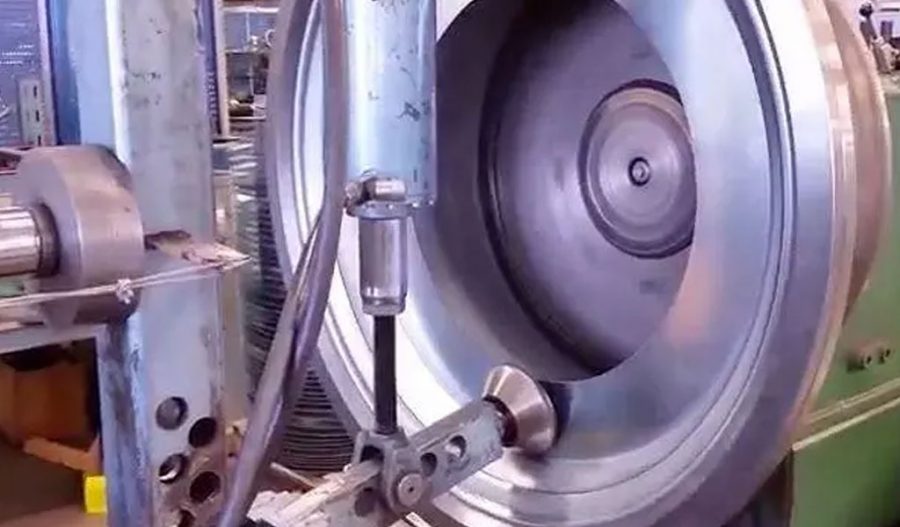
Today, I’m kicking off a two-part series on aftermarket wheels with a detailed FAQ. This article will dive into the more technical aspects, the ones better suited for text and images than video. Let’s get started.
Q1: What Do We Mean by Casting, Forging, and Semi-Forging?
A1: Casting is exactly what it sounds like: aluminum alloy is heated until it melts into a liquid, which is then poured into a mold. Once it cools and solidifies, voilà, you have a wheel! There are two main types of casting: low-pressure and high-pressure. Low-pressure casting is cost-effective and quick, which is why it’s often used for OEM wheels. However, for aftermarket wheels, where lightweight is a key factor, pressure is applied to the mold after pouring to ensure the metal cools with a tighter molecular structure, enhancing mechanical properties and reducing weight.
Forged wheels are created by “pressing” a solid piece of aluminum into shape using a forging press that exerts thousands to tens of thousands of tons of pressure. Since this process doesn’t involve melting and solidifying, the molecular structure remains intact, and the bonds between molecules become even stronger under the pressure, giving forged wheels superior mechanical properties compared to cast wheels.
In the market, you’ll find forged wheels from brands like Rays (Volk Racing series), BBS, TWS, and some from OZ and Enkei.
Semi-forging falls between casting and forging. If casting is like making ice cream from juice and forging is like molding a pastry from dough, semi-forging is like baking a cake from a mixture of batter. The costs and mechanical properties are somewhere in between casting and forging.
However, this middle ground is what makes semi-forging a bit awkward: it’s not as cheap as casting, so it doesn’t attract those seeking the best value, and it’s not as strong as full forging, so it doesn’t appeal to those chasing top performance. As a result, semi-forged wheels have never really become mainstream.
Q2: So, Does This Mean Forged Wheels Are the Best?
