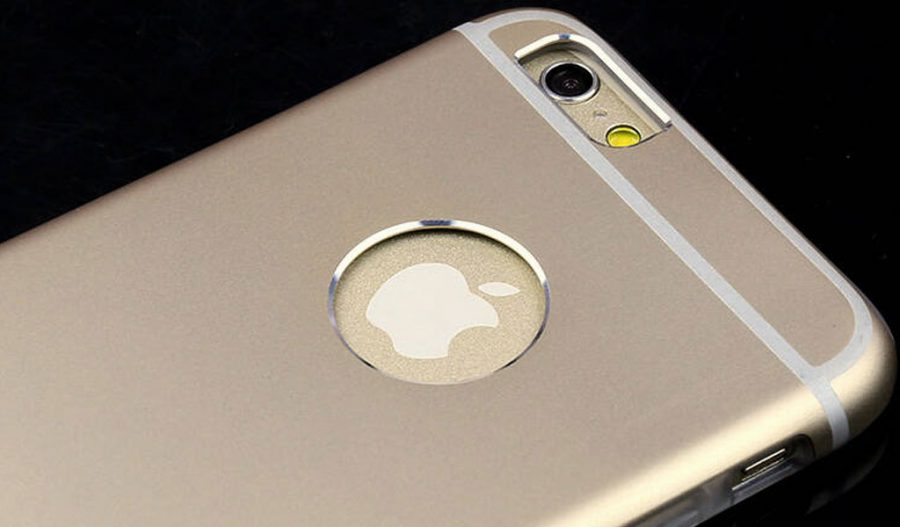
When it comes to full-metal phone casings, the first thing that often comes to mind is the unibody CNC spinning process. In this method, a solid aluminum block is die-cast into a columnar shape and then precisely machined to form the initial shape of the unibody casing. As the casing takes shape, various ports and openings are milled. This CNC spinning technique is favored by major manufacturers due to its high efficiency, precision, and consistent quality. However, its low material utilization and high production costs are significant drawbacks.
Today, we explore metal spinning technology, which offers high product precision, excellent surface finish, high material utilization, and lower production costs, effectively addressing the limitations of unibody CNC machining. Let’s take a closer look at how this innovative process can be used to create distinctive phone casings.
Precision Aluminum Forming through Stamping and Stretching
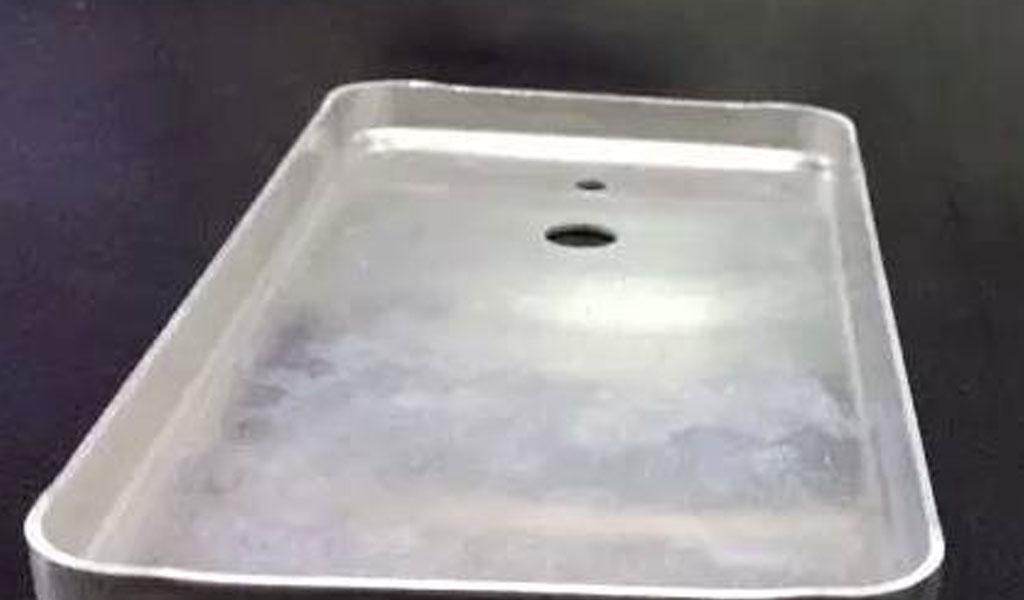
Select high-quality aluminum materials, punch and stretch them into the required shape on a punch press, and then adjust the phone casing to the appropriate size through a shaping process.
