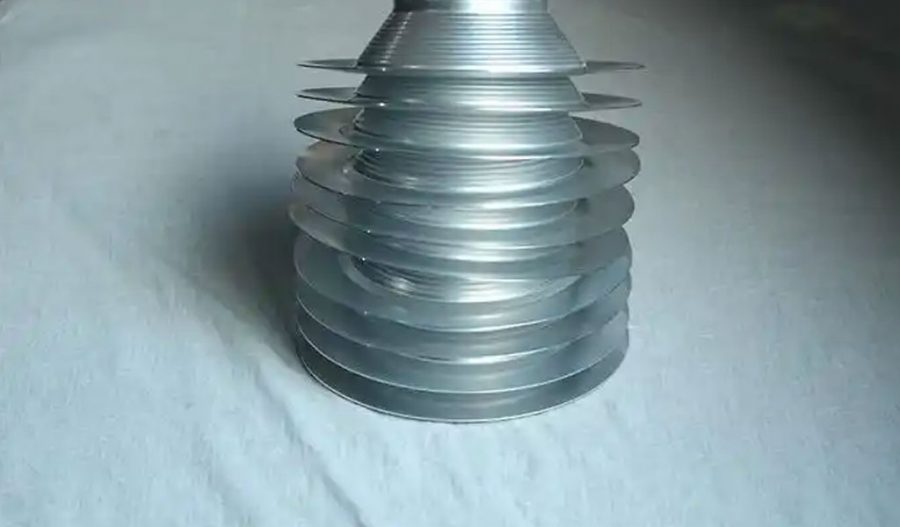
Metal spinning, a highly versatile manufacturing process, involves the shaping of metal into circular forms by rotating the workpiece on a lathe while applying pressure with tools. This technique is especially useful for producing components that require high precision, uniformity, and minimal material wastage. Within the realm of electronics, metal spinning plays a crucial role in creating complex, intricate, and durable parts that contribute to the functionality and aesthetics of electronic devices.
This article will explore the top 20 metal spinning parts used in the electronics industry, focusing on their specific applications, materials, benefits, and manufacturing considerations. From connectors and housings to heat sinks and reflectors, these parts are essential in delivering the performance and reliability that electronic products demand.
1. Connectors
Connectors are critical components in electronic systems, allowing for the transfer of electrical signals or power between different parts of a device. Metal spinning is used to produce various types of connectors, such as coaxial cable connectors, RF connectors, and power connectors. These parts are often made from materials like aluminum, brass, or stainless steel to ensure good conductivity and durability.
The metal spinning process enables manufacturers to achieve the precise geometries needed for connectors, ensuring a secure and reliable connection between components. The high-quality surface finish achievable with spinning is another reason why it is favored for these applications, reducing the likelihood of corrosion or wear over time.
2. Enclosures and Housings
In the electronics industry, enclosures and housings are essential for protecting delicate internal components from physical damage, dust, moisture, and other environmental factors. Metal spinning is commonly employed to create custom enclosures for various electronic devices, including power supplies, circuit boards, and sensors.
Spun metal enclosures are lightweight yet robust, offering superior protection while maintaining a compact and streamlined design. Aluminum is often the material of choice due to its excellent strength-to-weight ratio and corrosion resistance, but other metals such as stainless steel or copper can also be used depending on the specific application.
3. Heat Sinks
Heat sinks are essential in managing the temperature of electronic devices, especially those with high-power components like processors, transistors, and integrated circuits. These parts are designed to dissipate heat away from sensitive electronics, preventing overheating and ensuring reliable performance.
Metal spinning is used to manufacture heat sinks with precise geometries, such as fins and channels, that optimize heat dissipation. Materials like aluminum and copper are commonly used for their excellent thermal conductivity. The spinning process allows for the creation of heat sinks with high surface areas, which improves the efficiency of heat transfer.
4. Reflectors and Lenses
In electronic devices such as cameras, projectors, and lighting systems, reflectors and lenses are critical components that direct and shape light. Metal spinning is employed to create reflectors with smooth, reflective surfaces that help optimize the performance of optical systems.
These spun parts are made from materials such as aluminum, stainless steel, or titanium, which offer a combination of reflectivity, strength, and lightweight properties. The precision of the spinning process ensures that reflectors maintain their intended shape and reflective properties, even in demanding environments.
5. Batteries and Battery Casings
Batteries are the power sources for most electronic devices, and their casings are designed to contain the battery cells and protect them from physical damage and environmental hazards. Metal spinning is used to create battery casings, particularly for cylindrical and prismatic batteries, which are commonly found in consumer electronics like smartphones, laptops, and power tools.
Spun metal casings are typically made from stainless steel or aluminum, providing both strength and resistance to corrosion. The spinning process allows for the production of battery casings with tight tolerances and smooth, uniform surfaces, which are crucial for the proper functioning and safety of the battery.
6. Caps and Covers
Caps and covers are protective components used in a wide range of electronic devices to shield internal circuits, connectors, and other sensitive parts from dust, moisture, and physical impacts. Metal spinning is used to produce caps and covers in a variety of shapes and sizes, including domed, flat, and cylindrical forms.
