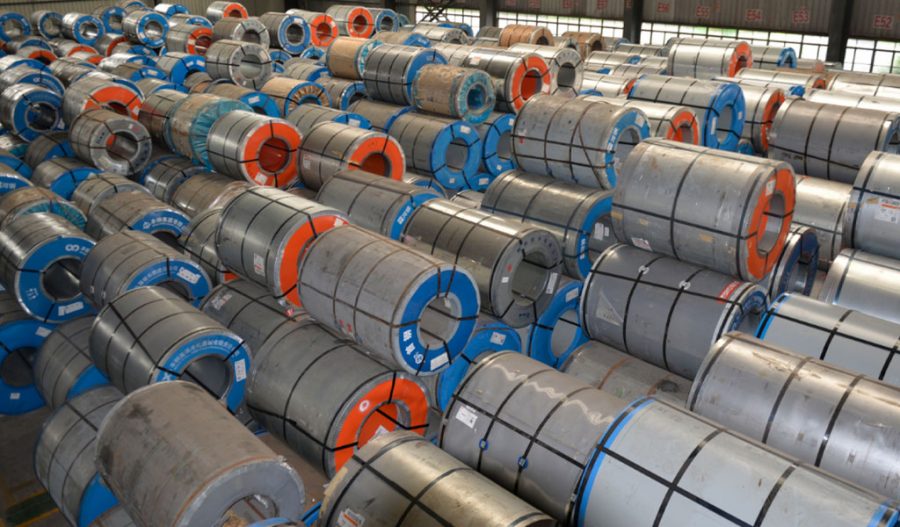
Robotic metal spinning is an advanced manufacturing process that integrates robotic systems with the traditional technique of metal spinning, a form of plastic deformation used to produce axially symmetric or non-axisymmetric metal components. Metal spinning, also known as spin forming or spinning, involves rotating a metal blank (typically a disc or tube) at high speed while applying localized pressure with a tool—historically a manual spoon or roller—to shape the material over a mandrel. The incorporation of robotics into this process enhances precision, repeatability, and flexibility, allowing for the production of complex geometries that were once limited by the skill of human artisans. This article explores the principles, history, technological advancements, applications, and scientific underpinnings of robotic metal spinning, with a focus on its evolution from a craft-based technique to a highly automated, intelligent manufacturing method.
Historical Context and Evolution
Metal spinning traces its origins to antiquity, with evidence of its use in ancient Egypt for shaping soft metals like copper and gold using rudimentary lathes powered by human effort. The process evolved significantly during the Industrial Revolution in the 18th and 19th centuries, when steam and hydraulic power enabled the spinning of harder materials such as brass and steel. By the early 20th century, electric motors provided the necessary rotational speeds and torque to refine the technique further, making it a staple in industries producing hollow, symmetrical parts like cookware, lighting fixtures, and automotive components.
The advent of robotics in the late 20th century marked a transformative shift in metal spinning. Early automation efforts, such as numerically controlled (NC) spinning machines introduced in the 1960s, relied heavily on pre-programmed tool paths and the expertise of skilled operators to adjust parameters. However, these systems lacked the adaptability to handle complex shapes or respond to real-time process variations. The integration of industrial robots, such as those developed by companies like Fanuc and Mitsubishi, introduced in the 1980s and 1990s, brought new capabilities to the field. Equipped with force feedback control, trajectory tracking algorithms, and multi-axis dexterity, robotic systems began to replace manual labor in spinning operations, paving the way for what is now termed robotic metal spinning.
Principles of Robotic Metal Spinning
At its core, robotic metal spinning is a plasticity forming process that deforms a ductile metal blank—typically aluminum, stainless steel, or mild steel—by applying controlled pressure against a rotating mandrel. The mandrel, a pre-shaped form that defines the final geometry, is mounted on a spindle, often driven by a servo motor for precise speed control. A robotic arm, fitted with a roller or paddle tool, exerts localized force on the blank, incrementally shaping it to conform to the mandrel’s contours. Unlike traditional spinning, where human operators relied on tactile feedback and experience, robotic systems utilize sensors and algorithms to regulate force, position, and speed, optimizing the forming process.
