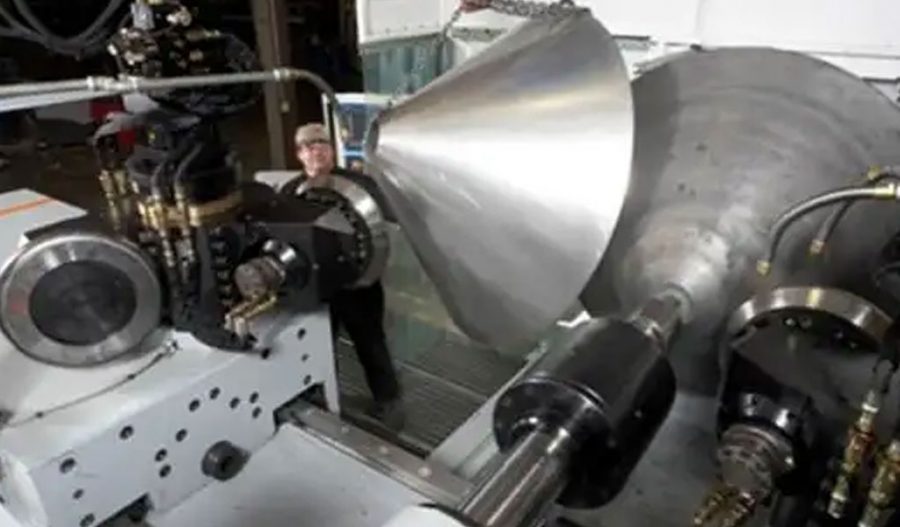
The design and development of flexible fixtures for positioning in the processing of digital electronic spinning parts represent a critical advancement in modern manufacturing technology. As industries increasingly rely on precision-engineered components for digital electronics—such as those used in smartphones, computers, and other advanced devices—the need for adaptable, efficient, and accurate fixtures has grown exponentially. This article explores the intricacies of designing such a fixture, delving into its mechanical principles, material considerations, adaptability to spinning processes, and integration with digital electronic part production. Through detailed explanations, comparisons, and technical tables, this discussion aims to provide a comprehensive resource for engineers, researchers, and manufacturers seeking to optimize the production of spinning parts in the digital electronics sector.
Flexible fixtures are specialized tools designed to hold and position workpieces during manufacturing processes, such as machining, assembly, or inspection. Unlike traditional rigid fixtures, which are tailored to specific parts and lack versatility, flexible fixtures offer adjustability to accommodate a range of part geometries and sizes. In the context of digital electronic spinning parts—components often produced through rotational forming or machining processes like spinning, turning, or milling—these fixtures must ensure high precision, repeatability, and stability while adapting to the unique demands of miniaturized, intricate designs. The spinning process itself involves forming metal or other materials into cylindrical or conical shapes by rotating a workpiece against a tool, a technique widely used in producing enclosures, connectors, and housings for electronic devices.
The importance of flexible fixtures in this domain lies in their ability to address the challenges posed by the rapid evolution of digital electronics. As product cycles shorten and consumer demand for customized, high-performance devices increases, manufacturers must produce parts with tight tolerances and complex geometries in small batches or even single-unit runs. Traditional fixtures, while effective for mass production of uniform components, are ill-suited to such variability. A flexible fixture, by contrast, can be reconfigured quickly, reducing downtime, minimizing setup costs, and enhancing overall efficiency. This adaptability is particularly valuable in the production of spinning parts, where the workpiece must be securely held and precisely aligned during high-speed rotation to avoid defects like eccentricity, surface imperfections, or dimensional inaccuracies.
Mechanical Principles of Flexible Fixture Design
At the core of a flexible fixture’s design are the mechanical principles that govern its functionality: clamping force, positional accuracy, and dynamic stability. Clamping force refers to the mechanism by which the fixture secures the workpiece. In spinning processes, this force must be sufficient to prevent slippage or vibration while avoiding excessive pressure that could deform delicate electronic components. Common clamping mechanisms include pneumatic, hydraulic, or manual systems, each with distinct advantages. Pneumatic clamps, for example, offer rapid actuation and consistent force, making them ideal for high-throughput environments, whereas hydraulic systems provide higher clamping strength for larger or more robust parts.
