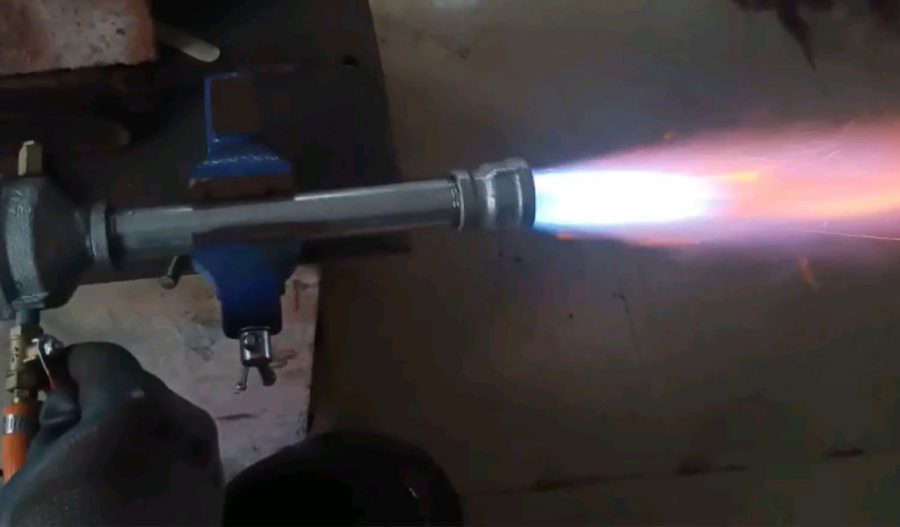
A Venturi burner is a type of burner that utilizes the Venturi effect to mix air and fuel in a specific ratio before combustion. The burner is named after the Italian physicist Giovanni Battista Venturi, who is known for his work on fluid dynamics, particularly the Venturi effect, which describes how the pressure of a fluid decreases as its velocity increases while passing through a constricted section of a pipe.
Venturi burners are commonly used in various industrial processes, heating systems, and in laboratory setups due to their efficiency in mixing fuel and air, which leads to cleaner and more controlled combustion. The basic principle behind a Venturi burner involves drawing in atmospheric air using the pressure difference created by the flow of fuel through a narrowed section of the burner.
Historical Background
The concept of the Venturi burner is rooted in the development of fluid dynamics in the 18th and 19th centuries. Giovanni Battista Venturi’s research laid the foundation for understanding how fluids behave when they pass through a constricted pathway. The practical application of the Venturi effect in burners emerged with the development of more sophisticated heating and combustion technologies during the industrial revolution. Early burners were simple in design, relying on the natural draft of air, but with the application of the Venturi principle, burners became more efficient and capable of sustaining higher temperatures with less fuel.
Principle of Operation
Venturi Effect
The Venturi effect is the core principle behind the operation of a Venturi burner. According to this principle, when a fluid (which could be a gas or a liquid) flows through a pipe that narrows to a constricted section, the fluid must speed up as it passes through this section. According to Bernoulli’s principle, an increase in the fluid’s velocity leads to a decrease in its pressure.
In the context of a Venturi burner, fuel (such as natural gas or propane) is forced through a narrow section of the burner tube. As the fuel passes through this narrow section, it creates a region of low pressure. This low pressure area naturally draws in air from the surrounding environment, mixing it with the fuel. The mixed fuel and air then proceed to the burner tip where combustion occurs.
Air-Fuel Mixing
Proper air-fuel mixing is crucial for efficient combustion. The Venturi burner achieves this by ensuring that the air is thoroughly mixed with the fuel before reaching the combustion zone. The ratio of air to fuel can often be adjusted to control the flame characteristics, including temperature, size, and cleanliness.
The precise control over this mixing process allows Venturi burners to operate more efficiently than traditional burners, as the complete combustion of the fuel is more likely. Incomplete combustion, which can occur if the air-fuel mixture is not properly controlled, can lead to the production of carbon monoxide and other harmful emissions.
Combustion Process
Once the air and fuel are properly mixed, the mixture is ignited at the burner tip. The combustion process in a Venturi burner is typically more stable and efficient compared to other burner designs. This stability is partly due to the consistent air-fuel mixture, which burns more completely and evenly.
In industrial applications, Venturi burners are often used where a precise flame temperature and stability are required. The combustion process in a Venturi burner can be fine-tuned by adjusting the air-fuel ratio and the fuel pressure, allowing for a high degree of control over the flame characteristics.
