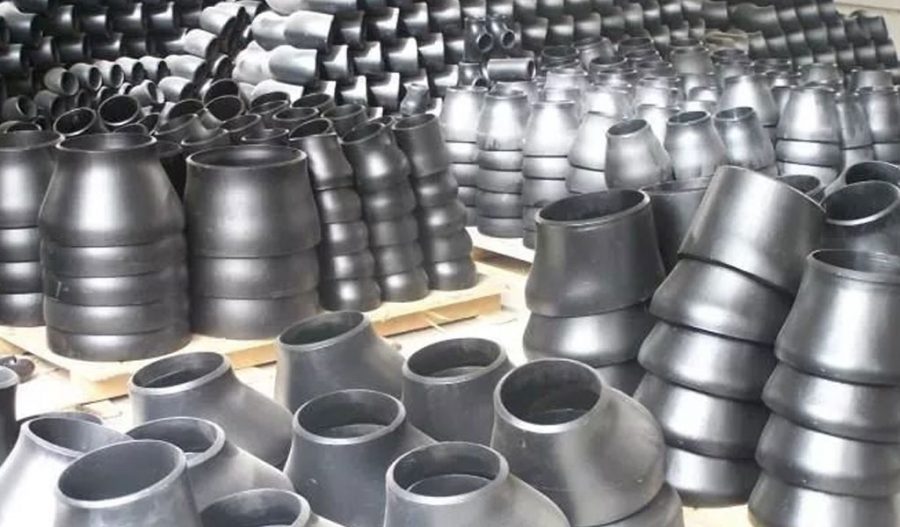
The newly developed integral hollow shaft roller is created by directly reducing and spinning the ends of a thin-walled tube to form the shaft neck. Through diameter-reduction spinning experiments on the rollers, this paper summarizes the deformation process of thin-walled tubes, analyzes the plastic deformation laws, forming mechanisms, changes in metallic properties during the spinning process, and methods to control and prevent defects in diameter-reduction spinning.
Belt conveyors are widely used in mines, ports, and other work sites, with rollers being their primary component and used in large quantities. Addressing defects in the existing roller structures, we have developed a new type of roller with a hollow shaft. The structure of the new roller is shown in Figure 1. The integral spinning hollow shaft roller is characterized by using the spinning process to form a semi-shaft structure from the roller tube, with bearings installed on the semi-shafts at both ends of the roller.
Given the thin wall thickness of the roller tubes and the lack of reference data on the forming mechanisms and deformation characteristics of diameter-reduction spinning for thin-walled tubes, it is necessary to conduct in-depth research to determine appropriate processing methods. According to the spinning requirements of the roller tubes, a dedicated thread lathe Q1319-1 was modified into a diameter-reduction spinning test device for the rollers, as shown in Figure 2.
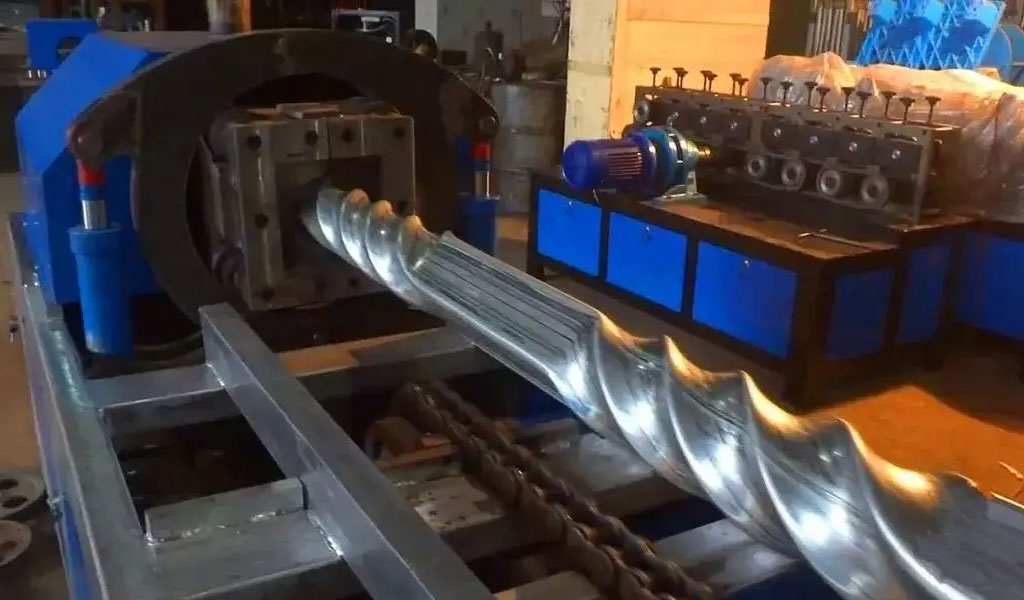
By conducting diameter-reduction spinning experiments on hollow shaft rollers, we analyze the deformation process of the roller tubes, grasping the deformation characteristics during the spinning process to determine appropriate spinning process parameters for thin-walled tubes.
