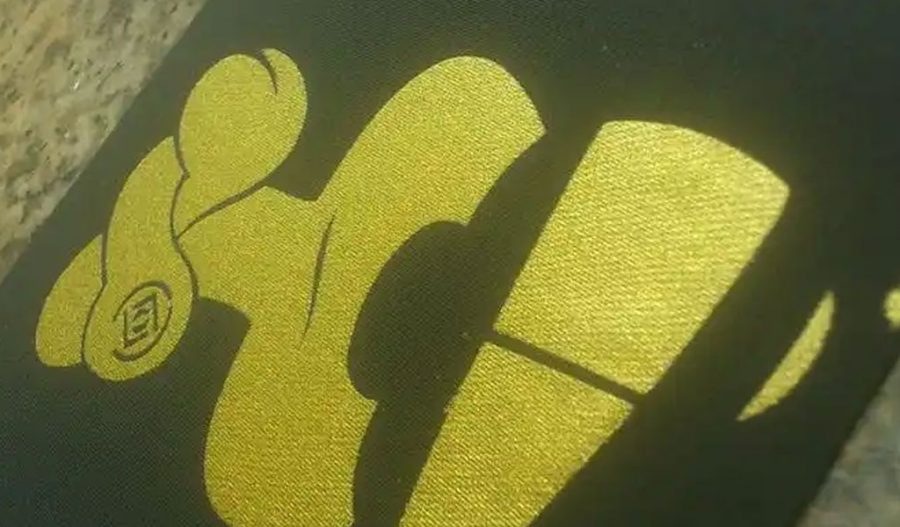
Pad printing and screen printing represent two distinct methodologies within the broader field of industrial and commercial printing technologies. Both techniques are widely utilized across various industries for applying ink to substrates, ranging from consumer goods to specialized technical components. Pad printing, also known as tampography, involves transferring a two-dimensional image from an etched plate onto a three-dimensional object using a silicone pad. Screen printing, conversely, employs a mesh screen through which ink is forced onto a flat or semi-flat surface, creating a design via a stencil-based process. These processes, while sharing the common goal of image transfer, diverge significantly in their mechanisms, applications, and technical attributes.
The origins of these printing methods reflect their evolution from traditional craftsmanship to modern industrial applications. Screen printing traces its roots to ancient China during the Song Dynasty (960–1279 CE), where it was initially used for textile decoration. Pad printing, a more recent innovation, emerged in the mid-20th century, with significant developments attributed to the Swiss engineer Wilfried Philipp in the 1960s, who refined the technique for precision printing on irregular surfaces. Today, both methods have been adapted to meet the demands of contemporary manufacturing, offering unique advantages and facing distinct limitations.
This article provides a comprehensive, scientific comparison of pad printing and screen printing, exploring their technical processes, material interactions, industrial applications, and economic considerations. By delving into the physics, chemistry, and engineering principles underlying each method, we aim to elucidate their respective strengths and weaknesses, supported by a detailed comparative table.
Technical Principles of Pad Printing
Pad printing operates on a principle of indirect gravure printing, wherein ink is transferred from a recessed image on a printing plate (cliché) to a substrate via an intermediary silicone pad. The process begins with the preparation of a cliché, typically made from steel or photopolymer, which is etched with the desired design using laser engraving or photochemical processes. The depth of the etch, often ranging from 20 to 30 micrometers, determines the volume of ink that can be held and subsequently transferred.
The ink, formulated to suit the substrate and desired durability, is applied to the cliché, filling the etched recesses. A doctor blade or ink cup then removes excess ink from the surface, leaving ink only within the etched design. The silicone pad, characterized by its elasticity and non-stick properties, is pressed onto the cliché, picking up the ink pattern. Due to the hydrophobic nature of silicone, the ink adheres temporarily to the pad without being absorbed. The pad is then pressed onto the substrate, transferring the ink and replicating the design with high fidelity.
