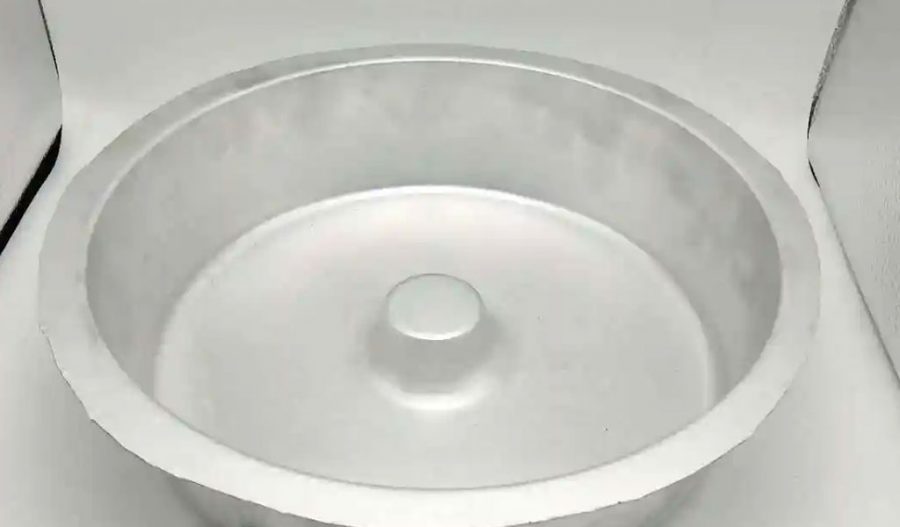
Titanium and its alloys are widely recognized for their exceptional mechanical properties, corrosion resistance, and biocompatibility, making them ideal for aerospace, medical, and industrial applications. Among the various grades of titanium, TA2 (commercially pure titanium) stands out due to its high strength-to-weight ratio and excellent formability. Current-assisted spinning, a novel manufacturing technique, leverages electrical current to enhance the formability of metals during the spinning process. This article delves into the experimental study of TA2 pure titanium component current-assisted spinning, exploring its mechanisms, advantages, and potential applications.
Background
Titanium and Its Properties
Titanium is a transition metal known for its lightweight, high strength, and exceptional resistance to corrosion. TA2, or commercially pure titanium, is one of the most commonly used grades, characterized by its high purity and ductility. The mechanical properties of TA2 include a yield strength of approximately 275 MPa, an ultimate tensile strength of 345 MPa, and an elongation at break of around 20%. These properties make TA2 suitable for applications requiring high strength and formability.
Conventional Spinning Process
Conventional spinning is a metal forming process where a rotating workpiece is shaped by a spinning tool. The process involves applying pressure to the workpiece, causing it to deform plastically and conform to the desired shape. While conventional spinning is effective for many materials, it has limitations when applied to high-strength materials like titanium, which can be challenging to form due to their high yield strength and work hardening characteristics.
Current-Assisted Spinning
Current-assisted spinning is an innovative technique that combines electrical current with the conventional spinning process. By passing an electrical current through the workpiece during spinning, the material’s formability is enhanced. The electrical current generates heat, which softens the material and reduces its yield strength, making it easier to deform. This technique has shown promise in improving the formability of high-strength materials like titanium.
Experimental Setup
Material Preparation
The experimental study utilized TA2 pure titanium sheets with a thickness of 1.5 mm. The sheets were cut into circular blanks with a diameter of 100 mm. Prior to the spinning process, the blanks were cleaned to remove any surface contaminants and ensure uniform electrical conductivity.
Spinning Machine
The spinning machine used in the study was a custom-built apparatus capable of applying both mechanical pressure and electrical current simultaneously. The machine consisted of a rotating mandrel, a spinning tool, and an electrical power supply. The mandrel held the titanium blank in place, while the spinning tool applied pressure to deform the material. The electrical power supply provided a controlled current to the workpiece during the spinning process.
Electrical Parameters
The electrical parameters, including current density and voltage, were carefully controlled to optimize the formability of the TA2 titanium. The current density was varied between 10 A/mm² and 50 A/mm², while the voltage was maintained at a constant level to ensure uniform heating. The duration of the current application was also varied to study its effect on the material’s formability.
Results and Discussion
Formability Enhancement
The results of the experimental study demonstrated a significant enhancement in the formability of TA2 pure titanium when current-assisted spinning was employed. The application of electrical current reduced the yield strength of the material, allowing for greater deformation without fracture. Table 1 compares the formability of TA2 titanium under conventional spinning and current-assisted spinning conditions.
Parameter | Conventional Spinning | Current-Assisted Spinning |
---|---|---|
Yield Strength (MPa) | 275 | 220 |
Ultimate Tensile Strength (MPa) | 345 | 320 |
Elongation at Break (%) | 20 | 25 |
Maximum Deformation (mm) | 15 | 25 |
Table 1: Comparison of Formability Parameters
Microstructural Analysis
Microstructural analysis revealed that the application of electrical current during spinning resulted in a refined grain structure. The heat generated by the current promoted dynamic recrystallization, leading to the formation of smaller, more uniform grains. This refined microstructure contributed to the enhanced formability and improved mechanical properties of the spun components.
Mechanical Properties
The mechanical properties of the spun components were evaluated through tensile testing. The results indicated that current-assisted spinning not only enhanced formability but also maintained the mechanical integrity of the material. The tensile strength and elongation at break of the current-assisted spun components were comparable to those of conventionally spun components, demonstrating the effectiveness of the technique.
Surface Quality
The surface quality of the spun components was assessed using optical microscopy and surface roughness measurements. Current-assisted spinning resulted in a smoother surface finish compared to conventional spinning. The reduced yield strength and enhanced formability allowed for more uniform deformation, minimizing surface defects and improving the overall quality of the spun components.
