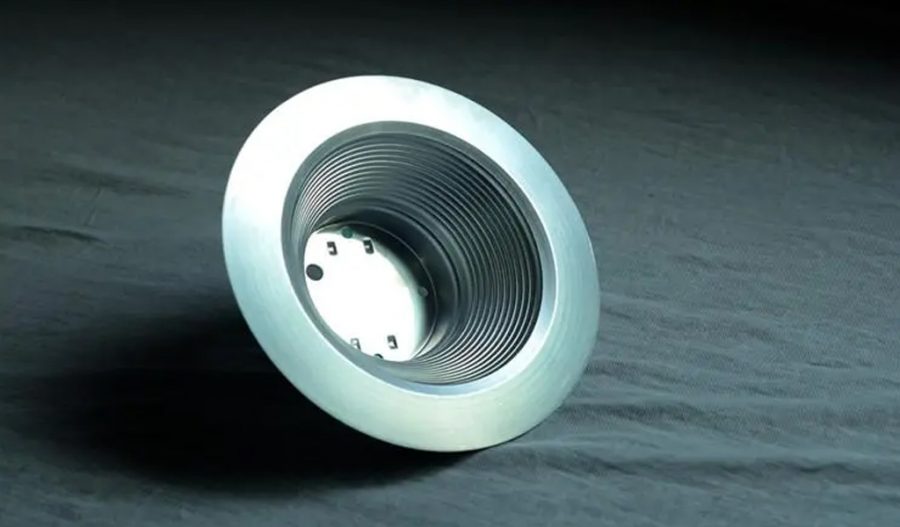
Metal spinning, a metalworking process that dates back centuries, has found its place in various industrial applications due to its efficiency, cost-effectiveness, and ability to produce high-quality parts. One area where metal spinning excels is in the production of roof drains. This article explores why metal spinning is the optimal choice for roof drains this season, delving into the process itself, its benefits, and its application in roofing systems.
History of Metal Spinning
Metal spinning, also known as spin forming or spinning, is a process that involves the shaping of metal over a rotating mandrel to create axially symmetric parts. This technique has been used for centuries, with origins tracing back to ancient Egypt and China. The process has evolved significantly, with advancements in technology enhancing precision and efficiency.
Ancient Beginnings
In ancient times, craftsmen used simple lathes to manually spin metals into desired shapes. These early techniques laid the foundation for modern metal spinning, showcasing the inherent flexibility and versatility of the process. The primary materials used included softer metals like gold, silver, and copper, which were easier to manipulate with the tools available at the time..
Industrial Revolution
The Industrial Revolution marked a significant turning point for metal spinning. The advent of steam power and later electricity led to the development of more sophisticated lathes and tools. These innovations allowed for greater precision and the ability to work with harder metals, such as steel and aluminum. Metal spinning became integral to the manufacturing of various components, from kitchenware to industrial parts.
Modern Advancements
Today, metal spinning benefits from computer numerical control (CNC) technology, which has revolutionized the process by enhancing accuracy and repeatability. CNC machines allow for the automation of metal spinning, reducing the reliance on skilled manual labor and enabling the production of complex shapes with tight tolerances. These advancements have expanded the range of applications for metal spinning, making it a preferred method in industries such as aerospace, automotive, and construction.
The Metal Spinning Process
Metal spinning involves several key steps, each crucial to achieving the desired final product. Understanding these steps provides insight into why metal spinning is an optimal choice for producing roof drains.
Design and Material Selection
The process begins with the design of the part and selection of the appropriate material. For roof drains, materials such as aluminum, stainless steel, and copper are commonly used due to their durability, corrosion resistance, and aesthetic appeal. The design phase involves creating detailed drawings and specifications, ensuring that the final product meets all functional and aesthetic requirements.
Blank Preparation
Once the design is finalized, the next step is preparing the metal blank. A blank is a flat, circular piece of metal that will be spun into the desired shape. The blank’s size and thickness are determined based on the specifications of the roof drain design. Cutting and preparing the blank with precision is essential to ensure consistent quality in the final product.
Spinning Process
The core of the metal spinning process involves shaping the blank over a mandrel using a combination of rotational force and pressure. This is typically done on a lathe, where the blank is clamped against the mandrel and rotated at high speeds. A roller or forming tool is then applied to the blank, gradually shaping it into the desired form.
There are two primary types of metal spinning: manual and CNC spinning.
- Manual Spinning: This traditional method relies on the skill of the operator to shape the metal. The operator uses hand tools to apply pressure to the blank, gradually forming it over the mandrel. While manual spinning allows for a high degree of control and flexibility, it requires significant skill and experience.