The physics of this process hinges on surface tension and adhesion. The ink’s viscosity, typically between 500 and 10,000 centipoise (cP), must be carefully balanced to ensure it fills the cliché without excessive spreading, yet releases cleanly from the pad to the substrate. The pad’s Shore hardness, ranging from 2A to 40A, influences its ability to conform to irregular surfaces, making pad printing particularly suited for three-dimensional objects such as medical devices, automotive parts, and promotional items.
Technical Principles of Screen Printing
Screen printing, also referred to as serigraphy or silk screening, relies on a direct stencil-based approach. The process utilizes a mesh screen, traditionally made of silk but now commonly constructed from polyester or stainless steel, with thread counts ranging from 40 to 400 threads per inch. The screen is coated with a photosensitive emulsion, and the design is created by exposing the emulsion to ultraviolet (UV) light through a film positive, hardening the exposed areas while leaving the design areas unexposed and washable.
Once prepared, the screen is placed over the substrate, and ink is applied to the top surface. A squeegee, typically made of polyurethane with a hardness of 60–90 Shore A, is drawn across the screen, forcing ink through the open mesh areas onto the substrate below. The ink passes through the screen in a controlled manner, with the mesh’s porosity and the squeegee’s pressure dictating the thickness of the ink deposit, often ranging from 10 to 100 micrometers.
The mechanics of screen printing involve capillary action and shear stress. The ink, with a viscosity of 1,000 to 20,000 cP, must flow through the mesh without clogging, while maintaining sufficient cohesion to form a sharp image. The substrate’s surface energy, measured in dynes per centimeter, influences ink adhesion, requiring compatibility between the ink chemistry (e.g., solvent-based, UV-curable, or water-based) and the material being printed, such as textiles, glass, or metal.
Phase 1: Material Interactions in Pad Printing
The efficacy of pad printing is heavily influenced by the interaction between ink, pad, cliché, and substrate. The ink’s chemical composition is tailored to the substrate’s properties, such as its polarity and surface roughness. For instance, printing on polypropylene, a low-surface-energy plastic (approximately 30 dynes/cm), necessitates inks with adhesion promoters or pre-treatment via corona discharge or flame treatment to increase surface energy to 40–50 dynes/cm.
The silicone pad’s role is critical in this phase. Its elasticity, governed by Young’s modulus (typically 1–10 MPa), allows it to deform and conform to complex geometries, such as concave or convex surfaces. This adaptability stems from the polymer’s cross-linked molecular structure, which provides resilience while minimizing ink absorption. The pad’s surface energy, approximately 20–25 dynes/cm, ensures that ink transfers to the substrate rather than remaining on the pad, a phenomenon explained by the Young-Dupré equation:
Wa=γ(1+cosθ) W_a = \gamma (1 + \cos\theta) Wa=γ(1+cosθ)
where Wa W_a Wa is the work of adhesion, γ \gamma γ is the ink’s surface tension, and θ \theta θ is the contact angle between the ink and the pad or substrate.
Environmental factors, such as temperature and humidity, also affect ink drying rates and transfer efficiency. For solvent-based inks, evaporation rates increase with temperature, potentially reducing tackiness and complicating transfer, necessitating precise control within a range of 20–25°C and 40–60% relative humidity.
Phase 1: Material Interactions in Screen Printing
In screen printing, material interactions occur primarily between the ink, screen, and substrate. The mesh screen’s thread diameter and open area percentage (typically 30–60%) determine ink flow and deposit thickness. Finer meshes (e.g., 300 threads/inch) produce sharper images but limit ink volume, while coarser meshes (e.g., 100 threads/inch) allow thicker deposits suited for textiles or ceramics.
Ink formulation is equally critical. UV-curable inks, polymerizing under 200–400 nm wavelengths, offer rapid drying and durability but require substrates resistant to UV exposure. Solvent-based inks, reliant on volatile organic compounds (VOCs), penetrate porous substrates like paper or fabric, while water-based inks suit eco-friendly applications but may struggle with non-porous surfaces like metals unless chemically modified.