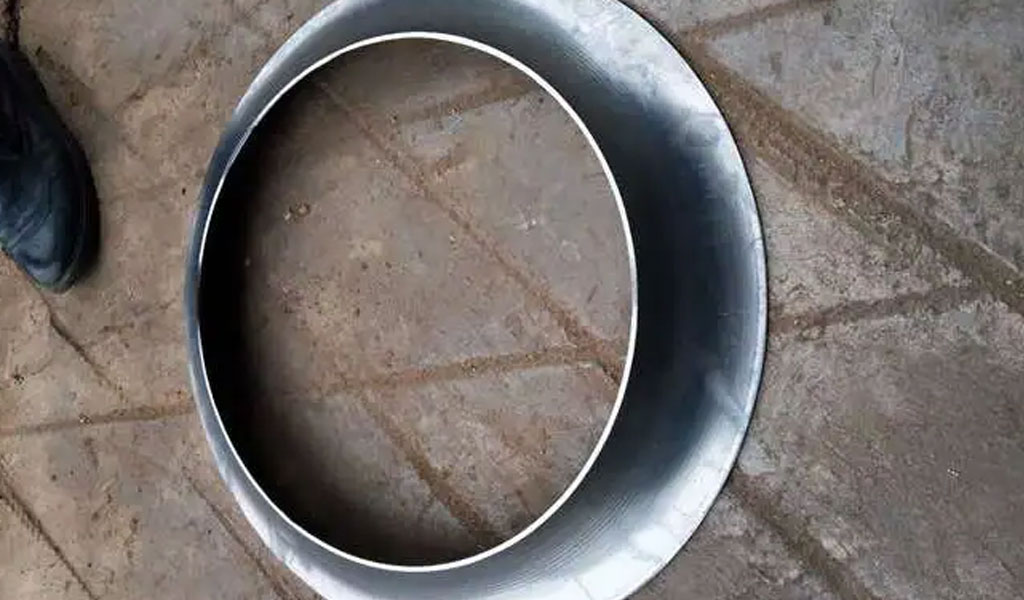
A2: In theory, full forging offers the highest stiffness-to-weight ratio. In other words, forged wheels are stiffer (or “harder,” as it’s commonly described) for the same weight, or they can be made lighter while achieving the same stiffness. However, the rigidity of a wheel also depends heavily on its design. Some wheels produced using flow forming, such as Weds TC105N, Enkei RPF1, or Advanti N718, can match or even surpass the weight of forged wheels like the original TE37 in the same size.
So, forged wheels aren’t necessarily the best option, especially considering the price. For example, a set of 17x7J forged wheels typically costs between ¥4500 and ¥6000 each, meaning a full set can easily run up to ¥20,000. In contrast, cast wheels from brands like OZ, Enkei, or Work are about half the price, and domestically produced flow-formed wheels from brands like Advanti or Artka are even more affordable. Essentially, for the price of one forged wheel, you could buy a decent set of flow-formed wheels.
If budget isn’t a concern, forged wheels are great. But if you’re hesitant to splurge on forged wheels and still want their performance benefits, those cast wheels I mentioned are worth considering. A well-made, lightweight cast wheel might only be 500 grams heavier than an ultra-light forged wheel, offering excellent value for money.
Q3: What is Flow Forming?
A3: Standard OE wheels are fully cast, meaning the mold is shaped like the entire wheel, and both the spokes and rim are formed during casting. Once the casting is complete, the wheel takes shape.
Flow forming, however, is somewhat of a “half-cast, half-forged” process. The spokes are cast, but the rim (or the “barrel” if you think of the wheel as a “bucket”) is formed by spinning the cast blank while applying pressure with a roller, similar to shaping pottery. This process, known as “spinning,” extends the barrel of the wheel with less material while achieving excellent strength. This results in a lighter wheel with a better stiffness-to-weight ratio than typical low-pressure cast wheels, and at a more affordable price.
Identifying a flow-formed wheel is easy: if you see a series of grooves on the barrel of a forged wheel, those are the marks left by the spinning process.
Q4: What Are the Drawbacks of Forged Wheels Besides the Cost?