Metal Spinning Forming
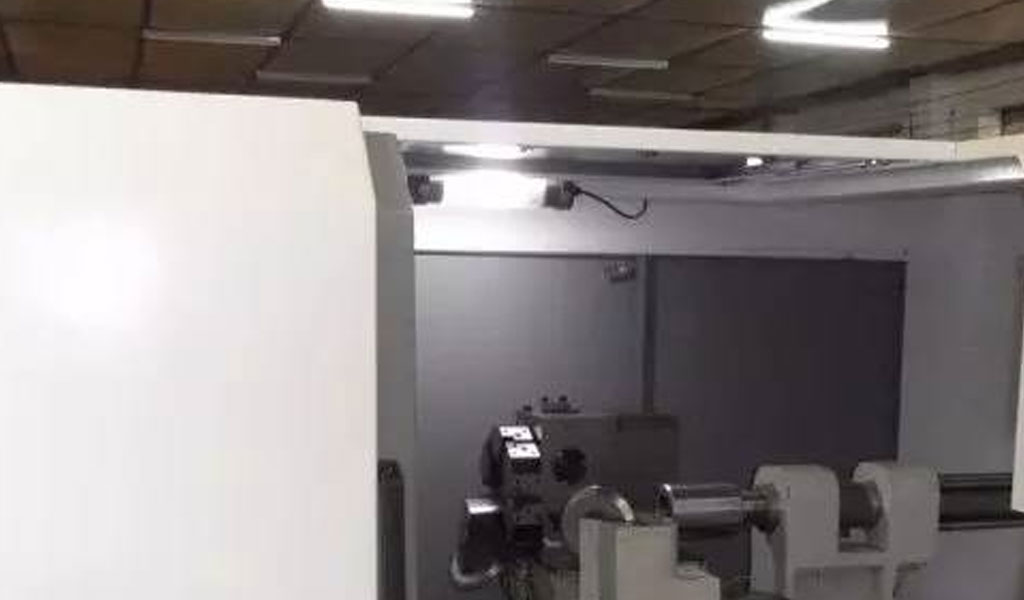
The shaped mobile phone shell is clamped on the spinning machine, and then pressure is applied to it point by point with a spinning wheel to make its four sides concavely bend to the required curvature.
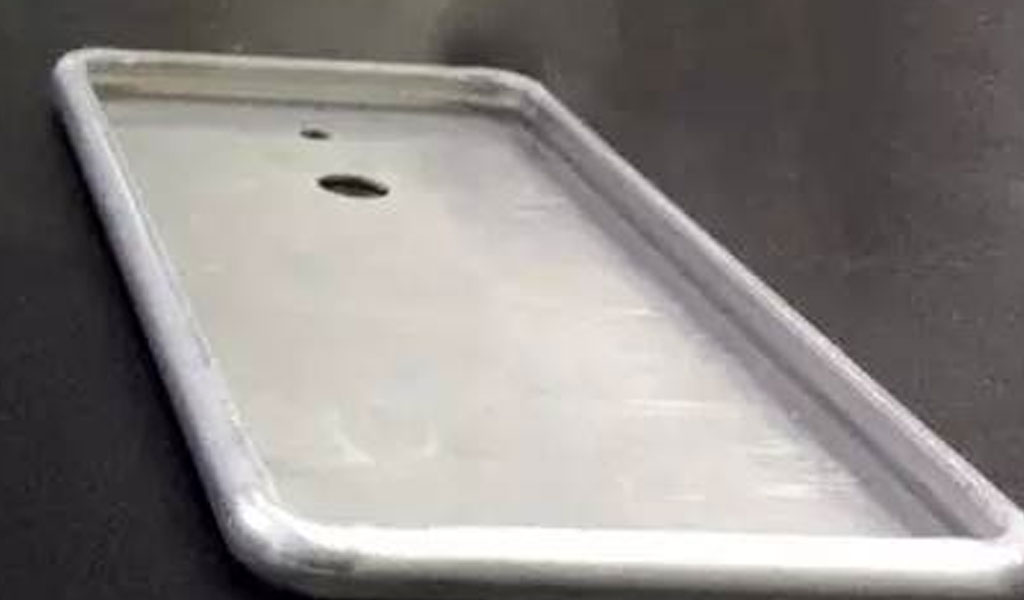
First CNC Precision Machining
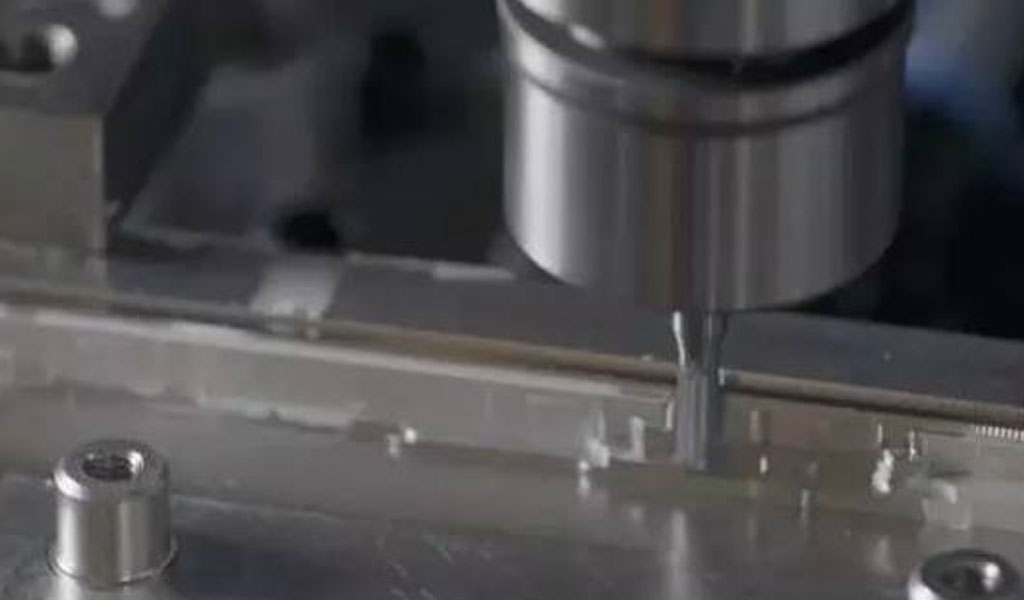
After spinning, the first CNC precision processing process begins, with 56 machine tool milling cutters used to mill out the outer shape, inner cavity, data cable interface, antenna groove and other parts of the mobile phone shell.