Positional accuracy is equally critical, as even minor misalignment during spinning can result in defective parts. Flexible fixtures achieve this through adjustable locating elements—such as pins, jaws, or modular bases—that can be repositioned to match the workpiece’s geometry. These elements are often paired with precision measurement systems, such as laser sensors or coordinate measuring machines (CMMs), to verify alignment in real time. Dynamic stability, meanwhile, ensures that the fixture maintains its integrity under the rotational forces and vibrations inherent in spinning. This is achieved through robust structural design, often incorporating materials with high damping capacities, such as cast iron or polymer composites, and optimized geometries that minimize resonance.
Material Selection for Flexible Fixtures
The choice of materials for a flexible fixture significantly influences its performance, durability, and cost. In the processing of digital electronic spinning parts, fixtures must withstand mechanical stress, thermal fluctuations, and potential chemical exposure (e.g., from cutting fluids) while remaining lightweight and easy to reconfigure. Common materials include aluminum alloys, tool steels, and advanced composites, each offering a unique balance of properties.
Aluminum alloys, such as 6061-T6 or 7075, are widely used due to their excellent strength-to-weight ratio, corrosion resistance, and machinability. These properties make them suitable for fixtures requiring frequent adjustments or lightweight construction, as is often the case in small-batch production of electronic components. However, aluminum’s relatively low hardness and wear resistance can limit its lifespan in high-wear applications, necessitating protective coatings like anodizing or the use of hardened inserts at contact points.
Tool steels, such as A2 or D2, offer superior hardness and wear resistance, making them ideal for fixtures subjected to prolonged use or abrasive conditions. Their high strength allows them to maintain dimensional stability under heavy loads, a key consideration for spinning parts with thicker walls or higher rotational speeds. However, tool steels are heavier and more expensive than aluminum, and their rigidity can complicate the design of adjustable features.
Advanced composites, including carbon fiber-reinforced polymers (CFRP) and glass fiber-reinforced polymers (GFRP), represent a modern alternative. These materials combine low weight with high stiffness and excellent vibration damping, reducing chatter during spinning and improving surface finish on the workpiece. Their non-conductive nature is also advantageous in electronic applications, minimizing the risk of electrical interference. However, composites are costly and less durable under impact or point loading, requiring careful design to avoid failure at stress concentrations.
Table 1: Material Properties Comparison for Flexible Fixtures
Material | Density (g/cm³) | Tensile Strength (MPa) | Hardness (HB) | Wear Resistance | Cost ($/kg) | Vibration Damping |
---|---|---|---|---|---|---|
Aluminum 6061-T6 | 2.7 | 310 | 95 | Moderate | 3-5 | Low |
Aluminum 7075 | 2.81 | 570 | 150 | Moderate | 5-7 | Low |
Tool Steel A2 | 7.86 | 620 | 200 | High | 8-12 | Moderate |
Tool Steel D2 | 7.7 | 750 | 250 | Very High | 10-15 | Moderate |
CFRP | 1.6 | 600-1200 | N/A | Moderate | 20-50 | High |
GFRP | 1.8 | 300-500 | N/A | Moderate | 10-20 | High |
Note: Values are approximate and depend on specific processing and alloy composition.
Design Features for Adaptability
A hallmark of flexible fixtures is their modularity, which allows them to adapt to a variety of workpiece shapes and sizes. In the context of digital electronic spinning parts, this adaptability is achieved through several key design features. First, interchangeable clamping modules enable the fixture to switch between different holding mechanisms—such as collets, chucks, or vacuum grips—depending on the part’s requirements. For instance, a thin-walled cylindrical housing might require a vacuum grip to avoid deformation, while a solid connector pin might use a collet for maximum rigidity.
