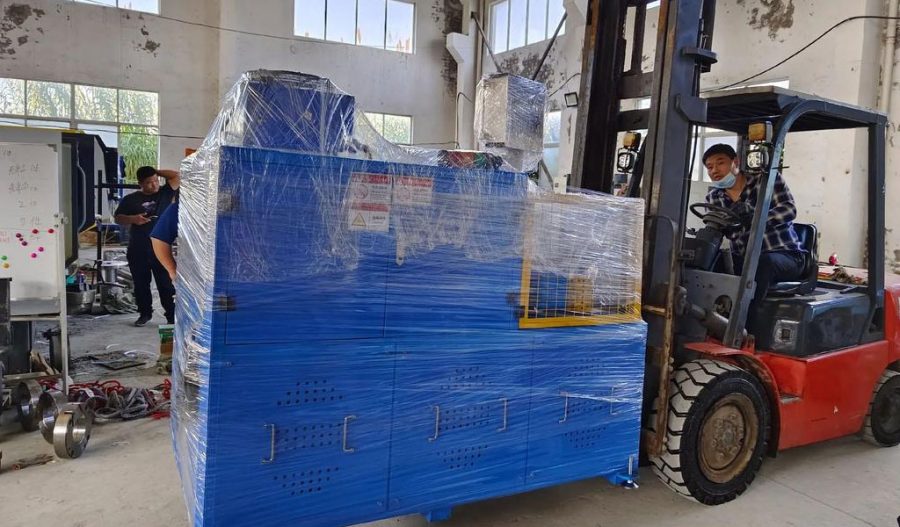
In the 1970s and 1980s, China imported several hydraulic programmable spinning machines, and at the end of the 20th century and the beginning of the 21st century, a batch of CNC spinning machines were introduced. This significantly enhanced China’s spinning processing capabilities and played a role in the absorption and assimilation of advanced technologies.
Transition to Digital Control
One of the significant factors contributing to the expansion of spinning technology applications in both military and civilian sectors is the transition from hydraulic to digital control in spinning equipment over the past 30 years. Especially in the past decade, the production capacity of domestic CNC general-purpose and specialized spinning machines has rapidly improved. CNC technology has solved issues related to the coordination between multiple spinning rollers, the setting and adjustment of roller motion trajectories (CAD/CAM design), and has elevated product precision to a new level. The development and popularization of CNC technology, along with market changes, have reduced the cost difference between CNC and hydraulic systems. The advantage of CNC systems has become more apparent, as complete sets of imported precision CNC systems, ball screws, linear guides, electro-hydraulic proportional servo drive systems, and advanced spindle frequency or servo speed control systems are now readily available on the market. Additionally, the use of computer-aided design (CAD) and the improvement of component matching markets have significantly shortened the development cycle of equipment. For instance, the delivery time for a medium-sized general-purpose spinning machine has been reduced from 3-5 years in the 1980s to less than a year today, with costs reduced to 1/3 to 1/2 of similar foreign equipment. Some experienced domestic spinning equipment manufacturers are now capable of providing contemporary CNC spinning equipment that meets current requirements, potentially replacing imports and even offering exports.
Upgrading Old Equipment
In the past decade, there has been a trend towards upgrading old spinning equipment in China. Many of the large and medium-sized spinning machines in use, mostly hydraulic, have been in service for 20-30 years. Some of the imported old equipment is no longer supported by the original manufacturers, and the original drawings are incomplete. These machines, often specialized, are large and costly. Upgrading and retrofitting these machines can save 60% to 80% of the cost compared to purchasing new equipment, as the foundation, bed, and tooling can be reused. In the 1990s, several small companies in foreign countries began this type of work. Some domestic units have also started this business, retrofitting 1970s-era domestic and imported spinning machines, including upgrading missing functions. For example, in the 1990s, North China University of Technology developed an automatic programming system for an imported CNC bottle closure machine to replace manual programming, achieving good results.
Development of Industry Standards
As the application range of spinning technology has expanded since the 1990s, China has gradually established and issued several industry standards. These include thinning spinning standards for the aviation industry, manufacturing and acceptance standards for spinning casings in the aerospace industry, spinning process preparation and product design standards in the machinery industry, and company standards for spinning machines. Additionally, industry standards for spinning heads and pulleys have been issued. The implementation of these standards has facilitated the orderly development of spinning technology in relevant industries.
Theoretical Research and Academic Contributions
In the 20th century, a notable trend in the forging industry was the focus of leading international scholars, such as B. Avitzur from the U.S., S. Kobayashi from Japan, and R. Kopp from Germany, on spinning as a topic for their doctoral theses. Many prominent Chinese professors in the forging field also began to engage in spinning theory research. Over the past 30 years, institutions such as Beihang University, Northwestern Polytechnical University, Harbin Institute of Technology, North China University of Technology, Yanshan University, and South China University of Technology have conducted extensive theoretical analysis and research on spinning. They have produced dozens of doctoral and master’s theses, contributing significantly to understanding spinning processes, selecting spinning process parameters, determining required force and energy parameters for spinning equipment, and improving product quality. Recent theoretical research includes three-dimensional finite element dynamic analysis, process simulation, and image demonstration, providing initial results in analyzing strain, stress, force, and deformation at every moment and minute region. Overall, China’s spinning theory research has effectively integrated with production practices.