- CNC Spinning: In contrast, CNC spinning utilizes computer-controlled lathes to automate the process. CNC machines follow pre-programmed instructions to shape the metal with high precision and repeatability. This method is ideal for producing complex shapes and large quantities of parts with consistent quality.
Trimming and Finishing
After the spinning process is complete, the part undergoes trimming and finishing to achieve the final dimensions and surface quality. Trimming removes any excess material, ensuring that the part meets the specified dimensions. Finishing processes such as polishing, anodizing, or coating may be applied to enhance the appearance and durability of the part. For roof drains, these finishing touches are crucial to ensure longevity and resistance to environmental factors.
Benefits of Metal Spinning for Roof Drains
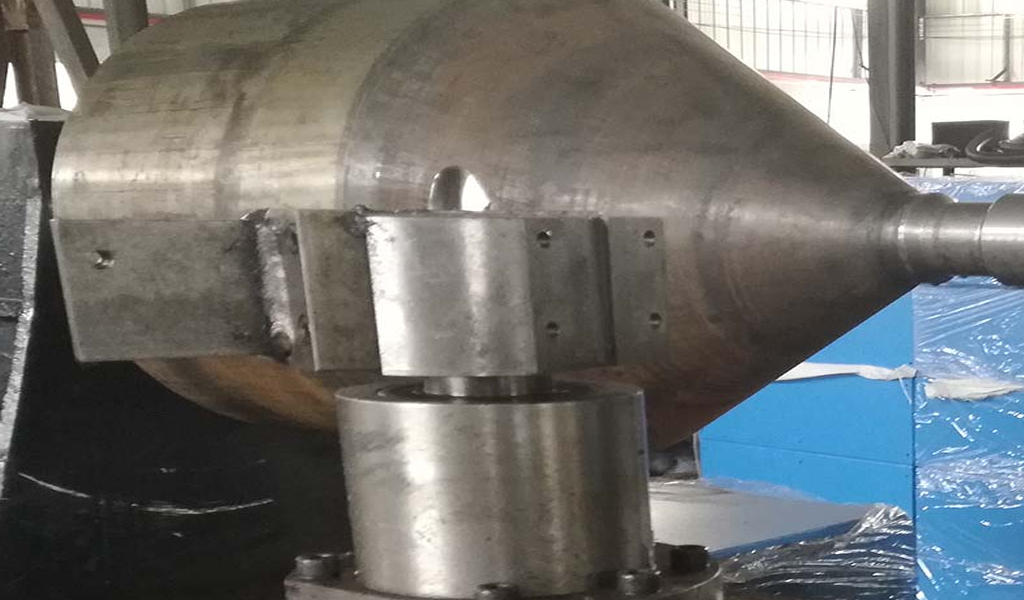
Metal spinning offers several advantages that make it an optimal choice for producing roof drains. These benefits include cost-effectiveness, material efficiency, design flexibility, and superior quality.
Cost-Effectiveness
One of the most significant advantages of metal spinning is its cost-effectiveness. The process involves minimal material waste, as the blank is shaped directly into the desired form without the need for extensive machining or welding. This efficiency translates into lower production costs, making metal spinning an economical choice for manufacturers.
Additionally, the ability to use CNC machines for automated spinning reduces labor costs and increases production speed. This is particularly beneficial for large-scale production runs, where consistency and efficiency are paramount. The cost savings achieved through metal spinning can be passed on to consumers, making high-quality roof drains more affordable.
Material Efficiency
Metal spinning is a highly material-efficient process, with minimal scrap generated during production. Unlike other manufacturing methods that require extensive cutting and welding, metal spinning shapes the blank directly into the final form. This not only reduces material waste but also minimizes the need for additional processing steps, further enhancing efficiency.
For roof drains, material efficiency is crucial to achieving optimal performance and durability. The seamless construction of spun metal parts ensures that there are no weak points or joints that could compromise the integrity of the drain. This results in a more robust and reliable product that can withstand the rigors of environmental exposure.
Design Flexibility
The versatility of metal spinning allows for a wide range of design possibilities. Manufacturers can produce complex shapes and custom designs with relative ease, enabling them to meet the specific requirements of different roofing systems. Whether it’s a standard round roof drain or a custom-designed part with unique features, metal spinning can accommodate diverse design needs.
This design flexibility is particularly advantageous for architects and builders who seek to incorporate innovative and aesthetically pleasing roof drains into their projects. The ability to create custom designs without incurring significant additional costs makes metal spinning an attractive option for both standard and bespoke roofing solutions.