Design and Components
Burner Tube
The burner tube is the main body of the Venturi burner. It is typically made of metal, such as stainless steel, which can withstand high temperatures and corrosion. The tube’s design is crucial for the proper operation of the burner, as it determines the speed and pressure of the fuel as it passes through the Venturi section.
Venturi Throat
The Venturi throat is the narrow section of the burner tube where the Venturi effect occurs. The size and shape of the throat are carefully designed to optimize the air-fuel mixing process. A properly designed Venturi throat will create the right amount of low pressure to draw in the necessary amount of air for combustion.
Air Inlet
The air inlet is where the surrounding air is drawn into the burner. The placement and size of the air inlet can affect the efficiency of the burner, as it determines how much air is mixed with the fuel. In some designs, the air inlet can be adjusted to control the air-fuel ratio.
Fuel Nozzle
The fuel nozzle is where the fuel is introduced into the burner. The nozzle must be designed to deliver the fuel at the correct pressure and flow rate to ensure proper mixing with the air. The nozzle’s design can also affect the burner’s overall efficiency and flame characteristics.
Ignition System
The ignition system is used to ignite the air-fuel mixture at the burner tip. In industrial applications, this is often done using an electric spark or pilot flame. The ignition system must be reliable and capable of operating under the high-temperature conditions created by the burner.
Flame Retention Head
A flame retention head is sometimes used in Venturi burners to stabilize the flame. This component helps to hold the flame close to the burner tip, preventing it from being blown out by the airflow. This is particularly important in applications where a stable, consistent flame is required.
Applications
Industrial Applications
Venturi burners are widely used in industrial applications due to their efficiency and control over the combustion process. They are often used in furnaces, kilns, and boilers where precise temperature control is necessary. In these applications, the ability to adjust the air-fuel ratio allows for fine-tuning of the combustion process, leading to increased efficiency and reduced emissions.
Heating Systems
Venturi burners are also commonly used in commercial and residential heating systems. In these applications, the burner’s ability to produce a consistent and stable flame is critical for maintaining a comfortable indoor environment. The efficiency of Venturi burners also makes them an attractive option for heating systems, as they can help reduce fuel consumption and lower energy costs.
Laboratory Burners
In laboratory settings, Venturi burners are used in Bunsen burners and other types of burners where a controlled flame is necessary for experiments. The ability to adjust the flame characteristics makes Venturi burners ideal for a wide range of laboratory applications.
Cooking Equipment
Venturi burners are used in various types of cooking equipment, including stoves, grills, and ovens. In these applications, the burner’s efficiency and ability to produce a consistent flame are important for cooking food evenly. The ability to adjust the flame size and temperature also allows for more precise cooking.
Advantages
Efficiency
One of the main advantages of Venturi burners is their efficiency. By ensuring that the air and fuel are thoroughly mixed before combustion, Venturi burners can achieve complete combustion, reducing fuel consumption and minimizing the production of harmful emissions.
Control
Venturi burners offer a high degree of control over the combustion process. By adjusting the air-fuel ratio and fuel pressure, the flame characteristics can be fine-tuned to meet the specific needs of the application. This control is particularly important in industrial applications where precise temperature control is required.
Stability
The design of Venturi burners helps to produce a stable and consistent flame. This is important in applications where a reliable heat source is necessary, such as in industrial furnaces and heating systems.
Low Maintenance
Venturi burners are typically low maintenance, as they have few moving parts and are designed to operate under high-temperature conditions. This makes them an attractive option for applications where reliability and durability are important.
Disadvantages
Complexity in Design
While Venturi burners offer many advantages, their design can be more complex than other types of burners. The need to carefully design the Venturi throat, air inlets, and fuel nozzles can make these burners more expensive to manufacture and maintain.
Sensitivity to Fuel Pressure
Venturi burners can be sensitive to changes in fuel pressure. If the fuel pressure is too low or too high, it can affect the air-fuel mixing process, leading to incomplete combustion or an unstable flame. This sensitivity requires careful monitoring and control of the fuel supply.
Noise
In some applications, Venturi burners can produce more noise than other types of burners. This is due to the high velocity of the fuel and air as they pass through the Venturi section. While this noise can often be mitigated through design modifications, it can be a concern in certain settings.