Summary and Future Outlook
In summary, over the past half-century, especially in the 30+ years of reform and opening up, China’s spinning technology has advanced rapidly. The application in both military and civilian sectors has continually expanded, with spinning products becoming indispensable key products in many industries, creating significant economic benefits. Future developments in Chinese spinning technology can be summarized as follows:
- Formation of domestic CNC and hybrid CNC spinning machine capabilities
- Mass production and industrialization of spun products such as pulleys, heads, and gas cylinders
- Development of new structures, materials, and equipment for military products
- Export of domestic spinning products and equipment
- Introduction and development of advanced spinning equipment and production lines for new needs
- Technological upgrades of old spinning equipment
- Formulation of industry standards
- Expansion and deepening of spinning theory research
Despite these advancements, there remain gaps compared to international advanced levels in terms of series production, commercialization, automation, installation levels, expanding application fields, and the independent development of new spinning products and processes. Looking ahead, with technological progress and economic development, the variety of spinning products in China is expected to increase, and the spinning manufacturing industry will play a larger role in the national economy. Efforts will continue to further promote the development of Chinese spinning technology and narrow the gap with global advanced levels.
Global Trends in Spinning Technology
Globally, trends in spinning technology development can be summarized as follows:
- Advancing spinning machines towards CNC, achieving CNC for both high-force and conventional spinning machines, or more flexible CNC hybrid control
- Significantly increasing the operating speed of spinning machines to maximize production efficiency
- Achieving full automation of the spinning production process, with robots or mechanical hands handling automatic loading and unloading or even unmanned operations
- Developing multifunctional spinning machining centers that complete full processing of workpieces and integrate into production lines
- Evolving spinning equipment towards full automation, high precision, and larger sizes.
Maximize Tooling and CNC Metal Spinning Capabilities.
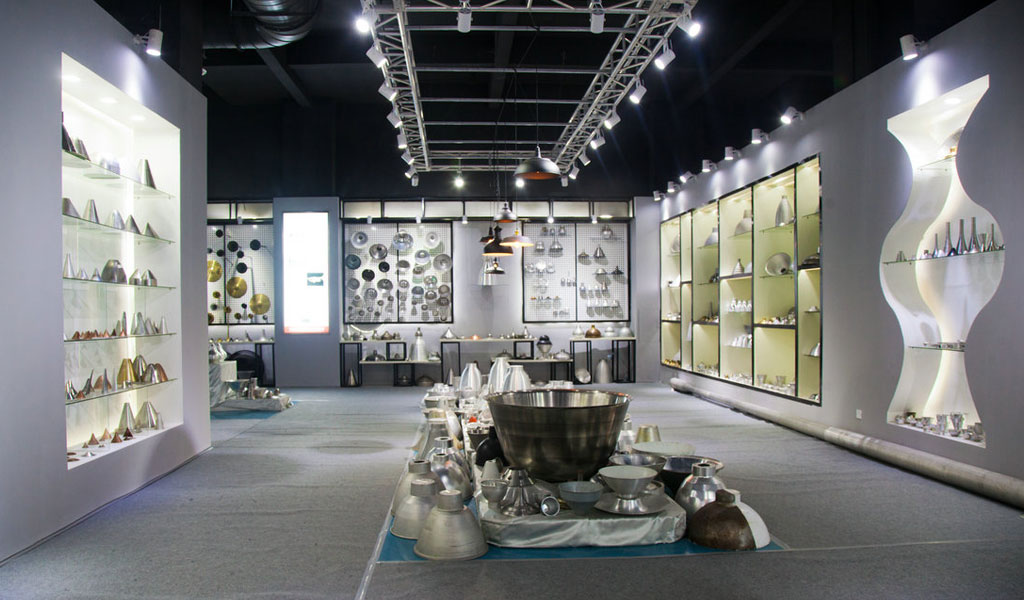
At BE-CU China Metal Spinning company, we make the most of our equipment while monitoring signs of excess wear and stress. In addition, we look into newer, modern equipment and invest in those that can support or increase our manufacturing capabilities. Our team is very mindful of our machines and tools, so we also routinely maintain them to ensure they don’t negatively impact your part’s quality and productivity.
Talk to us today about making a rapid prototype with our CNC metal spinning service. Get a direct quote by chatting with us here or request a free project review.
BE-CU China CNC Metal Spinning service include : CNC Metal Spinning,Metal Spinning Die,Laser Cutting, Tank Heads Spinning,Metal Hemispheres Spinning,Metal Cones Spinning,Metal Dish-Shaped Spinning,Metal Trumpet Spinning,Metal Venturi Spinning,Aluminum Spinning Products,Stainless Steel Spinning Products,Copper Spinning Products,Brass Spinning Products,Steel Spinning Product,Metal Spinnin LED Reflector,Metal Spinning Pressure Vessel,