T Treatment
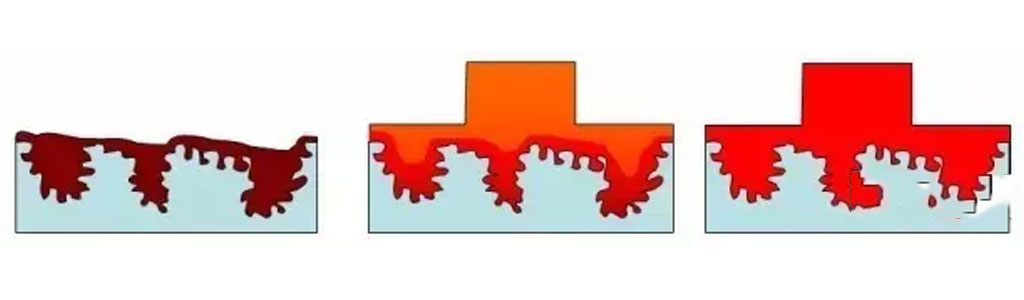
T treatment requires alkaline washing to remove impurities such as grease from the phone shell, then acid washing to neutralize and form large-sized nanopores, and finally 8 T treatments, water washing and drying. The entire T treatment process takes about 30 minutes. After the T treatment, a honeycomb pore layer with a diameter of 6-12nm can be formed on the surface of the aluminum part, which can increase the adhesion between aluminum and plastic.