The process can be categorized into two primary variants: conventional spinning and shear spinning. Conventional spinning involves multiple passes of the roller to gradually reduce the blank’s thickness and shape it into a desired form, preserving much of the original material volume. Shear spinning, by contrast, thins the material significantly by applying a single, forceful pass, resulting in a conical or tapered shape with reduced wall thickness. Robotic systems excel in both variants, offering the ability to switch between techniques or combine them in hybrid approaches, depending on the product requirements.
Technological Components
The implementation of robotic metal spinning relies on several key components:
- Robotic Manipulator: Industrial robots, such as the Mitsubishi PA10-6CE or Fanuc models, provide the multi-degree-of-freedom motion necessary for precise tool positioning. These robots are equipped with articulated arms capable of six or more axes, enabling complex trajectories around the mandrel.
- Tooling: The roller tool, typically made of hardened steel or brass, varies in diameter and radius depending on the material and desired finish. In robotic applications, tools may incorporate bearings to reduce friction or ceramic coatings to extend lifespan.
- Mandrel and Spindle: The mandrel defines the final shape and is mounted on a spindle driven by a DC servo motor. Rotational speeds typically range from 300 to 2000 rpm, adjustable based on material properties and forming conditions.
- Sensors: Force sensors, such as piezoelectric or strain-gauge-based systems, measure the contact force between the roller and blank, enabling real-time adjustments via force feedback control. Position sensors and encoders ensure accurate tool path tracking.
- Control Systems: Advanced algorithms, including hybrid position/force control and impedance control, govern the robot’s movements. These systems integrate data from sensors to adapt to material behavior, minimizing defects like wrinkling or cracking.
Scientific Foundations
The mechanics of robotic metal spinning are rooted in the principles of plastic deformation, where the metal undergoes permanent shape change under applied stress beyond its yield point. The process involves a combination of tensile, compressive, and shear stresses, influenced by factors such as material ductility, strain rate, and temperature. For a typical aluminum alloy (e.g., 6061-T6), the yield strength might range from 240–310 MPa, with an elongation at break of 12–17%, making it suitable for spinning due to its balance of strength and formability.
The strain distribution during spinning is non-uniform, with the highest deformation occurring at the point of roller contact. Finite element analysis (FEA) studies, such as those conducted using software like MSC Simufact.Forming, reveal that radial spinning forces press the blank against the mandrel, while axial forces induce tensile stress along the tool path. Excessive axial force can lead to cracking, while high tangential forces may cause wrinkling—phenomena that robotic control systems aim to mitigate through precise force regulation.
Vibration is another critical factor, as high-speed rotation and tool contact can induce oscillations that affect surface quality. Research has shown that adding vibration suppressors, such as tuned mass dampers or active control algorithms, can reduce these effects, improving dimensional accuracy by up to 15% in experimental setups.
Advancements in Robotic Metal Spinning
Recent advancements have expanded the scope of robotic metal spinning beyond traditional axisymmetric parts. One notable development is the use of force-controlled robots to form non-axisymmetric products, such as square cups or oval dish covers. By synchronizing the roller’s motion with a noncircular mandrel and adjusting the pushing force dynamically, robots can track varying radii, achieving shapes unattainable with manual methods. Experiments with linear motor-driven rollers, as opposed to traditional hydraulic systems, have demonstrated faster response times (on the order of milliseconds) and improved forming speeds, reducing cycle times by 20–30%.
Trajectory tracking algorithms have also evolved, incorporating variable speed profiles to optimize strain distribution. For instance, a study using a Mitsubishi PA10-6CE robot demonstrated that a variable feed rate of 40–60 mm/min, combined with a spindle speed of 500 rpm, minimized wrinkle formation in aluminum blanks compared to constant-speed approaches. These algorithms often employ cascaded control loops, integrating position, velocity, and force feedback to enhance stability and precision.
Additive manufacturing techniques have further complemented robotic spinning by enabling the rapid production of custom mandrels. Using materials like high-strength polymers or low-melt alloys, manufacturers can create complex mandrel geometries tailored to specific products, reducing lead times and costs compared to traditional machining.
Applications
Robotic metal spinning finds applications across diverse industries due to its versatility and efficiency:
- Aerospace: Components like nose cones, nozzles, and fuselage sections benefit from the process’s ability to produce lightweight, high-strength parts with tight tolerances. Japan’s H-IIA rocket, for example, uses manually spun nose cones, a task increasingly automated with robotics.