Spinning Deformation Process
Diameter-reduction spinning of thin-walled cylindrical parts involves local, progressive plastic deformation. During deformation, the displacement, stress, and strain distribution at various points on the workpiece are highly uneven, with the plastic zone surrounded by a large elastic zone, which constantly changes positions during spinning. A typical spinning pass includes three stages: initial spinning, stable spinning, and final spinning. In the stable spinning stage, deformation force stabilizes, making the spinning process easier to control. Unlike the stable stage, initial and final spinning stages involve abrupt changes in deformation force, making them critical control stages.
When the spinning wheel first contacts the blank, it should do so after the blank has stabilized in rotation. There is a significant speed difference and friction between the spinning wheel and the blank, leading to uneven deformation force and localized bending or imprinting, depending on the blank’s thickness. If the spinning wheel’s radius is too large, wrinkles may form on the blank surface. Excessive diameter reduction of a thin blank can cause local bulging and deformation at the workpiece’s front edge.
For thin-walled cylindrical parts, when the spinning wheel approaches the outward flange, uneven deformation makes stress concentration and potential fracture more likely. Therefore, maintaining a certain distance between the final spinning point and the blank edge helps avoid unstable deformation. Excess metal at the outer end can be removed by milling.
Mechanisms of Hot Spinning Forming for Integral Rollers
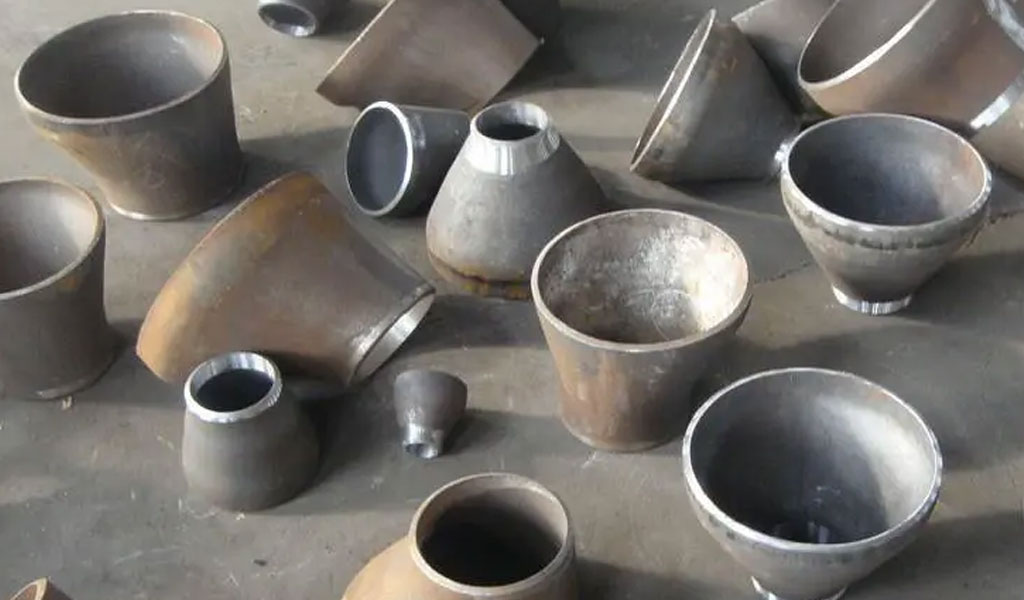
The integral roller is formed from a steel tube blank using air molds (without core molds) and is spun after heating. The contact part between the spinning wheel and the workpiece is a small curved surface, applying pressure to reduce the radial dimension. Under stress, material undergoes three-dimensional flow in axial, tangential, and radial (thickness) directions, eventually converting tangential flow to radial and axial flow as spinning continues. Macroscopically, the workpiece can be divided into undeformed zone 1, deformation zone 2, and outward extension deformation zone 3, as shown in Figure 3.