Nano Injection Molding
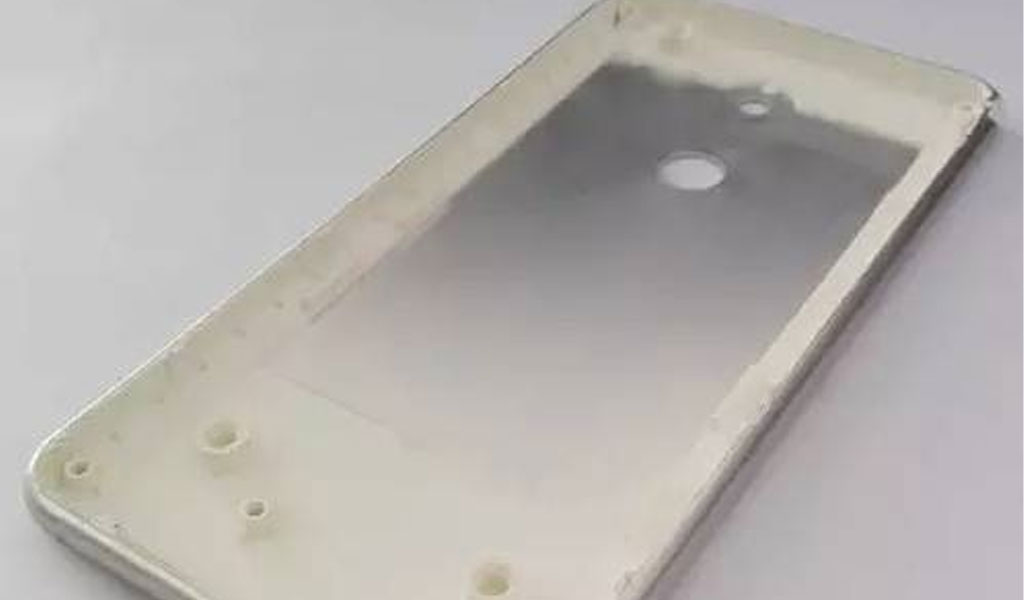
After the T treatment is completed, the mobile phone shell can be subjected to nano injection molding. Nano injection molding is to first nano-treat the metal surface, and then directly inject the plastic onto the metal surface, so that the metal and plastic can be integrally molded to obtain the internal structure and antenna slot injection molding required for the mobile phone shell.
