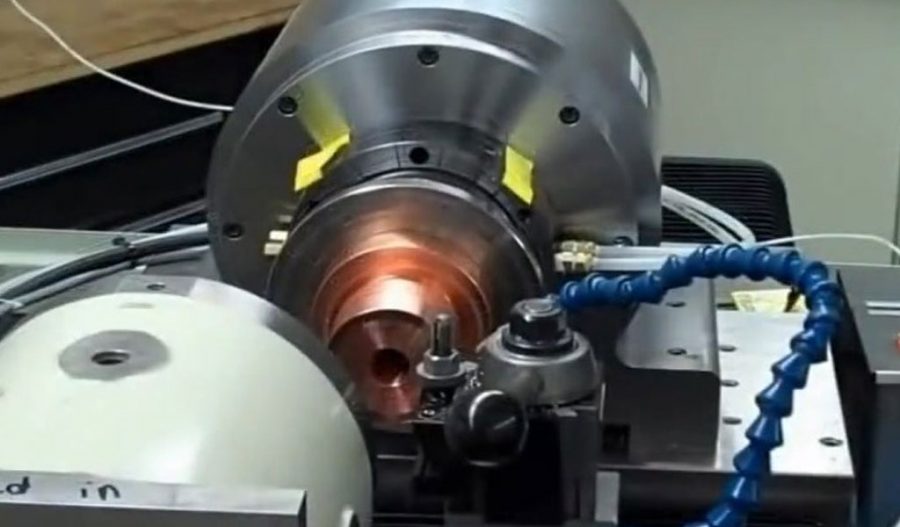
Metalworking is a broad field encompassing various techniques used to shape and form metal into desired forms. Among the most commonly used methods are metal spinning and sheet metal fabrication. Both processes are essential in manufacturing, offering unique advantages and applications. This article delves into the differences, advantages, disadvantages, and applications of metal spinning and sheet metal fabrication.
Metal Spinning
Metal spinning, also known as spin forming or spinning, is a metalworking process by which a disc or tube of metal is rotated at high speed and formed into an axially symmetric part. This is achieved by applying localized pressure with a blunt tool, either manually or with a CNC lathe, to gradually shape the metal around a pre-formed mandrel.
Materials:
Common materials used in metal spinning include aluminum, copper, stainless steel, and brass. The process can be applied to both ferrous and non-ferrous metals, making it versatile across various industries.
Advantages:
- Cost-Effective for Small Batches: Metal spinning is economical for producing small quantities of parts, as it requires minimal tooling.
- High Precision: The process allows for precise control over the thickness and dimensions of the final product.
- Flexibility: Metal spinning can produce complex shapes that would be challenging to achieve with other methods.
- Strength: The process can enhance the strength and rigidity of the metal through work hardening.
Disadvantages:
- Labor-Intensive: Traditional metal spinning is labor-intensive and requires skilled operators.
- Limited to Symmetric Parts: The process is limited to producing parts with axial symmetry.
- Surface Finish: Achieving a high-quality surface finish can be challenging and may require additional processing.
Applications:
Metal spinning is commonly used in industries such as aerospace, automotive, and cookware manufacturing. Typical products include cones, hemispheres, domes, and cylindrical parts.
Sheet Metal Fabrication
Sheet metal fabrication encompasses a wide range of processes used to manipulate flat sheets of metal into various shapes and structures. These processes include cutting, bending, punching, and assembling. Sheet metal fabrication can be performed using manual tools or advanced machinery such as CNC machines, laser cutters, and press brakes.
Materials:
The materials used in sheet metal fabrication are diverse, including aluminum, steel, stainless steel, copper, and brass. The choice of material depends on the desired properties and application of the final product.
Advantages:
- Versatility: Sheet metal fabrication can produce a wide array of shapes and structures, from simple brackets to complex enclosures.
- Scalability: The process is well-suited for both prototyping and large-scale production.
- Precision and Repeatability: Advanced machinery ensures high precision and consistency across multiple parts.
- Customization: The process allows for significant customization in terms of design and material selection.
Disadvantages:
- Tooling Costs: Initial setup and tooling costs can be high, particularly for custom or complex designs.
- Material Waste: Some sheet metal processes, such as punching and cutting, can generate significant material waste.
- Surface Finish: Like metal spinning, achieving a high-quality surface finish may require additional processing.
Applications:
Sheet metal fabrication is used in a wide range of industries, including construction, electronics, automotive, and HVAC. Common products include enclosures, brackets, frames, and ductwork.
