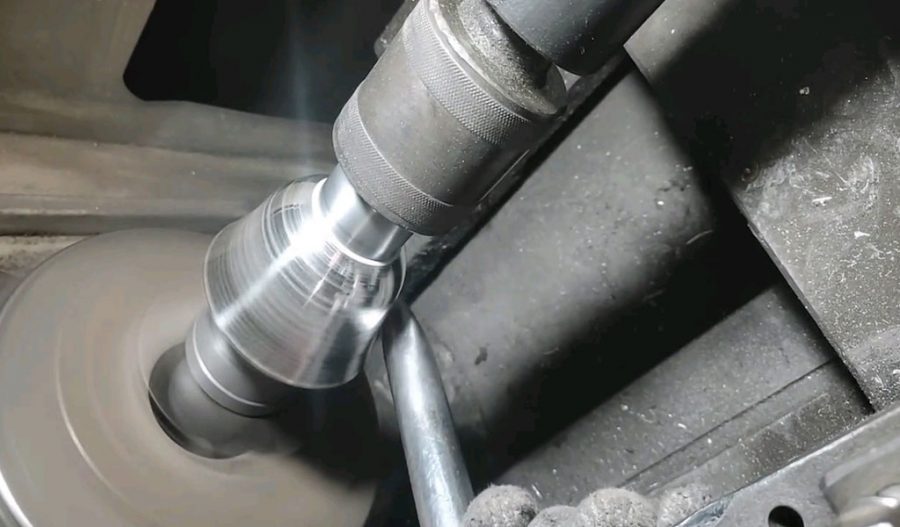
Metal spinning, also known as spin forming or metal cnc turning, is a metalworking process by which a flat metal disc, known as a blank, is formed into a rotational symmetrical object. This process is widely used in industries such as aerospace, automotive, and household goods manufacturing. Understanding the cost and time involved in metal spinning is crucial for both manufacturers and customers. In this article, we will delve into the factors that influence the cost and time of metal cnc spinning and provide a comprehensive guide on how to calculate them.
Factors Affecting Metal CNC Spinning Cost
Material Cost
The choice of material significantly impacts the overall cost of metal spinning. Different metals have varying costs per pound, with materials like aluminum being less expensive than titanium or stainless steel. Additionally, specialized alloys or high-grade metals can drive up the material cost.
To calculate the material cost:
Material Cost=Weight of Blank (lbs)×Cost per Pound of Material
Labor Cost
Labor cost is another significant component of metal spinning. Skilled labor is required to operate the spinning machine, monitor the process, and perform finishing tasks. Labor costs can vary depending on the region, skill level, and labor rates of the company.
To calculate labor cost:
Labor Cost=Number of Hours Spent×Hourly Labor Rate
Machine and Tooling Cost
Metal spinning machines and tooling are expensive investments. The cost of the machine and tooling amortized over its lifespan adds to the cost per part. Additionally, specialized tooling may be required for complex shapes or tight tolerances.
To calculate machine and tooling cost:
Machine and Tooling Cost per Part=Expected Number of Parts Produced/Total Machine and Tooling Cost
Overhead and Miscellaneous Costs
Overhead costs such as rent, utilities, and administrative expenses also contribute to the overall cost. These costs are often allocated based on the percentage of direct labor or machine hours.
To calculate overhead cost:
Overhead Cost per Part= Total Number of Parts Produced/Total Overhead Costs
Profit Margin
Finally, a profit margin is added to ensure the business remains profitable. Profit margins can vary depending on the industry, market conditions, and company policies.
To calculate profit margin:
Profit Margin=(Total Cost−Material Cost−Labor Cost−Machine and Tooling Cost−Overhead Cost)×Profit Percentage
Factors Affecting Metal Spinning Time
Complexity of the Part
The complexity of the part being spun is a major factor affecting the spinning time. Simple shapes with fewer contours require less time compared to complex shapes with intricate details.
Material Thickness
Thicker materials require more force and time to be spun into shape compared to thinner materials.
Machine Speed
The speed at which the spinning machine operates also affects the spinning time. Higher machine speeds can reduce the spinning time, but it may compromise the quality of the finished part.
Operator Skill Level
Skilled operators can optimize the spinning process, reducing errors and improving efficiency, thereby reducing the spinning time.
Calculating Metal Spinning Cost
To calculate the total cost of metal spinning, you can use the following formula:
Total Cost per Part=Material Cost+Labor Cost+Machine and Tooling Cost per Part+Overhead Cost per Part+Profit Margin
Calculating Metal Spinning Time
To calculate the spinning time, you can use the following formula:
Spinning Time per Part=Base Spinning Time×( Standard Material Thickness Material Thickness)×( Standard Complexity Factor Complexity Factor)
Example Calculation
Let’s consider an example to illustrate the calculation of metal spinning cost and time.