Substrate flatness is a key constraint. Unlike pad printing, screen printing excels on planar or near-planar surfaces, as the squeegee requires uniform contact to ensure consistent ink transfer. Surface energy mismatches can lead to poor adhesion, addressed through primers or plasma treatments, aligning the substrate’s energy with the ink’s wetting properties.
Phase 2: Process Efficiency and Automation
Pad printing’s efficiency lies in its adaptability to automation. Modern pad printing machines, equipped with rotary or linear systems, achieve cycle times of 1–3 seconds per print, with multi-color setups using multiple pads or clichés. Precision is enhanced by closed-cup systems, which minimize ink exposure to air, reducing solvent evaporation and maintaining viscosity stability over runs of 10,000–50,000 impressions.
However, setup complexity increases with design intricacy. Each color requires a separate cliché and pad cycle, limiting throughput for multi-color jobs compared to screen printing. Energy consumption, averaging 0.5–2 kWh per machine hour, remains moderate, though cliché production via laser engraving or chemical etching adds upfront costs and time.
Screen printing, by contrast, excels in high-volume production on flat surfaces. Automated rotary screen presses, common in textile manufacturing, achieve rates of 500–1,000 impressions per hour, with single-pass multi-color capabilities using aligned screens. Energy demands are higher, often 2–5 kWh per hour, due to drying ovens or UV curing units, but setup is streamlined for large runs, as a single screen can print thousands of identical designs without adjustment.
Phase 2: Precision and Resolution
Pad printing offers superior resolution for small, intricate designs, achieving line widths as fine as 0.05 mm under optimal conditions. This precision stems from the cliché’s etching accuracy and the pad’s ability to replicate micro-scale patterns, making it ideal for electronics (e.g., circuit board markings) or medical devices (e.g., syringe scales).
Screen printing’s resolution, limited by mesh size, typically ranges from 0.1 to 0.5 mm. Finer meshes improve detail but reduce ink volume, compromising opacity on dark substrates. Advances in emulsion technology and laser-cut stencils have narrowed this gap, yet screen printing remains less suited for micro-scale applications.
Phase 3: Applications and Industry Relevance
Pad printing dominates in industries requiring three-dimensional printing, such as automotive (dashboard dials), consumer electronics (remote buttons), and medical (catheter markings). Its ability to print on curved, uneven, or recessed surfaces ensures versatility, though it is less efficient for large-area coverage.
Screen printing thrives in textiles (t-shirts, banners), signage, and thick-film electronics (solar cells, membrane switches). Its capacity for heavy ink deposits suits applications demanding durability or opacity, such as outdoor graphics or ceramic decals, but it struggles with non-flat substrates.
Phase 3: Economic and Environmental Considerations
Pad printing’s initial costs include cliché fabrication ($50–$200 per design) and pad production ($10–$50 each), with ink costs of $20–$100 per liter. Small-batch flexibility offsets these expenses, though waste from solvent-based inks raises environmental concerns, mitigated by water-based alternatives.
Screen printing incurs higher setup costs for screens ($20–$100 each) but benefits from economies of scale in large runs. Ink usage is less efficient due to overspill, and VOC emissions remain a challenge, though UV-curable inks reduce solvent reliance.
