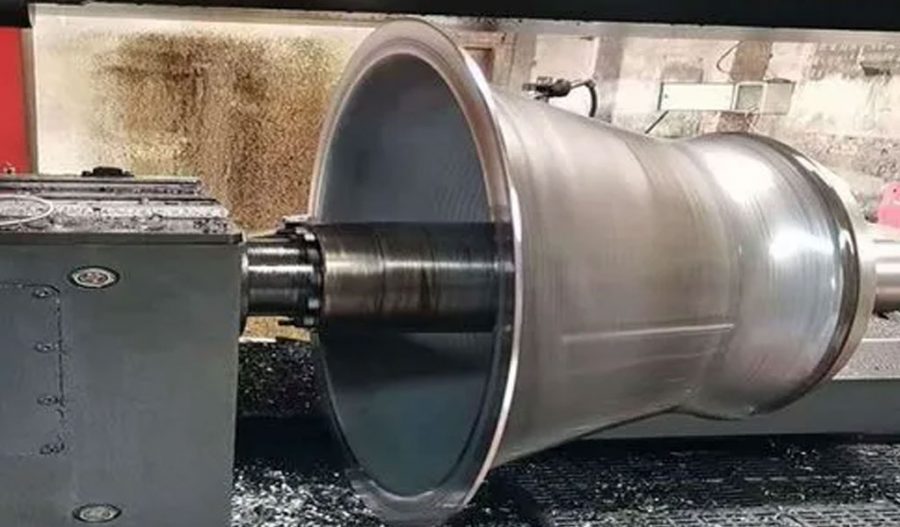
Metal spinning, a versatile manufacturing process, has found widespread applications across industries ranging from aerospace to household goods. One critical aspect influencing the performance and quality of metal spun parts is thickness tolerance. Understanding the nuances of thickness tolerances by application is paramount for achieving desired outcomes in terms of functionality, durability, and aesthetics.
In this comprehensive guide, we delve into the intricacies of metal spinning thickness tolerances across diverse applications. From automotive components to architectural elements, we examine how varying tolerances impact the performance and suitability of spun metal parts.
Automotive Industry
In the automotive industry, where precision and reliability are paramount, metal spinning plays a crucial role in the fabrication of components such as exhaust systems, wheel rims, and decorative trim. Tight thickness tolerances ensure optimal performance and structural integrity, particularly in high-stress areas like engine components and chassis parts.
When considering metal spinning thickness tolerances for automotive applications, factors such as material selection, design complexity, and functional requirements come into play. For instance, in exhaust system components, where temperature resistance and dimensional stability are critical, adherence to stringent thickness tolerances is imperative to prevent issues like warping and leakage.
Aerospace Sector
In aerospace applications, where safety and performance are non-negotiable, metal spinning contributes to the production of lightweight yet robust components such as fuel tanks, engine housings, and structural elements. The stringent regulatory standards governing the aerospace industry necessitate precise adherence to thickness tolerances to ensure compliance and reliability.
Given the extreme operating conditions and performance demands in aerospace applications, metal spinning thickness tolerances must be meticulously controlled to minimize material fatigue, enhance structural integrity, and meet strict weight requirements. Any deviation from specified tolerances could compromise the safety and performance of aerospace components, highlighting the criticality of precision in manufacturing processes.
Household Goods and Consumer Products
Metal spinning finds ubiquitous use in the manufacture of household goods and consumer products, ranging from kitchenware and lighting fixtures to decorative accents and furniture components. In these applications, thickness tolerances influence not only functional performance but also aesthetic appeal and product longevity.
For instance, in the production of stainless steel cookware, maintaining consistent thickness tolerances ensures even heat distribution, preventing hot spots and enhancing cooking performance. Similarly, in the fabrication of decorative lighting fixtures, precise control over thickness tolerances ensures uniformity in design and surface finish, contributing to the overall aesthetic appeal of the product.
Architectural Applications
In architectural design and construction, metal spinning offers limitless possibilities for creating custom-made components such as balustrades, handrails, and signage. Thickness tolerances play a crucial role in ensuring structural integrity, dimensional accuracy, and visual coherence in architectural elements.
Whether it’s crafting intricate patterns in ornamental metalwork or fabricating load-bearing structural components, controlling thickness tolerances is essential for achieving design intent, meeting building codes, and ensuring long-term durability. In architectural applications, where metal spun parts may be exposed to environmental elements and mechanical stresses, adherence to specified thickness tolerances is paramount to maintain performance and aesthetics over time.