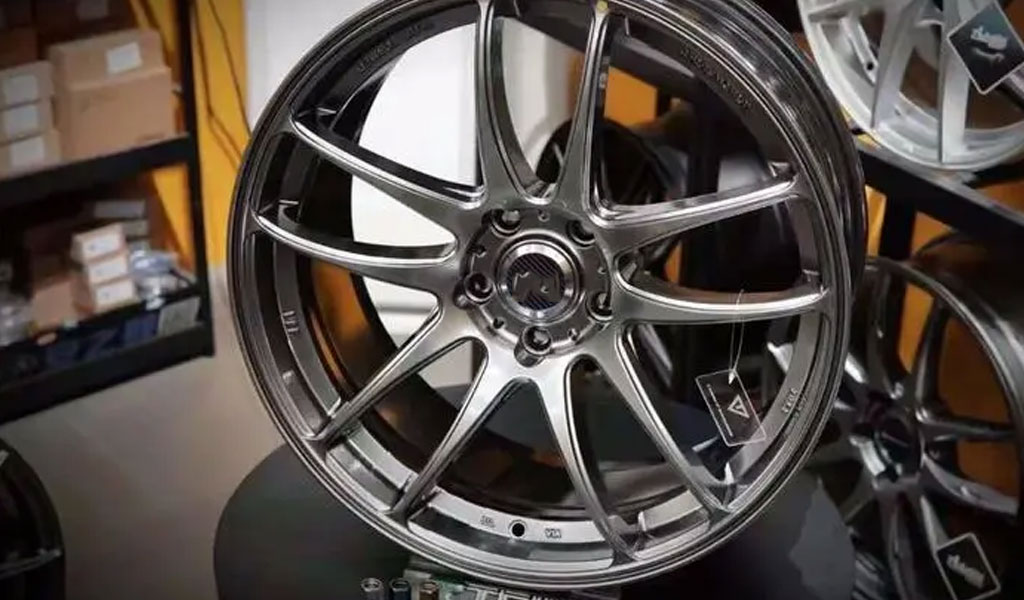
A4: Since forged wheels are made by compressing a block of aluminum alloy into a wheel shape, they are limited by the material’s inherent lack of malleability. This leads to two main drawbacks:
- Limited Design Flexibility: The design freedom for forged wheels is more restricted compared to other manufacturing methods.
- Material Constraints: Because the material must be malleable enough to be forged, very hard alloys can’t be used, which makes it challenging to create wheels with thick, strong spokes or a thick transition between the spokes and the rim. As a result, achieving extremely high hardness often still relies on casting techniques.
Due to these reasons, the world’s most precision-demanding races, like F1, GT series, and WEC endurance races, use forged wheels for their lightweight and rigidity. However, in more rugged and intense competitions like touring car racing, rally racing, and cross-country racing—where wheel strength is paramount—cast wheels are often preferred, despite being heavier.
Q5: What’s the Deal with “Custom BBS Forged” Wheels Made in China?
A5: These so-called custom forged wheels typically start with a forged blank—a large aluminum disc with no spokes, just a solid slab. The spokes are then carved out of this blank using a CNC milling machine.
The CNC process is quite interesting. The operator simply inputs the desired design program, and the machine carves out the wheel’s shape. So, whether you want something resembling a BBS RI-D, a TE37, or even a design similar to Ferrari or Bentley wheels, it’s all possible by machining the generic forged blank with the right program. This is what we mean by “custom forged.” It’s worth noting that custom forging isn’t unique to Chinese manufacturers; many international brands, especially those that emphasize design, also use CNC machining to create their wheels.
Q6: Are These “Custom Forged” Wheels Reliable?
A6: As many of you know, true forged wheels (from brands like BBS, Rays, TWS, OZ, etc.) maintain the molecular bonds within the aluminum, which aren’t broken during the process, unlike in casting. The forging process compacts these bonds even further, creating a dense metal flow on a macroscopic level, which enhances the wheel’s mechanical properties.
In contrast, “custom forged” wheels have spokes that are CNC-carved rather than forged. This means they miss out on the strengthening benefits of forging. Additionally, the CNC cutting process severs the molecular bonds at the edges, negatively impacting the wheel’s structural integrity.
Therefore, to match the performance of fully forged wheels, custom forged wheels require more material, leading to increased weight. If the goal is to keep them lightweight, their performance may fall short of fully forged wheels or even flow-formed cast wheels of similar weight.
In China, as in many industries, there’s a high ceiling but also a very low floor. The quality of custom forged wheels varies greatly, and factors such as aluminum quality, wheel design, and heat treatment processes can significantly affect both performance and safety. I wouldn’t personally recommend custom forged wheels unless someone has a specific need for them.
Q7: Who Should Consider Buying “Custom Forged” Wheels?
A7: While custom forged wheels might not match the mechanical performance of fully forged ones, they do offer greater design freedom thanks to CNC machining. This allows for more intricate and unique designs that casting or forging methods alone can’t achieve, making custom forged wheels an excellent choice for those who want flashy, unique styles.