These parts are often made from materials such as aluminum, steel, and brass, which offer strength and durability while keeping the weight of the device to a minimum. The ability to spin these components with tight tolerances ensures that they fit securely over the protected parts, providing a reliable barrier against external factors.
7. Cable Shields
Cable shields are used in electronic cables to protect the inner conductors from electromagnetic interference (EMI) and physical damage. These shields are typically made from metal, and the metal spinning process is ideal for creating cylindrical, flexible, and robust shields that can wrap around cables to provide full coverage.
Spun cable shields are made from materials like aluminum, copper, or tinned copper, which provide effective shielding against EMI and corrosion resistance. The metal spinning process ensures that the shields have consistent wall thicknesses and smooth surfaces, which are essential for their performance.
8. Chassis and Frames
The chassis or frame of an electronic device serves as the structural foundation that houses and supports internal components. These parts are typically made from metal, and metal spinning allows for the creation of custom chassis with complex shapes and high structural integrity.
Spun metal chassis are often made from aluminum or stainless steel, offering both lightweight properties and resistance to corrosion. The precision of the spinning process ensures that the chassis components fit together perfectly, providing a secure and stable housing for the electronics.
9. Heat Exchangers
Heat exchangers are used in various electronic applications, particularly in power electronics and data centers, to manage heat dissipation. These devices transfer heat from one fluid or gas to another and require the use of materials with high thermal conductivity.
Spun heat exchangers are often made from aluminum or copper, and the metal spinning process allows for the production of parts with intricate fins and channels that maximize surface area for heat transfer. The ability to create uniform geometries with minimal waste makes metal spinning an ideal process for manufacturing heat exchangers.
10. Capacitor Casings
Capacitors are electronic components that store and release electrical energy. They are used in a wide range of devices, from power supplies to communication systems. The casings that house these capacitors must be both durable and electrically conductive to protect the internal components and ensure proper functionality.
Metal spinning is used to create capacitor casings with precise dimensions and tight tolerances. These casings are typically made from aluminum, which is lightweight and resistant to corrosion. The spinning process allows for the creation of custom shapes that suit different capacitor designs, ensuring a perfect fit for the internal components.
11. Inductor Cores
Inductors are essential components in electronic circuits, used to store energy in a magnetic field. The cores of these inductors are often made from metal, and metal spinning is used to produce high-precision cores with uniform thickness and material consistency.
Spun inductor cores are typically made from materials like stainless steel or soft magnetic alloys, which provide high magnetic permeability. The spinning process ensures that the cores are free of defects and have the precise geometry needed to maximize the inductance and efficiency of the component.
12. Oscillator Cases
Oscillators are electronic circuits used to generate a periodic signal, typically in the form of a sine wave, square wave, or triangular wave. The cases that house these oscillators must provide protection against external factors while allowing for effective heat dissipation.
Metal spinning is used to create oscillator cases, typically made from aluminum or steel, which offer strength, durability, and effective thermal management. The precision of the spinning process ensures that the oscillator cases have the correct dimensions, providing a secure and functional enclosure for the oscillator circuits.
13. Sensor Housings
Sensors are integral to many electronic devices, converting physical stimuli (such as light, temperature, or motion) into electrical signals. The housings for these sensors must be designed to protect the sensitive components inside while maintaining the necessary performance characteristics.
Spun metal sensor housings are typically made from aluminum or stainless steel and can be produced in a variety of shapes, including cylindrical, conical, or dome-like. The metal spinning process ensures that the housings have a smooth, uniform surface and precise dimensions, which are essential for the proper functioning and protection of the sensors.
14. Circuit Board Supports
Circuit boards are the backbone of most electronic devices, providing the platform for all the components that make the device function. Circuit board supports, which are metal parts that help secure and stabilize the boards within enclosures, are often produced through metal spinning.
These supports are typically made from aluminum or stainless steel and are spun to the exact dimensions required to hold the circuit boards in place. The spinning process ensures that the supports are uniform and strong, preventing any damage or misalignment of the boards during operation.
15. Voltage Regulators
Voltage regulators are used in electronic circuits to maintain a constant output voltage regardless of input voltage variations. These components often require custom metal enclosures to protect the sensitive electronic circuits inside.
Spun metal voltage regulator enclosures are typically made from aluminum or copper, which provide both thermal conductivity and electromagnetic shielding. The precision of the metal spinning process ensures that the enclosures have the correct size, shape, and thickness to protect the internal components while allowing for efficient heat dissipation.
16. Antennas
Antennas are vital components in wireless communication systems, responsible for transmitting and receiving radio waves. Metal spinning is used to manufacture various types of antennas, including helical, dipole, and parabolic antennas.
These spun antennas are typically made from metals like aluminum, copper, or stainless steel, which offer the necessary conductivity and durability for long-term performance. The spinning process allows for the creation of antennas with complex shapes and geometries that would be difficult to achieve through other manufacturing methods.
