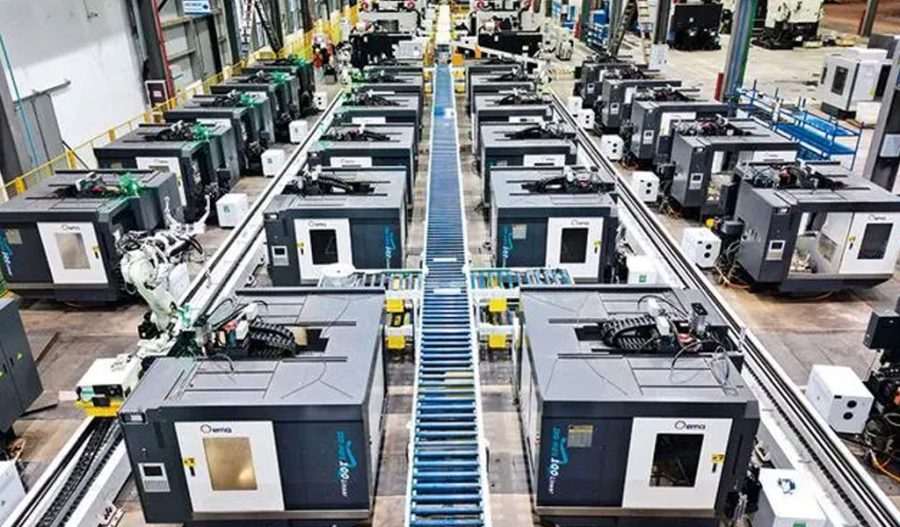
In July this year, the Lu Wei aluminum wheel hub production line, with a total investment of over 1 billion yuan, began trial operation in Fuzhou, Jiangxi. This is the first digital, continuous, and automated forging aluminum wheel hub production line in China and abroad, marking the industrialization stage of the Demma “Four-Dimensional Manufacturing” project, which has undergone 8 years of research and development.
“Four-Dimensional Manufacturing” is an advanced method based on the traditional three-dimensional manufacturing, introducing new mechanical considerations through force counteraction and balance principles to form the “Four-Dimensional Manufacturing” working method. By innovating and transforming traditional equipment such as forging presses, “Four-Dimensional Manufacturing” effectively achieves energy saving, emission reduction, and green manufacturing.
For example, in the aluminum wheel hub production line, the series of equipment using “Four-Dimensional Manufacturing” technology features a symmetric integrated structure and modular production. Force and torque counteraction are nearly 100%, reducing amplitude by 75%, cutting energy consumption by 80%, increasing rigidity by 4 times, improving precision by four geometric levels, and enhancing production efficiency by 10 times. Overall performance, energy savings, and environmental benefits are improved by 10 times.
The wheel hub is a crucial automotive component connecting the wheel rim through pillars, playing roles in bearing, steering, driving, and braking.
In July this year, the Lu Wei aluminum wheel hub production line, with a total investment of over 1 billion yuan, began trial operation in Fuzhou, Jiangxi. This digital, continuous, and automated forging aluminum wheel hub production line, as a demonstration project of the “Four-Dimensional Manufacturing” project, signifies the transition of Demma’s “Four-Dimensional Manufacturing” project results into the industrialization phase.
“Four-Dimensional Manufacturing” builds upon traditional three-dimensional manufacturing, applying principles of force counteraction and balance to introduce a new dimension of mechanical consideration. According to Li Wenlong, the Chief Engineer and Project Chief Scientist of Demma, the “Four-Dimensional Manufacturing” technology focuses on the transformation and iteration of high-end equipment and industrial mother machines, targeting energy saving, emission reduction, and lightweight in the automotive industry. This approach breaks away from traditional thinking and path dependence, achieving breakthroughs in fundamental theories and technical methods.
Currently, the “Four-Dimensional Manufacturing” R&D team has completed basic theoretical verification, topological data assessment, production of the first set of equipment, and scenario-based simulation assembly lines. They have obtained 125 patents in 15 countries and regions, including China, the US, Japan, and the EU, with 58 invention patents. The development of four-station spinning machines using “Four-Dimensional Manufacturing” technology has resulted in a 75% reduction in material use, 25% of the weight and cost of traditional equipment, and a 4-fold increase in work efficiency.