Design Considerations
Throat Design
The design of the Venturi throat is critical to the burner’s performance. The throat must be designed to create the right amount of low pressure to draw in the correct amount of air. The size and shape of the throat can also affect the burner’s efficiency and flame characteristics.
Air-Fuel Ratio
The air-fuel ratio is a key factor in the performance of a Venturi burner. The ratio must be carefully controlled to ensure complete combustion and minimize emissions. In some applications, the ratio may need to be adjusted based on the specific fuel being used or the desired flame characteristics.
Material Selection
The materials used in the construction of a Venturi burner must be able to withstand the high temperatures and corrosive conditions created by the combustion process. Stainless steel is commonly used for the burner tube and other components due to its durability and resistance to corrosion.
Ignition System
The ignition system must be reliable and capable of operating under the high-temperature conditions created by the burner. In some applications, a pilot flame may be used to ignite the air-fuel mixture, while in others, an electric spark may be used.
Conclusion
Venturi burners are a versatile and efficient type of burner that are used in a wide range of applications, from industrial furnaces to residential heating systems. Their ability to thoroughly mix air and fuel before combustion leads to cleaner and more controlled combustion, making them an attractive option for applications where efficiency and stability are important. While their design can be more complex than other types of burners, the benefits they offer in terms of efficiency, control, and stability make them a popular choice in many industries.
Maximize Tooling and CNC Metal Spinning Capabilities.
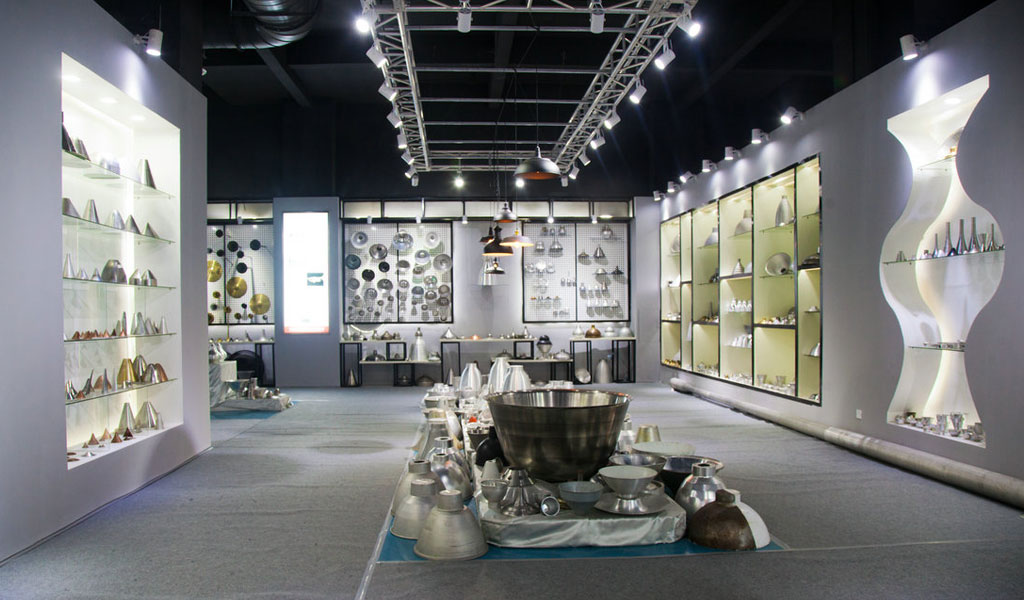
At BE-CU China Metal Spinning company, we make the most of our equipment while monitoring signs of excess wear and stress. In addition, we look into newer, modern equipment and invest in those that can support or increase our manufacturing capabilities. Our team is very mindful of our machines and tools, so we also routinely maintain them to ensure they don’t negatively impact your part’s quality and productivity.
Talk to us today about making a rapid prototype with our CNC metal spinning service. Get a direct quote by chatting with us here or request a free project review.
BE-CU China CNC Metal Spinning service include : CNC Metal Spinning,Metal Spinning Die,Laser Cutting, Tank Heads Spinning,Metal Hemispheres Spinning,Metal Cones Spinning,Metal Dish-Shaped Spinning,Metal Trumpet Spinning,Metal Venturi Spinning,Aluminum Spinning Products,Stainless Steel Spinning Products,Copper Spinning Products,Brass Spinning Products,Steel Spinning Product,Metal Spinnin LED Reflector,Metal Spinning Pressure Vessel,