Second, adjustable locating pins or rails allow the fixture to reposition its reference points. These components are often mounted on slotted bases or T-slot systems, enabling precise sliding or rotational adjustments. In some advanced designs, servo motors or piezoelectric actuators drive these adjustments, integrating the fixture with computer numerical control (CNC) systems for automated reconfiguration. This is particularly useful in spinning processes, where the workpiece must be centered with sub-micron accuracy to ensure uniform material flow and wall thickness.
Third, modular baseplates provide a foundation for rapid fixture assembly. These plates feature standardized hole patterns (e.g., M6 or 1/4-20 threads) compatible with a range of attachments, allowing operators to build custom setups from a library of components. For digital electronic parts, which often vary in diameter and length, this modularity reduces the need for bespoke fixtures, cutting lead times and costs.
Integration with Spinning Processes
Spinning, as a metal-forming technique, involves rotating a workpiece at high speed while a tool applies pressure to shape it. In digital electronics, spinning is used to produce components like heat sinks, RF shields, and battery casings, which require precise dimensional control and smooth surfaces. The flexible fixture must therefore integrate seamlessly with the spinning machine—typically a lathe or dedicated spinning center—while accommodating the process’s unique demands.
One key requirement is rotational balance. Any asymmetry in the fixture or workpiece can induce vibrations, leading to chatter marks or uneven thickness. To mitigate this, flexible fixtures often incorporate counterweights or dynamic balancing systems that adjust automatically as the part is reconfigured. Additionally, the fixture must allow for tool access, ensuring that the spinning tool can contact the workpiece at the correct angle and depth without interference.
Another consideration is thermal management. Spinning generates heat through friction and deformation, which can affect both the workpiece and the fixture. For electronic parts made from materials like aluminum or copper, excessive heat can alter microstructure or introduce residual stresses, compromising performance. Flexible fixtures address this by incorporating cooling channels for air or liquid circulation, or by using thermally stable materials that resist expansion and contraction.
Table 2: Comparison of Clamping Mechanisms in Spinning Fixtures
Mechanism | Actuation Speed (s) | Clamping Force (N) | Precision (μm) | Cost ($) | Suitability for Thin Parts | Automation Compatibility |
---|---|---|---|---|---|---|
Pneumatic Clamp | 0.5-1 | 500-2000 | 10-20 | 100-300 | Moderate | High |
Hydraulic Clamp | 1-2 | 1000-5000 | 5-15 | 200-500 | Low | Moderate |
Manual Clamp | 5-10 | 200-1000 | 20-50 | 50-150 | High | Low |
Vacuum Grip | 0.1-0.5 | 100-500 | 5-10 | 300-700 | Very High | High |
Note: Values are indicative and vary by specific design and application.
Application to Digital Electronic Spinning Parts
Digital electronic spinning parts encompass a wide range of components, from micro-scale connectors to larger enclosures. For example, a typical smartphone might include a spun aluminum antenna housing, a copper heat pipe, and a stainless steel battery cover—all of which benefit from flexible fixturing. The fixture’s ability to adjust to these diverse shapes ensures that manufacturers can maintain a single production line for multiple products, a critical advantage in an industry characterized by rapid design iteration.
Consider the production of a heat pipe, a hollow tube used to transfer heat from a processor to a cooling surface. The spinning process forms the tube from a flat blank, requiring precise control over wall thickness (often 0.1-0.5 mm) and diameter (typically 3-10 mm). A flexible fixture for this application might use a vacuum grip to hold the blank, adjustable pins to center it, and a pneumatic clamp to secure it during rotation. As the design evolves—say, to accommodate a larger processor—the fixture can be reconfigured by swapping the grip size and repositioning the pins, avoiding the need for a new tool.
Similarly, in RF shield production, spinning forms a thin-walled conical shield to block electromagnetic interference. Here, surface finish is paramount, as imperfections can disrupt signal integrity. The fixture’s damping properties and balance ensure a smooth spin, while its modularity allows it to handle shields of varying heights and angles.
Challenges and Future Directions
Despite their advantages, flexible fixtures face several challenges. Cost remains a barrier, as adjustable components and automation systems increase initial investment compared to rigid fixtures. Additionally, the complexity of reconfiguration can introduce setup errors, necessitating skilled operators or robust quality control. For spinning parts, wear on adjustable elements like pins or jaws can also degrade precision over time, requiring regular maintenance.