Innovative “Four-Dimensional Manufacturing” Working Method
The investor of the “Four-Dimensional Manufacturing” project is Ningbo Jingyi Micro Shaft Co., Ltd. (hereinafter referred to as “Jingyi”). This company, known for producing and exporting micro shafts, has accumulated production of over 10 billion micro shafts over decades and exports to more than 30 countries and regions including the US, Europe, and Japan. Its investment in R&D has led to the development of Blu-ray intelligent energy-saving windows, filling several domestic and international gaps with advanced concepts.
To adapt to the trend of automotive lightweight development, in 2010, Jingyi’s Chairman Dong Xiangyi discovered during a visit to the US that developed countries and regions like Europe, America, and Japan were promoting automotive lightweight trends, including the substitution of forged aluminum wheel hubs for steel and cast aluminum hubs. Meanwhile, China was just beginning. Upon returning to China, Dong Xiangyi, along with the company’s management and technical team, researched and verified the concept and established Ningbo Demma Intelligent Machinery Co., Ltd. in early 2015, focusing on research and development of the project and equipment.
After investigating domestic wheel hub manufacturers, the Demma team found that their equipment technology and manufacturing processes were relatively traditional, with high energy consumption, fragmented production processes, and significant cost risks, making them unsuitable for future large-scale industrial applications. Consequently, Demma proposed leveraging Jingyi’s experience in micro shafts and energy-saving windows to develop high-end specialized equipment as a breakthrough and pave a unique path for smart manufacturing transformation and upgrading.
Innovation in “Four-Dimensional Manufacturing” Working Method
Demma’s Vice General Manager Huang Jìn stated that forging alloy aluminum wheel hubs requires high-efficiency, high-power specialized forging presses. During the disassembly of existing equipment components, it was discovered that the true stress points of a 10,000-ton forging press are the four screws and eight nuts within the columns, relying on the tightening force of these components to withstand processing pressure and also endure the rebound force from forging impacts.
In improving the equipment structure, Dong Xiangyi proposed eliminating the four columns and using force counteraction and balance theory to design the forging press with 2 or 4 stations. The team initially struggled with whether this concept could stand up to theoretical scrutiny.
Experts and senior engineers validated that introducing Newtonian mechanics principles into machine tool equipment and industrial mother machine research is scientifically based. The existing equipment technology conditions and digital manufacturing capabilities in China can support this. After extensive discussions, the idea was named the “Four-Dimensional Manufacturing” working method, focusing on high-end specialized equipment and aluminum wheel hub production lines.
The “Four-Dimensional Manufacturing” method innovatively transforms traditional equipment, achieving energy saving, emission reduction, and green manufacturing. For example, the high-efficiency, high-power forging press used in forging aluminum wheel hubs was redesigned from a 16-meter-tall, 1,000-ton vertical press to a 2-meter-high, horizontal press, improving load balance and stability.
Additionally, the press’s shape was redesigned to an elegant, streamlined oval form, with two symmetric stations, significantly improving operational efficiency. Traditional equipment was rectangular or square, with many weak stress points and cumbersome designs. The new elliptical or oval shape allows for uniform stress distribution, reducing material and energy consumption.
The dual-station horizontal press’s workload is equivalent to that of two traditional presses. The new press, using “Four-Dimensional Manufacturing” technology, weighs 120 tons including reinforced steel rings, just 6% of the original press’s weight, with a 5-fold increase in compressive strength. The number of components in the equipment assembly has been reduced from over 200 to less than 30, simplifying manufacturing and assembly.
The Demma team invited professionals to evaluate the comprehensive functionality and efficiency of the “Four-Dimensional Manufacturing” technology. For example, in the aluminum wheel hub production line, the “Four-Dimensional Manufacturing” technology’s equipment features a symmetric integrated structure and modular production. Force and torque counteraction are nearly 100%, reducing amplitude by 75%, cutting energy consumption by 80%, increasing rigidity by 4 times, improving precision by four geometric levels, and enhancing production efficiency by 10 times. Overall performance, energy savings, and environmental benefits are improved by 10 times.