Comparison
Process Complexity:
- Metal Spinning: Involves a relatively simple setup with a spinning lathe and mandrel but requires skilled operators for manual spinning.
- Sheet Metal Fabrication: Involves multiple processes and machinery, offering greater complexity and versatility in shapes and designs.
Production Volume:
- Metal Spinning: More cost-effective for small to medium production runs due to lower tooling costs.
- Sheet Metal Fabrication: Better suited for high-volume production, offering economies of scale despite higher initial tooling costs.
Shape and Design:
- Metal Spinning: Limited to axially symmetric shapes but allows for intricate designs within those constraints.
- Sheet Metal Fabrication: Capable of producing a vast array of shapes and designs, including asymmetrical and complex structures.
Material Utilization:
- Metal Spinning: Generally results in less material waste, as the metal is deformed rather than cut away.
- Sheet Metal Fabrication: Certain processes, such as punching and cutting, can result in higher material waste.
Conclusion
Both metal spinning and sheet metal fabrication are vital metalworking techniques with unique advantages and applications. Metal spinning is ideal for producing axially symmetric parts with high precision and strength, particularly in small to medium production runs. In contrast, sheet metal fabrication offers versatility and scalability, making it suitable for a wide range of shapes and high-volume production. The choice between these methods depends on the specific requirements of the project, including the desired shape, material, production volume, and cost considerations. Understanding the strengths and limitations of each process enables manufacturers to select the most appropriate technique for their needs.
Maximize Tooling and CNC Metal Spinning Capabilities.
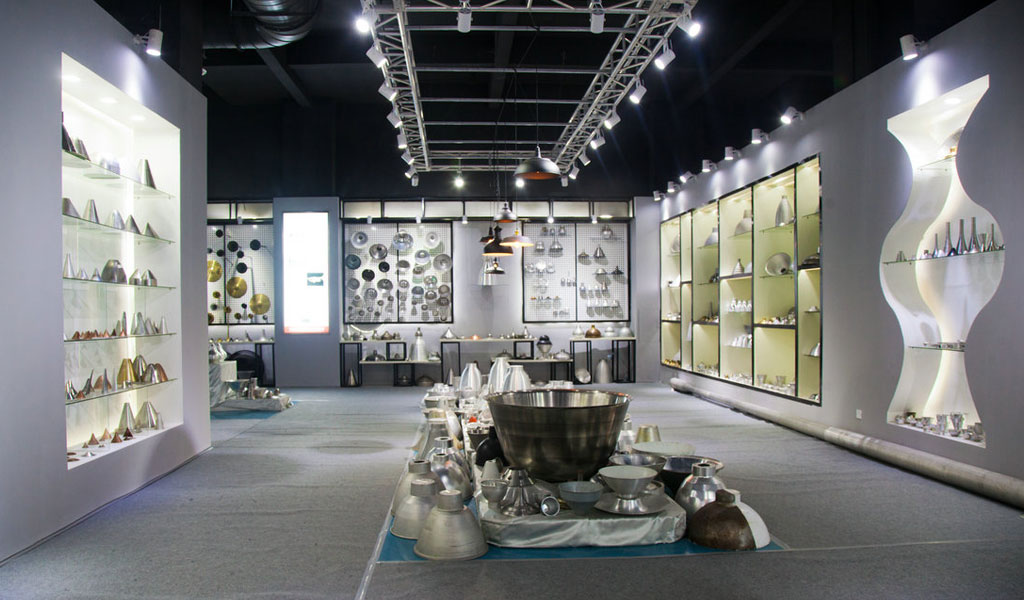
At BE-CU China Metal Spinning company, we make the most of our equipment while monitoring signs of excess wear and stress. In addition, we look into newer, modern equipment and invest in those that can support or increase our manufacturing capabilities. Our team is very mindful of our machines and tools, so we also routinely maintain them to ensure they don’t negatively impact your part’s quality and productivity.
Talk to us today about making a rapid prototype with our CNC metal spinning service. Get a direct quote by chatting with us here or request a free project review.
BE-CU China CNC Metal Spinning service include : CNC Metal Spinning,Metal Spinning Die,Laser Cutting, Tank Heads Spinning,Metal Hemispheres Spinning,Metal Cones Spinning,Metal Dish-Shaped Spinning,Metal Trumpet Spinning,Metal Venturi Spinning,Aluminum Spinning Products,Stainless Steel Spinning Products,Copper Spinning Products,Brass Spinning Products,Steel Spinning Product,Metal Spinnin LED Reflector,Metal Spinning Pressure Vessel,