Within deformation zone 2, stress causes particles to flow. Particles near the inner surface A experience triaxial compressive stress, while those near the outer surface B undergo complex tensile and compressive stresses, resulting in radial and axial flow and plastic deformation.
Analyzing this deformation is complex. We conducted hot spinning experiments on seamless steel tubes with an outer diameter of 108mm, wall thickness of 4mm, and material of 20# steel to study the plastic deformation laws of diameter-reduction spinning. If the actual change in wall thickness at point A (B) is Δt, and the actual change in outer diameter is ΔD, their relative changes are Δt/t and ΔD/D, respectively. The relationship between wall thickness reduction and outer diameter reduction is shown in Figure 4.
This figure indicates that as the outer diameter decreases, wall thickness also reduces but by no more than 20%. During hot spinning, radial material flow occurs, but the reduction rate is controllable within a certain range.
We also studied the axial dimension changes in spun parts, finding that under certain conditions (outer diameter D and wall thickness t), the relationship between axial dimension increment ΔL and relative change in outer diameter ΔD/D is shown in Figure 5. This indicates material axial flow during hot spinning causes minor changes in axial dimensions.
Combining Figures 3 and 4, we conclude that for hot spinning of uniform steel tubes, when ΔD/D ≤ 0.2, the relative wall thickness change Δt/t is approximately 1/4 of the relative diameter reduction ΔD/D, and the relative axial length change ΔL/L is also about 1/4 of ΔD/D. Defining k1 ≈ k2 ≈ 1/4, hot spinning experiments show that diameter reduction per pass is limited by steel tube stability. Excessive reduction causes bulging, cracking, or wrinkling. The diameter reduction per pass should be based on the D/t ratio, with allowable reduction increasing as wall thickness increases. Generally, ΔD = 6-12mm, and for a blank outer diameter D0, after N spinning passes, the final neck diameter DN is calculated by a specific formula. The spinning frequency for rollers is 5-6 passes.
Changes in Metal Properties During Diameter-Reduction Spinning
During spinning, metal grains undergo sliding due to three-directional deformation forces, resulting in grain elongation and consistent fiber alignment with the deformation direction, maintaining metal fiber continuity. This increases the strength of the spun product, enhancing hardness, tensile strength, and yield limit. The metal microstructure after hot diameter-reduction spinning is shown in Figure 6.
Significant residual stress forms at bending and straight edge parts due to circumferential compressive strain, with influencing factors including wheel-blank friction, wall thickness, metal structure and properties, temperature changes, and process factors. Axial residual stress is generally greater than circumferential residual stress, indicating minimal circumferential deformation, with a residual stress distribution trend of external compression and internal tension.
Defect Analysis and Control in Diameter-Reduction Spinning

Spinning is a chipless forming process involving continuous local plastic deformation, with defect causes including wheel radius, feed rate, spinning passes, and trajectory, leading to surface wrinkling, local thinning, and cracking.
- Wrinkles from circumferential compressive stress: Thin walls experience circumferential bending under spinning force, with circumferential compressive stress due to diameter reduction. Reducing spinning ratio and wheel radius and increasing passes can minimize wrinkling.