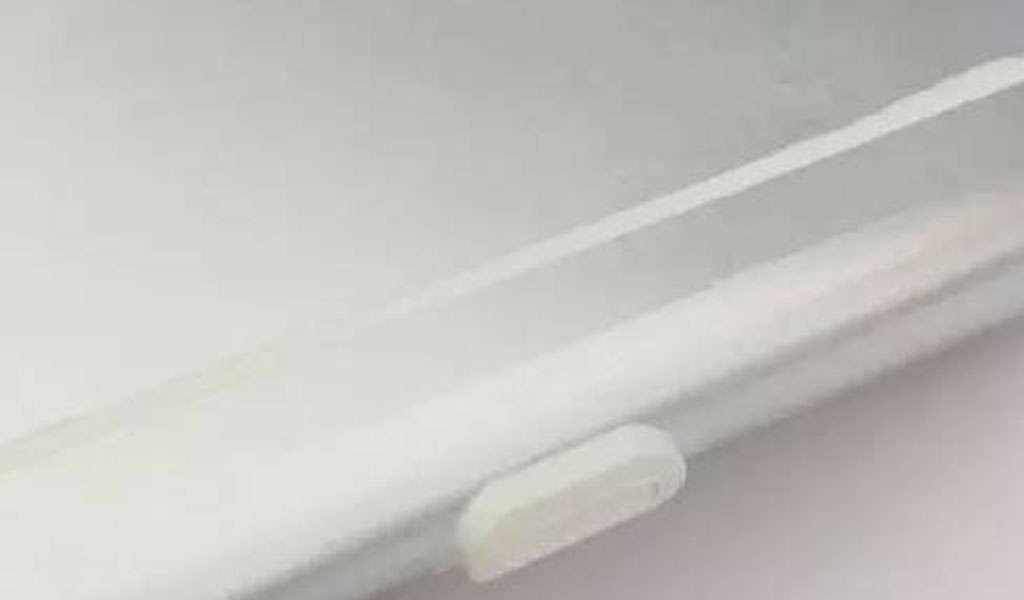
Secondary CNC Precision Machining
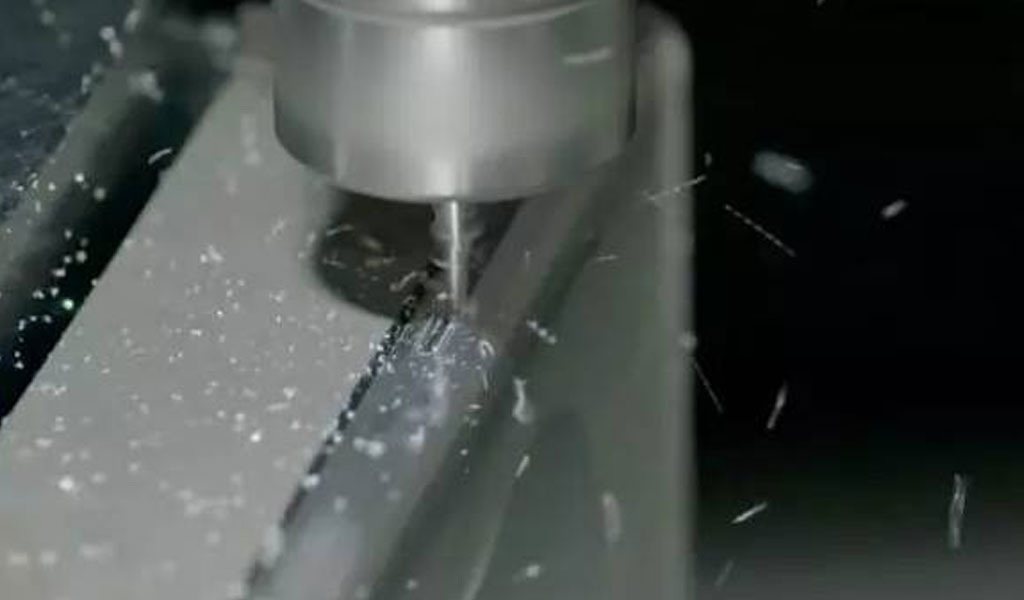
Use secondary CNC machining to mill out the data cable interface, camera hole, headphone jack, button side holes, card slot and appearance.
Polishing
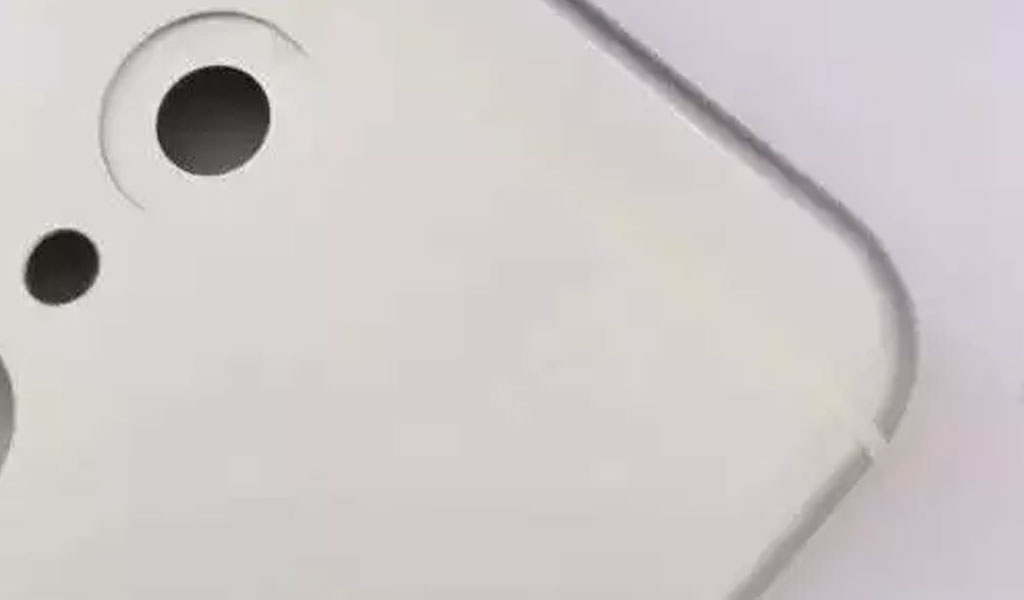
Use high-speed precision CNC machine tools for polishing to eliminate knife marks and prepare for subsequent sandblasting.