Superior Quality
Metal spinning produces parts with superior quality and structural integrity. The process involves continuous deformation of the metal, resulting in a seamless and uniform construction. This seamless construction enhances the strength and durability of the part, making it well-suited for demanding applications such as roof drains.
Roof drains are exposed to harsh environmental conditions, including rain, snow, and debris. The superior quality of spun metal parts ensures that they can withstand these challenges without degrading or failing. Additionally, the smooth and consistent surface finish achieved through metal spinning enhances the appearance of the roof drain, contributing to the overall aesthetic of the roofing system.
Applications of Metal Spinning in Roof Drains
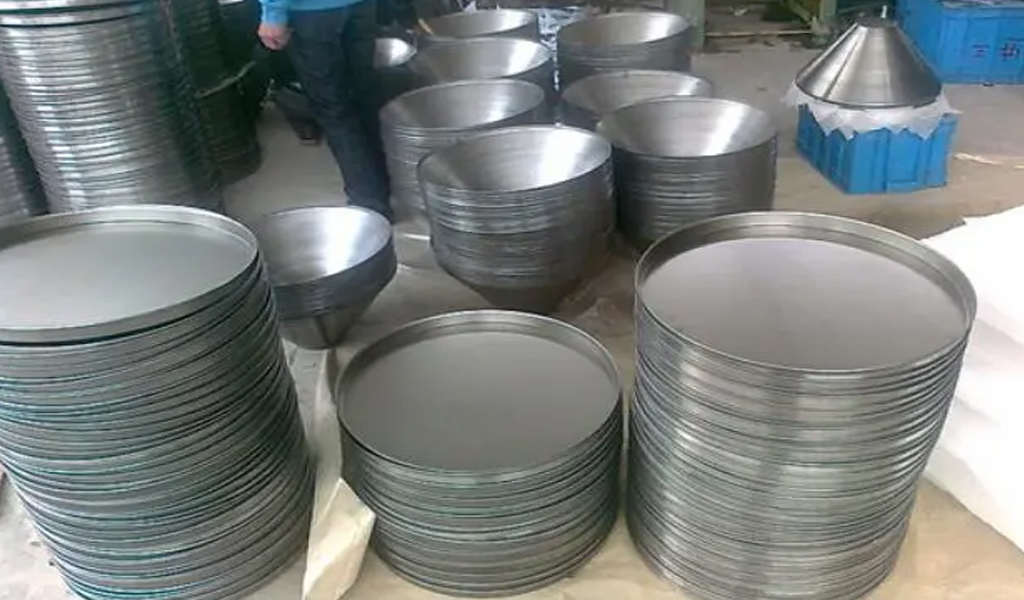
Metal spinning is widely used in the production of various components for roofing systems, including roof drains, scuppers, and downspouts. Each of these components plays a crucial role in ensuring effective water drainage and preventing water damage to the building.
Roof Drains
Roof drains are essential for directing water off the roof and into the drainage system. Properly functioning roof drains prevent water accumulation, which can lead to structural damage, leaks, and other issues. Metal-spun roof drains offer several advantages, including durability, corrosion resistance, and a seamless construction that ensures reliable performance.
Scuppers
Scuppers are openings in the parapet or edge of a roof that allow water to drain off the roof surface. They are often used in conjunction with roof drains to provide additional drainage capacity. Metal-spun scuppers are durable and can be customized to fit the specific design requirements of the roofing system. Their seamless construction ensures that water flows efficiently without leaks or blockages.
Downspouts
Downspouts are vertical pipes that carry water from the roof drains or scuppers to the ground or a designated drainage area. Metal-spun downspouts offer superior strength and resistance to environmental factors, ensuring that water is effectively channeled away from the building. The seamless construction of spun metal downspouts minimizes the risk of leaks and enhances their overall performance.