Refining and Detailing Machine Tools
According to traditional technology and process, to match the processing capability of the production line forging presses, four single-station spinning machines are required, which are costly and inefficient. “We used ‘Four-Dimensional Manufacturing’ technology to successfully develop a balanced and symmetrical four-station spinning machine, which can reduce material use by 75%, with a cost equivalent to 25% of the original equipment, and work efficiency increased by 4 times,” said Huang Jin.
However, the new equipment initially did not meet the target performance. Researchers invited Wang Jun, a senior technician from China Baowu, along with several experts, to evaluate the issue. It was found that while the equipment’s structural design was sound, there were flaws in the process guidance and insufficient motor torque. Several experts replaced the ordinary motors with high-power ones and installed servo motor drives at each station, effectively solving the efficiency issues of the spinning machine.
Technical development relies heavily on extensive collaboration between industry, academia, and research. In recent years, Demma has integrated various resources to build an industry-academia-research community that includes Zhejiang University, Fudan University, Shanghai Jiao Tong University, Xi’an Jiaotong University, Beijing University of Science and Technology, and Tianjin University, as well as leading manufacturing enterprises like China FAW, China First Heavy Industries, Ansteel, Baowu Steel, Jingda Equipment, the Chinese Mechanical Engineering Society, the China Mechanical Intelligent Equipment Association, and the China Smart Industry Research Institute, along with engineering and technical personnel from authoritative industry institutions.
The final shaping of the automotive wheel hub is completed during the milling process. Traditional milling machines are mostly single-arm cantilever structures with arm lengths of 50 to 100 centimeters. The larger the wheel hub, the longer the cantilever arm and the more prone it is to tilt, requiring the equipment’s own weight to reach one or two tons for stability. Chen Zhen, Demma’s Technical Director, stated that the single-arm cantilever design causes fundamental structural instability, resulting in poor machining stability and limited spindle speed. Additionally, the depth of milling was restricted, leading to surface precision only reaching grade 7, equivalent to semi-finished products that required further polishing.
Based on “Four-Dimensional Manufacturing” technology, the Demma team redesigned the milling machine from a single-arm cantilever structure to a double-arm overcross design, extending the processing arms to both ends. Chen Zhen explained that with this design, both milling cutters rotate simultaneously, centering the spindle at the midpoint, which counteracts and offsets the vibration stress, effectively ensuring equipment stability while significantly reducing its weight.
The application of new technology has achieved remarkable results. The spindle box of the milling machine, originally weighing 1 ton, is now reduced to 200 kilograms, with a material saving rate of 80%. The spindle speed, previously up to 7,000 revolutions per minute, has increased to 17,000 RPM. Milling depth has increased from 2 millimeters to 8 millimeters, and surface precision surpasses that of grinding machines, achieving grade 11.
Now, the forged aluminum automotive wheel hubs do not require polishing and can be directly sprayed to become finished products. According to authoritative calculations, the multi-head milling composite processing center using “Four-Dimensional Manufacturing” technology has more than a tenfold increase in efficiency compared to traditional equipment, with superior product quality and performance.
While optimizing the equipment system and simulation production lines, the Demma team has also focused on each process and tooling in the production flow to enhance technical content and added value. During a technical analysis meeting, it was pointed out that the wheel hub blanks weigh 25 to 30 kilograms, but the milling fixture weighs 200 kilograms, requiring two robot flips and reducing operational efficiency. Dong Xiangyi suggested using the existing holes in the wheel hub as a fixture support, providing a new idea for improving tooling.
A small fixture modification not only improved work efficiency but also reduced costs. Researchers used an internal support fixture to hold the wheel hub, reducing the weight of the fixture to only 20 kilograms, a 90% reduction. The new fixture can process four wheel hubs in one go, taking only one minute, with an average processing time of 15 seconds per hub, compared to 4 minutes for one hub previously. The new solution increased the efficiency of wheel hub milling by 32 times, saving 3 million yuan in annual electricity costs per machine.