Sandblasting
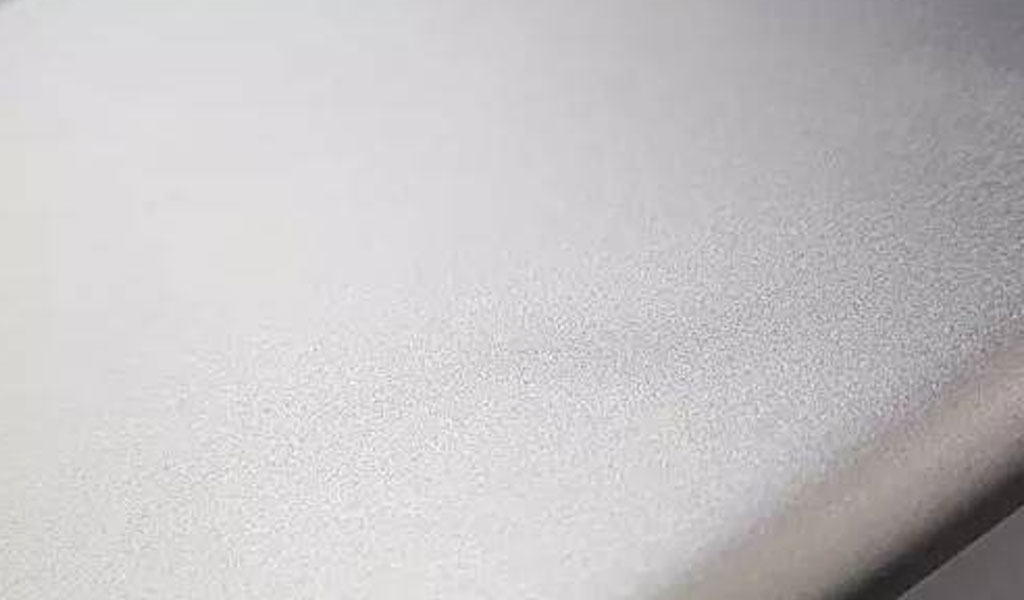
Use 170 zircon sand to treat the surface of the mobile phone shell to a frosted effect.
First Anodizing
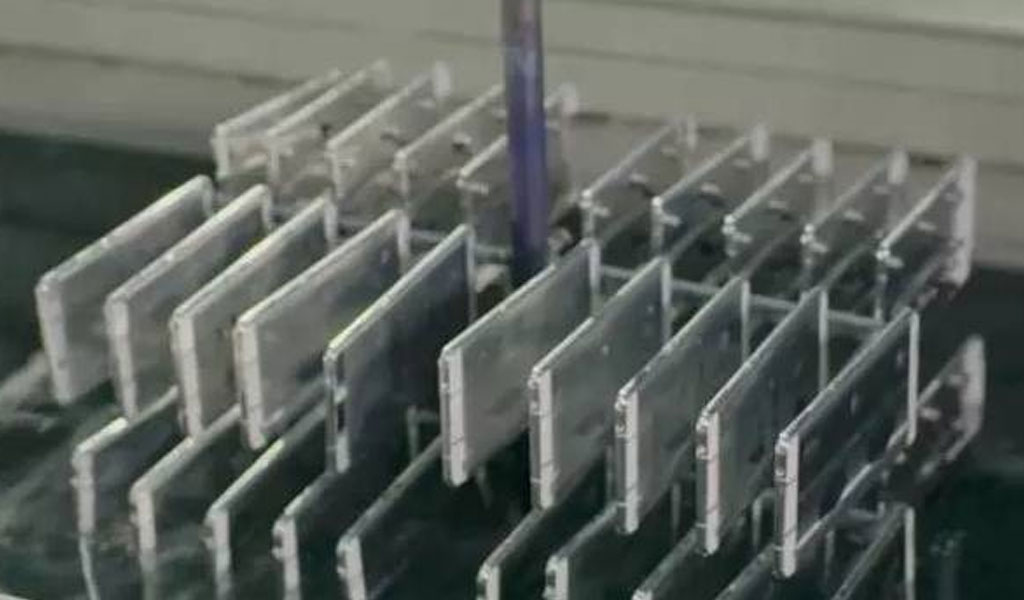
Coloring the phone case while improving the stability of the surface material
Highlight
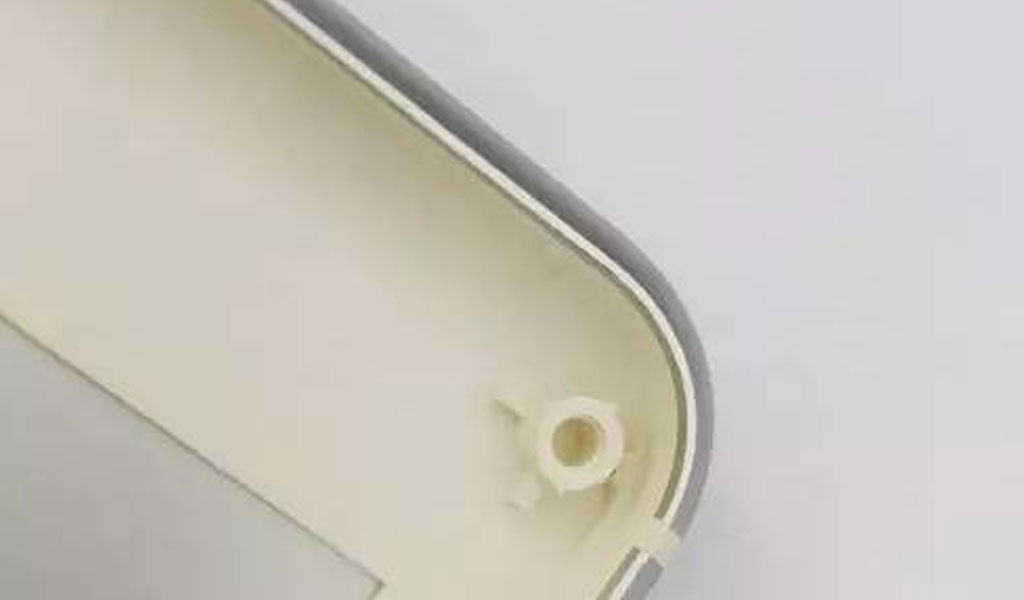