Challenges and Solutions
Despite the advancements in manufacturing technologies and quality control measures, achieving precise thickness tolerances in metal spinning remains a complex endeavor. Variations in material properties, tooling wear, machine dynamics, and operator skill can all contribute to deviations from target thicknesses, posing challenges for manufacturers.
To address these challenges and enhance process reliability, manufacturers employ a combination of strategies, including advanced tooling design, real-time monitoring systems, automated control algorithms, and rigorous quality assurance protocols. By integrating these solutions into their manufacturing workflows, companies can minimize variability, improve consistency, and ensure compliance with specified thickness tolerances across diverse applications.
Conclusion
Metal spinning thickness tolerances play a pivotal role in determining the functionality, performance, and quality of spun metal parts across various applications. Whether it’s in the automotive, aerospace, household goods, or architectural sectors, precise control over thickness tolerances is essential for meeting functional requirements, regulatory standards, and aesthetic expectations.
As industries continue to push the boundaries of innovation and demand higher levels of performance and reliability, the importance of understanding and optimizing thickness tolerances in metal spinning will only grow. By leveraging advanced manufacturing technologies, process optimization techniques, and quality management systems, manufacturers can achieve tighter tolerances, enhance product quality, and unlock new possibilities in design and engineering.
Maximize Tooling and CNC Metal Spinning Capabilities.
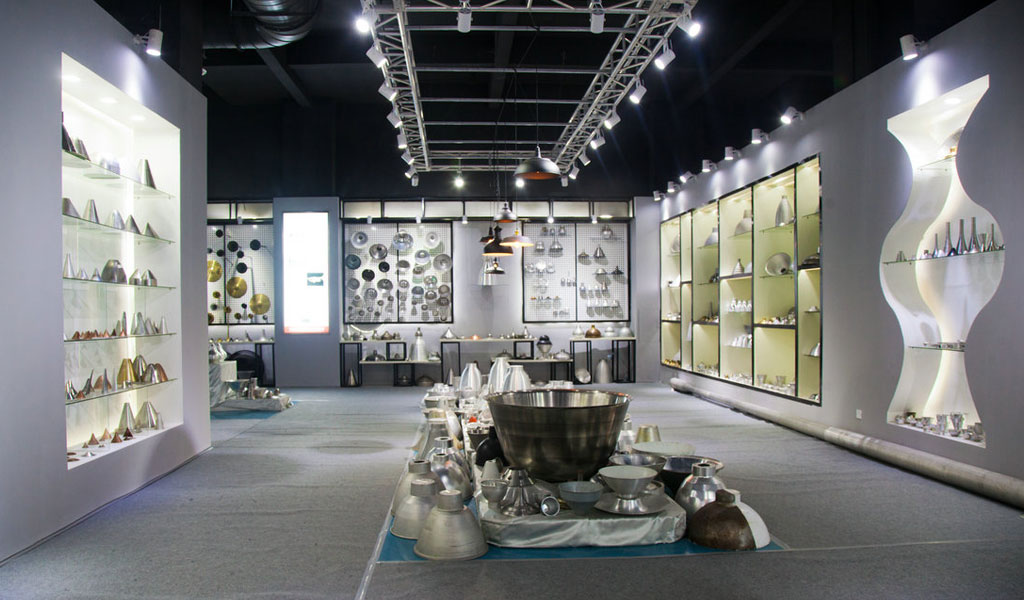
At BE-CU China Metal Spinning company, we make the most of our equipment while monitoring signs of excess wear and stress. In addition, we look into newer, modern equipment and invest in those that can support or increase our manufacturing capabilities. Our team is very mindful of our machines and tools, so we also routinely maintain them to ensure they don’t negatively impact your part’s quality and productivity.
Talk to us today about making a rapid prototype with our CNC metal spinning service. Get a direct quote by chatting with us here or request a free project review.
BE-CU China CNC Metal Spinning service include : CNC Metal Spinning,Metal Spinning Die,Laser Cutting, Tank Heads Spinning,Metal Hemispheres Spinning,Metal Cones Spinning,Metal Dish-Shaped Spinning,Metal Trumpet Spinning,Metal Venturi Spinning,Aluminum Spinning Products,Stainless Steel Spinning Products,Copper Spinning Products,Brass Spinning Products,Steel Spinning Product,Metal Spinnin LED Reflector,Metal Spinning Pressure Vessel,