17. Microphone Grills
Microphones are used in a variety of electronic devices, from telephones to recording equipment. The grills that protect the sensitive microphone elements from damage and contamination are often made using the metal spinning process.
Spun microphone grills are typically made from materials like stainless steel or aluminum, which offer both strength and corrosion resistance. The precision of the spinning process ensures that the grills have a uniform mesh structure that allows sound to pass through while providing adequate protection for the microphone’s sensitive components.
18. Reflective Coils
In certain electronic devices, such as transformers and inductors, reflective coils are used to direct electromagnetic energy. These coils must be manufactured with a high degree of precision and uniformity to ensure proper performance.
Spun metal reflective coils are typically made from copper or aluminum, materials known for their excellent electrical conductivity. The metal spinning process allows for the creation of coils with uniform diameters and wall thicknesses, which are essential for the efficient transfer of electromagnetic energy.
19. Magnetic Shielding
Magnetic shielding is used to protect sensitive electronic components from external magnetic fields that can interfere with their performance. Metal spinning is used to produce custom magnetic shields that provide effective protection without compromising the functionality of the device.
These shields are typically made from materials with high magnetic permeability, such as soft iron or mu-metal, and the spinning process allows for the creation of shields with precise geometries and uniform material distribution, ensuring maximum effectiveness.
20. Light Diffusers
In electronic devices like LED lighting systems and display panels, light diffusers are used to scatter light evenly and prevent hotspots. Metal spinning is used to create diffusers with complex surface textures that scatter light effectively while maintaining structural integrity.
Spun light diffusers are often made from aluminum or stainless steel, which provide both durability and a reflective surface. The metal spinning process ensures that the diffusers have the necessary surface characteristics to achieve the desired light dispersion properties.
This article provides an overview of some of the top metal spinning parts used in electronics. These components, ranging from connectors and enclosures to heat sinks and reflectors, play a pivotal role in the performance and longevity of electronic devices. Metal spinning, with its ability to produce high-precision parts with minimal material waste, is a valuable manufacturing process in the electronics industry.
Maximize Tooling and CNC Metal Spinning Capabilities.
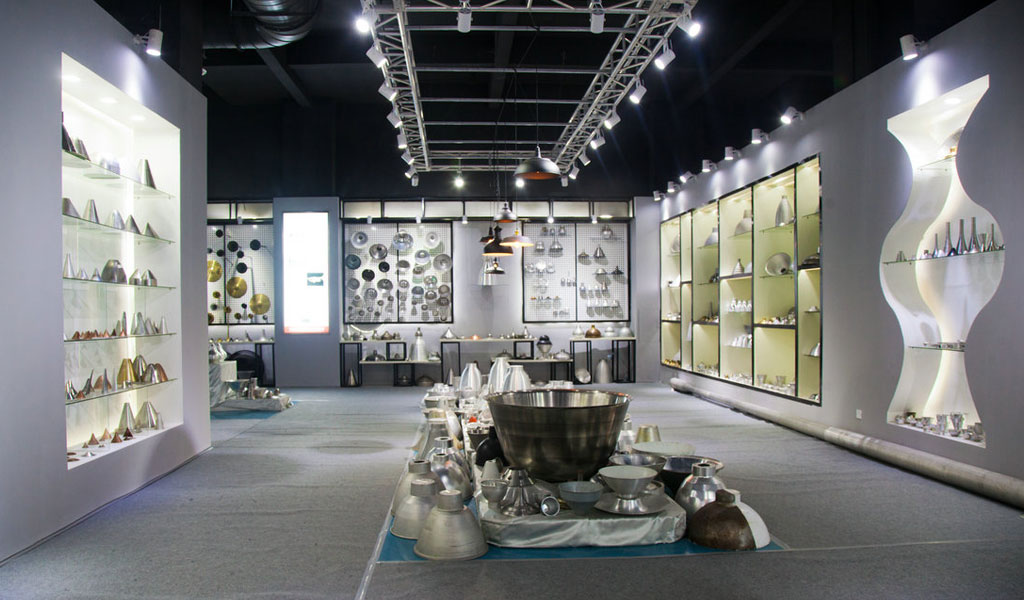
At BE-CU China Metal Spinning company, we make the most of our equipment while monitoring signs of excess wear and stress. In addition, we look into newer, modern equipment and invest in those that can support or increase our manufacturing capabilities. Our team is very mindful of our machines and tools, so we also routinely maintain them to ensure they don’t negatively impact your part’s quality and productivity.
Talk to us today about making a rapid prototype with our CNC metal spinning service. Get a direct quote by chatting with us here or request a free project review.
BE-CU China CNC Metal Spinning service include : CNC Metal Spinning,Metal Spinning Die,Laser Cutting, Tank Heads Spinning,Metal Hemispheres Spinning,Metal Cones Spinning,Metal Dish-Shaped Spinning,Metal Trumpet Spinning,Metal Venturi Spinning,Aluminum Spinning Products,Stainless Steel Spinning Products,Copper Spinning Products,Brass Spinning Products,Steel Spinning Product,Metal Spinnin LED Reflector,Metal Spinning Pressure Vessel,