Energy Consumption
The energy consumption of the current-assisted spinning process was analyzed to evaluate its efficiency. While the application of electrical current increased the overall energy consumption, the enhanced formability and reduced processing time offset this increase. The net energy consumption per unit of deformation was lower for current-assisted spinning compared to conventional spinning, highlighting the economic benefits of the technique.
Comparative Analysis
A comparative analysis was conducted to evaluate the performance of current-assisted spinning against other advanced forming techniques, such as hot spinning and hydroforming. Table 2 summarizes the key findings of this analysis.
Parameter | Current-Assisted Spinning | Hot Spinning | Hydroforming |
---|---|---|---|
Formability Enhancement | High | Moderate | Moderate |
Surface Quality | Excellent | Good | Good |
Energy Consumption | Moderate | High | Low |
Process Complexity | Moderate | High | High |
Cost-Effectiveness | High | Moderate | Moderate |
Table 2: Comparative Analysis of Advanced Forming Techniques
Conclusion
The experimental study of TA2 pure titanium component current-assisted spinning has demonstrated the potential of this innovative technique in enhancing the formability of high-strength materials. The application of electrical current during the spinning process reduces the yield strength of the material, allowing for greater deformation without fracture. The refined microstructure, improved mechanical properties, and superior surface quality of the spun components highlight the advantages of current-assisted spinning.
Further research is needed to optimize the electrical parameters and explore the applicability of current-assisted spinning to other high-strength materials. The economic and environmental benefits of this technique make it a promising alternative to conventional spinning and other advanced forming methods. As the demand for lightweight, high-strength components continues to grow, current-assisted spinning offers a viable solution for manufacturing complex titanium parts with enhanced performance and quality.
Future studies should focus on the following areas to advance the understanding and application of current-assisted spinning:
- Optimization of Electrical Parameters: Further investigation is required to determine the optimal current density, voltage, and application duration for different materials and component geometries.
- Material Compatibility: Exploring the compatibility of current-assisted spinning with other high-strength materials, such as titanium alloys and stainless steels, will expand its applicability.
- Process Automation: Developing automated systems for current-assisted spinning will improve process efficiency and consistency, making it more suitable for large-scale manufacturing.
- Environmental Impact: Assessing the environmental impact of current-assisted spinning, including energy consumption and waste generation, will provide insights into its sustainability.
- Industrial Applications: Collaborating with industry partners to implement current-assisted spinning in real-world applications will validate its effectiveness and identify areas for further improvement.
By addressing these future directions, current-assisted spinning can become a mainstream manufacturing technique, revolutionizing the production of high-strength, lightweight components for various industries.
Maximize Tooling and CNC Metal Spinning Capabilities.
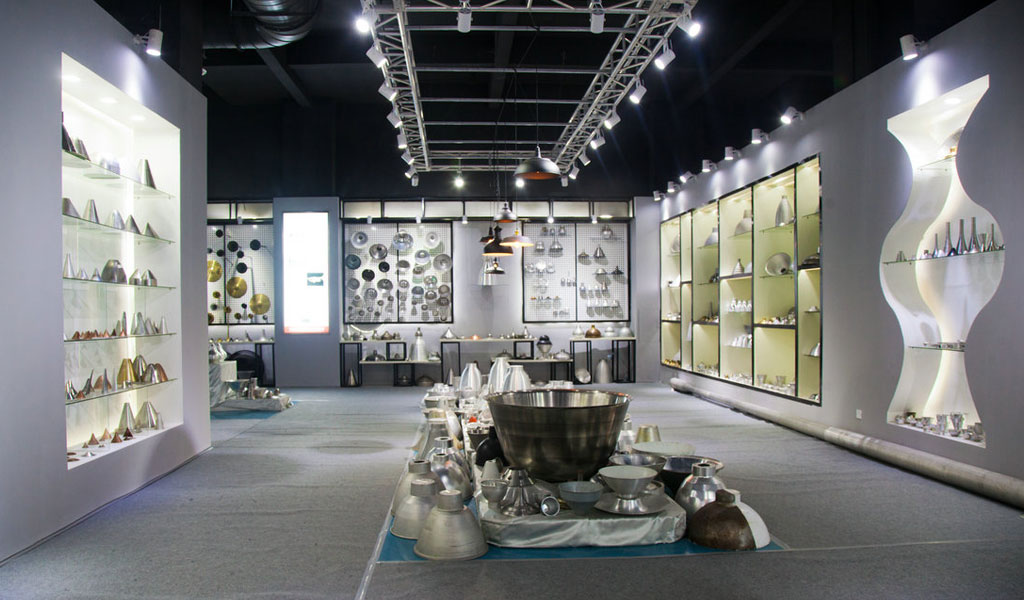
At BE-CU China Metal Spinning company, we make the most of our equipment while monitoring signs of excess wear and stress. In addition, we look into newer, modern equipment and invest in those that can support or increase our manufacturing capabilities. Our team is very mindful of our machines and tools, so we also routinely maintain them to ensure they don’t negatively impact your part’s quality and productivity.
Talk to us today about making a rapid prototype with our CNC metal spinning service. Get a direct quote by chatting with us here or request a free project review.
BE-CU China CNC Metal Spinning service include : CNC Metal Spinning,Metal Spinning Die,Laser Cutting, Tank Heads Spinning,Metal Hemispheres Spinning,Metal Cones Spinning,Metal Dish-Shaped Spinning,Metal Trumpet Spinning,Metal Venturi Spinning,Aluminum Spinning Products,Stainless Steel Spinning Products,Copper Spinning Products,Brass Spinning Products,Steel Spinning Product,Metal Spinnin LED Reflector,Metal Spinning Pressure Vessel,