The extremely glossy cut edge design requires the use of the highest grade ultra-high speed CNC machine tools to cut the corners, a process also known as drilling or highlighting.
Second Anodizing
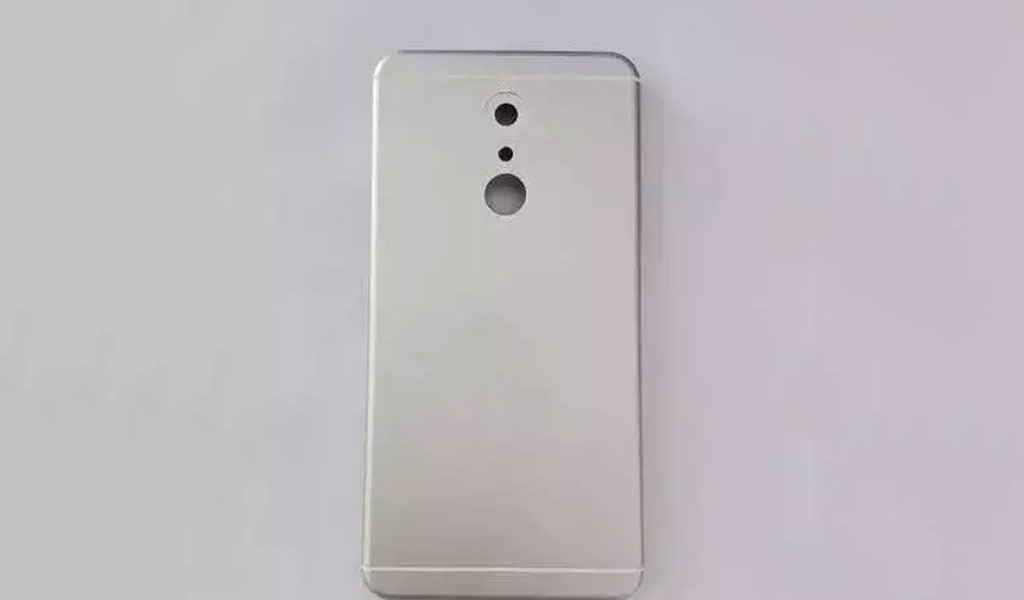
A strong and dense oxide film is formed on the surface of the mobile phone shell, which enhances wear resistance and is not easy to get dirty.