Looking ahead, advancements in additive manufacturing (3D printing) and artificial intelligence (AI) promise to enhance flexible fixture design. 3D printing enables the rapid prototyping of custom fixture components, such as lightweight lattice structures or conformal cooling channels, tailored to specific spinning tasks. AI, meanwhile, can optimize fixture configurations by analyzing part geometries and process parameters, predicting the best setup for efficiency and accuracy.
Conclusion
The design of a flexible fixture for positioning in the processing of digital electronic spinning parts is a multifaceted endeavor, blending mechanical engineering, materials science, and manufacturing strategy. By leveraging modularity, precision, and adaptability, these fixtures enable the efficient production of complex, high-quality components essential to modern electronics. As technology evolves, so too will these tools, driving innovation in both design and application.
Maximize Tooling and CNC Metal Spinning Capabilities.
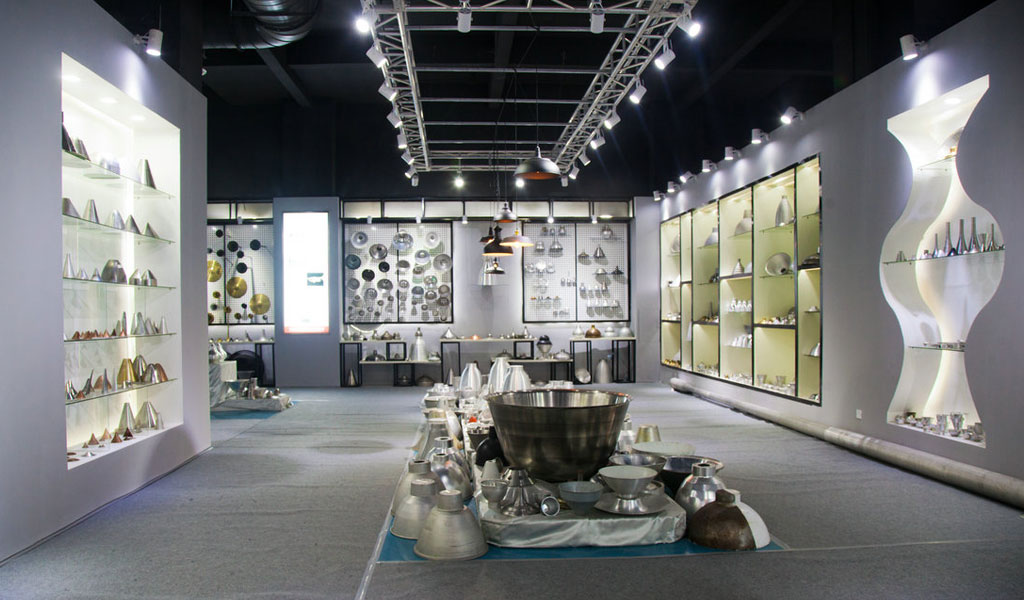
At BE-CU China Metal Spinning company, we make the most of our equipment while monitoring signs of excess wear and stress. In addition, we look into newer, modern equipment and invest in those that can support or increase our manufacturing capabilities. Our team is very mindful of our machines and tools, so we also routinely maintain them to ensure they don’t negatively impact your part’s quality and productivity.
Talk to us today about making a rapid prototype with our CNC metal spinning service. Get a direct quote by chatting with us here or request a free project review.
BE-CU China CNC Metal Spinning service include : CNC Metal Spinning,Metal Spinning Die,Laser Cutting, Tank Heads Spinning,Metal Hemispheres Spinning,Metal Cones Spinning,Metal Dish-Shaped Spinning,Metal Trumpet Spinning,Metal Venturi Spinning,Aluminum Spinning Products,Stainless Steel Spinning Products,Copper Spinning Products,Brass Spinning Products,Steel Spinning Product,Metal Spinnin LED Reflector,Metal Spinning Pressure Vessel,