- Radial cracks from alternating tensile and compressive stress: Rolling initial wrinkles causes bending stress, leading to radial cracks. Reducing tensile stress and optimizing spinning parameters can prevent this.
- Circumferential cracks from radial tensile stress: Axial feed force induces radial tensile stress, causing circumferential cracks, indicated by wall thinning. Avoiding excessive spinning passes, small wheel radius, and fast feed rates helps prevent cracking.
Conclusion
In diameter-reduction spinning of thin-walled tubes, radial and axial metal flow occurs under spinning force, with wall thinning approximately 1/4 of the relative diameter reduction ΔD/D. For rollers with 4mm wall thickness, thinning does not exceed 20%, meeting strength requirements. Proper spinning pass selection, wheel radius, and feed rate effectively control spinning defects.
Maximize Tooling and CNC Metal Spinning Capabilities.
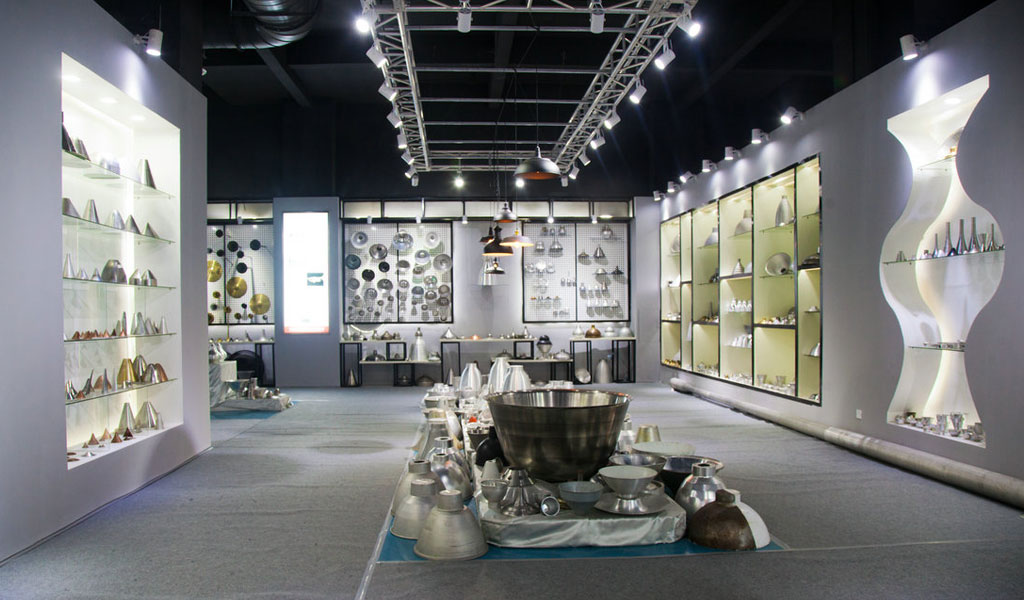
At BE-CU China Metal Spinning company, we make the most of our equipment while monitoring signs of excess wear and stress. In addition, we look into newer, modern equipment and invest in those that can support or increase our manufacturing capabilities. Our team is very mindful of our machines and tools, so we also routinely maintain them to ensure they don’t negatively impact your part’s quality and productivity.
Talk to us today about making a rapid prototype with our CNC metal spinning service. Get a direct quote by chatting with us here or request a free project review.
BE-CU China CNC Metal Spinning service include : CNC Metal Spinning,Metal Spinning Die,Laser Cutting, Tank Heads Spinning,Metal Hemispheres Spinning,Metal Cones Spinning,Metal Dish-Shaped Spinning,Metal Trumpet Spinning,Metal Venturi Spinning,Aluminum Spinning Products,Stainless Steel Spinning Products,Copper Spinning Products,Brass Spinning Products,Steel Spinning Product,Metal Spinnin LED Reflector,Metal Spinning Pressure Vessel,