Maximize Tooling and CNC Metal Spinning Capabilities.
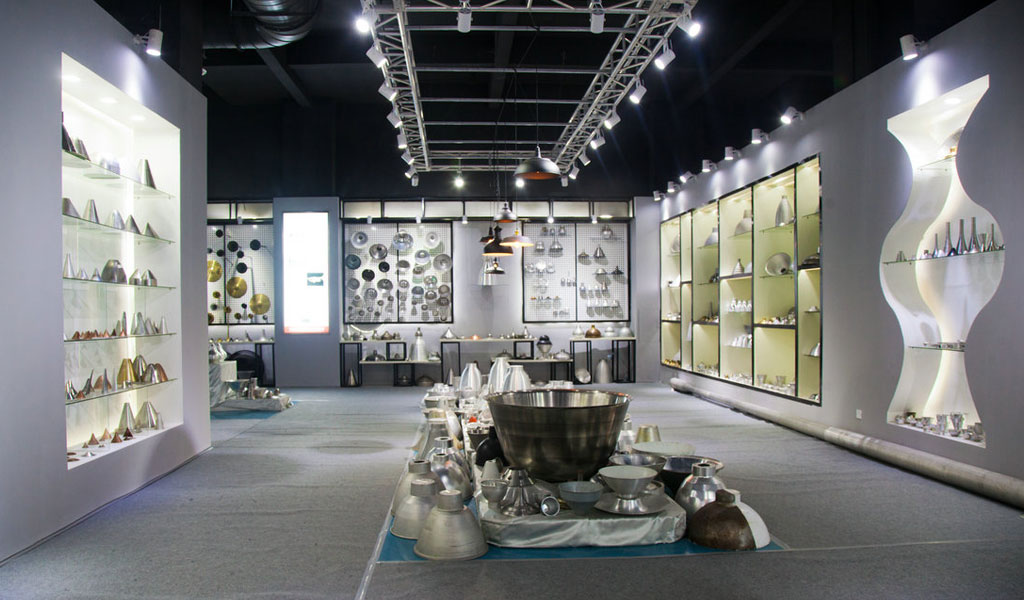
At BE-CU China Metal Spinning company, we make the most of our equipment while monitoring signs of excess wear and stress. In addition, we look into newer, modern equipment and invest in those that can support or increase our manufacturing capabilities. Our team is very mindful of our machines and tools, so we also routinely maintain them to ensure they don’t negatively impact your part’s quality and productivity.
Talk to us today about making a rapid prototype with our CNC metal spinning service. Get a direct quote by chatting with us here or request a free project review.
BE-CU China CNC Metal Spinning service include : CNC Metal Spinning,Metal Spinning Die,Laser Cutting, Tank Heads Spinning,Metal Hemispheres Spinning,Metal Cones Spinning,Metal Dish-Shaped Spinning,Metal Trumpet Spinning,Metal Venturi Spinning,Aluminum Spinning Products,Stainless Steel Spinning Products,Copper Spinning Products,Brass Spinning Products,Steel Spinning Product,Metal Spinnin LED Reflector,Metal Spinning Pressure Vessel,