Case Studies: Success Stories of Metal Spun Roof Drains
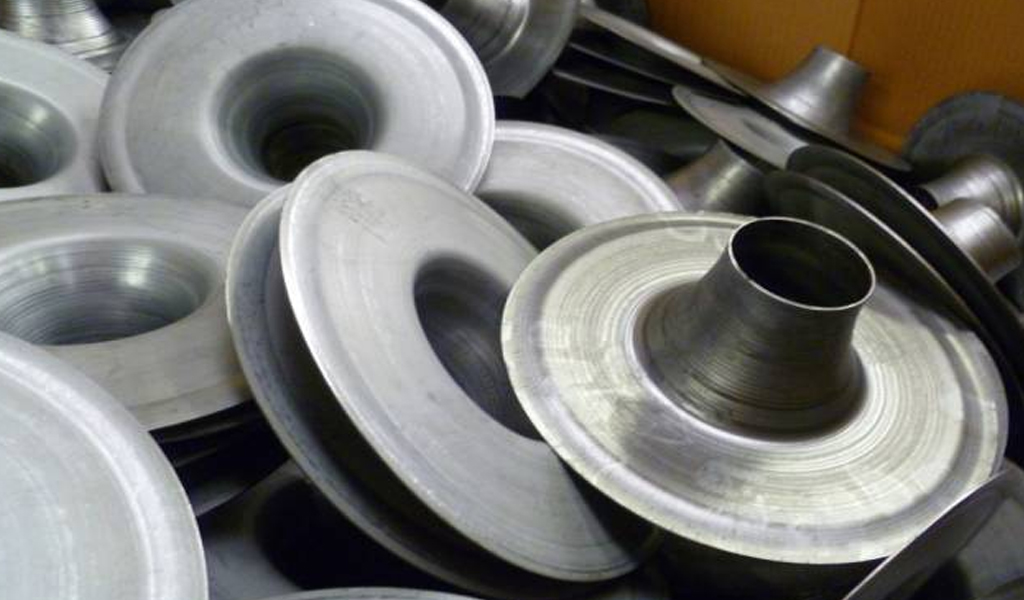
To illustrate the benefits of metal spinning for roof drains, several case studies highlight successful implementations in various projects. These examples demonstrate how metal-spun roof drains have contributed to the effectiveness and longevity of roofing systems.
Case Study 1: Commercial Building in Urban Environment
A commercial building in a densely populated urban area faced challenges with water drainage due to heavy rainfall and limited space for traditional drainage systems. The building’s architect chose metal-spun roof drains and downspouts for their durability and design flexibility. The custom-designed roof drains effectively directed water away from the roof, preventing water accumulation and potential damage. The seamless construction of the spun metal parts ensured reliable performance, even in challenging weather conditions.
Case Study 2: Residential Development in Coastal Area
A residential development located in a coastal area required a roofing system that could withstand the harsh marine environment. Metal-spun roof drains made from corrosion-resistant stainless steel were selected for their durability and ability to resist saltwater exposure. The roof drains provided efficient water drainage, protecting the buildings from water damage and prolonging the lifespan of the roofing system. The aesthetic appeal of the polished stainless steel roof drains also enhanced the overall appearance of the development.
Case Study 3: Historic Building Restoration
A historic building undergoing restoration required roof drains that matched the original design while meeting modern performance standards. Metal spinning allowed for the production of custom-designed roof drains that replicated the original architectural details. The seamless construction and high-quality finish of the spun metal parts ensured that the restored roof drains not only preserved the building’s historic integrity but also provided reliable water drainage. The use of metal-spun roof drains contributed to the successful preservation of the building’s historical significance.
Environmental Considerations
Metal spinning is an environmentally friendly manufacturing process, offering several benefits that align with sustainable practices. These include material efficiency, energy savings, and recyclability.
Material Efficiency
As previously mentioned, metal spinning generates minimal material waste, as the blank is shaped directly into the final form without extensive cutting or machining. This material efficiency reduces the consumption of raw materials, contributing to resource conservation. Additionally, the use of durable metals such as aluminum and stainless steel ensures that the parts have a long lifespan, further reducing the need for frequent replacements and conserving resources.
Energy Savings
Metal spinning requires less energy compared to other metalworking processes such as casting or forging. The use of CNC machines enhances energy efficiency by automating the process and reducing the need for manual labor. The streamlined production process minimizes energy consumption, contributing to lower overall energy usage and a reduced carbon footprint.
Recyclability
Metals used in the spinning process, such as aluminum, stainless steel, and copper, are highly recyclable. At the end of their useful life, metal-spun roof drains can be recycled and repurposed into new products. This recyclability supports a circular economy, reducing waste and conserving natural resources. The environmental benefits of metal spinning make it a sustainable choice for manufacturers and consumers alike.
Future Trends in Metal Spinning for Roof Drains
The future of metal spinning for roof drains looks promising, with several trends and advancements expected to shape the industry. These include advancements in CNC technology, the development of new materials, and the integration of smart technologies.
Advancements in CNC Technology
Continued advancements in CNC technology are expected to enhance the precision, efficiency, and versatility of metal spinning. Improved CNC machines with advanced controls and capabilities will allow for the production of even more complex and intricate designs. This will enable manufacturers to meet the evolving demands of the construction industry and offer innovative solutions for roofing systems.
