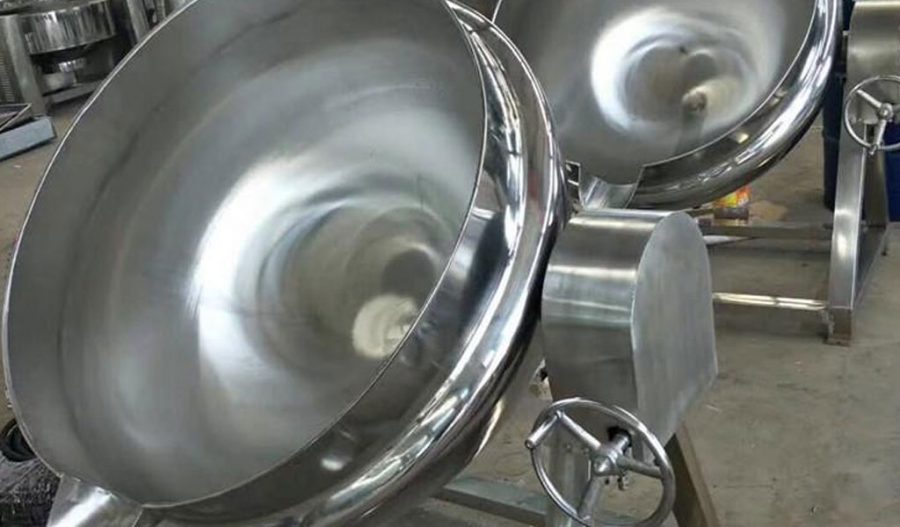
Metal CNC (Computer Numerical Control) spinning, also known as metal spinning or spin forming, is a metalworking process used to create axially symmetric parts. This technique is often employed in the production of various cylindrical items, including pots, pans, and other kitchenware. In this article, we will explore the detailed process of CNC spinning a stainless steel pot, from the initial design to the final product.
History and Background
Metal spinning has been used for centuries, with origins tracing back to ancient Egypt and China, where artisans manually shaped metal on a lathe. The advent of CNC technology revolutionized the process, enabling greater precision, efficiency, and consistency. Stainless steel, known for its corrosion resistance, strength, and aesthetic appeal, is a popular material choice for many metal-spun products, including cookware.
Materials and Equipment
Materials
- Stainless Steel Sheet: The primary material used in this process is a stainless steel sheet, typically between 0.5mm to 3mm in thickness. Common grades include 304 and 316 stainless steel due to their excellent formability and resistance to corrosion.
- Lubricants: Various lubricants are used to reduce friction and prevent the metal from overheating during the spinning process. These can include oil-based, water-based, or synthetic lubricants.
Equipment
- CNC Spinning Lathe: A specialized lathe equipped with CNC capabilities for precision control over the spinning process. It includes a headstock, tailstock, and a CNC controller to guide the spinning tools.
- Spinning Tools: These include rollers and mandrels, which are essential for shaping the metal. Rollers apply pressure to the metal, while mandrels support the workpiece and define the internal shape of the pot.
- Cutting Tools: Used for trimming excess material and refining the edges of the spun pot.
- Measuring Instruments: Precision measuring tools like calipers and micrometers ensure the final product meets the desired specifications.
CNC Spinning Process
Design and Programming
The process begins with designing the stainless steel pot using CAD (Computer-Aided Design) software. The design includes detailed specifications of the pot’s dimensions, shape, and any additional features. This CAD model is then converted into a CNC program using CAM (Computer-Aided Manufacturing) software. The program includes instructions for the CNC lathe on tool paths, feed rates, and spinning speeds.
Material Preparation
A stainless steel blank, typically a circular disc, is prepared according to the required dimensions. The blank is cleaned to remove any contaminants that could affect the spinning process.
Mounting the Blank
The prepared blank is mounted on the CNC lathe. It is clamped securely between the headstock and tailstock, with the mandrel positioned to support the blank from behind. Proper alignment is crucial to ensure the accuracy of the final product.
Initial Forming
The CNC lathe begins the spinning process by rotating the blank at high speeds. The roller tools, controlled by the CNC program, apply pressure to the blank, gradually shaping it over the mandrel. This stage involves several passes, with each pass bringing the blank closer to the desired shape.
Intermediate Forming
As the pot takes shape, intermediate forming steps are performed to refine its dimensions and features. This may include adding contours, flanges, or other design elements specified in the CAD model. The CNC program precisely controls these operations to ensure consistency and accuracy.
Trimming and Smoothing
Once the pot has reached its final shape, excess material is trimmed using cutting tools. The edges are smoothed and finished to remove any burrs or sharp edges. This stage may also involve additional machining operations, such as drilling holes or adding decorative elements.
Heat Treatment and Finishing
Depending on the application, the spun pot may undergo heat treatment to enhance its mechanical properties. This could include annealing to relieve stresses or hardening to improve strength. Finally, the pot is polished to achieve the desired surface finish. This may involve mechanical polishing, buffing, or chemical treatments to enhance the pot’s appearance and corrosion resistance.
