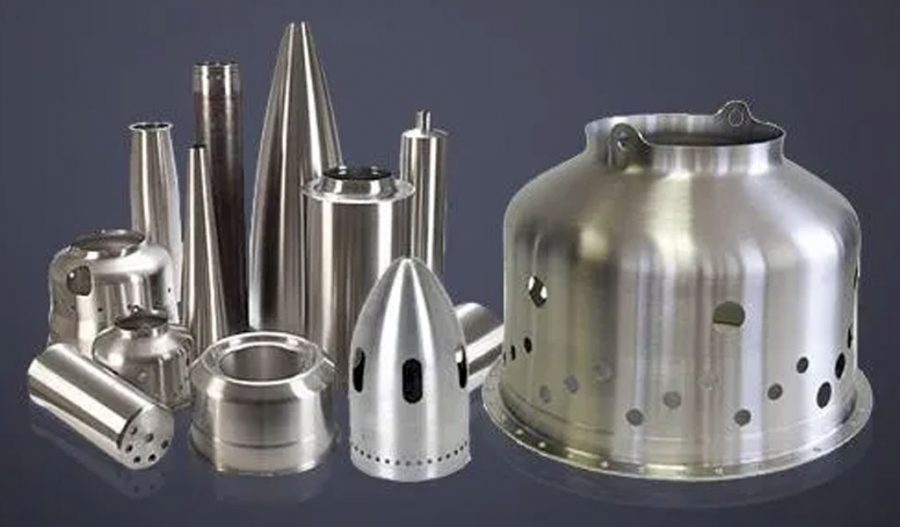
When spinning various thin-walled cross-section products, the main purpose of spinning is to change the shape of the slab, and the thickness of the slab changes little. This type of spinning is called ordinary spinning. The basic methods of ordinary spinning are: deep drawing spinning (drawing spinning), shrinking spinning (shrinking spinning) and expansion spinning (expanding spinning).
What Is Deep drawing spinning
Drawing spinning is a forming process that uses radial drawing as the main body to reduce the diameter of the blank (sheet or prefabricated part). It can also be said that it is similar to deep drawing, but it uses a core mold instead of a punch, and a spinning wheel instead of a die. It is the most important and widely used forming method in ordinary spinning. Blank bending plastic deformation is its main deformation mode.
Because the workpiece is spun by the movement of the spinning wheel, its processing conditions have greater freedom than deep drawing, and it can produce very complex rotationally symmetrical bodies. During the spinning process, there are higher requirements for the motion trajectory of the spinning wheel. Therefore, it is not an exaggeration to say that the forming technology of deep drawing and spinning is to master the law of the movement of the spinning wheel. For the motion trajectory control of the spinning wheel in forming, there are mainly A manual; B mechanical profiling; C hydraulic profiling device; D numerical control (NC or CNC); E recording and replay system (or relearning system).
Simple deep drawing and spinning
As shown in the figure above, a cylindrical spinning part with an inner diameter of d (the same as the diameter of the core mold) is made from a blank with a diameter of D0 and a thickness of t0. When D0 is small, only short cylindrical parts can be made, but the forming is very easy, and only simple deep drawing and spinning is needed. D0/d is called the drawing ratio. When its value is small, the spinning wheel only needs to move along the core mold once, that is, one-pass deep drawing and spinning can be formed. It is called simple deep drawing and spinning to distinguish it from multi-pass deep drawing and spinning. The spinning wheel of the spinning machine should only move along the core mold to ensure the gap C between it and the core mold. In actual forming, the following issues need to be considered.
- The shape of the roller. Usually, a circular roller with a diameter of D and a top corner radius of R is selected. The roller shown in the figure above is called a standard roller.
- The feed speed of the roller. Usually, it is expressed by the speed u0 (m/min) of the slide movement. However, since the rotation speed of the blank must be considered when judging the forming effect, the size of the roller movement U per blank rotation is an extremely important factor, which is called the roller feed. For example, under the condition that the feed speed U remains unchanged, if the blank rotation speed is doubled, the movement distance of the roller relative to the blank becomes 1/2 of the original, so the instantaneous forming amount becomes smaller.