Development of New Materials
The development of new materials, such as advanced alloys and composites, will expand the range of possibilities for metal spinning. These materials will offer enhanced properties, such as increased strength, corrosion resistance, and lightweight characteristics. The use of advanced materials in metal-spun roof drains will further improve their performance and durability, making them suitable for a wider range of applications and environments.
Integration of Smart Technologies
The integration of smart technologies, such as sensors and IoT (Internet of Things) connectivity, is expected to revolutionize the functionality of roof drains. Smart roof drains equipped with sensors can monitor water flow, detect blockages, and provide real-time data to building management systems. This information can be used to optimize maintenance schedules, prevent potential issues, and improve overall building performance. The combination of metal spinning and smart technologies will result in more efficient and intelligent roofing systems.
Conclusion
Metal spinning is an optimal choice for producing roof drains due to its cost-effectiveness, material efficiency, design flexibility, and superior quality. The process’s ability to produce high-quality parts with minimal waste and energy consumption aligns with sustainable manufacturing practices. Metal-spun roof drains offer reliable performance, durability, and aesthetic appeal, making them a preferred option for a wide range of roofing applications. As advancements in technology and materials continue to evolve, the future of metal spinning for roof drains looks promising, with new opportunities for innovation and improved performance on the horizon.
Maximize Tooling and CNC Metal Spinning Capabilities.
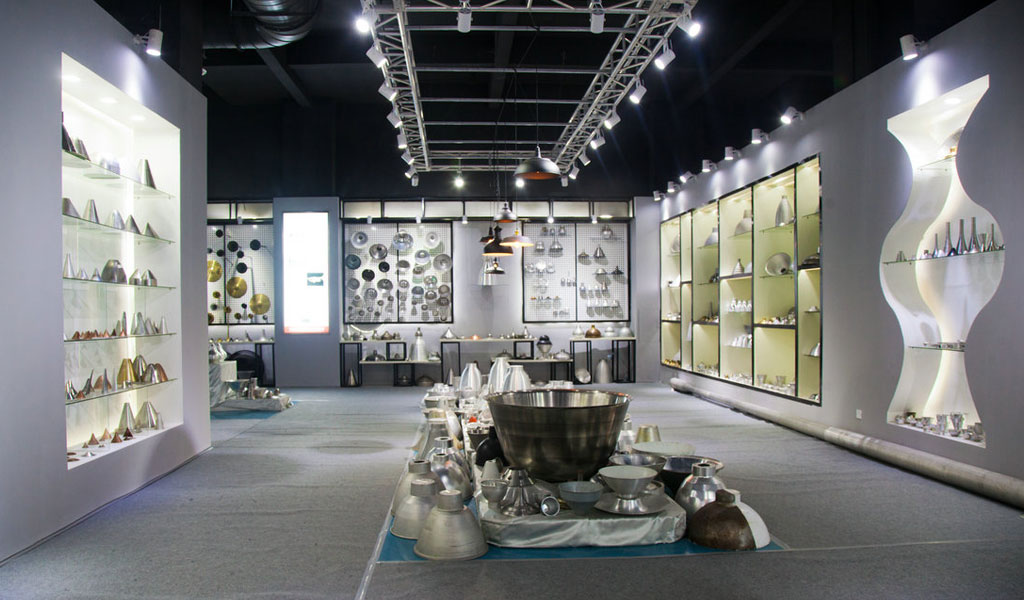
At BE-CU China Metal Spinning company, we make the most of our equipment while monitoring signs of excess wear and stress. In addition, we look into newer, modern equipment and invest in those that can support or increase our manufacturing capabilities. Our team is very mindful of our machines and tools, so we also routinely maintain them to ensure they don’t negatively impact your part’s quality and productivity.
Talk to us today about making a rapid prototype with our CNC metal spinning service. Get a direct quote by chatting with us here or request a free project review.
BE-CU China CNC Metal Spinning service include : CNC Metal Spinning,Metal Spinning Die,Laser Cutting, Tank Heads Spinning,Metal Hemispheres Spinning,Metal Cones Spinning,Metal Dish-Shaped Spinning,Metal Trumpet Spinning,Metal Venturi Spinning,Aluminum Spinning Products,Stainless Steel Spinning Products,Copper Spinning Products,Brass Spinning Products,Steel Spinning Product,Metal Spinnin LED Reflector,Metal Spinning Pressure Vessel,