- Automotive: Wheel rims, exhaust components, and fuel tanks are spun using robotic systems to ensure consistency and reduce material waste.
- Consumer Goods: Hollowware such as pots, pans, and lighting fixtures leverage the process for its low tooling costs and high surface quality.
- Industrial Equipment: Tanks, pressure vessels, and parabolic antennas are produced with robotic spinning for their durability and geometric precision.
The process is particularly advantageous for small-to-medium batch production, where flexibility and minimal setup time outweigh the economies of scale offered by mass-production methods like stamping.
Comparative Analysis
To illustrate the advantages and limitations of robotic metal spinning, the following tables compare it with traditional manual spinning and other automated forming processes, such as CNC spinning and stamping.
Table 1: Comparison of Metal Spinning Techniques
Parameter | Manual Spinning | CNC Spinning | Robotic Spinning |
---|---|---|---|
Automation Level | None (human-operated) | High (pre-programmed) | Very High (adaptive) |
Shape Complexity | Limited to simple symmetry | Moderate (axisymmetric) | High (non-axisymmetric) |
Setup Time | Low (minimal equipment) | Moderate (programming) | Low (flexible robotics) |
Cycle Time | Slow (10–20 min/part) | Moderate (2–5 min/part) | Fast (1–3 min/part) |
Precision | Variable (skill-dependent) | High (±0.1 mm) | Very High (±0.05 mm) |
Tooling Cost | Low ($50–$200) | Moderate ($500–$2000) | Moderate ($1000–$3000) |
Force Control | Manual (tactile feedback) | Limited (fixed parameters) | Advanced (real-time) |
Material Thickness | Thin (<3 mm) | Medium (<6 mm) | Wide Range (<10 mm) |
Defect Rate | High (10–20%) | Moderate (5–10%) | Low (1–5%) |
Table 2: Comparison with Other Forming Processes
Parameter | Robotic Spinning | Stamping | Hydroforming |
---|---|---|---|
Material Utilization | High (90–95%) | Moderate (70–80%) | High (85–90%) |
Production Volume | Low to Medium (10–1000) | High (1000+) | Medium (100–5000) |
Geometric Flexibility | High (complex shapes) | Low (fixed dies) | Moderate (symmetric) |
Tooling Cost | Moderate ($1000–$3000) | High ($10,000–$50,000) | High ($5000–$20,000) |
Forming Force | Low (kg range) | High (tons range) | Moderate (tons range) |
Surface Finish | Excellent (Ra < 1 µm) | Good (Ra 1–3 µm) | Good (Ra 1–2 µm) |
Cycle Time | Fast (1–3 min/part) | Very Fast (<1 min/part) | Moderate (2–5 min/part) |
Energy Consumption | Low (10–50 kW) | High (100–500 kW) | Moderate (50–200 kW) |
These tables highlight robotic spinning’s strengths in flexibility, precision, and low-force requirements, making it ideal for niche applications, while stamping excels in high-volume production with simpler shapes.
Challenges and Limitations
Despite its advantages, robotic metal spinning faces several challenges. The complexity of deformation mechanics—three-dimensional and highly nonlinear—complicates real-time modeling and simulation. Finite element models, while accurate, are computationally intensive, often requiring hours to simulate a single pass, which limits their use for online toolpath correction. As a result, process optimization still relies heavily on experimental data and trial-and-error adjustments.
Material behavior poses another hurdle. High-strength alloys, such as titanium or Inconel, exhibit limited ductility at room temperature, necessitating elevated temperatures or specialized tooling, which increases costs. Wrinkling and cracking remain persistent risks, particularly in thin-walled parts (<1 mm), where small variations in force or speed can destabilize the process.
Cost is also a factor. While robotic systems reduce labor expenses, the initial investment in robots, sensors, and software (often exceeding $50,000) can be prohibitive for small manufacturers. Maintenance of precision components, such as force sensors and articulated joints, further adds to operational overhead.
Future Directions
The future of robotic metal spinning lies in the integration of artificial intelligence (AI) and machine learning (ML). AI-driven systems could analyze sensor data in real time to predict defects, optimize tool paths, and adjust parameters like feed rate and spindle speed dynamically. For example, a neural network trained on experimental spinning data could reduce setup time by 50% by suggesting optimal starting conditions for new materials or geometries.