- The shape of the core mold. In the case of the figure above, the core mold is cylindrical with a diameter of d and a corner radius of pm at the end. In other cases, the shape of the core mold varies with the shape of the spun part.
- The rotation speed of the blank. To determine whether the rotation speed n used can complete the processing, it is always necessary to consider it in conjunction with the feed speed of the roller. As mentioned in (2), the rotation speed can be changed under the condition that the feed speed of the rotary wheel remains unchanged, or the feed speed of the rotary wheel can be changed under the condition that the rotation speed remains unchanged.
- Size and properties of the blank The drawing ratio D0/d or the relative speed to/d of the blank is an important parameter for whether the deep drawing and spinning can proceed smoothly. For deep drawing and spinning, the material of the blank is mainly low carbon steel, low alloy steel and other materials with good plasticity.
Maximize Tooling and CNC Metal Spinning Capabilities.
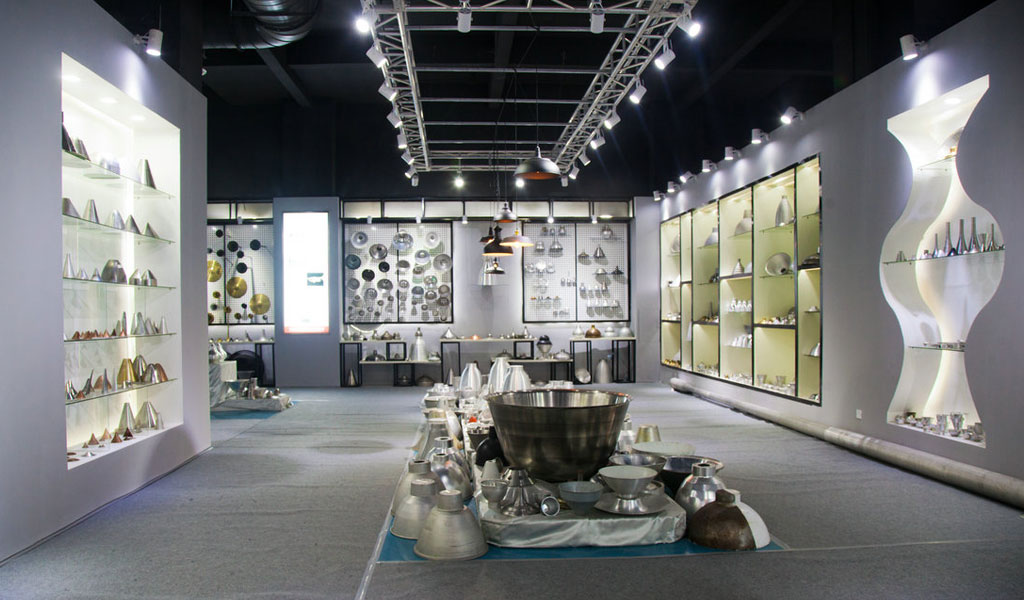
At BE-CU China Metal Spinning company, we make the most of our equipment while monitoring signs of excess wear and stress. In addition, we look into newer, modern equipment and invest in those that can support or increase our manufacturing capabilities. Our team is very mindful of our machines and tools, so we also routinely maintain them to ensure they don’t negatively impact your part’s quality and productivity.
Talk to us today about making a rapid prototype with our CNC metal spinning service. Get a direct quote by chatting with us here or request a free project review.
BE-CU China CNC Metal Spinning service include : CNC Metal Spinning,Metal Spinning Die,Laser Cutting, Tank Heads Spinning,Metal Hemispheres Spinning,Metal Cones Spinning,Metal Dish-Shaped Spinning,Metal Trumpet Spinning,Metal Venturi Spinning,Aluminum Spinning Products,Stainless Steel Spinning Products,Copper Spinning Products,Brass Spinning Products,Steel Spinning Product,Metal Spinnin LED Reflector,Metal Spinning Pressure Vessel,