Quality Control
Quality control is an integral part of the CNC spinning process. Each pot undergoes rigorous inspection to ensure it meets the required specifications. This includes dimensional checks, surface finish evaluation, and testing for mechanical properties. Non-destructive testing methods, such as ultrasonic or dye penetrant inspection, may also be used to detect any internal defects.
Applications and Advantages
Applications
Stainless steel pots produced through CNC spinning are widely used in various industries, including:
- Cookware: High-quality pots and pans for domestic and commercial kitchens.
- Chemical Industry: Containers for storing and processing chemicals.
- Aerospace: Components such as fuel tanks and structural elements.
- Automotive: Parts like exhaust components and fuel tanks.
Advantages
- Precision: CNC spinning provides high precision and repeatability, ensuring consistent product quality.
- Efficiency: The automated process reduces production time and labor costs.
- Material Utilization: Metal spinning generates less waste compared to other forming processes.
- Flexibility: CNC technology allows for easy modifications to the design and quick adaptation to different product specifications.
Challenges and Solutions
Challenges
- Tool Wear: The high forces involved in metal spinning can lead to rapid tool wear, affecting the quality of the final product.
- Material Properties: Stainless steel’s high strength and work-hardening characteristics can make it challenging to form without cracking or excessive thinning.
- Heat Generation: The friction between the tool and the workpiece generates heat, which can cause thermal distortion or affect the material’s properties.
Solutions
- Tool Maintenance: Regular inspection and maintenance of tools, along with the use of high-quality tool materials, can mitigate wear issues.
- Lubrication: Proper lubrication reduces friction and heat, improving tool life and product quality.
- Process Optimization: Fine-tuning the CNC program parameters, such as feed rates and spinning speeds, helps achieve the desired balance between formability and material integrity.
Conclusion
CNC spinning is a sophisticated metalworking process that enables the production of high-quality stainless steel pots with precision and efficiency. By leveraging advanced CAD/CAM technologies and CNC machinery, manufacturers can achieve consistent results and meet the demanding requirements of various industries. Despite its challenges, CNC spinning remains a vital technique for producing durable, aesthetically pleasing, and functional metal components.
Maximize Tooling and CNC Metal Spinning Capabilities.
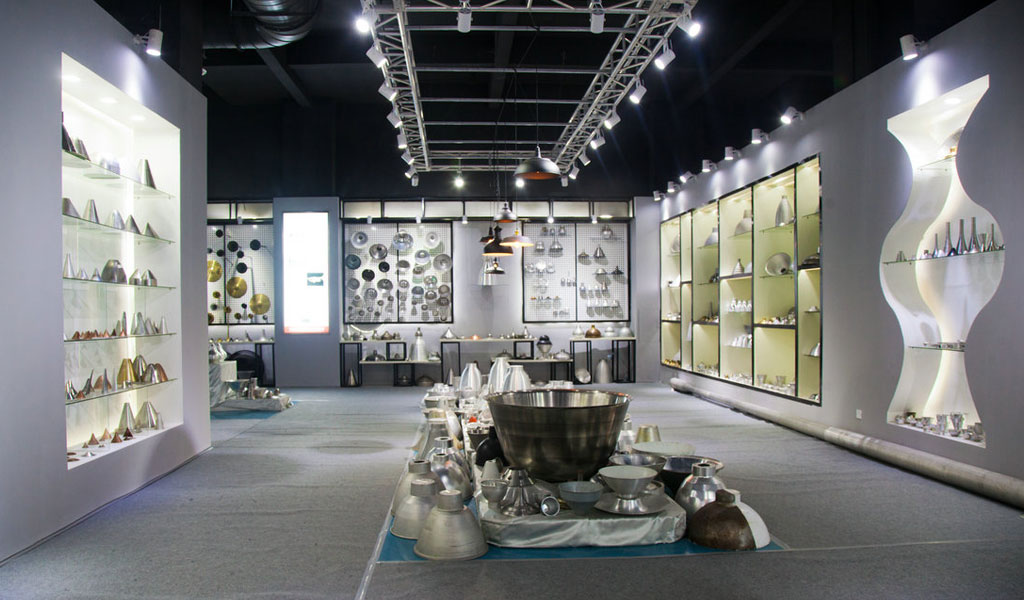
At BE-CU China Metal Spinning company, we make the most of our equipment while monitoring signs of excess wear and stress. In addition, we look into newer, modern equipment and invest in those that can support or increase our manufacturing capabilities. Our team is very mindful of our machines and tools, so we also routinely maintain them to ensure they don’t negatively impact your part’s quality and productivity.
Talk to us today about making a rapid prototype with our CNC metal spinning service. Get a direct quote by chatting with us here or request a free project review.
BE-CU China CNC Metal Spinning service include : CNC Metal Spinning,Metal Spinning Die,Laser Cutting, Tank Heads Spinning,Metal Hemispheres Spinning,Metal Cones Spinning,Metal Dish-Shaped Spinning,Metal Trumpet Spinning,Metal Venturi Spinning,Aluminum Spinning Products,Stainless Steel Spinning Products,Copper Spinning Products,Brass Spinning Products,Steel Spinning Product,Metal Spinnin LED Reflector,Metal Spinning Pressure Vessel,