Zhu Lifu, Director of the Enterprise Cultivation and Cooperation Department of the Ningbo Economic and Information Technology Bureau, stated that the bureau actively supports and assists companies in technological upgrades. Last year, they helped the “Four-Dimensional Manufacturing” project apply for provincial-level advanced equipment first-set preferential policies and are now assisting Demma’s technical team in applying for national or international advanced equipment first-set policies.
“Force balance and multi-station flexible milling processes offer high efficiency, precision, and low cost, aligning with the low-carbon economy, green manufacturing, and sustainable development industrial orientation, and are highly praised by users,” said Chen Bingrong, Chairman of the Ningbo Intelligent Manufacturing Expert Committee. “Advanced manufacturing must prioritize fundamental research on various high-end equipment and industrial mother machines, refining and perfecting the design, manufacturing, and technological processes of machine tools to build a solid foundation for the manufacturing industry.”
Promoting Innovation and Iteration of “National Heavy Equipment”
High-end machine tools, which advanced manufacturing relies on, are known as the “national heavy equipment” of industrial mother machines. China is the world’s largest producer, importer, and consumer of industrial mother machines, but it has long relied on imports for high-end CNC machine tools and key components.
Professor Cang Daqiang from the School of Metallurgy and Ecology at Beijing University of Science and Technology believes that aerospace, ocean shipping, nuclear industry, automotive, high-speed rail, military industry, mining, and tunnel boring machines all require large or super-large high-precision intelligent machinery. Many still rely on imported equipment and technology, urgently needing innovative theories and new equipment technologies.
Several industry experts believe that Demma’s “Four-Dimensional Manufacturing” technology’s fundamental theories and core technologies can be widely applied in high-end equipment “industrial mother machines” and advanced manufacturing fields, especially in leading high-precision specialized equipment and high-end machine tool industries.
On the one hand, innovation breakthroughs in fundamental theories inject “new vitality” into the design and manufacturing of mechanical equipment. Cang Daqiang believes that the fundamental theoretical innovation of Demma’s “Four-Dimensional Manufacturing” lies in its application of action and reaction forces and even multiplication principles, breaking traditional mechanical equipment design and manufacturing concepts, providing new ideas and approaches for the upgrade and green transformation of high-end equipment and industrial mother machines.
Data shows that Demma’s horizontal forging press reduces material use by 94%, with a 5-fold increase in work efficiency; the integrated milling machine reduces material use by 80%, with 4 times increased rigidity, 4 times improved milling precision, and a 50% reduction in overall energy consumption, with some equipment even down by 80%. Third-party evaluations show that the material and energy savings, environmental friendliness, and performance quality of Demma’s forged aluminum wheel hub demonstration production line are improved by 10 times compared to traditional technology equipment.
On the other hand, advancing technological innovation applications provides important technical support for the development and manufacturing of advanced equipment. Yan Shanwu, an expert from the China Forging Association, said that Demma’s “Four-Dimensional Manufacturing” technology can be applied to various high-end CNC machine tools, including turning, milling, and grinding machines, as well as special processing machines and specialized processing centers. It innovatively applies technology to high-end product production fields and sets a practical example, both developing advanced equipment and producing high-quality products.
Currently, intelligent, precise, and lightweight manufacturing has become a major trend in the CNC machine tool industry.
At Demma’s Lu Wei production line, the multi-axis, multi-station CNC machine tool is equipped with 4 stations, 8 tool turrets, and 4 spindles with 16 auxiliary spindles. The machine runs smoothly with seamless connections. Surface processing precision exceeds that of grinding processes, with errors as low as 0.2 microns, only 2% of a human hair’s thickness.
Professor Lü Zhengyu from the School of Electrical Engineering at Zhejiang University said that the Demma team has introduced topology, established data simulation models, and used digital calculations for pre-control, integrating robots into the entire production scenario. This enables real-time tracking and switching of each process and technical link on the production line, demonstrating a significant breakthrough in smart manufacturing transformation.
At Fuzhou Lu Wei Wheel Hub Manufacturing Co., Ltd., the Demma Lu Wei wheel hub production line has begun trial operation. This is the first fully independently owned intellectual property production line, achieving original blank cutting, low-temperature forging, spinning molding, and turning milling in one go, with digital automation for forged aluminum wheel hubs. The production time per unit is 15 seconds, with an annual output of 1.5 million wheel hubs.