Additive manufacturing’s role is also expanding, with hybrid processes combining 3D-printed mandrels and robotic spinning showing promise for rapid prototyping. Research into smart materials, such as shape-memory alloys, could enable self-adaptive mandrels that adjust shape during spinning, further enhancing flexibility.
Sustainability is another focus area. Robotic spinning’s high material utilization and low energy consumption align with green manufacturing goals, and future innovations may incorporate recycled metals or biodegradable lubricants to reduce environmental impact.
Conclusion
Robotic metal spinning represents a fusion of traditional craftsmanship and cutting-edge technology, transforming a centuries-old process into a cornerstone of modern manufacturing. By leveraging robotic precision, advanced control systems, and scientific insights into material behavior, this technique offers unparalleled flexibility and quality for producing complex metal components. While challenges remain, ongoing research and technological advancements promise to push the boundaries of what robotic spinning can achieve, cementing its place in industries ranging from aerospace to consumer goods. As automation and intelligence continue to evolve, robotic metal spinning stands poised to redefine the art and science of metal forming for the 21st century.
Maximize Tooling and CNC Metal Spinning Capabilities.
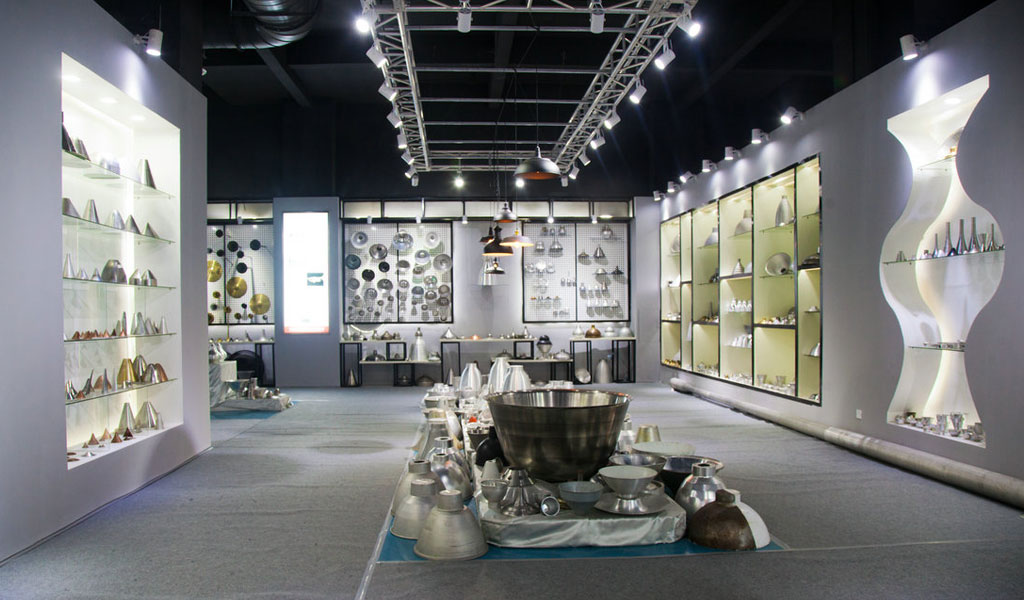
At BE-CU China Metal Spinning company, we make the most of our equipment while monitoring signs of excess wear and stress. In addition, we look into newer, modern equipment and invest in those that can support or increase our manufacturing capabilities. Our team is very mindful of our machines and tools, so we also routinely maintain them to ensure they don’t negatively impact your part’s quality and productivity.
Talk to us today about making a rapid prototype with our CNC metal spinning service. Get a direct quote by chatting with us here or request a free project review.
BE-CU China CNC Metal Spinning service include : CNC Metal Spinning,Metal Spinning Die,Laser Cutting, Tank Heads Spinning,Metal Hemispheres Spinning,Metal Cones Spinning,Metal Dish-Shaped Spinning,Metal Trumpet Spinning,Metal Venturi Spinning,Aluminum Spinning Products,Stainless Steel Spinning Products,Copper Spinning Products,Brass Spinning Products,Steel Spinning Product,Metal Spinnin LED Reflector,Metal Spinning Pressure Vessel,