The second advantage of custom forged wheels is in their “custom” nature. Enthusiasts who care about vehicle stance may need wheels with specific offset (ET) and width measurements, which is where custom wheels shine. Additionally, for owners of rare cars with uncommon PCD (bolt pattern) specifications, like GM vehicles with a PCD of 115 or Ford/Mazda/Volvo/PSA vehicles with a PCD of 108, finding suitable wheels can be challenging. Custom forged wheels allow for flexibility in PCD selection, making them a great option for owners of these vehicles.
Q8: Are Forged Wheels Really Indestructible?
A8: The idea that forged wheels are “indestructible” is somewhat misleading. As mentioned earlier, racing disciplines like touring car, rally, and cross-country, where impacts are severe, often use cast wheels, showing that well-made cast wheels can be highly durable too.
If the impact is strong enough, a forged wheel can still deform—it’s not immune to damage. However, forged wheels are less likely to crack or break completely due to the material’s inherent toughness and ductility. This property allows the wheel to absorb impacts better and deform rather than shatter, which is why they are preferred in high-performance applications.
Maximize Tooling and CNC Metal Spinning Capabilities.
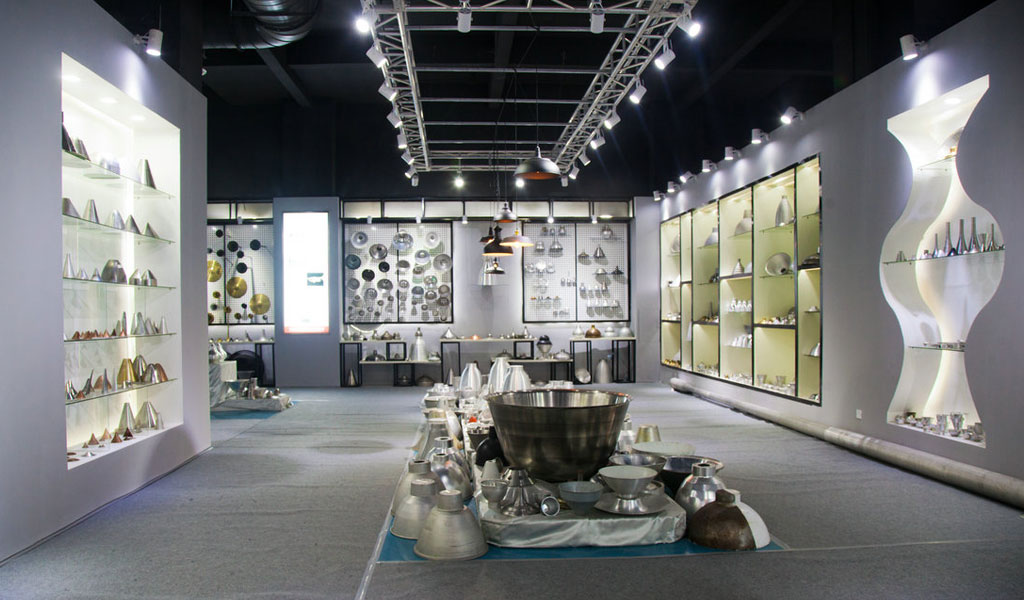
At BE-CU China Metal Spinning company, we make the most of our equipment while monitoring signs of excess wear and stress. In addition, we look into newer, modern equipment and invest in those that can support or increase our manufacturing capabilities. Our team is very mindful of our machines and tools, so we also routinely maintain them to ensure they don’t negatively impact your part’s quality and productivity.
Talk to us today about making a rapid prototype with our CNC metal spinning service. Get a direct quote by chatting with us here or request a free project review.
BE-CU China CNC Metal Spinning service include : CNC Metal Spinning,Metal Spinning Die,Laser Cutting, Tank Heads Spinning,Metal Hemispheres Spinning,Metal Cones Spinning,Metal Dish-Shaped Spinning,Metal Trumpet Spinning,Metal Venturi Spinning,Aluminum Spinning Products,Stainless Steel Spinning Products,Copper Spinning Products,Brass Spinning Products,Steel Spinning Product,Metal Spinnin LED Reflector,Metal Spinning Pressure Vessel,