“Compared with enterprises of the same investment scale, Lu Wei has significant advantages in site area and labor costs,” said Sang Jianguo, General Manager of Fuzhou Lu Wei Wheel Hub Manufacturing Co., Ltd. This production line covers 20 acres, with a factory area of 10,000 square meters, only one-tenth of the area of similar enterprises, and an annual per-acre tax revenue of up to 10 million yuan. In terms of labor costs, traditional equipment requires 800 to 1,000 operators, while Lu Wei only needs 40 to 50 managers.
In the future, the Demma team will use new technologies and equipment to assist the upgrading and transformation of industrial parks and clusters. Huang Jin said that they will build a “Four-Dimensional Manufacturing” technology town through technological cooperation, investment construction, and equipment leasing, providing efficient and cost-effective one-stop technical services for small and micro enterprises in mold design, product development, and finished product delivery.
Maximize Tooling and CNC Metal Spinning Capabilities.
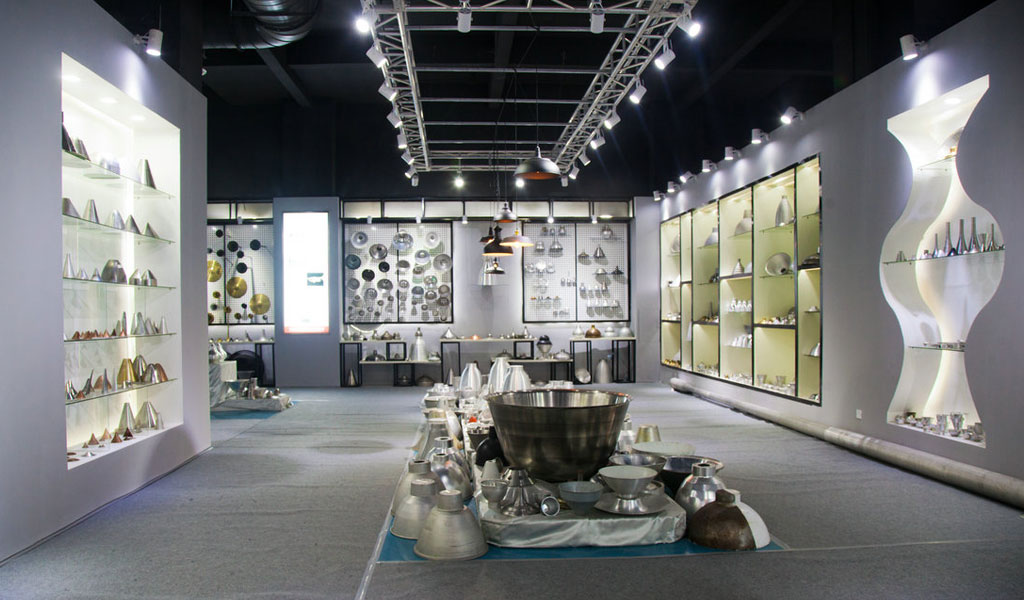
At BE-CU China Metal Spinning company, we make the most of our equipment while monitoring signs of excess wear and stress. In addition, we look into newer, modern equipment and invest in those that can support or increase our manufacturing capabilities. Our team is very mindful of our machines and tools, so we also routinely maintain them to ensure they don’t negatively impact your part’s quality and productivity.
Talk to us today about making a rapid prototype with our CNC metal spinning service. Get a direct quote by chatting with us here or request a free project review.
BE-CU China CNC Metal Spinning service include : CNC Metal Spinning,Metal Spinning Die,Laser Cutting, Tank Heads Spinning,Metal Hemispheres Spinning,Metal Cones Spinning,Metal Dish-Shaped Spinning,Metal Trumpet Spinning,Metal Venturi Spinning,Aluminum Spinning Products,Stainless Steel Spinning Products,Copper Spinning Products,Brass Spinning Products,Steel Spinning Product,Metal Spinnin LED Reflector,Metal Spinning Pressure Vessel,