Detailed Comparison Table
Attribute | Pad Printing | Screen Printing |
---|---|---|
Mechanism | Indirect gravure via silicone pad | Direct stencil via mesh screen |
Substrate Suitability | 3D, irregular surfaces | Flat or semi-flat surfaces |
Resolution | 0.05–0.2 mm | 0.1–0.5 mm |
Ink Thickness | 2–20 µm | 10–100 µm |
Setup Cost | $50–$200 (cliché) | $20–$100 (screen) |
Production Speed | 20–60 prints/min (automated) | 500–1,000 prints/hour (rotary press) |
Multi-Color Capability | Separate cycles per color | Single pass with multiple screens |
Ink Types | Solvent, UV, water-based | Solvent, UV, water-based |
Energy Consumption | 0.5–2 kWh/hour | 2–5 kWh/hour |
Environmental Impact | Moderate (solvent waste) | Higher (VOC emissions, ink overspill) |
Conclusion
Pad printing and screen printing serve complementary roles in the printing ecosystem, each excelling in specific niches. Pad printing’s precision and adaptability to complex surfaces make it indispensable for technical applications, while screen printing’s scalability and robustness suit high-volume, flat-surface production. Advances in ink chemistry, automation, and sustainability continue to refine both methods, ensuring their relevance in an evolving industrial landscape.
Maximize Tooling and CNC Metal Spinning Capabilities.
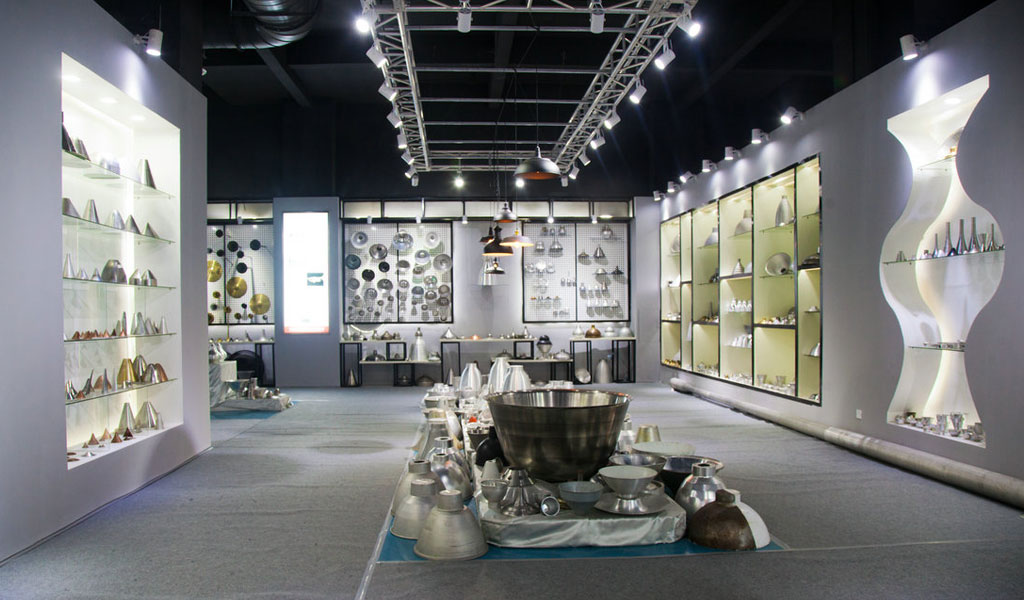
At BE-CU China Metal Spinning company, we make the most of our equipment while monitoring signs of excess wear and stress. In addition, we look into newer, modern equipment and invest in those that can support or increase our manufacturing capabilities. Our team is very mindful of our machines and tools, so we also routinely maintain them to ensure they don’t negatively impact your part’s quality and productivity.
Talk to us today about making a rapid prototype with our CNC metal spinning service. Get a direct quote by chatting with us here or request a free project review.
BE-CU China CNC Metal Spinning service include : CNC Metal Spinning,Metal Spinning Die,Laser Cutting, Tank Heads Spinning,Metal Hemispheres Spinning,Metal Cones Spinning,Metal Dish-Shaped Spinning,Metal Trumpet Spinning,Metal Venturi Spinning,Aluminum Spinning Products,Stainless Steel Spinning Products,Copper Spinning Products,Brass Spinning Products,Steel Spinning Product,Metal Spinnin LED Reflector,Metal Spinning Pressure Vessel,