Material: Aluminum
Weight of Blank: 5 lbs
Cost per Pound of Aluminum: $2
Number of Hours Spent: 2 hours
Hourly Labor Rate: $20
Total Machine and Tooling Cost: $10,000
Expected Number of Parts Produced: 100
Total Overhead Costs: $5,000
Profit Percentage: 20%
Base Spinning Time: 1 hour
Material Thickness: 0.125 inches
Standard Material Thickness: 0.1 inches
Complexity Factor: 1.2
Standard Complexity Factor: 1.0
Material Cost: \text{Material Cost} = 5 \text{ lbs} \times $2/\text{lb} = $10
Labor Cost: \text{Labor Cost} = 2 \text{ hours} \times $20/\text{hour} = $40
Machine and Tooling Cost per Part: \text{Machine and Tooling Cost per Part} = $10,000/100 = $100
Overhead Cost per Part: \text{Overhead Cost per Part} = $5,000/100 = $50
Profit Margin: \text{Profit Margin} = ($10 + $40 + $100 + $50) \times 0.20 = $40
Total Cost per Part: \text{Total Cost per Part} = $10 + $40 + $100 + $50 + $40 = $240
Spinning Time per Part: Spinning Time per Part=1 hour×(0.1250.1)×1.2=1.5 hoursSpinning Time per Part=1 hour×(0.10.125)×1.2=1.5 hours
Conclusion
Understanding how to calculate the cost and time of metal spinning is essential for budgeting, pricing, and production planning. By considering factors such as material cost, labor cost, machine and tooling cost, overhead costs, complexity of the part, material thickness, machine speed, and operator skill level, you can accurately estimate the cost and time involved in metal spinning.
By using the formulas and example calculations provided in this article, manufacturers and customers can make informed decisions, optimize their processes, and achieve cost-effective and timely production of spun metal parts. Whether you are a manufacturer looking to price your services competitively or a customer looking to understand the cost structure, this guide serves as a comprehensive resource for calculating metal spinning cost and time.
Maximize Tooling and CNC Metal Spinning Capabilities.
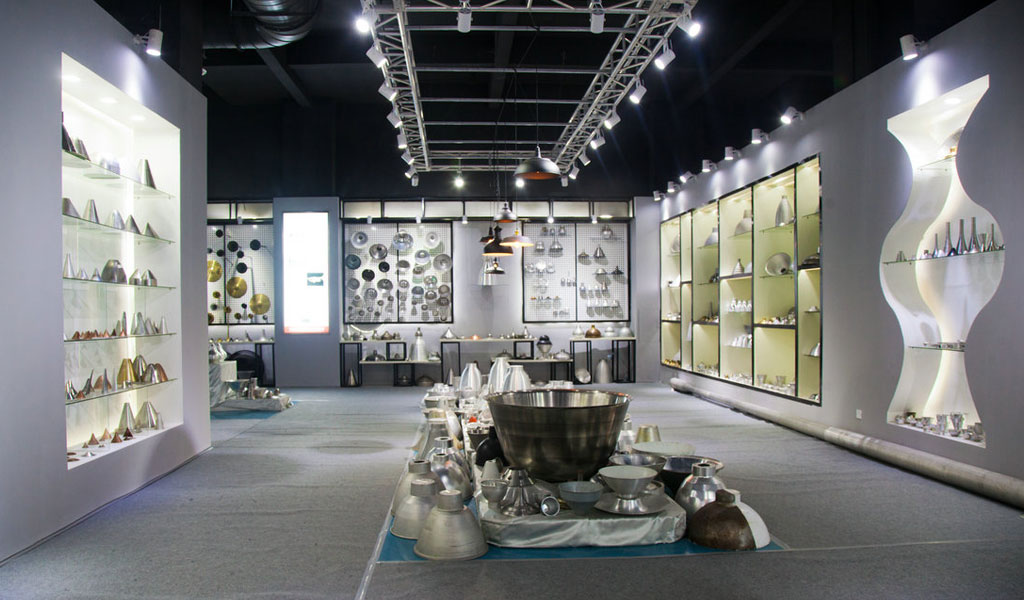
At BE-CU China Metal Spinning company, we make the most of our equipment while monitoring signs of excess wear and stress. In addition, we look into newer, modern equipment and invest in those that can support or increase our manufacturing capabilities. Our team is very mindful of our machines and tools, so we also routinely maintain them to ensure they don’t negatively impact your part’s quality and productivity.
Talk to us today about making a rapid prototype with our CNC metal spinning service. Get a direct quote by chatting with us here or request a free project review.
BE-CU China CNC Metal Spinning service include : CNC Metal Spinning,Metal Spinning Die,Laser Cutting, Tank Heads Spinning,Metal Hemispheres Spinning,Metal Cones Spinning,Metal Dish-Shaped Spinning,Metal Trumpet Spinning,Metal Venturi Spinning,Aluminum Spinning Products,Stainless Steel Spinning Products,Copper Spinning Products,Brass Spinning Products,Steel Spinning Product,Metal Spinnin LED Reflector,Metal Spinning Pressure Vessel,